In our latest on-demand webinar, engineers from Xometry discuss the injection molding process, the best practices for injection molding, and answer questions about injection molding in a live Q&A. Greg Paulsen, Director of Application Engineering, and Kyra Stawson, Technical Sales Engineer, discuss everything from resins to drafting angles to sink when optimizing designs for injection molding.
Key points in the webinar:
- A live demo on quoting injection molding with the Xometry Instant Quoting Engine℠
- An overview of Xometry injection molding services
- Injection molding principles, including the process, common terms, and common resins
- The Molding Trinity: undercuts, uniformity, drafts
- Specific design tips, such as mitigating sink, insert and overmolding, and threads
Ready to try manufacturing in injection molding? Get a quote in injection molding now.
You can also view the webinar transcript below:
Serena Ngoh: Hi, everyone. Welcome to today's live webinar. We're going to go ahead and get started as our attendees continue to roll in. So welcome to our webinar on injection molding design strategies and on the Xometry injection molding service. Before we get started, I'd like to introduce myself. I'm Serena. I'm on the marketing team here at Xometry. And here are a couple of other quick notes. Please submit your questions throughout the webinar, we will be monitoring the question box throughout and we will answer them during our Q&A session at the end. After the webinar, we'll send you a webinar recording to re-watch or share with your colleagues. So look out for that email and stick around also for a special discount on your first injection molding order.
Serena Ngoh: So with that, let's pass it over to Greg and Kyra. I'll introduce them. So Greg Paulsen your first presenter. He is our Director of Application Engineering at Xometry. He has spent over a decade working with engineers on custom manufacturing projects using CNC machining, additive manufacturing, sheet metal, [inaudible 00:01:14] casting and most importantly here injection molding. Prior to Xometry, Greg worked in product development with a focus on rubberized electromechanical systems.
Serena Ngoh: Next up, we have Kyra Stawson. Kyra is our technical sales engineer for the injection molding division here at Xometry. She graduated from Penn State Behrend with a Degree in Plastics Engineering, and has a background in automotive manufacturing. Her passion lies in stage design of injection molded parts, which makes her very valuable here at Xometry for helping customers take their projects from start to finish. So with that, I will pass it over to your engineers.
Greg Paulsen: All right, awesome. Hey, Serena, thank you so much again for bringing a webinar together, making sure we have the right crew on board. Kyra is an awesome resource. And if you have already worked with Xometry from the injection mold side of things, you may ... let me get my video back on. You may have already worked with Kyra in the past. She's an amazing almost consultant for you when you're going through the mold stages and strategies and a go to resource here it's Xometry. Today is about injection mold. So on our agenda, we're going to start with talking about Xometry for those who are new and briefly going over the website, our quoting tool and even how you use that tool for injection mold requests. Then we're going to talk about molding with Xometry, some of the injection mold principles. So you have to know the process, understand these design fundamentals.
Greg Paulsen: And then I'm going to go through what I call the molding trinity, which are the three things I do on every single mold project and something that you can do instantly within your CAD platform. It's something that's extremely useful, an extremely useful tool for evaluating your project for mold. We're going to go into some more specific design tips and then finish up with additional resources and Q&A.
Greg Paulsen: All right. So, if you are new to Xometry, we are a company that is solving this problem of [inaudible 00:03:29]. So, we are building out a simple, elegant experience to design parts where you can upload your 3D design, get an instant price and then with that price and lead time purchase right online. So, we are making a very quick process to what typically is a very opaque situation where you're sending out to five, six vendors you may not know and getting some feedback 5, 6, 7 days later. We are very quick, we're very responsive. And again, a lot of our processes actually get instant price and feedback directly online.
Greg Paulsen: Because we have this beautiful on the storefront for getting custom manufactured parts, we also help solve this issue for local machine shops and distributed manufacturers all across the US here, which is they're looking to fill their capacity. We actually have a Manufacturing Partner Network over 3000 shops that are distributed and have different talents sets to them. Were able to pair the work that is ordered through Xometry with those shops that are most capable of performing that work. So we're able to get more competitive pricing. And we're also able to hit the quality and specifications that you require by giving those shops the work they're actually looking for.
