Lost foam casting is as close as you can get to manufacturing “magic”—the way it can transform a delicate foam model into a solid metal item with almost unreal precision is practically sorcery. This particular process is often used for metal casting, and while it’s certainly a popular expert technique, it’s no less a fascinating option. We’re going to explore exactly what this process is and how it works, plus we’ll explain what downsides and upsides there are and when you should use it.
What Is Lost-Foam Casting?
Also going by the names evaporative casting and the expanded polystyrene process, lost-foam casting is a technique that involves using expanded polystyrene foam as a mold that shapes molten metal and evaporates when it’s done. It came about in the late 1950s and is still a popular method today for both manufacturers and intrigued hobbyists.
The pattern for the item you’re looking to make is cut from a foam block and coated in ceramic or another covering. This keeps the product separated from the sand that’s poured around it, especially once the mold goes away. It’s similar to injection molding, but with the (intended) disappearance of the mold, it does differ in some respects. You can see how it works in the diagram below.

There are a handful of perks that come with this kind of casting. It’s a top-notch choice for creating precise parts with specific dimensions and it’s a lot simpler than other methods to do so. Because of the way it works, it also avoids flash. The disadvantages of lost-foam casting tend to be the cost of the die (if you’re using a closed-die molding method) and a higher level of porosity in your castings. You also might find that the patterns or molds tend to get damaged more easily.
How It Works
Here is a look at the step-by-step process for lost-foam casting.
- First, the foam molds are prepared. These are in the shape of the intended finished product and they get filled through a gating system with passages that allow for precise design specs.
- Next, you bond the foam pattern or mold to the gating mechanism to make sure the alignment is spot on.
- Then you’ll apply dip paint, which, when dry, creates a ceramic coating on your mold, boosting its toughness, heat resistance, and ability to handle the high temperatures of the metal.
- Once this is done, you’ll place the mold and gating mechanism (which are now one piece) into a bucket, container, or vessel of dry sand. This holds your piece in place and keeps it in the right position during casting.
- After filling with sand, the container will go through vibration to make sure that the sand fully encompasses the module.
- This is when the molten metal gets poured into the mold. The heat of this makes the mold vaporize (sorcery!), leaving room for the metal to fill in and form.
- Finally, after the molds have cooled, they’ll go through cleaning and finishing. You can also recycle the sand.
Applications
When you want an intricate or complex part with thinner walls or perhaps inner channels, you can look to lost-foam casting to get the job done. You’ll find the likes of cylinder heads, engine blocks, cooling system housings, and other engineered parts made in this way.
Materials and Metals Used
Here are the types of metals and materials you’ll most usually find in the lost-foam casting process.
- Steels and stainless steels: These alloys are popular for melting down and pouring into the mold because they're strong and very resistant to corrosion. Stainless steel is usually a touch more expensive than other metals, but its positive characteristics often make it worth the price.
- Aluminum alloys: These are often pretty affordable materials when used for lost-foam casting. Because they’re lightweight, strong, and thermally conductive, manufacturers and hobbyists often look to different aluminum alloys.
- Cast irons: Whether gray or ductile, cast iron is strong and resistant to wear, making it a good choice for this manufacturing method. This is especially true for more heavy-duty situations.
- Nickel alloys: Thanks to how well they can handle heat and corrosive environments, nickel alloys are another go-to choice for lost-foam casting. They can be more expensive, but knowing the properties of nickel and what’s needed for the particular product you’re creating might make it worth it.
- Sand: You’ll typically use dry sand to fill the container for lost-foam molding. Sometimes “green sand” is used, which is a mixture of bentonite clay and sand, giving it a soft, pliable, and slightly-damp feel.
Lost-Foam Casting vs. Sand Casting
The table we’ve put together below helps detail the differences between lost-foam and sand casting.
Details | Lost-Foam Casting | Sand Casting |
---|---|---|
Details Process | Lost-Foam Casting Molds are made from foam and coated, then vaporized, leaving the molten metal in sand | Sand Casting Molds are made of compacted sand and are removed after the products solidify and cool |
Details Complexity | Lost-Foam Casting Ideal for complex and intricate parts | Sand Casting Ideal for bigger, simpler parts |
Details Surface Finish and Tolerance | Lost-Foam Casting Smooth finish with precise dimensions | Sand Casting Rougher surface and looser tolerances |
Details Cost and Tooling | Lost-Foam Casting The upfront cost is higher, but the foam pattern balances things out | Sand Casting More cost-effective when you’re working with low to medium volumes |
Details Part Size and Weight | Lost-Foam Casting Can be used for small and large parts alike | Sand Casting Great for larger parts, especially components made for heavy machinery |
Lost-Foam vs. Sand Casting
FAQs on Lost-Foam Casting
Can Copper Alloys Be Used as Casting Material for Lost-Foam Casting?
Yes, copper alloys can be used for lost-foam casting, but they have a few unique considerations you should keep in mind. They can release sulfurous gasses during the process, leading to defects, and other impurities may crop up too.
Are Lost-Foam Casting Products Heat Resistant?
If you use a heat-resistant material to create your molds, then yes. Many of the most common materials used in lost-foam casting are heat resistant (like aluminum and steel alloys), and therefore, the end product retains this heat resistance.
Are Lost-Foam Casting Products High Quality?
For the most part, yes, you can get great, high-quality products with this method. That said, how durable they are depends on the design, materials used, and casting technique.
How Xometry Can Help
At Xometry, we have numerous services you can get a free quote for, whether you’re interested in lost-foam casting, or something different, such as die casting, plastic extrusion, or bridge molding.
Disclaimer
The content appearing on this webpage is for informational purposes only. Xometry makes no representation or warranty of any kind, be it expressed or implied, as to the accuracy, completeness, or validity of the information. Any performance parameters, geometric tolerances, specific design features, quality and types of materials, or processes should not be inferred to represent what will be delivered by third-party suppliers or manufacturers through Xometry’s network. Buyers seeking quotes for parts are responsible for defining the specific requirements for those parts. Please refer to our terms and conditions for more information.
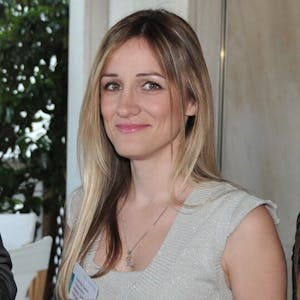