Pressure die casting is loved in manufacturing as it can quickly produce precise parts with consistent dimensions in high volumes. It allows for complex shapes with intricate details and thin walls, and the castings generally have a smooth surface straight out of the mold. It can handle tight tolerances, and produces much less waste than other similar methods. It’s compatible with a wide range of non-ferrous metals, and cost-effective when it comes to mass production.
We take a closer look at exactly how it works, the different types, and provide a step-by-step guide on how to do it.
What is Pressure Die Casting?
Pressure die casting is a type of die casting that involves using a metal mold that’s usually made from premium, heat-resistant steel grades, into which a non-ferrous metal like aluminum or zinc is injected. Basically, the mold cavity, or die, is machined into whichever shape is needed, and the molten metal is forced into it under pressure and high velocity.
The two main types of pressure die casting are low- (LPDC) and high-pressure (HPDC) die casting. LPDC requires the metal to be injected into the mold at low pressures, between around 2–15 psi, and takes a more controlled and gentle approach which takes longer because the inert gas pressure gently forces the alloy upwards into the mold. HPDC involves injecting the alloy into the mold at higher pressures, around 1,500–25,400 psi, is faster than LPDC, usually taking between 10 and 100 milliseconds to inject the alloy into the die through a high-speed ram. It’s better suited to extra high-volume production and parts that need to have very tight tolerances.
Apart from these, die casting in general can also be classified based on the type of chamber: hot or cold. Hot chamber die casting is where the metal is heated inside the casting machine. Many Xometry customers prefer this method when working with tin, magnesium, lead alloys, and other lower-melting-point metals. In cold chamber die casting, the metal is pre-heated in a furnace before being transferred into the casting machine. Our customers find that this method works perfectly with brass, copper, aluminum, and other metals with high melting points.
The pressure die casting process begins with an engineered closed steel die cavity, into which the molten metal is forcefully injected under pressure. This die is made out of two main parts, one moving, and one stationary, which are secured to the die casting machine’s platens. The machine itself has an injection mechanism on one end that uses both hydraulics and pressurized gas to propel a piston forward, and, on the other end, a clamping mechanism that uses hydraulics and mechanical toggles. The design ensures the machine can survive intense pressure during injection, and the die remains firmly closed as the metal part hardens. Impressively, this process can convert molten metal into a solid, near-net-shape part within just a few seconds. You can see all the different parts involved in the below diagram.

Pressure Die Casting Diagram
Non-ferrous metals are usually used for HPDC because they just fit the bill. Aluminum (particularly 380, 390, 412, 443, and 518) is a common go-to because it’s dimensionally stable, corrosion-resistant, electrically conductive, and able to withstand high temperatures. Compared to aluminum, zinc alloys (like Zamak 2, Zamak 3, and Zamak 5) they have a lower melting point, but they’re strong and ductile, and can be used with both hot and cold chamber die casting systems.
Magnesium is another option as it’s the lightest structural metal, highly machinable, and suitable for hot chamber die casting thanks to its lower melting point. Ideal for high strength-to-weight ratio applications, many Xometry customers prefer using magnesium (like AE42, AM60, AS41B, and AZ91D) for certain automotive and aerospace components. In addition to the aforementioned industries, these materials are also used in the pressure die casting process to make things like consumer electronics, and other decorative items that require intricate shapes or thin walls.
A few of the process’s downsides are its high initial cost and material limitations (it can only work with non-ferrous metals). There tend to be size limitations for cast parts, and it can be prone to porosity issues, cold shuts (where two fronts of molten metal meet but don’t fuse properly, creating a weak spot), and misruns which lead to incomplete castings or parts that are not fully formed. You may experience flash—excess thin layers of metal that escape and need trimming. This can be minimized, though, by clamping the mold halves tighter. Finally, it can create blisters—a type of gas porosity that looks like raised bubbles on the surface. If you try to minimize any trapped air further, you may be able to avoid this.
High-Pressure Die Casting: Designing the Mold
Once you understand the geometry of your part, as well as its intended purpose, tolerances, and surface finish, you’ll want to think about which material you’re going to use. This will determine the melting temperature, shrinkage rate, and flow characteristics, among other things. Once all that’s done, CAD software is usually used to create the design and simulate things like the flow and solidification of the molten metal. You typically have complete control over a design within CAD software, and that will allow you to foresee any potential issues, and fix them before you even begin manufacturing.
Many of our customers who design molds using CAD software will carefully plan and include a gating system and a cooling system to keep the flow intact and free from gases, as well as regulate the temperature and allow the part to cool and solidify quickly. By taking their time with these steps, professionals can create molds that will stand the test of time and endure all sorts of use.
