Case Study: Xometry’s Precise Laser Tube Cutting Helps Sea Box Build, Scale Up a Big Project for a Defense Customer
Learn how this New Jersey-based small business utilized Xometry’s sheet cutting and laser tube cutting services to build a custom structure from the ground up and quickly scale up production.
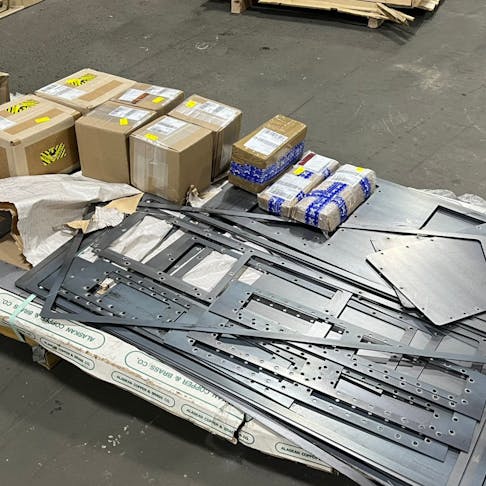
Industries | Manufacturing Services Utilized | Project Brief | Solution |
---|---|---|---|
Industries ISO containers and modular buildings for commercial and military customers | Manufacturing Services Utilized Sheet cutting and laser tube cutting | Project Brief Sea Box relies on its in-house engineers and manufacturers for many of its builds, but a large project on a tight timeline required more parts than they could make in-house. | Solution The company turned to Xometry to provide the steel sheet metal and tube components for the ground-up build. |
Since 1984, Sea Box has designed, customized, and manufactured ISO containers and modular buildings for commercial and military applications. From ready-made containers for storage and shipping to custom-built structures for uses ranging from residential to medical, the New Jersey-based small business has expanded its offerings and workforce over the years. Today, it employs about 350 people, including a team of engineers who design unique solutions to fit customers’ needs.
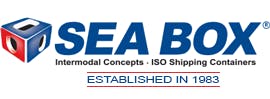
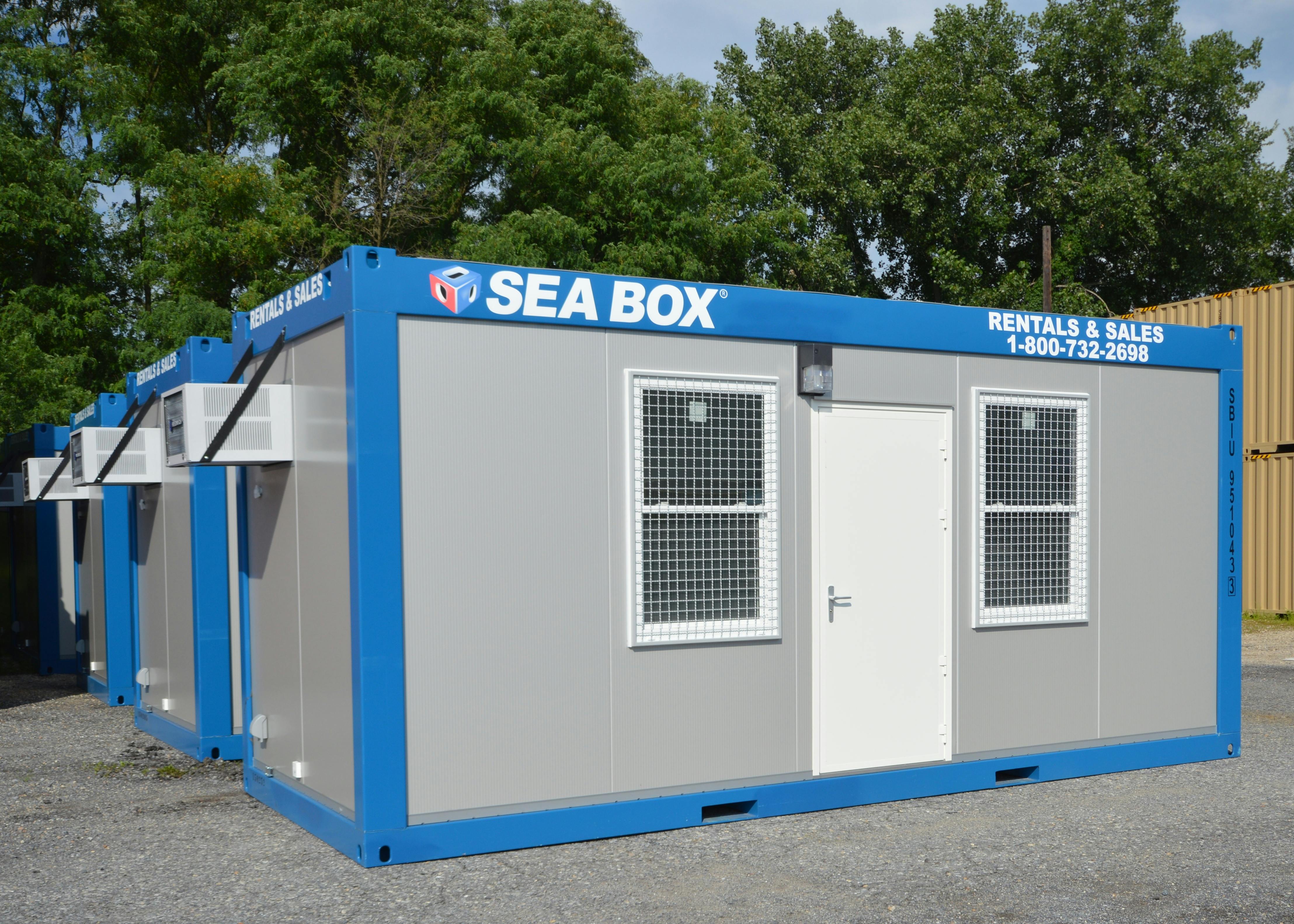
