The road from rapid prototyping to finished production can pose a number of challenges.
For instance, creating and optimizing product design, sourcing production and balancing investments in inventory with market demand are just a few of the potential pitfalls.
One firm that’s successfully navigated this process is POST-IS (http://post-is.com). The company provides hardware and software that automates postal logistics, including sophisticated bar code scanners and cameras that can accurately count and route packages.
We were fortunate to work with POST-IS from the prototype phase through to early production runs, and in hopes of sharing info among the Xometry community, wanted to highlight a few lessons learned:
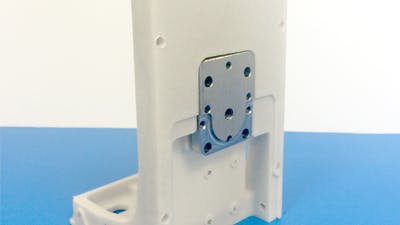
An early POST-IS prototype, which was created in SLS and included a metal insert (Source: POST-IS).
POST-IS selected SLS (Selective Laser Sintering) for their initial prototypes.
SLS, which builds parts using a strong, flexible nylon material, was an ideal fit in this instance. The process is accurate, fast and cost-affordable – particularly on a low-volume basis, and allowed POST-IS to quickly fit-check their design and make any adjustments before gravitating to machining (where errors can potentially be more costly).
The 3D printed prototypes were built in four business days. To top it off, we added a custom finish and metal installations.
Note: other 3D printing processes for creating plastic prototypes include FDM (Fused Deposition Modeling) and PolyJet 3D.
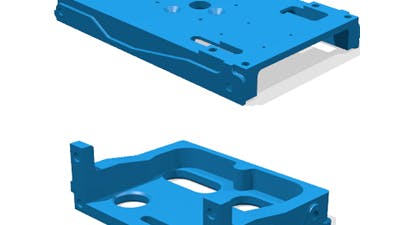
The original 1-piece prototype design was split into two separate components to help reduce machining costs.
POST-IS’ original product design involved an “L” shaped product housing – to be built using CNC machining.
However, if you milled this design from a single block of material, you would end up with large amount of material wasted (everything but the “L”). Also, removing this material requires additional machining time and potentially more operations – all of which adds manufacturing costs.
As an alternative, our project engineering team suggested splitting up the design into two separate components. This helped eliminate material waste and made the project more cost-effective. The result? Over 40% in cost savings.
Note: for more cost-saving tips, visit our earlier post on the “Top 10 ways to save on CNC machining.”
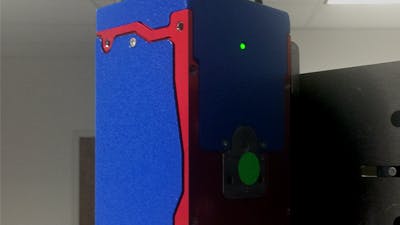
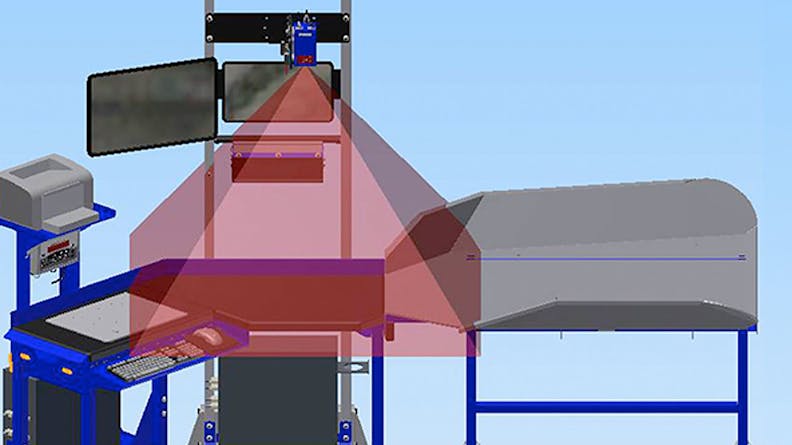
The finished product. This POST-IS assembly includes a sophisticated camera that can accurately count and route packages. (Source: POST-IS).
At Xometry, all parts are built on-demand and with no set-up costs. This allows customers to scale as demand grows.
POST-IS started by ordering a relatively small number of parts – less than a 100 units – just enough to fulfill their purchase order. The technique generated two key benefits:
- Reduced upfront costs
- Minimized inventory costs
And since overhead was low, POST-IS is able to iterate on their design and gear up for launch in new markets. Looking ahead, the company has big plans and is now preparing for its next government contract.
To the POST-IS team: congratulations on all your success and good luck on the new launch!
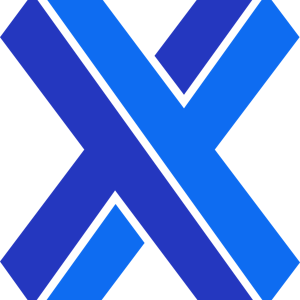