4 Emerging Injection Molding Technologies
Specialized forms of injection molding, as well as the use of new advanced software, will continue to expand the industry, allowing manufacturers to keep up with customer demand for complex, lightweight part geometries.
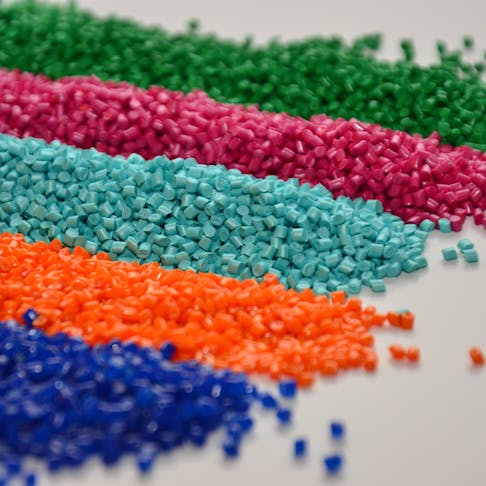
Plastic injection molding has revolutionized mass production. It allows manufacturers to create large volumes of parts with consistent quality. Since the post-war industrial boom, plastic injection processes have been refined through a combination of new technologies and a deeper understanding of the process.
Today, new advancements in injection molding continue to push the industry forward. Innovations such as gas-assisted injection have been developed to improve the injection molding process itself, and new software helps engineers streamline both design and assembly-line stages. This article will examine how manufacturers can benefit from the latest technologies.
Advancements in Injection Molding
Innovation has propelled plastic injection molding from a niche production method in the late 19th century into a modern multibillion-dollar industry. As prevalent as it is today, manufacturers continue to push the limits of the process to create lightweight, bespoke injected parts for customers. Here are four advancements in injection molding that can offer manufacturers amazing new ways to process parts and to optimize cycle times.
1. Gas-assisted injection molding
Filling complex mold shapes can be difficult. No matter the molder’s experience level, intricate molds make part defects harder to avoid. One new technology uses gas to assist in the injection process, improving the even distribution of molten material into complex molds. As with a typical injection process, the resin is shot into the mold, but in this case, only about 70% of the space is initially filled. The gas — typically nitrogen or carbon dioxide — is then injected through a separate nozzle into the filled portion of the mold as the melted resin cools. This forces liquified plastic into the unfilled portions.
Because of this gas injection, the resin solidifies on the surfaces that make up the part’s shape but leaves the interior hollow. Pressure from the gas is then relieved and the part is ejected from the mold just like any other injected part.
Gas-assisted molding offers three other benefits as well:
- It limits the amount of material required to produce the part, thus creating less waste and saving money.
- The pressurization makes surface defects like flow lines or sink marks less common.
- Because of the pressurized gas, the resin itself is less likely to shrink while solidifying, thus resulting in stronger parts.
Advancements such as gas-assisted injection molding help manufacturers mass-produce complicated shapes with ease and continue to push the industry forward as demand for lightweight, complex parts increases.
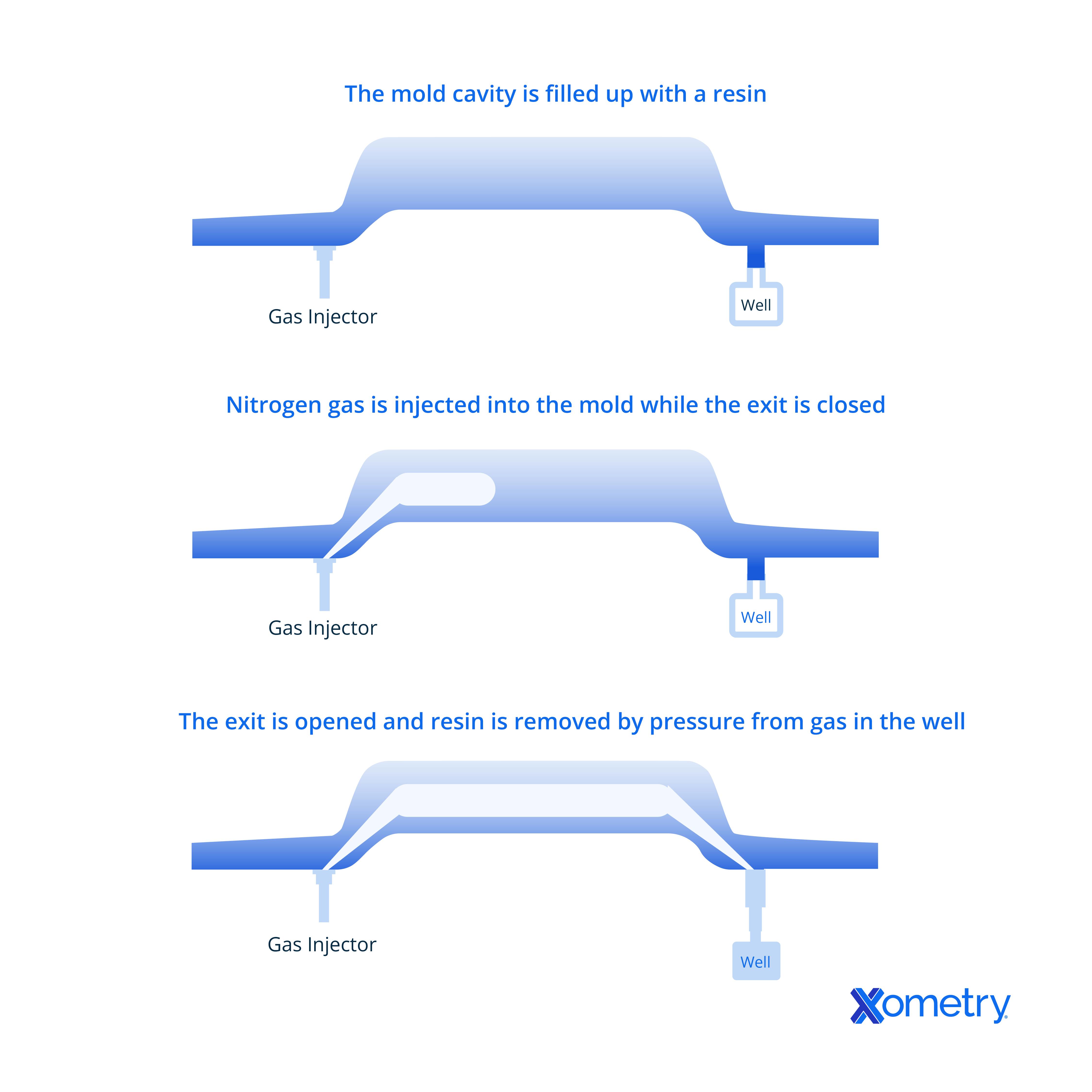
2. Structural Foam Molding
As market demand for lightweight parts increases, more metal components are getting replaced with plastic. Aside from being lighter, plastic parts are typically cheaper to make, offer better corrosion resistance, and - if engineered properly - have similar thermal and mechanical properties. Structural foam molding makes those changeovers easier.
Structural foam is a composite material made up of a melted thermoset or thermoplastic and a gas such as nitrogen. The gas is mixed with the resin and expands once the mixture is injected into the mold. What results is not a solid object, but a shape composed of two components - a low-density “foam” core and a high-density “skin” that makes up the outer surfaces of the part. Like with gas-assisted molding, the sponge-like core keeps the part’s overall weight low while the skin helps the part maintain rigidity and strength. Similarly, structural foam molding can be used to achieve part geometries and flow lengths that a typical injection mold could not achieve.