Pressure Die Casting: The Steps
To start the process, the die will need to be designed and manufactured using high-grade steel that’s suitable for the part’s flow, solidification, cooling, and other specs. Once assembled, the die has a release agent applied to it in order to prevent any of the molten metal from sticking to it and making removing the part a nightmare. You also have to preheat the die before casting to minimize any thermal shock and avoid any issues with the flow of the metal. The die is then ready to go into the casting machine, get aligned, and clamped in place. Lubrication and cooling systems are often integrated within the die to keep the temperature optimal and everything running smoothly.
After you’ve designed the mold, these are the steps to follow:
- Start by cleaning the two halves of the die and applying a release agent. If necessary, preheat the die.
- Heat the metal in a furnace until it reaches its melting point
- Transfer the molten metal to the injection system of the die-casting machine, using a piston to inject it into the die cavity at high speed and pressure. For low-pressure die casting, use lower speeds and pressures.
- Keep the pressure consistent until the metal has completely solidified and cooled
- Once nice and solid, separate the die halves, and remove the solidified part using ejector pins
- Use a trimming process to remove any excess material from the sprue, runners, gates, or flash
- If needed, this is the step where you’d carry out additional procedures to the casting like machining, painting, or assembly
- In this final step, you’d apply any finishing touches and make sure the part meets the standards you initially set out.
Key Factors Affecting Mold Design
There are some key factors that can affect the design of your mold:
- Shape, size, and complexity of part. The more complex the part, the more intricate mold features you’ll likely need, like cores, collapsible cores, or slides.
- Material properties. These include its melting temperature, fluidity, shrinkage rate, and thermal conductivity.
- Machine specs. Machine specs like clamping force, platen size, and injection system need to be compatible with the design of the mold.
- Mold material. This can impact the mold’s lifespan and performance. The goal is to find a material that can withstand high temperatures and pressures without degrading.
- Gate/runner system design. This will affect the flow of the molten metal, ultimately having an impact on the quality of the part.
- Cooling and heating channels. If you have the proper cooling and heating channels, this will help you control the mold temperature, which has a bearing on the solidification process and cycle times.
- Ejection system. The ejector system needs to be designed with the placement and number of ejector pins in mind. That way you can remove the cast part without damaging it or the mold.
- Adequate venting. Having adequate venting is very important if you are to make a high-quality part. Good venting will allow gases to escape, preventing defects. An overflow system can also capture any excess material.
- Desired surface finish. The surface finish you’ll eventually want will help you dictate the preparation of the mold’s surface, and help you decide which mold material and coatings to use.
- Tolerances and dimensional accuracy. By understanding these in advance, you can make sure that your cast parts meet specifications.
- Expected production volume. If you’re planning on making a ton of parts, you’ll quite obviously need to make sure the mold is durable enough to keep going.
The Impact of Wall Thickness
Wall thickness has a significant impact on the pressure die-casting process. Thinner walls mean the part can cool and solidify faster, leading to lower cycle times. It requires a lot of control over the injection pressure and speed to make sure the mold is completely filled and no defects arise. There’s also the danger of porosity or shrinkage because the interior will solidify slower than the exterior.
Additionally, having uneven wall thicknesses can cause another batch of problems, like warping or residual stresses in the final part because of the different cooling rates. That’s why we usually recommend balancing your wall thickness. It will increase your chances of producing a stronger part, with less material usage, part weight, and defects, and creating an all-around high-quality casting.
Pressure Variations vs. the Final Product
Put simply, variations in pressure during the die-casting process will directly impact the final product, both in quality and in its characteristics. If the pressure is too low, the molten metal might not fully fill the mold, leading to parts that are incomplete or lacking detail on the surface. They could also come out weaker and less dense.
On the other hand, using too much pressure can cause the molten metal to infiltrate even the smallest crevices of the mold, leading to flash formation around the part—something you’ll need to spend time removing. Ultimately, using excessive pressure could make the mold wear and tear faster. That’s why choosing the right amount of pressure is really important.
How Xometry Can Help
Xometry provides a wide range of manufacturing capabilities, including 3D printing, laser cutting, CNC machining, and even pressure die casting. If you’d like to find out more information about pressure die casting, or request an online quote, reach out to a Xometry representative today.
Disclaimer
The content appearing on this webpage is for informational purposes only. Xometry makes no representation or warranty of any kind, be it expressed or implied, as to the accuracy, completeness, or validity of the information. Any performance parameters, geometric tolerances, specific design features, quality and types of materials, or processes should not be inferred to represent what will be delivered by third-party suppliers or manufacturers through Xometry’s network. Buyers seeking quotes for parts are responsible for defining the specific requirements for those parts. Please refer to our terms and conditions for more information.
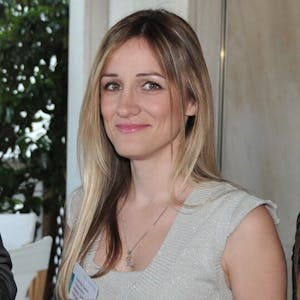