Greg Paulsen: So it is a pair that is really fundamental within our technology platform. So the platform itself starts with the site. I'm going to take you through the site very quickly here. So actually, let's go to the main Xometry homepage. So Xometry's homepage is a resource in itself for manufacturing. I'm going to actually show you some quick tips on where to navigate to if you're looking for different technologies because we offer 11 core technology umbrella. So sometimes you may want to start off with our design guides under our resources tab. You can check out some of the videos including some pre-recorded webinars like we're doing today here on our blog, which is usually highlighting case studies and other manufacturing tips.
Greg Paulsen: Our FAQ, which is exactly what you're looking for, if you're searching for something, we're looking at that, we're creating an article around it. So it is true FAQ there, and other resources about things like tolerances, finishes or manufacturing standards, you can find right on Xometry site. Let's go and talk about this interface. Let's go and get a quote. So like I said, everything on Xometry's technology platform starts with this 3D CAD model. So once you have your 3D CAD model, you can go ahead and upload it to our website. I'm going to go ahead and add this X tile. It's just a little demo piece that we do of our logo here. And that's it.
Greg Paulsen: What just happened there was that instant pricing. So the second this is uploaded, it actually defaulted to the least expensive material to make this part a quantity one. And you can see already a standard an expedited delivery fee. In this case, it's actually looking at 3D printing technology. So this is 3D printed FDM to make this part, but I want to show you how easy is to configure to other technology. So I'm going to click modify part here. And again, you can do this with one or multiple parts. If you have a whole bill of material, you can upload all those at once as well. So you can go and preview your part here, see how its interpreted through. You could change your quantities, change your processes and even change things like part marking, inspection requirements, et cetera.
Greg Paulsen: So let's go ahead and say I'm in a prototyping phase. So I'm taking this part I'm about to bring it to mold. So maybe I want to do a fit check. I'm going to use stereolithography, which is a very accurate and very quick process that we could choose here. So I'm going to go down to one of our seven 3D printing technologies, SLA in this case. And under SLA, I have 14 different materials. I like Accura 60 as a go to staple. Has some translucency to it. Very dimensionally stable. You can see here I have my price and lead time right away for this Accura 60 part. I could change my quantity, see how the price updates instantly within our website.
Greg Paulsen: But you know what? We're talking about molding today, so let me show you how easy it to change this to a mold request. Going through our process again, you can see our 3D printing processes. We also offer machining services, sheet metal, urethane casting, and I'm going to select injection molding. So injection molding has choices. If you look around yourself right now probably actually the computer in front of you itself probably has about 20 pieces that are injection molded. It's an extremely common process with a lot of choices. So as you're looking through you see we have a very robust list of materials available. We even have custom materials and customer supplied material checklist here. You can choose from your materials a bunch of different colors.
Greg Paulsen: If you're looking for filler like a glass fill, for instance, or additives like say you need to make static dissipative, you can take a look there. Again, if you have a custom resin, you guys should write it in your notes. And also we want a little bit more information about your project needs. So what does the next six months look like for you? What do the next six years look like for you? Because that's going to help us understand what this part is going to live it. Is it a prototype? Do you really think you're going to need like 2000 and you're probably going to be done. Or maybe even like only 50 for this run. Or is it production where you're expected to have estimated annual volumes of X. And at that point, you could choose these two requirements, let's say this production tool, I'm going to keep it at 50,000 unit there, and keeps some of these other defaults save properties.
Greg Paulsen: What I've created here is a communication to the Xometry molding team. I could press request in manual quote and our team will get back to you probably Kyra actually, to discuss some more about the project. If you have any specific certifications needed, you can also add certifications. We do have an entire ITAR network so if you are working on defense related work, make sure that you are checking something like ITAR/EAR registration. A lot of times also those will compare with needs for COCs and even make some material search as well. So you can add the certification again in the upper left tag corner. So I can request a quote, it'll go to our team. Our team will review it and get back to you as soon as we can usually within that day, within 24 hours.
Greg Paulsen: That's your quoting engine, lots configurability to it, one site. And again, beyond injection molding, we do a ton of 3D printing. We have the seven different technologies as far as materials listings, probably hundreds of different materials and configurations for 3D printing, sheet metal casting, metal 3D printing, and CNC machining are all staples of Xometry's platform. So now let's talk molding guys. So I'm going to actually pass this off to Kyra and Kyra will be discussing molding of Xometry and molding as the process itself. So Kyra.