Structural foam is a cost-effective process. Because the composite material is made up of a gas-impregnated plastic melt, the molding machine can operate under lower pressures and clamping forces than gas-injected molds. This means lower-cost materials like aluminum are viable options for molds.
3. Injection Overmolding
Injection overmolding generates a single part in three steps:
- The base part made of metal or plastic is created first.
- The overmold tooling and the base part are assembled into the overmolding machine.
- A new material, typically a thermoplastic elastomer or liquid silicone rubber (LSR), is injected to form the overmolded portion.
Some materials form chemical bonds during an overmolding process while others cannot and will require mechanical features to prevent separation. Overmolded parts can be designed for either bonding style.
Overmolding can lower production costs in the same way gas-assisted molding and structural foam molding can - they allow metal components to be replaced with plastic. The parts also exhibit less shock and vibration effects than similar metal structures, thus protecting the part and improving its lifespan. Overmolding is now common in items like multicolored toothbrushes and power-tool hand grips.
4. Software for Injection Molding
New advancements in software for injection molding — things like mold flow simulation and structural analysis software — allow designers and manufacturers to simulate how a mold will fill and predict how products will fail when under load. These same programs can help engineers design gas-assisted and structural foam molds and products. Other new software for injection molding, including the use of robot-pickers and Internet-of-Things (IoT) devices, help to automate the labor-intensive process of moving components into and out of a mold.
Design for manufacturing (DFM) practices also help with injected-plastic product development and processing. When DFM is used in conjunction with new software, manufacturers can benefit from the reduced machine downtimes, lead times, prototyping costs, and tooling costs. The improvements all compound to help optimize processes and maximize revenue.
Plastic injection molding is a multibillion-dollar industry primed for continued growth as innovations and new advancements push the industry forward. Specialized forms of injection molding like gas-assisted molding, structural foam molding, and overmolding as well as the use of new advanced software will undoubtedly continue to expand within the industry, allowing manufacturers to keep up with customer demand for complex, lightweight part geometries. Manufacturers who are slow to adopt such innovations can risk being left behind as more new technologies emerge.
Disclaimer
The content appearing on this webpage is for informational purposes only. Xometry makes no representation or warranty of any kind, be it expressed or implied, as to the accuracy, completeness, or validity of the information. Any performance parameters, geometric tolerances, specific design features, quality and types of materials, or processes should not be inferred to represent what will be delivered by third-party suppliers or manufacturers through Xometry’s network. Buyers seeking quotes for parts are responsible for defining the specific requirements for those parts. Please refer to our terms and conditions for more information.
