How Much Does Injection Molding Cost?
Injection molding costs from $10,000 or less to $100,000, depending on order size, part complexity, and other factors. Injection molding can be expensive to set up, but is cheaper over the long run, so it works best for large production volumes. There is a range of factors affecting the final price you would pay for injection molded parts, including the cost of the resin itself, tooling, cycle time, mold cavitation, and other details.
Plastic Resin and Additives
Plastic resins, which can range between $.90-$2+ per pound, are the primary material used in plastic injection molding, while additives can range from more expensive additives like heat stabilizers to cheaper plasticizers. When choosing a resin, take into account the following considerations:
- Use case – arguably the most important one, since it dictates the properties the base material should exhibit
- Resistance to chemical and environmental processes
- Part appearance, meaning the texture, color, and even opacity of the desired surface/part
- Regulatory concerns – which are heavily dependent on the industry or indented uses
- Part life, or in other words, the life expectancy of the molded part
The form impacts the cost of this material it is bought in, as not all polypropylenes are molding-ready. It is thus necessary to buy the plastic resin in pellet form. You may notice that engineering-grade plastics are generally more expensive (as with POM and PC). Overall though, the more materials you buy, the better your cost-effectiveness will become, as producers and distributors often have high-volume discounts which translate into better prices for your project.
The table below can be used to approximate the cost of plastic injection molding related to the most commonly used materials. These prices can vary, depending on the supplies and volume order.
Material | Possible Applications | Comments | Price ($/lb) |
---|---|---|---|
Material ABS (Acrylonitrile Butadiene Styrene) | Possible Applications Computer keyboards, face-guard on wall sockets | Comments Can be easily recycled. High-strength, general-purpose engineering plastic. | Price ($/lb) 1.30 |
Material PE (Polyethylene) | Possible Applications Packaging, grocery bags, cable insulation | Comments Lots of use cases, produced in the order of tens of millions of tons per year | Price ($/lb) 1.20 |
Material PP (Polypropylene) | Possible Applications Packaging, equipment, textiles, electrical equipment, automotive parts | Comments Excellent electrical properties and little moisture absorption properties | Price ($/lb) 0.90 |
Material PC (Polycarbonate) | Possible Applications Agriculture equipment, electrical equipment with a focus on safety, barriers/fences, storefront protection | Comments One of the stronger, more durable, and highly impact-resistant plastics | Price ($/lb) 2.30 |
Material PS (Polystyrene) | Possible Applications Laboratory ware, food packaging, automobile parts, gardening pots and equipment | Comments Preferred for solid parts that are not supposed to interact with the environment (PS is inert) | Price ($/lb) 1.00 |
Material POM (Polyacetal) | Possible Applications Precision parts, fuel caps, fuel rails, valves, filters | Comments Dubbed an engineering thermoplastic, this is favored for its high stiffness, stability, and low friction | Price ($/lb) 2.20 |
Data is recent as of 2020 and is taken from Rex Plastics
If you want to impart special physical properties to the resin you're using, or simply defray the cost of using pure plastic resin, you can add additives. Commonly used materials like plasticizers and mineral fillers are among the cheapest that can be used, while products like lubricants and heat stabilizers can cost more than the polymer itself. There is a wide array of additives that impart a variety of properties, including glass fiber, ceramic fillers, pigments, UV stabilizers, plasticizers, and antioxidants. These materials can increase strength, impact resistance, durability, elasticity, and fatigue limit.
Besides physical properties, the color of the part can also be influenced, which is one of the most popular uses for additives. These providers will also sometimes establish partnerships with the thermoplastic producers to offer customers cheaper deals.
FREE Injection Molding Design Guide
Injection Molding Tooling Cost
Injection molding tooling for a mid-level order (around 1000-2000 small parts), can cost up to $10,000. For more complex geometries and large orders, the cost can go up to $100,000.
Tooling costs depend on how complex or large your parts will be. In other words, if your part is complex (for example, if it has intricate geometry or dense walls), the manufacturer may need to use a special (i.e. more expensive) machine to complete your order.
Injection molding tooling cost increases exponentially if we are talking about a large custom-designed part. From the operator's perspective, it is preferable to use small (desktop) injection molding machines (and even 3D printers) in order to fulfill low-volume orders.