Many of Sea Box’s projects are designed and manufactured in-house, but sometimes a large project requires the company to outsource some of the manufacturing. That was the case for a recent project for a defense customer that needed a custom-built prototype on a short timeline.
“The schedule and the sheer number of parts required us to reach outside our normal networks and look for other options,” said Jeff Lucas, a senior project manager at Sea Box.
Some of Lucas’ colleagues at Sea Box had used Xometry before to get quotes and place orders for custom parts, and they recommended it as a solution for his project.
Lucas needed to order roughly 400 machined parts, including sheet metal and laser-cut tubes, so “instead of going to a shop that specializes in sheet metal and another shop that specializes in just tube cutting, we sent everything we needed over,” Lucas said of Xometry. “It was a one-stop shop.”
Building From the Ground Up
“For most projects, we start with an existing container, and then we modify that,” Lucas said. “For this project, we built it from the ground up, which required specialty tubes and a whole lot more work, because every single piece of the entire build had to be designed, made and purchased, versus just starting with a container, cutting out the corrugated walls and putting in some framing. Additionally, the tolerances that were required on this project were very, very tight—not quite aerospace, but pretty tight—and so the machining capability and the machine work had to be pretty tight.”
With such a detailed design, Lucas knew the project would be complicated to schedule since all the parts would need to arrive in a specific order.
