Shell molding is a casting process used to produce metal parts. The mold is composed of resin-infused sand that gives the final product a high-quality surface finish and good dimensional stability. Shell molding products are common in piston engines for parts like camshafts, valves, and gears.
This article will discuss shell molding. We’ll examine how it works, its importance, its advantages, and a few examples of shell-molded products.
What Is Shell Molding?
Shell molding is a special form of metal casting that bears many similarities to regular sand casting. Both processes see molten metal poured into a sand mold. The pattern for shell molding, however, is formed using a mix of resin and sand, which is shaped using a mold tool. This particular mixture improves the parts’ surface finish and dimensional accuracy.
What Is Shell Molding Also Known As?
Shell molding was originally referred to as the Croning process after Johannes Croning. He patented the process in Germany in 1943. Later, the process became known as “shell mold casting” or simply “shell molding.”
What Is the Purpose of Shell Molding in Manufacturing?
The goal of shell molding is to produce metal items with more accurate dimensions and nicer surface finishes than can be achieved with normal sand casting. It’s done at a good production rate and with relatively minimal labor. These characteristics are important for high-precision parts such as camshafts, for which sand casting is not accurate enough.
What Are the Industries That Use Shell Molding?
Shell molding is employed extensively in many settings within the oil and gas, aerospace, and medical industries, among others. It sees the highest use in the automotive industry where it is used for: camshafts, crankshafts, bearing housings, lever arms, valve bodies, and cylinder heads.
How Does Shell Molding Work?
The shell mold itself must first be created by placing a sand-and-resin mixture around a heated “pattern” of the part and letting it cure. The mold is usually made up of two halves. With the patterns removed, the two halves are clamped together and molten metal is poured into the cavity and allowed to cool. The mold is then often broken to extract the metal part.
What Is the Step-by-Step Process of Shell Molding?
Shell molding is a six-step process:
1. Create All the Pattern Parts
The first step in shell molding is creating a pattern part. This is achieved by first machining a metal pattern tool, usually from iron or steel, in the shape of the part you want. Usually, each pattern represents one-half of the part; a second pattern is required for the other half. If you’re casting reactive metals, the pattern will need to be made of graphite rather than metal. Figure 1 is an example of a pattern tool:
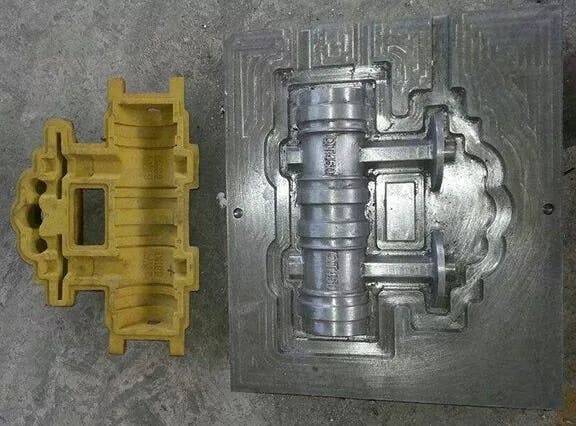
Pattern tool.
Image Credit: https://sinowayindustry.com/capabilities/metal-casting/shell-mold-casting/
2. Construct the Mold
Molds can be repeatedly made from a single pattern. Lubricate the pattern with calcium stearate and then preheat it to between 175 ºC and 370 ºC. Next, place the pattern atop a “dump box” full of the sand and resin mixture. Flip the box so the resin and sand contact the pattern; the heat will cause the resin to cure.
3. Assemble All the Pattern Parts
After the shell has cooled, it can be ejected from the pattern tool and assembled with the other half of the shell in a flask. The flask is filled with a metal shot that fills in the space between the two-part shell and the flask’s walls. Mold halves must be clamped tightly together.
5. Allow To Cool
After the molten metal is poured, it must be allowed to cool properly in room-temperature air. Any attempt to cool the casting actively and/or with liquid coolants can lead to changes in the metal’s structure and properties. Total cooling time depends on the volume and specific type of metal involved.
6. Eject the Casting
Once the metal has cooled, it is ejected from the casting. This may be done by separating the mold halves at their seam or by simply breaking the mold itself. The mold material is easier to remove from the metal if it was properly lubricated before the molten metal was introduced.
What Are the Metals Used in Shell Molding?
Many ferrous and non-ferrous metals can be used in shell molding. Some of the common ones are listed and described below:
1. Carbon Steel
Carbon steel is an iron alloy that has less than 10.5% alloying elements. Carbon steel grades that work well with shell molding include: C20, C25, C30, and C45. The benefit of shell molding carbon steel is that it is very machinable and resists wear. It is also ferromagnetic and highly recyclable. However, carbon steel is more susceptible to corrosion than other forms of steel.
2. Stainless Steel
Stainless steel contains at least 10.5% chromium. Cast stainless steel can come in several varieties: ferritic, martensitic, austenitic, precipitation-hardened, and duplex stainless steel. Stainless steel alloys are more brittle and exhibit less tensile strength than carbon steel, but they’re very corrosion-resistant and durable.
3. Aluminum Alloys
Cast aluminum alloys include: ASTM A356, ASTM A413, and ASTM 360. They may be used in place of steel if weight is a bigger concern than strength. Aluminum also has great conductivity. However, it is not as strong as steel and is considered less sustainable because the refining process creates more greenhouse gasses.
4. Alloy Steel
Common alloy steel grades that are cast using shell molding include: 20Mn, 45Mn, ZG20Cr, 40Cr, 20Mn5, 16CrMo4, 42CrMo, 40CrV, 20CrNiMo, GCr15, and 9Mn2V. Each alloy has unique characteristics. Alloy steels vary in density, corrosion resistance, strength, cost, and temperature resistance.