Large, industrial plastic injection molding machines can cost over $200,000 and have additional costs that are related to skilled labor training, maintenance, monitoring, and even industry regulations. These types of machines are reserved for high-volume orders.
Injection Molded Parts
Injection molded parts cost varies based on mold upkeep, the time to form a part, and factors around the plastic. These include the part rate, the estimated amount of scrap (usually 3-5%), the plastic weight, and sometimes a mold maintenance fee, which covers the cost of injection mold warranties. The quoted price should also include any setup costs for the molds.
1. Injection Molding Cycle Time
Injection molding cycle time takes up about 60% of final part cost. The part rate comes down partially to cycle time and partially to cavitation, which is covered in the next section. Generally, manufacturers will have set hourly rates they charge for their machines.
The molding cycle can be divided into two parts:
- Injection time. This represents the time it takes for the polymer (material) to be injected into the mold. It is usually a few seconds and depends on the machine's power and shot size.
- Cooling time. This represents approximately 80% of the entire cycle time. It heavily affects the quality of the end part, as it is the time it takes the material to cool and shrink.
The overall cycle time can be estimated as:
In this equation α is the thermal diffusivity coefficient and h max is the maximum wall thickness in millimeters. While the first is a material-specific constant, the latter is a design choice or requirement. As such, depending on the part's complexity, the cycle time can take up to two minutes.
As a manufacturer, it is preferable to maintain the cycle time to as low as a number as possible, since that translates into the production of more parts in a given time.
2. Mold Cavitation
Mold cavitation cost, another factor in price per part rate, increases with the number of cavities. Cavitation is the amount of identical cavities that produce parts per mold. The injection mold itself can cost thousands of dollars.
Mold cavitation is related to part size and design. If your part is relatively simple, single cavity molds are usually more affordable. However, if the part's geometry allows it, it is preferable to go for multiple-cavity molds to speed up the production process (making production less expensive over time). Larger parts may, however, not allow for this.
You can either buy a ready-made injection mold or have one made for you. Ready-made mold use is a common practice and the less expensive option, especially in the electronics industry since standardization is quite prevalent. You can also have one produced for you, which is better for unique designs.
Another aspect to keep in mind is that for custom injection molds, the geometry has to be compatible with the machine used by the manufacturer. This constraint may affect your project (and possibly design), so it is best to make sure the company you are interested in can fulfill the order.
3. Plastic Weight
Plastic weight cost includes both the plastic formed into parts and the hardened plastic left over in the mold. You'll also have to cover the cost of the plastic weight, not only in the parts but in the runner, sprue, and gate as well (the runner and sprue are channels molten plastic flows through to get into the mold, while the gate prevents plastic from flowing out once it's inside). For example, if you end up with 4lbs of parts, and 1lb of leftover plastic that hardens in the sprue and runner, you'll pay for 5 lbs.
Set scrap rates will also go into the final cost of injection molding. These are for purging the plastic injection molding machines of previous plastics from the barrel and screws as well as reloading them with your plastic.
4. Injection Molding Setup Costs
Mold setup costs include optimizing the process as well as physically setting up the materials and machinery to create your parts. These are part of the final price per part. The process will be optimized, and there may be some setup time that goes into preparations, which most companies will charge as its own flat fee. This may encompass processes like drying the resin, hanging the molds, arranging water lines, external troubles, and any type of sensors in the mold. It may also include any type of special cooling required or specific gating scheme that acts as a hot manifold system (which keeps runners hot enough to keep the plastic in them liquid).

Additional Services
Extra steps such as finishing or post-processing services, inspection, and packaging represent an additional cost to the price per part and setup fees.
1. Secondary Services
Secondary services will range in cost, though often you can get a discount for ordering both injection molding and secondary services from the same provider (this also saves on shipping costs for another facility). These may come in the form of:
- Additional manufacturing processes, including machining, drilling, and inserts
- Assembly services, including gluing and sonic welding
- Decorating or marking, including pad printing logos or other designs
Some parts may not need secondary services, while others do. The cheapest parts fall out of the machine and into a box, but others will form attached to the gate. Those require post-process machining to remove the gate, but they are used because gating makes the overall process more efficient and less wasteful.
2. Part Packaging
Part packaging costs range depending on whether you require consumer-facing or just shipping packaging. Larger manufacturers can also make use of automatic packaging, which reduces the risk of error and damage.
