Sand casting uses a cavity formed in lightly bonded sand to form a temperature-resilient and reliable tool to allow molten metal to be formed into complex parts. It is a low-tech and relatively simple process that is commonly integrated into the manufacture of complex and technologically sophisticated products. However, it can produce variable results and tends towards low dimensional precision and repeatability other than in very skilled hands.
Sand casting is a piece of ancient metallurgy knowledge that has translated seamlessly from the Bronze Age (or earlier) to a modern manufacturing context. It is a critical tool across many industries, widely applied in the manufacture of large and small metal parts, from one-offs to large-scale mass production.
This article will discuss sand casting, how it works, its advantages, disadvantages, and examples.
What Is Sand Casting?
Sand casting is a commonly employed and very ancient metal casting technique. It involves forming cavities within packed and bonded sand that is then charged with molten metal. The chosen metal solidifies to reproduce the cavity shape in fine detail. The most common technique uses a pair of boxes into which is packed the sand, to form two sides of a cavity. It is also common to cast into an open depression in sand, for a flat-backed result. It is the oldest and lowest technology casting method for producing metal components, but it retains its relevance. The technique is extensively used for one-off, small-batch, and automated large-scale production.
The origin of sand casting lies in pre-recorded history, dating back as far as the practice of metallurgy. It was the earliest and most universal technique for metal forming. Historical evidence confirms that sand casting was prevalent in Egypt (predating the first dynasty in 3,150 BC), Mesopotamia, and ancient China. The process clearly evolved independently in disparate and unconnected regions wherever metalworking and metal refining became established.
Sand casting is hugely versatile and in many regards ideal for producing an unparalleled range of metal parts. It works well in parts as small as a few grams and up to tons in weight and is suited to virtually all metals such as: gold, iron, lead, and titanium. While sand of various types is employed in the process, these materials are required to have much higher melting temperatures than the liquefaction temperatures of metals.
Sand Casting vs. Other Types of Casting
All casting forms a cavity into which the melt is poured. The variation is in the methods by which the cavity is formed. Die casting uses a machined metal cavity for the part forming, with various approaches to introducing fill material and mechanization of the process. Investment casting uses a plaster cavity cast over a then volatilized pattern or master. Various options exist in pattern material and fill technique, from simple hand pour to full automation. Meanwhile, metal injection molding uses polymer-bonded, powdered metal feedstock, which is molded in machined steel cavities, processed, and finally sintered. Sand casting uses a variety of techniques from entirely manual to fully automated, and even automated core production/placement to form cavities using bonded sand which is then machine-charged and de-molded.
How Sand Casting Works
