Injection molding technology is highly optimized for speed and consistency. The entire process, from the initial plastic injection to the final ejection of a completed part, is carefully tuned to strike a balance between production speed and part quality. One key optimization parameter is mold cooling. Improved cooling methods can dramatically reduce cycle time while also improving part consistency and quality. This article will compare conformal cooling vs. conventional cooling and describe their respective advantages.
What is the Importance of Cooling a Mold?
Keeping the cost per unit low is one of the key drivers for injection molding. Apart from the cost of the mold and raw materials, one of the biggest determinants of cost is the injection molding cycle time. The cycle time refers to the overall time that elapses between the initial plastic injection and the final part ejection. However, before the part can be safely ejected, it needs to cool enough to properly crystallize (harden).
As a rule of thumb, the ideal temperature for ejecting a plastic part is 80% of its HDT (Heat Deflection Temperature). HDT is simply the temperature at which plastic will deform under a predefined load. It’s fine for the part to cool in the mold beyond this point, but that only increases the injection molding cycle time and adds no value to the process. To cool a part, cooling channels inside the mold need to direct a heat transfer fluid (typically water) around the mold cavity to draw heat from the part. These mold cooling channels must cool the part to its ejectable temperature as quickly as possible while ensuring the plastic is cooled evenly. On top of being strategically placed around the mold, these channels also need to be manufactured to generate turbulent flow. Turbulence increases heat transfer efficiency approximately five-fold and thus improves cycle times. This is easiest to achieve by rough milling the channels to create uneven inner surfaces.
If the cooling channels are not positioned properly and the part cools unevenly, it will develop internal stresses, poor surface quality, and may not maintain consistent dimensions. Additionally, if it is not sufficiently cooled before ejection, the part will likely warp or exhibit damage and will have to be scrapped.
Mold cooling is subdivided into two categories: conventional cooling and conformal cooling.
What is Conventional Cooling?
To allow for post-injection cooling, an injection mold needs to have cooling channels machined into it. In a conventional cooling arrangement, the cooling channels are manufactured by straight-drilling channels such that they form cooling circuits at strategic places around the mold. These channels are often machined to have rough-machined finishes. The rough inner surfaces increase turbulence in the flow and thus improve heat transfer capacity.
When is Conventional Cooling Used?
Conventional cooling has been used in the injection molding industry for many years and is good enough for most molding applications – especially those with relatively simple geometries. However, the simplicity of conventional cooling channels makes them inefficient on more complex shapes. Some features will not be reached by the cooling effect and will wind up as localized hot spots that don’t cool at the same rate as the rest of the part.
Relative Costs
The cooling channels used in conventionally cooled molds are easy to machine due to their simplistic geometry. Usually, they’re simply drilled into the mold, so no advanced machining techniques are needed. As such, conventionally cooled molds are cheaper than conformally cooled ones.
What is Conformal Cooling?
In a conformally cooled mold, the cooling channels follow the profile of the part as closely as possible. This means that the cooling channels are more effective at transferring heat, thus improving cooling efficiency. However, it is very difficult to manufacture these types of cooling channels with conventional machining techniques. Conformal cooling often demands the addition of cooling chambers with baffles or multi-part molds. However, metal additive manufacturing, specifically DMLS (Direct Metal Laser Sintering) has reached the point where it can be used to build reliable injection molds with these complex cooling channels printed in the most optimal positions, a feat that is simply not possible with CNC (Computer Numerical Control, which uses automated machine tools) or EDM (Electrical Discharge Machining, which removes material via electrical discharges). There is almost no limit to the cooling channel complexity in a printed mold.
When is Conformal Cooling Used?
Conformal cooling is far more efficient than the conventional style, especially since the geometry of the cooling channels can be designed to induce extra turbulence. As such, conformal cooling design is used in cases where it is difficult to achieve mold temperature uniformity and fast cooling throughout the entire mold. This is a common problem with complex geometries and thin-walled parts.