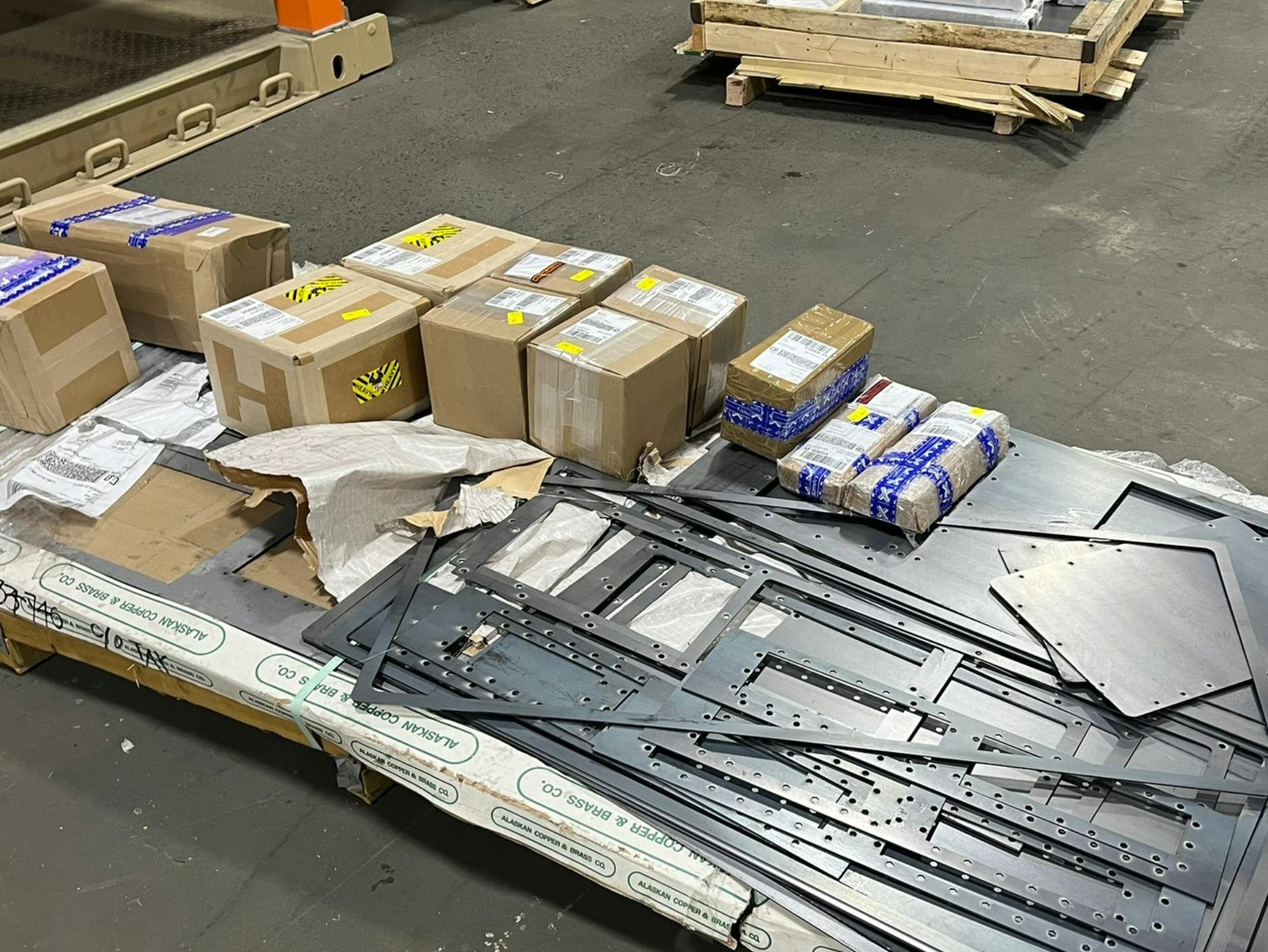
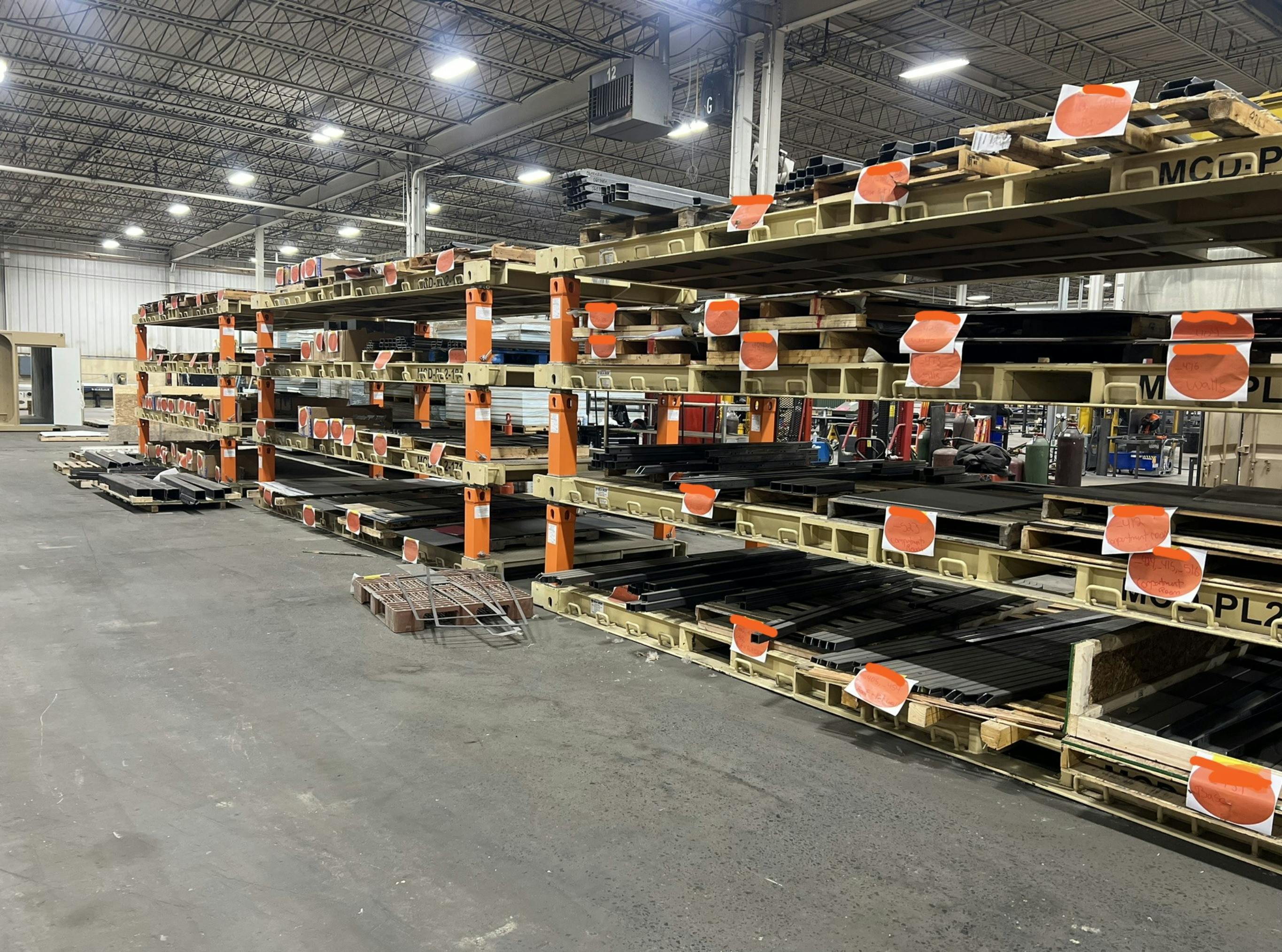
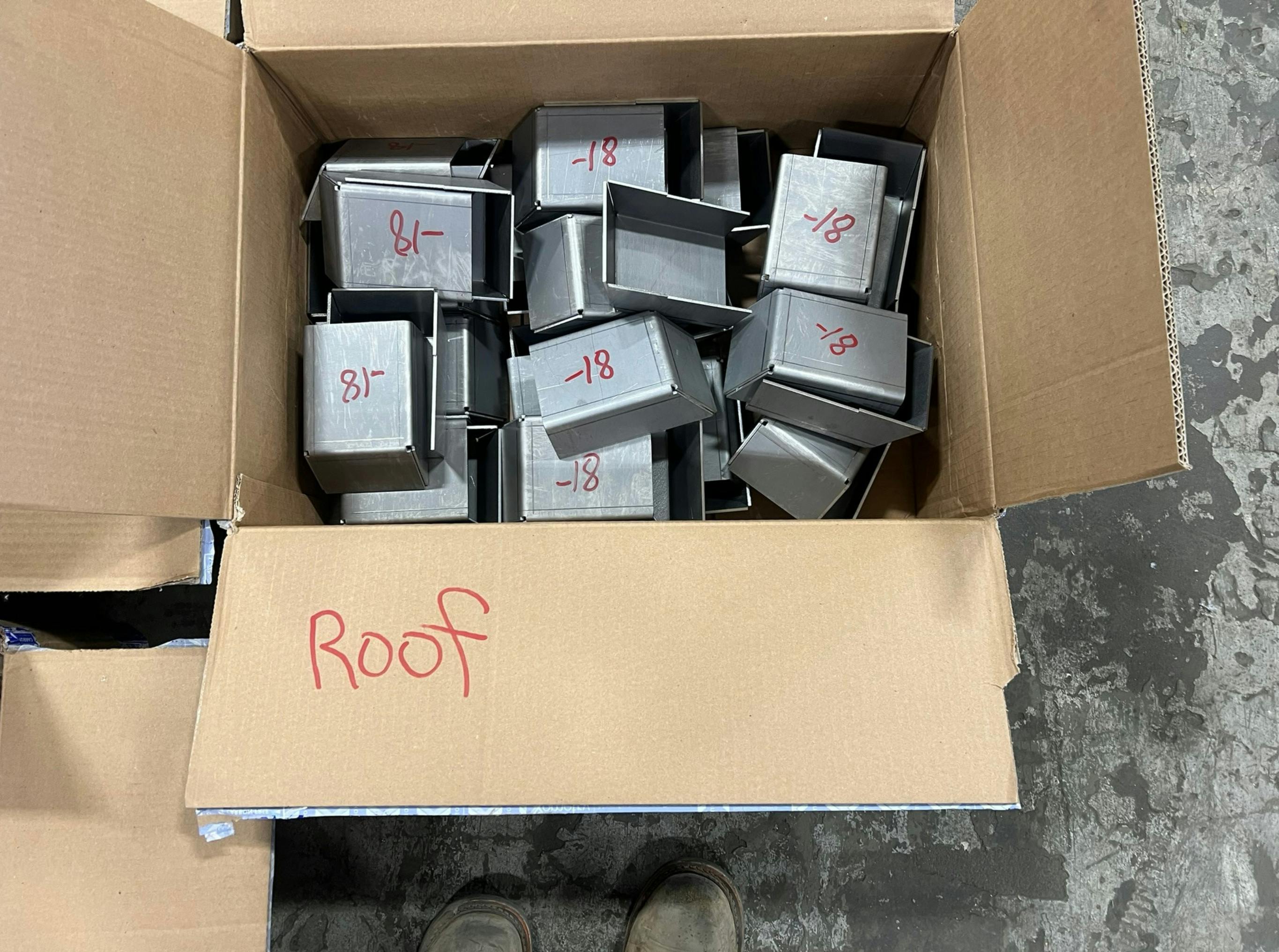
Sea Box ordered about 400 machined parts, including sheet metal and laser-cut tubes, from Xometry for a ground-up build for a defense customer. (Image Credit: Sea Box)
“Trying to schedule all of them and determine lead times is a major driver of our schedule because we can't build anything if we don't have parts here,” he said.