Sand casting works by generating a mold by forming a packed sand body around a wooden or rapid prototype master/pattern (or a part to be copied/reproduced). This mold requires features related to gas venting, fill and thermal compensation volumes, and core support, and it can then be filled with molten metal, which cools in place to faithfully reproduce the sand cavity.
With a pattern made, setting up a cavity can take as little as an hour or less, if the process is well established. Drying/curing times for best casting results depend on the sand type and can be up to 12 hours. Filling is the work of moments, and the cooling time depends heavily on the size of the parts. Very large parts (tons) can require several days of cooling.
Sand casting is an intricate process of many small steps, each are simple and easily defined and not complex to master. However, all of these steps must be correctly executed to allow the possibility of a good-quality casting at the end of the process. Figure 1 below is a summary of the general process:
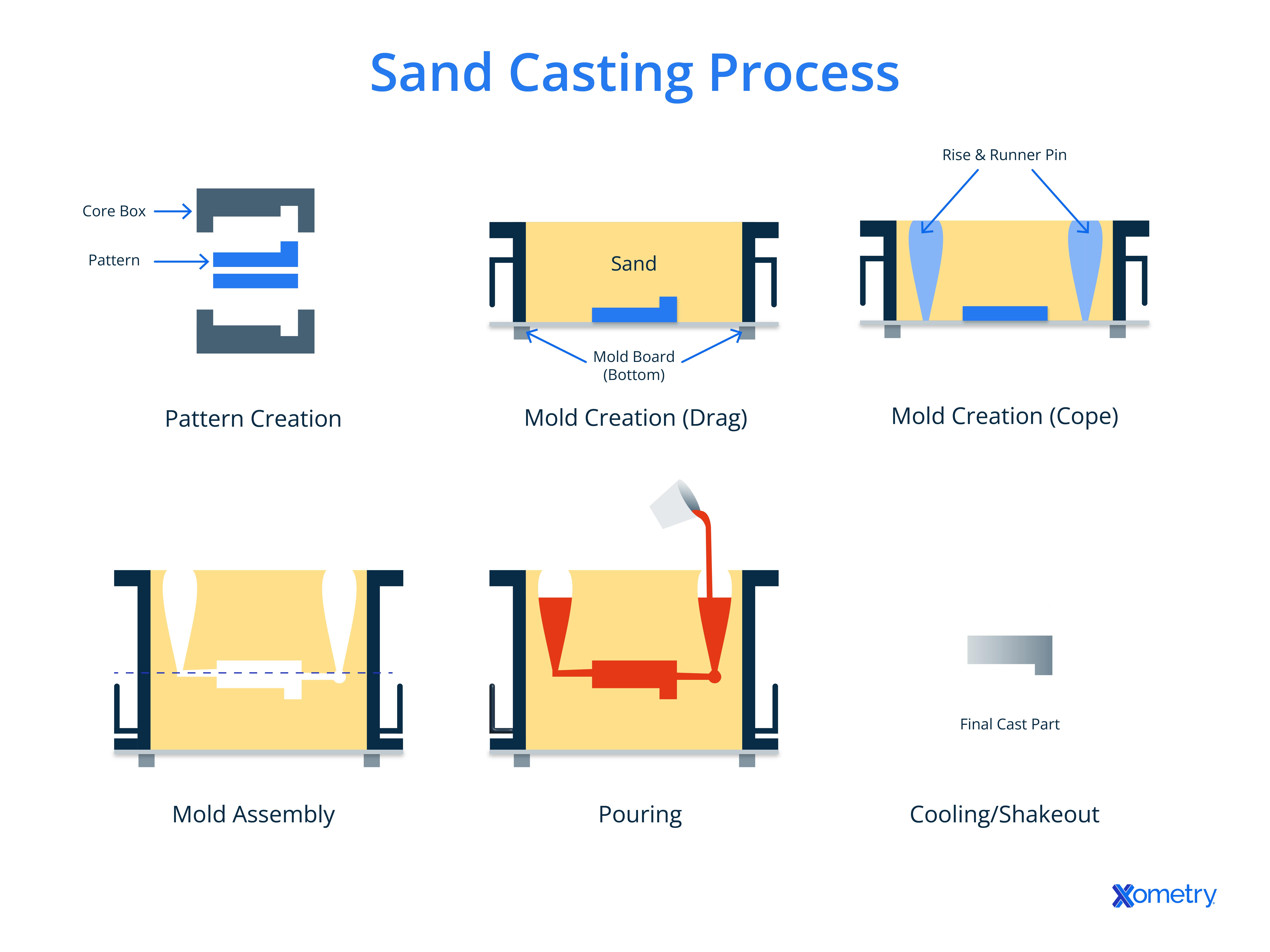
The general process is described below:
1. Position the Mold Pattern Within the Sand
The drag and cope are two open frames within which the cavity is formed. Together they make a casting box referred to as a flask. Place the drag (lower box) on a stable and robust work surface and place the pattern onto the work surface in the center of the drag, flat face down. Dust the pattern and the work surface with release powder such as talc to enable decoupling of the work surface and the pattern later. Cover the pattern and the inside of the drag with sand that has been riddled (shaken through a coarse sieve or riddler to remove clumps). Carefully ram this sand into the drag to form an integrated mass that closely fits the pattern. Complete the fill with sand and further ram this to integrate the whole. Be careful not to disturb the position of the half pattern, but ensure that the mass is well integrated. Use a strike bar to cut any bulge of sand from the face of the drag, to make a flat and smooth surface. Any stiff straight edge will suffice to cut this sand, but make sure the drag is filled with packed sand.
2. Establish the Gating System
With the drag filled, invert it to expose the upper face and the pattern. Decide where the conical feed and vent sprue positions should be placed. Trim a small receiver well and vent reservoir at each position, using a finisher tool (blunt knife or spoon). These features are small depressions that should be large enough for the sprue patterns to seat into. Cut channels from the receiver and vent wells to the faces of the pattern. This will allow the fill to flow from the wells to the cavity and the gas to escape as the second well fills. Liberally dust the entire drag surface with parting powder to allow the next stage to disengage when formed.
3. Position the Cope and Sprues and Complete the Fill
Place the cope onto the drag and position the sprue cones into the two wells you cut in the drag surface. Re-dust the surface with parting powder. Begin to riddle sand into the open top of the cope, making sure not to disturb the sprue patterns. Ram this new sand with care to not damage the drag setup but ensure that the sand is well integrated. Complete the fill of the cope and ram the sand, so that the fill forms an integrated and robust whole. Strike the upper face of the cope to produce a flat surface. When this is complete, remove the sprue patterns, being careful not to disturb the packed fill in the cope. Don’t worry about sand that falls into the hole, you can clear this later.
