Many of the products we use in everyday life are made through injection molding, and their prototypes were most likely made using urethane casting. While both of these methods involve shaping plastics into a final product using molds, they work in very different ways. For starters, injection molding forcefully inserts the melted material into the mold’s cavities, while urethane casting typically lets gravity do all the hard work. When it comes to manual labor, though, casting is a pretty hands-on process, while injection molding is heavily automated. Their differences don’t end there. To let you decide for yourself which method is better (or better suited to your particular needs), we’re laying out all the facts on these two processes below, and there’s even a side-by-side comparison table. Read on to see how they measure up against each other.
What is Urethane Casting?
Urethane casting is the process of creating parts by mixing and pouring a liquid form of urethane—a thermoset plastic—into a mold that’s made from silicone or other soft material. The filled molds are then placed in an oven for the material to cure, although some urethanes don’t need heating and can cure at room temperature over time. Curing takes a few hours, but some fast-drying urethanes can do it within half an hour. The mold can be opened up when the material has set, revealing the cast part, which is then removed.
Urethanes need to be properly prepared before they can be cast. Most come as two-part liquid resins that must be mixed in precise ratios before being poured into molds. Once in liquid form, the material needs to be mixed with different chemicals at just the right ratios so that it will cure properly and get the desired properties, for instance, a certain color. The ratios can be adjusted for different perks like more compressive strength or abrasion resistance.
Urethane casting molds are created from a “master pattern”—a replica of the final part that’s usually made with CNC machining or 3D printing. The master pattern then gets liquid silicone poured over it. When it cures, the silicone is carefully cut in half so that the master can be taken out. This leaves behind two mold halves with internal cavities which, when put together, are identical to the final part.
A single mold can make around 1–10 parts per day, but this depends on the type of urethane used and the shape and size of the part. While the making of the master pattern and mold is fairly quick, taking only one to two days, the same cannot be said of the production process—this can take up to four weeks.
Advantages
- Tooling lead times are faster as they’re made with 3D printing or CNC machining and liquid silicone
- Cost-effective for prototyping and low-volume manufacturing
- Affordable (tooling costs, silicone for molds, urethane resins, curing agents)
- Flexible silicone molds easy to create
Disadvantages
- Urethane can break down over time, especially in extreme temperatures, UV radiation, and moisture exposure
- Low production volume compared to other methods
- Labor-intensive, manual process that drives up cost per part
- Not suitable for large manufacturing ops
- Master pattern needs expensive SLA printers or CNC machines (better to outsource)
- Silicone molds not as durable as metal molds
- Long production lead times
- Post-processing and trimming needed after part is removed from mold
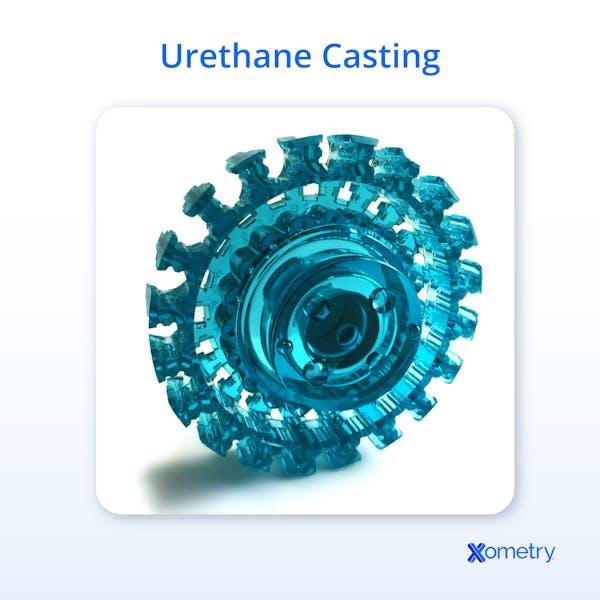
What is Injection Molding?
Injection molding is a manufacturing method that forms highly precise products by forcing—or injecting, if you will—molten plastic material into the cavities of a mold at very high pressure. The parts go through rapid cooling which, combined with the forceful material placement, makes this process very fast and repeatable, and ideal for large-scale manufacturing projects. Although it’s mainly used for plastics, there are variations like Metal Injection Molding (MIM) that use metal powders with a binder.
The molds used need to be durable enough to withstand the high pressure and temperatures in the plastic injection molding process, which is why they’re commonly made of hardened steel or aluminum via CNC machining or EDM (electric discharge machining). These methods can create cavities with tolerances typically around ±0.002” to ±0.005” and in some cases, as tight as +0.001”.
Die sets usually have many different parts like ejection pins, springs, cooling channels, runners, and gates, so manufacturing and assembling these costs a lot of money—anywhere from a few thousand to hundreds of thousands of dollars.
The longest part of injection molding is the making of metal molds because these need a lot of precision and time to perfect. They also need several machining processes and post-processes. Once they’re made, though, the parts can be made very quickly with short cycle times. Some molds have only one or two cavities, so they can make only one or two products per cycle. Others, however, can have anywhere from 50–100 (or more!) and can churn out hundreds, if not thousands, of identical parts a day.