Kyra Stawson: Awesome. So thank you for that Greg. One thing I do like to talk about is not only why molding with Xometry, but why would you choose Xometry amongst everyone else. So the injection molding offers the cheapest process for you and all your at-scale plastics. It's the most consistent and repeatable process out there to produce a plastic part. We target mid-to-high volumes for manufacturing. We have the highest variety of materials, colors and configurations out there. This process does specifically amongst other processes such as thermal forming, blow molding, such as that. And also the custom cosmetics from polish to texturing. So we offer a wide range of that as well.
Kyra Stawson: So molding with Xometry. I like to call this the have it your way approach. So with that being said, we don't only focus on open close molds, we offer side action course, we specialize a lot in complex projects, such as something that has a lot of holes in it or a lot of different features, anything like that. We offer long term solutions, so we don't just focus on prototyping. Like Greg said before, we do offer a prototype tool that can go as high as a million parts per se on the tool life of that tool.
Kyra Stawson: One thing that Xometry holds a high standard to is our communication not only between the customer and the sales representative but also engineering resources. So like Greg said, I will be answering a lot of calls as well. And I am obviously an engineer, so that is not common in a lot of the industry. We do offer 24 hour quoting and DFM feedback as well. So like Greg said, as soon as you hit that request manual quote button, somebody will get back to you in 24 hours. We have a large Partner Network domestically, so that's where we default. We take a lot of pride in that. And last on the slide is that we do manage the project from start to finish. So there's only one point of contact for the customer.
Greg Paulsen: Yeah, and something to note too is just going back to our Manufacturing Partner Network is that we have this large variety. Every single machine [inaudible 00:12:48], every single manufacturer has kind of their key target audience like what type of parts they like to make, and with diversity of the SOPs, I know we have some that just love to do the ITAR/EAR work, something that just love these short little aluminum molds that offer prototypes and rapid turns. We have the whole gamut. Is that right, Kyra?
Kyra Stawson: That's correct. Yep.
Greg Paulsen: Yeah, it's pretty exciting.
Kyra Stawson: So here we just talk about a little bit about the quotes, how it's common to share within the 24 hours of receiving it from our internal quoting team to you as a customer. So, Greg, go ahead. All right, now I'm going to hand it back off to Greg. Or actually, no, I think I'm going to take over this one. Sorry about that.
Greg Paulsen: You can [crosstalk 00:13:38].
Kyra Stawson: Yeah, we can go together. That's okay. So a little bit about how the process works. So how does injection molding works? Well, first we start off with, there's a big amount of pelletized plastic resin is fed through the hopper, where then it gets fed into the barrel and the screw heats it up so it becomes a homogenous melt. It's then channeled into the tool where it's injected, and becomes the form or the shape of the part. So once you tell them there for a while it cools, and then the part is injected into a bin or a conveyor for final process and that is a cyclic process so it happens as soon as that cycle ends, it starts over again.
Greg Paulsen: Which looks like a normal cycle time usually for a part.
Kyra Stawson: Typically, depending on the size of course, less than a minute easily. Typically, we see around 30 to 60 seconds.
Greg Paulsen: Awesome.
Kyra Stawson: So some terms that we feel could be helpful. Single cavity tool is basically just having one part in a mold. So you're only producing one part coming out of each cycle. A family tool is multiple parts with similar geometries and masses if you will. So, that way we're shooting the same amount of plastic into two different parts. It might be like a left hand and or right hand of assembly housing or something like that. A multi cavity tool is just the same part over and again in a tool. Typically, you have a cheaper per piece price, if you will. But the only, I guess you could say consideration of that is having a higher upfront tooling costs. So with producing a larger amount of parts at once you have to get somewhere right? So that is the higher tool costs.
Kyra Stawson: A setup fee is a line item that you'll see on our quote. It is associated per run of the tool so once the tool is taken off the shelf and put it in the machine that is applied there. So this typically occurs whenever a customer is to come back and reorder the part that we had made the tool for originally. So gating and gate vestige. Our features on the part where the material is injected. Like Greg said, there's a ton of injection molded parts around you. If you go and look at one, you'll see a little blemish on the edge of the part and that is where it was injected at. So just really cool. Ejector pins. Again, when you're looking at that part, you're going to turn around on the non cosmetic side, you'll see a little circular features. That's where the parts are kicked out of the mold. The parting line. Again, this is a visible line as well on the part that you're looking at. It is where the two halves come together to make the part. The two halves of the mold that is.