4. Extract the Mold Pattern
Carefully lift the cope off the drag and place it inverted next to the drag. Use a slick tool (precise repair and sand manipulation tool) to remove any upstanding features from the face of the cope fill. This is usually achieved by screwing one or more hooks into prepared holes in the flat surface of the pattern to lift it. More traditionally, draw spikes are hammered into the pattern to provide the lift “handle”. Where you cut the receiver/vent wells larger than the sprue patterns that were socketed into them, the space will have filled as you rammed the cope with fill. Cut away this excess and clean up any detritus by blowing it away. Without damaging the formed cavity, lift the pattern out of the cavity in the drag. Clean up any residues and make sure the feed channels are open and clear.
5. Vent the Cope, Reassemble the Flask, and Prepare for Fill
Using a vent rod, form small holes from the cavity to the topside of the cope. This will allow extra gas passages for venting when the cavity is filled. Make sure that the damage to the cavity is minimal. Vent the “high” points of the cavity. Try to avoid/minimize any cosmetic damage to the cavity face. Clean up any detritus by blowing it away. Clean up damaged edges of the sprue holes using a slick. Place the cope back onto the drag and lock the two halves together. Move the completed flask to the casting floor, ready to fill. Allow sufficient time (for green sand casts) for the moisture content to fall to an acceptable level. Other systems such as dry sand or furan-resin-bonded sand require less wait time.
6. Introduce Molten Metal Into the Mold Cavity
This description assumes melt has been completed and degassed. Poor degassing will result in a failed and porous casting. The crucible must be de-slagged and de-gassed completely, ready for the charge to be used to fill the cavity.
To complete this process, lift the crucible out of the furnace using crucible lift tongs. Place the crucible into the carrier tongs. Perform a final slag removal to make sure the surface of the melt is clean and smooth. Lift the crucible with the appropriate tongs that allow you to carry and tilt it with reliable precision. Carry the crucible to the flask and carefully commence the pour. Do not rush this stage; there will be steam and smoke, and a rushed pour will be less accurate, more hazardous, and more likely to erode the cavity faces and “include” sand detritus in the finished cast. Fill until the sprue holes are visibly full—this not only confirms fill but maintains some pressure to flow material into the cavity from these two cones, to compensate for initial shrinkage as the fill cools.
7. Allow Sufficient Time for the Metal To Cool
A rushed unpacking of the cast is hazardous and can result in distortion if the fill remains soft.
8. Crack Open the Mold To Extract the Metal Casting
Once cooled, unlock the cope from the drag and break out the casting and sand manually or using a shaker table. Sand is returned for re-use. Remove the casting features that are not part of the required component (sprue or feeder) by cutting with a saw or grinder. Fettle (clean up and improve) the finished part with a die-grinder or file to remove bumps from vent features, fill channels, and any sand that broke away from the cavity parts before casting.
Types of Sand Used for Sand Casting
Several types of sand methods and materials are commonly used and are listed below:
1. Dry Sand
Dry sand is a specific type of molding sand that uses clay (either kaolinite or bentonite) with very little water as a binding agent. This binder creates a mold that retains its pattern-rammed shape and withstands the pouring of molten metal without collapsing or causing defects in the casting. A major advantage of this approach is that there is less steam in the fill process that can otherwise fracture and destabilize the sand construct, or disrupt the pour.
2. Resin Sand
Resin sand, also referred to as resin-coated sand or furan sand, is a type of molding sand used in sand casting processes. Furan refers to the use of furfuryl alcohol resin. It is a mixture of silica sand or other aggregate materials and a synthetic resin binder that bonds sand grains into a coherent mass, creating a stable and robust mold for casting metal parts.
Using resin-coated sand in sand casting offers several advantages over traditional green sand or dry sand processes. Resin-sand molds are stronger and have better dimensional stability compared to green-sand molds, resulting in more accurate and consistent castings. The cure duration for furan-sand molds is shorter than the drying time required for green-sand molds. Furan-sand molds often result in castings with smoother and cleaner surface finishes due to reduced mold surface defects. Resin-sand molds are less prone to deformation or mold collapse during metal pouring, leading to higher productivity through fewer failures, low or zero steam defects, or reduced need for post-casting fettle.
3. Sodium Silicate or Water Glass
Sodium silicate or water glass casting is a specialized sand casting process that exploits a sodium silicate binder to integrate the sand for mold formation. The mold is formed in the traditional way and is dried and cured to create a more precise structure than green-sand casts. This technique is traditionally preferred for more intricate and delicate patterns, but may well be performance and cost surpassed by furan-sand casting.