If your provider is expected to deliver a ready or almost ready-to-use product, the packaging used may be the one your customers get to see directly. Some providers also offer personalized packaging services for this purpose.
3. Part Inspection Requirements
Part inspection requirements costs for quality can include standard inspection or specialized certification, though specialized certification will cost more. The injection molding process itself can introduce defects of various degrees to parts (from cosmetic to critical). Some of them may be acceptable, depending on industry standards.
Trained personnel are required to validate the quality of the parts included in your order. Generally, however, if the part does not meet requirements (or expectations), the quality verification team of your provider is tasked with identifying the area and possible cause of the issue. This is, however, an internal process that is taken into account when you first make your order (no additional costs should be applied in this scenario).
Some companies offer the possibility of additional certification to your parts, at a cost. This implies the involvement of specialized engineers that are also licensed and are legally capable of offering these certifications.
Such services are vital in the case of safety-critical parts, as is the case in the automotive industry.
Saving Money on Injection Molding
Saving money on injection molding can be helpful, but it’s important to be strategic around which areas you save money in. In order to maintain a cost-effective strategy for low cost injection molding, it is just as important to identify areas where trying to save money could cause bigger issues down the line as it is to find areas to lower the cost. The following tips will help you with both:
- Be upfront with your tooling budget. When dealing with the manufacturer, it's better to be open about what you can afford from the beginning. It's important to remember that plastic injection molds are expensive, so you're not likely to save much of your budget on that part of the process. Costs will, however, depend on the application and whether you're trying to make thousands of parts or millions.
- Seek a reputable company. Many reputable suppliers have tool repair capabilities on-site which are valuable as tooling starts to wear and break. A reputable molder can guarantee your tooling will last up to 50,000, 100,000, or even up to a million cycles depending on the company.
- Reuse plastic waste. Including plastic that hardened in the sprue and runner, and that was cut off in post-processing, can help reduce material costs. However, there is a small percentage of mechanical property decrease each time plastic and its additives are recycled through, so it can't be recycled too many times. For example, glass filler fibers become shorter when they're used for recycled plastic, which leads to a decrease in properties like tensile and impact strengths. Studies show that both properties can be reduced by up to 40% after multiple recycling steps (eight in the study mentioned above).
- Buy replacement components upfront. This will be an extra cost, but you will end up spending less in the long run. Consider it a type of insurance as you are preparing for the worst.
- Maximize design efficiency. In the concept stage, it's important to focus on the basic features that ensure optimum performance of your part. You may come across elements that could be classified as "nice to have," but may not contribute to the market value of your part.
- Consider how relevant part appearance is. Glossy or shiny finishes look nice, but are they vital for your project? If they do not translate to increased sales, you can consider removing them.
- Consider insert molding. This works by inserting one product inside a mold and encasing it in plastic. This gives you the option of adopting an injection mold to two products by using inserts. These inserts can then either be removed or placed in different areas depending on the given cycle. This is a very versatile technique that can help decrease costs.
Injection Molding with Xometry
Injection molding costs can vary depending on materials, equipment, mold cavitation, packaging, necessary certifications, and additional services employed. While your project may have strict requirements for the functionality of the desired part, there are multiple ways one can cut costs without sacrificing quality.
However, to be able to do this, you should understand what exactly these areas are and how vital they are for your project. At Xometry, we offer the Xometry Quoting Engine to quickly get started on quoting your next injection molding project. Insert your requirements and designs into the Xometry's Quote Engine to get started and our experts will be in touch with you to start working out the details!
Disclaimer
The content appearing on this webpage is for informational purposes only. Xometry makes no representation or warranty of any kind, be it expressed or implied, as to the accuracy, completeness, or validity of the information. Any performance parameters, geometric tolerances, specific design features, quality and types of materials, or processes should not be inferred to represent what will be delivered by third-party suppliers or manufacturers through Xometry’s network. Buyers seeking quotes for parts are responsible for defining the specific requirements for those parts. Please refer to our terms and conditions for more information.
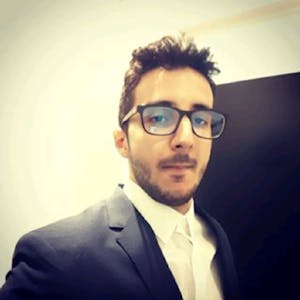