Uploading parts to Xometry and being able to track everything on the Teamspace Dashboard simplified the project by giving Lucas and his team an organized source of information.
“Being able to look at a full quote for all the parts, and then being able to pick the lead time that worked with our our schedule made it very easy,” he said. “Anytime a part would ship, we would get a notification and the tracking number. We could go on to the project dashboard and see the status of everything that we've ordered, which is very valuable, being able to track that and have access to certification documents and packing slips and whatever other inspection documents we required. In our particular case, we had some parts that were ITAR, so being able to handle the ITAR stuff as well was a major plus. Everything's kind of at your fingertips. Some of the old-school machine shops don't have that sort of tech.”
Tight Tolerances Call for Laser Precision
Laser-cut tubes were an integral part of the project because “the tubes make up the full structure of this particular container,” Lucas said.
“Shipping containers are held to an ISO standard for size and tolerance, so right off the bat, we have to be able to hold those tolerances. But further, for our customers’ equipment to fit, to meet the ISO standards for tolerances on the ultimate size of the container, and for form, fit, and function, ultimately, these tubes have to be the size, and they have to be held within the tolerances that we require. If they're not, there's one or two things that happen. One is we either have to fix the part or replace the part, which is going to drive the schedule down and drive the cost up because we’ve got to re-make it or re-buy it. Or two, it goes in and ultimately, you end up with something else that ends up being out of tolerance, and that impacts our customers’ integration.”
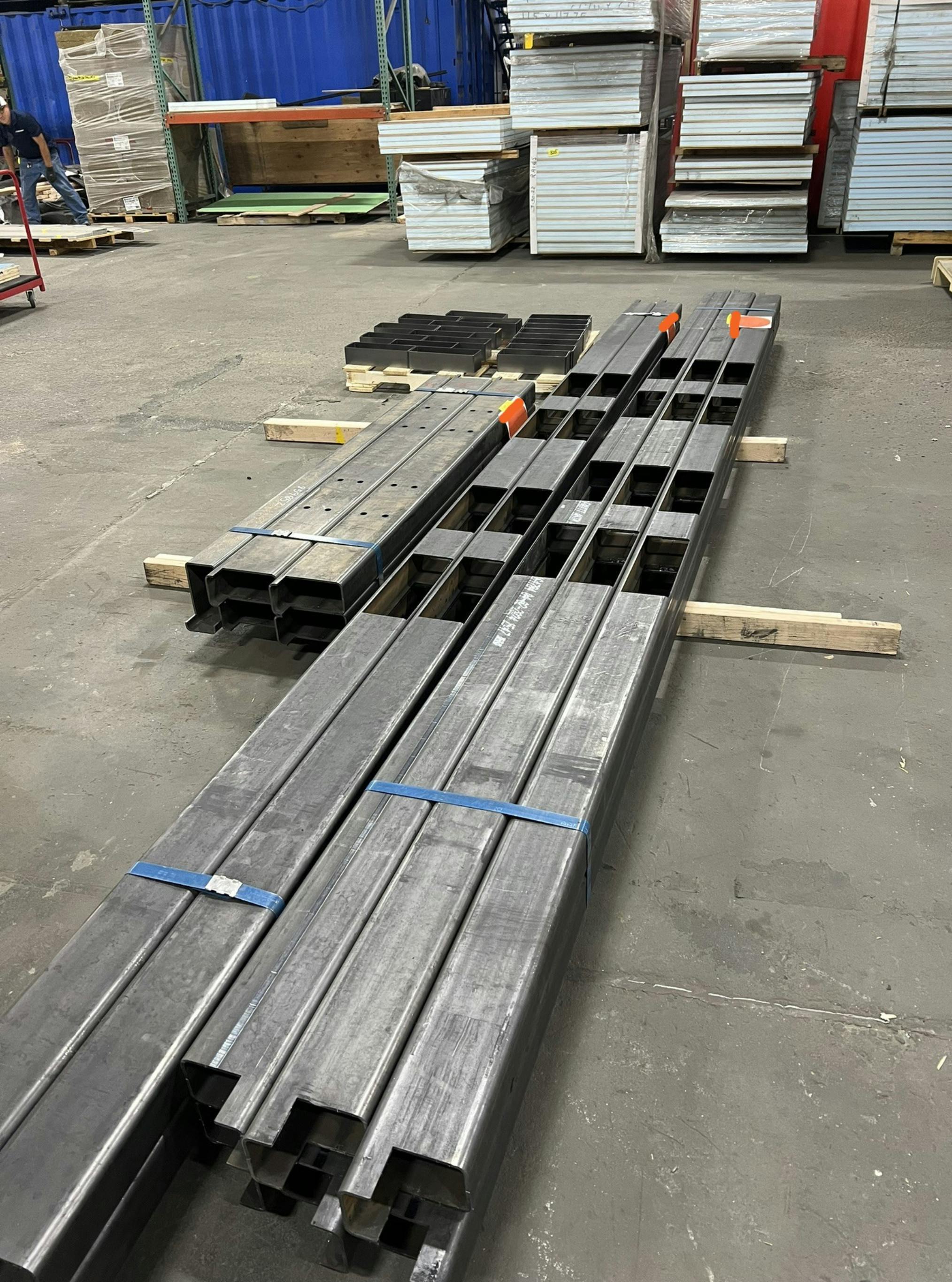
For some parts of the project that didn’t have such tight tolerances, Lucas’ team ordered tube steel cut to length directly from the steel mill, knowing they could grind off any excess in-house. But for the parts that needed to be perfectly to spec, the team turned to the laser tube cutting capabilities from Xometry.
With Xometry parts, “we can have confidence that they're going to be within the tolerances, they're going to be the material they need to be, and they're going to fit the first time without having to rework any part of the job,” he said.