Relative Costs
Due to the manufacturing methods required, conformal cooling channels are more costly to create than conventional straight-drilled cooling channels. However, the reduced injection molding cycle time means they increase production rates, thereby improving the productivity of the mold. In many cases, the higher initial manufacturing costs are offset by overall savings from faster cycle times and enhanced production efficiency. A careful cost analysis can determine whether conformal channels are worthwhile for your product.
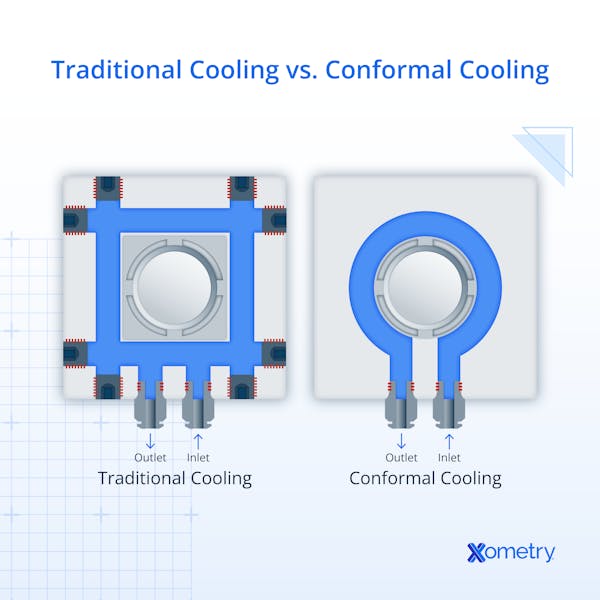
Conventional Cooling | Conformal Cooling | |
---|---|---|
Conventional Cooling Advantages | Conformal Cooling Low Cost: Conventionally cooled molds cost less because they do not require advanced manufacturing methods to produce. | Reduced Injection Molding Cycle Time: Depending on the part, conformal cooling can reduce cycle times by 30% to 50% due to improved cooling efficiency. Reduced Scrap Rate: The more precisely controlled cooling process results in fewer defects, a lower scrap rate, and better part consistency. |
Conventional Cooling Disadvantages | Conformal Cooling Poor Heat Transfer: Conventional cooling is less efficient at removing heat from the part due to the limitations of traditional manufacturing techniques. | Costly: Additive manufacturing is currently more expensive than traditional machining, so a conformally cooled mold will generally be more expensive. |
Conformal Cooling vs. Conventional Cooling
When deciding on which type of cooling methodology is best suited to your application, it is important to understand the differences between each. Conformal cooling can result in improved part quality and reduced injection molding cycle time in complex parts. However, when it comes to parts with simple geometries, expensive conformal cooling channels may be unnecessary. If the required heat transfer can be achieved with straight-drilled cooling channels, a much more cost-effective conventional setup can be implemented using methods such as CNC or EDM.
Summary
This article contrasted conformal and conventional cooling techniques applied to mold cooling in injection molding applications. To learn more about injection molding, review our Ultimate Guide to Injection Molding or reach out to us for help with your injection mold design questions.
Xometry offers a full range of injection molding capabilities to help with your production needs. For those interested in mold manufacturing, Xometry also provides advanced CNC, EDM, and DMLS services. Visit our website to explore the full range of our capabilities or to request a free, no-obligation quote.
Disclaimer
The content appearing on this webpage is for informational purposes only. Xometry makes no representation or warranty of any kind, be it expressed or implied, as to the accuracy, completeness, or validity of the information. Any performance parameters, geometric tolerances, specific design features, quality and types of materials, or processes should not be inferred to represent what will be delivered by third-party suppliers or manufacturers through Xometry’s network. Buyers seeking quotes for parts are responsible for defining the specific requirements for those parts. Please refer to our terms and conditions for more information.
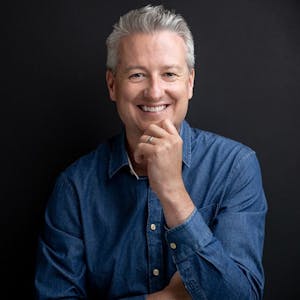