Advantages
- Large and rapid production capacity
- Highly automated process makes price per part low
- Parts are ready for use straight after molding—no curing time needed
- Molds are durable and long-lasting
Disadvantages
- Making the mold takes a long time and needs a lot of precision
- Expensive upfront costs for tooling and die set
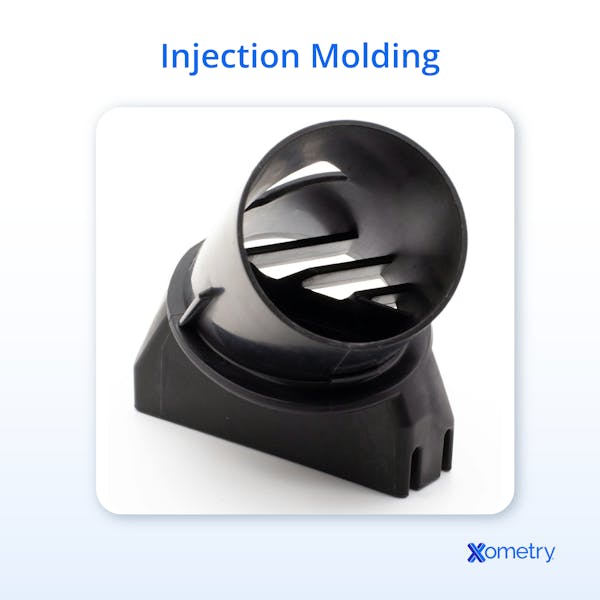
Comparing Urethane Casting and Injection Molding
Both urethane casting and injection molding are widely used and relied-upon manufacturing processes, but their pros and cons make them suitable for very different needs. To help you choose the right one for your projects, we’ve put all the necessary information on these two methods in the below side-by-side comparison table.
Factor | Urethane Casting | Injection Molding | Verdict |
---|---|---|---|
Factor Suitable materials | Urethane Casting Limited set of curable urethanes | Injection Molding Variety of thermoplastics and thermosets, metals (in metal injecting) | Verdict Injection molding is more versatile |
Factor Production volume and time | Urethane Casting 3–4 weeks (1–10 parts p/day) — best for low-volume production | Injection Molding Hundreds a day, depending on number of mold cavities | Verdict Injection molding is better for medium to large production runs |
Factor Tolerance | Urethane Casting Around ±0.010” to ±0.020” (varies with material used, part size, and complexity) | Injection Molding Averages +0.005” can get as low as +0.001” | Verdict Injection molding offers more precision |
Factor Mold lifespan | Urethane Casting Silicone molds wear out faster than metal, typically last 20–25 cycles | Injection Molding Metal molds can last decades and millions of cycles | Verdict Injection molding casts are more durable and long-lasting |
Factor Tooling cost | Urethane Casting Affordable (soft tooling, silicone molds) | Injection Molding More expensive (hard tooling, metal die sets) | Verdict Urethane casting is a lot cheaper upfront |
Factor Part cost | Urethane Casting Higher per part due to manual labor and low volumes | Injection Molding Lower due to rapid, large-scale production volume | Verdict Injection molding is more cost-effective for large runs |
Factor Applications | Urethane Casting Prototyping, bridge tooling, gaskets, casters, rollers, pulleys, bushings, shock absorbers, scraper blades | Injection Molding Automotive parts, medical disposables, food packaging, bottle caps, electronics casings, toys, kitchenware | Verdict Varies with needs |
Urethane Casting vs. Injection Molding
FAQs on Urethane Casting vs. Injection Molding
Can you injection mold urethane?
Yes, urethane can be injection molded in the form of polyurethane. Polyurethane is a polymerized version of urethane that behaves similarly to common thermoplastics such as polypropylene and polyethylene.
Is urethane a banned material?
No, urethane is not banned—although the Professional Bowlers Association did recently announce that no urethane bowling balls made before August 2022 would be allowed in the national tour because some tested below the acceptable bowling ball hardness standard. Unless you’re manufacturing bowling balls, you should be fine. While it’s not banned, there are a lot of regulations related to its use and production, especially within the European Union.
Can these two processes be used together?
Not together as in at the same time, but they can work together on the same project. Urethane casting is often used to create finished parts for small production runs or for the rapid prototyping of a product that will eventually be injection-molded for mass production.
How Xometry Can Help
For any clarifications on the differences between urethane casting and injection molding, or if you have questions regarding either process, contact one of our representatives, who will be able to guide you in the right direction. If you already know which method you want to use, you can get started today by uploading your designs to the Xometry Instant Quoting Engine® for your free, no-obligation quote.
Disclaimer
The content appearing on this webpage is for informational purposes only. Xometry makes no representation or warranty of any kind, be it expressed or implied, as to the accuracy, completeness, or validity of the information. Any performance parameters, geometric tolerances, specific design features, quality and types of materials, or processes should not be inferred to represent what will be delivered by third-party suppliers or manufacturers through Xometry’s network. Buyers seeking quotes for parts are responsible for defining the specific requirements for those parts. Please refer to our terms and conditions for more information.
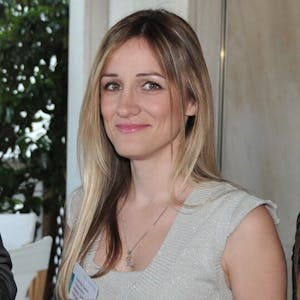