These molds are less resilient in use and handling than some other methods. Sodium silicate casting is still widely used, for benefits such as: good dimensional stability, low cost, shorter curing time compared to green-sand molds, and lower moisture content at fill than green-sand casting.
4. Green Sand
Green-sand (or greensand) casting is a widely used process for manufacturing metal parts. The green appearance of the sand is due to the presence of moisture, bentonite clay, and sea coal. Sea coal is powdered bituminous coal that coincidentally washes up on beaches and is “naturally” present in beach sand as the first casting medium. This cast-making process offers a poorer surface finish and lesser precision/repeatability than more modern processes using less volatile and fragile binders.
Nonetheless, green-sand casting offers various advantages that keep it in heavy use, such as: suitability for producing the widest range of part sizes and complexities, simplicity, minimal tooling requirement, and the sand can be reused.
Types of Metals Used in Sand Casting
Sand casting is applicable to all metals other than exotics such as mercury and gallium. It is particularly well suited to high-cost/high-temperature materials such as titanium and nickel. It is most practical in the manufacture of relatively low cost and larger parts, often including some post machining to impose dimensional precision in the areas that require it. Metals commonly sand cast are: aluminum alloys, bronzes (gunmetal, nickel-aluminum bronze, etc.), steel, iron (nodular (gray), white, ductile, and malleable), brass, and stainless steels.
Advantages of Sand Casting
Sand casting, despite being an ancient process, offers advantages that render it highly relevant in high-technology production. Such benefits are:
- Versatility.
- Low cost.
- Simple tooling.
- Adaptability.
- Easy scale-up, but great for prototyping.
- Fast turnaround.
- Few design limitations, shape complexity.
- Extremely wide range of materials with few/no process changes.
- A wide spectrum of part sizes from grams to tons.
- Lower ecological footprint than most alternatives.
Disadvantages of Sand Casting
There are various disadvantages and limitations to this casting method. These are:
- The surface finish cannot be particularly fine.
- Dimensional accuracy and repeatability can be variable.
- Contaminated sand waste represents a disposal issue.
- Patterns can degrade as production scales.
- Cooling rates are uncontrolled, so there is often variability in microstructure anisotropy.
- Complex sand cores for internal spaces can be hard to handle.
- Non-automated production requires skilled labor.
- Automated production can require moderate to high costs to establish.
- Some processes offer low sand reusability and difficulty in restoring the sand condition.
Examples of Sand Casting Products
Examples of sand cast products abound in almost all market sectors, particularly in low-cost products and in heavy industries are listed below:
- Medium-speed marine diesel flywheels—can be several tons in weight.
- Through-hull nickel-aluminum bronze skin fittings in boat/ship hulls.
- Barbecue grills and burner components.
- ICE engine blocks.
- Vehicle brake discs.
- Door furniture.
- Decorative end pieces for aluminum extrusions.
- Tools used in heavy machinery and oil fields.
- Jewelry in various precious and common metals.
Sand Casting vs. Die Casting?
Functionally, the differences between sand casting and die casting are extensive. Die casting uses steel cavities, while sand casting uses sand molds. Die-cast tools offer higher dimensional accuracy/repeatability than sand casts. They also have high durability, often allowing thousands of casts before reconditioning—whereas, sand casts are not reusable. Die-cast tools and equipment are very costly, while sand casting is low-cost to establish.
Die casting also tends towards higher pressure, lower porosity, and better-compensated shrinkage than sand casting. Die casting has cycle times in minutes or seconds, while sand casting is generally much slower per part. Die casting uses a wide range of highly skilled labor, whereas sand casting is relatively low-skilled and often a single-person task.
Summary
This article presented sand casting, explained it, and discussed how it works and its advantages. To learn more about sand casting, contact a Xometry representative.
Xometry provides a wide range of manufacturing capabilities, including casting and other value-added services for all of your prototyping and production needs. Visit our website to learn more or to request a free, no-obligation quote.
Disclaimer
The content appearing on this webpage is for informational purposes only. Xometry makes no representation or warranty of any kind, be it expressed or implied, as to the accuracy, completeness, or validity of the information. Any performance parameters, geometric tolerances, specific design features, quality and types of materials, or processes should not be inferred to represent what will be delivered by third-party suppliers or manufacturers through Xometry’s network. Buyers seeking quotes for parts are responsible for defining the specific requirements for those parts. Please refer to our terms and conditions for more information.
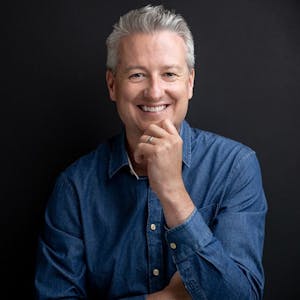