5. Copper
Copper is a lightweight, ductile metal that can be cast using shell molding. All copper-based alloys are suitable for casting with the exception of brass. The use of copper is advantageous in applications that require conductivity, machinability, ductility, or corrosion resistance. However, copper alloys can be expensive and weaker than steel.
6. Low Alloy Steel
Low-alloy steels are defined as steel with less than 8% alloying content. Low-alloy steels are very similar to carbon steels but are more hardenable. They’re valued because they’re cheap and perform well in most ordinary engineering settings.
How Long Does It Take for Shell Molding To Finish?
Some pattern tools are complex and take a long time to produce. Once you have the pattern in hand, the slowest part of the molding process is cooling. Depending on your automation process and the size and complexity of the mold, you may produce between 5 and 50 parts in an hour.
How Accurate Is Shell Molding?
Shell molding is much more accurate than most casting processes. Though similar to sand casting, the use of resin as a binder improves the surface finish of the sand pattern. This higher-quality surface finish is then imparted onto the final part resulting in a better-quality finish and tighter dimensional tolerances.
How Much Does Shell Molding Cost?
Shell molding typically costs around $0.25-0.30/kg. This is pricier than regular sand casting because the resin-infused sand is more expensive than ordinary casting sand. The need for more equipment to cure the resin and sand mix contributes to a higher final part price.
Is Shell Molding Expensive Compared To Die Casting?
The relative cost depends on production volume. Shell molding is cheaper than die casting for small production runs. This is because die casting requires an expensive reusable mold, whereas shell molding’s sand and resin are much simpler. However, as the production volume increases, die casting becomes cheaper since the cost of tooling is shared between more parts. Shell molding, meanwhile, continues to demand new sand and resin for each batch.
What Are the Advantages of Shell Molding?
Automating the shell molding process can be a major advantage because it minimizes labor costs. Other advantages of shell molding are:
- High-quality surface finishes and dimensional accuracy reduce post-processing.
- The resin binder is burned in the casting process, making the final product easy to remove.
- Shell molding can be used for complex geometry.
- The sand and resin mixture can be reused.
- The tooling is cheap and lead times can be short.
- Both ferrous and non-ferrous metals can be cast using this process.
What Are the Disadvantages of Shell Molding?
Gating systems are often needed to make the casting process go smoothly, but they’re expensive and generate extra waste material. Other disadvantages of shell molding include:
- Phenolic resin is expensive (although it is used in small quantities).
- High initial investment for equipment.
- Creates porosity and shrinkage of the final part.
- Post-processing may be required despite the increase in surface quality.
- Labor-intensive process when not automated.
What Are Examples of Shell Molding Products?
Shell molding has a huge list of applications across different industries. Parts are usually less than 20 kg and therefore relatively small. Examples of shell-molded products are:
- Gearboxes.
- Truck hooks.
- Cylinder heads.
- Camshafts.
- Body panels.
- Lever arms.
What Is the Lifespan of Shell Molding Products?
The lifespan of shell-molded products depends entirely on the material and application. For example, camshafts, crankshafts, and gearboxes, which are used in cars and other piston-engined vehicles, tend to outlast their cars. These parts may spend many thousands of hours in service over decades without failure.
What Is the Quality of Shell Molding Products?
Compared to other casting processes, shell molding creates high-quality finishes and impressive dimensional tolerance. Shell molding products’ longevity, wear, and heat resistance, and other performance characteristics depend primarily on the metals used in the molding process.
Are Shell Molding Products Durable?
Yes, shell molding products are durable. This is due in part to the low number of surface defects. Nearly all cracking and corrosion starts at or is accelerated by the presence of a defect. Therefore the high-quality finish of shell molding results in good durability.
What Is the Difference Between Shell Molding and Sand Casting?
Shell molds are made of resin-infused sand which results in a smoother mating face between the tool and the molten metal. Sand casting uses no such resin, so the resulting parts have lower-quality surface finishes. Additionally, in sand casting, sand fills up the whole tool container, whereas in shell molding the shell is surrounded by metal shot in a flask.
What Is the Difference Between Shell Molding and Investment Casting?
For shell molding, sand, and resin are laid over a pair of male patterns and cured. The resulting female mold halves are then assembled into one full mold into which the molten metal can be poured. In investment casting, wax is injected into a female mold pattern tool to create a replica of the part. The solidified wax is then submerged in sand or plaster and then melted leaving a female mold for the molten metal to be poured into. Shell molding makes stronger and more intricate shapes while investment casting allows for thinner walls and results in a higher-quality finish.
Summary
This article presented shell molding, explained it, and discussed how it works and its advantages. To learn more about shell molding, contact a Xometry representative.
Xometry provides a wide range of manufacturing capabilities, including casting and other value-added services for all of your prototyping and production needs. Visit our website to learn more or to request a free, no-obligation quote.
Disclaimer
The content appearing on this webpage is for informational purposes only. Xometry makes no representation or warranty of any kind, be it expressed or implied, as to the accuracy, completeness, or validity of the information. Any performance parameters, geometric tolerances, specific design features, quality and types of materials, or processes should not be inferred to represent what will be delivered by third-party suppliers or manufacturers through Xometry’s network. Buyers seeking quotes for parts are responsible for defining the specific requirements for those parts. Please refer to our terms and conditions for more information.
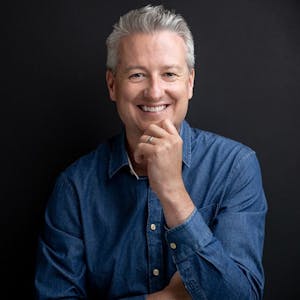