Xometry Has the Laser Tube Cutting Solutions You Need for Your Next Project
Xometry offers an extensive range of laser tube cutting services. Laser types utilized include fiber laser or CO2 lasers, depending upon the material and application, allowing for very tight tolerances and the ability to cut through wall thicknesses up to 1/2“ on round, square, or rectangular tubes.
We now offer instant quotes for tube cutting and tube bending through the Xometry Instant Quoting Engine®, so it’s simpler than ever to get a quote for your next project.
Scaling Up for the Future
In addition to the ease of ordering parts and his confidence in knowing they would arrive on time, Lucas credits Xometry with making it easy to reorder parts. Repeating or scaling up a project is simple since “all the parts and all the quotes from the prototype were still in the Xometry database,” he said.
“So when a customer says, ‘Hey, we're looking for five more, how fast can you do it?’ I can say [to Xometry], ‘Take everything we already did, multiply it by five and give us the pricing, lead time, and all that stuff,” Lucas said.
His team did exactly that after the customer approved the prototype and wanted to scale up the project into production.
“For all the different parts, we were able to select the lead times that we were looking for. So for parts that we didn't need until a little bit later in the build, we brought them in later, which obviously had an impact on the cost, and we were able to use the money saved on some of that to expedite the parts we needed earlier. So we were able to get started on our build much earlier than anticipated…We issued something like 10 or 11 different purchase orders, and every single one was on time, so there were no late shipments and we haven't had to rework anything, so we were able to go right into production, which was excellent.”
Lucas credits Xometry with keeping the project on track and helping Sea Box be able to scale it up for the future. “We wouldn't have been able to pull this job off in the time frame or even on budget [without Xometry,]” he said.
Once this low-rate production run of five units is complete, Sea Box plans to scale up production further in 2025. Part of that effort may include augmenting its order with Xometry to include more parts that are pre-assembled, rather than ordered as separate components and welded together onsite. This change could equate to even more time savings that Sea Box could pass along to their customer.
