Sometimes called liquid metal forging, squeeze casting is a method used in metal manufacturing that’s a bit of a blend of two other processes: forging and casting. It’s used in aerospace, automotive, defense, and many other industries, for things like bevel gears, mortar shells, architectural domes… and the list goes on. Keep on reading to learn more about it and all its wonderful benefits.
What is Squeeze Casting?
Able to make high-quality parts at practically the exact net shape you planned for, squeeze casting is a technique that can make extremely high-quality parts that don’t go through much shrinkage during the procedure. The process involved molten metal being poured into a heated die, and then left to cool down and solidify. The die on the top closes and pushes the metal to fill out the mold cavity—it’s this part that ensures accuracy and quality, and prevents the shrinkage. Comparable to die casting in terms of accuracy, squeeze casting tolerances range from around 0.25 mm for 100 mm parts to 0.6 mm for 500 mm parts. You can see how the process works in the below picture:
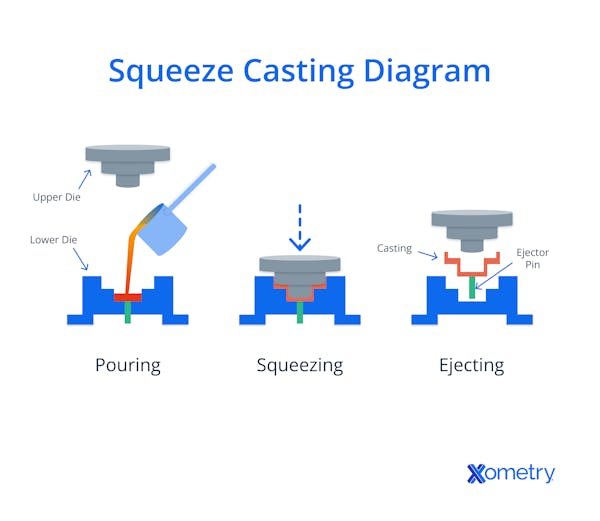
This process dates back to 1819, when it was first patented by Hollinggrak (although rumor has it that it was created long before the patent by others). Later on, in 1878, it was improved by Chernov, and consisted of 15,000 psi and high temperatures. The process was invented to try to improve on already existing metalworking techniques and make parts with better properties. And it definitely worked because squeeze casting allows for reinforcement wettability (basically bonding), mass production, and precise control over process parameters, and it enhances metallurgical quality because of the pressure used during solidification.
Advantages
- Parts are high-quality, strong, dense, ductile, and dense with low porosity
- Consistent results
- Allows you to reinforce specific areas in a part
- Repeatable process
- Parts can be further heat-treated
- Minimal (if any) post-processing required
Disadvantages
- Expensive—needs special tools/equipment
- Extensive machining needed for highly precise tolerances
- Less versatile than other casting methods, especially for complex shapes
Squeeze Casting Types
To make things even more interesting, there’s not one type of squeeze casting, but two: direct and indirect.
Indirect
For this, the molten metal is poured into a shot sleeve, which is then pushed through gates that are pretty big. It then makes its way into the die cavity at a velocity typically below 0.5 m/s—which is relatively low. The indirect part of the process actually comes from how the high pressure is applied—through the rather complex gating system. This all makes the process more controllable in terms of solidification and helps prevent any defects, but seeing as the gating is as complex as it is, you’ll end up using more material and energy.
Direct
Sometimes abbreviated as DSC (for Direct Squeeze Casting), this method relies more on pouring the metal in its liquid state inside a heated and lubricated die. The metal then gets forged as it hardens. When it starts to freeze, pressure gets applied and held there until the whole thing has become solid. In most cases, this technique is done using a vertical machine that looks kind of like a forging press.
Compatible Metals
While the process also works on stainless steel (it’s basically another metal that needs to be solidified in a controlled manner), there are four main metals used in squeeze casting:
Metal | Properties | Notes |
---|---|---|
Metal Zinc-based alloys | Properties Low melting point, fluid (ideal for intricate parts) | Notes Only suitable for cooler operating temperatures, mechanical properties don’t match those of other metals |
Metal Magnesium (and alloys) | Properties Lightweight, strong, flammable, susceptible to oxidation | Notes Temperature needs to be carefully controlled during squeeze casting |
Metal Aluminum | Properties Strong, low-density, corrosion-resistant, versatile | Notes Careful alloy selection and strict temperature control necessary for squeeze casting |
Metal Copper alloys (bronze, brass, etc.) | Properties Durable, electrically conductive, wear-resistant | Notes Expensive, limited market reach as only used in specialized applications |
Squeeze Casting Compatible Metals
Frequently Asked Questions on Squeeze Casting
What’s the difference between squeeze casting and die casting?
Basically, you can view squeeze casting as an adaptation of standard die casting, which also includes forging. Die casting machines will force the liquid metal into a mold cavity, but with squeeze casting, extra pressure is used. As we already alluded to earlier, this is what gives the final part better mechanical properties and not as many defects.
What’s the difference between squeeze casting and high-pressure casting?
It can be rather easy to confuse these particular techniques because they sound like they do the same thing. But they’re different when it comes to pressure application. In this article, we spoke about how squeeze casting uses high pressure, but even so, the pressure it uses is considered low to medium in comparison with high-pressure die casting, also known as HPDC. In even simpler terms, HPDC is an even more enhanced version of squeeze casting, and it can make parts that are even more intricate and higher in quality.
Are there any similar alternative methods?
Quite a few, but if you’re looking for the closest in terms of quality and production style, we’d say the best alternative is HPDC, mentioned earlier. It usually works really well with magnesium, zinc, and aluminum. If you’re trying to avoid the higher costs of squeeze casting tools and equipment, you could try centrifugal casting. This process doesn’t need extreme skills and can produce parts with high-quality, smooth finishes at a more affordable cost.
How Xometry Can Help
To learn more about squeeze casting and how you might be able to use it for your projects, contact us, and one of our representatives will guide you in the right direction. We also offer a whole bunch of manufacturing services, from CNC machining and laser cutting to our forte, 3D printing. Your free, no-obligation quote is just a click away.
Disclaimer
The content appearing on this webpage is for informational purposes only. Xometry makes no representation or warranty of any kind, be it expressed or implied, as to the accuracy, completeness, or validity of the information. Any performance parameters, geometric tolerances, specific design features, quality and types of materials, or processes should not be inferred to represent what will be delivered by third-party suppliers or manufacturers through Xometry’s network. Buyers seeking quotes for parts are responsible for defining the specific requirements for those parts. Please refer to our terms and conditions for more information.
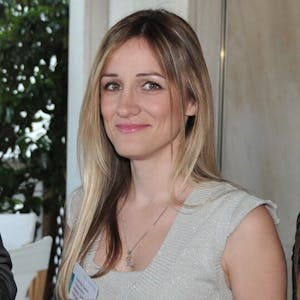