Kyra Stawson: Then a shut off is just a term for where the mold comes together and shuts against itself to produce any plastic or prevent any press plastic from flowing out. So those are just some terms that we feel would be helpful. With injection molding, there is a lot of terms thrown out there that might not be common sense or obvious to what the description is. So we just like to share that.
Greg Paulsen: Yeah. I think we were talking about this because we're talking about the essentially mold size, right? When you think about a mold tool, it's not just the things that are the corn cavity. So if I'm moving a part that say the size of my hand, is not just something that's slightly bigger than my hand. It's a multi layered block, and two sides of that, to that have multiple assembly. So oftentimes it doesn't have parts within these assemblies, and all these mechanized pieces have a purpose. So particularly those ejector pins, where that material is flowing through from that screw auger to the parts has something called a runner, for example, and all these feet designed to have a purpose.
Greg Paulsen: So, I know I may be getting ahead of us [inaudible 00:17:32] for example, you own your tool at Xometry. So if you ordered Xometry injection molding and paying for the upfront cost, you are buying your tool, and that tool itself, I know sometimes [inaudible 00:17:46] like, "Hey, should I just hold on to them?" Let's have the motors hold on to that because that's about 800 pounds. Let's have someone who has a forklift and the crane and the proper environment to hold on to that tool, keep a hold of it.
Greg Paulsen: We usually will keep tools for two, three years, I will give a call and say "All right, so tell me a little bit about this. Has it out revved? What's the future of this?" But just know that when we talk about these [inaudible 00:18:14] injection molding, it's not just the shape, right? It is this entire assembly that goes in and has to be essentially pressed together with what we call tonnage. So it's literally when we talk about 100 compress it means I'm pressing this mold phase together 100 times in order to allow that [inaudible 00:18:33] plastic to eject in without actually squeezing out the sides and creating flash.
Kyra Stawson: Mm-hmm (affirmative). Absolutely. Thank you. And then one thing on that previous slide real quick is what I first mentioned with the family tool, we find that customers really like this option because again, it saves money up front. So instead of, if a customer submits two parts to get quoted, and they're kind of similar in shape and geometry and mass and everything, instead of getting two separate molds, which be a large capital investment of course, we have the ability to put those together. And that way we save a lot of money up front on that capital investment. So that's just one thing I wanted to mention.
Greg Paulsen: Oh yeah, it's super popular. It's something that's not commonly offered. But it's very accessible. Actually a lot of our mold makers are like that as well.
Kyra Stawson: Yes. Some common resins that are used in the industry and that we have capability of sourcing as well. Commodity thermal plastics, we find that a polystyrene or [inaudible 00:19:30], ABS, polycarbonate, polypropylene. Those are all very common plastics. Nylon too especially. And we have the ability to source whatever is available in the US. So, if you come to us and either you select polystyrene on the drop down menu, which is that PS, we can just choose a generic grade or if you come and say, "Hey, I want polystyrene, this number, this grade, this supplier," we have the capability to do that as well. So, that's one thing that separates Xometry from the rest as well as just being able to source whatever materials that you want.
Kyra Stawson: With that being said, we have the capability to do that. With coloring as well, if you have a Pantone Color, or Pantone number excuse me that you provide, we can source that. So no problem at all. Another thing I'll mention too listed under exotic or specialty resins is customer supplied resin. So I believe Greg briefed on this before but we do have the ability to receive the material straight from the customer. So from you, if you have a Gaylord sitting in your shop or whatever you're like, well, I really want to use this material on this project. But obviously our mold isn't in house, you can just ship that to us and we can use that.
Greg Paulsen: Yeah, and just something to know is because we have this network, I know sometimes there is a resin that may be only available in like China, easily available there, but it may be very difficult to get domestically. We do have the resources, especially with our material providers and compounders to even find a comparable match to offer for this difficult to source resins because sometimes resins can be the longer lead time to the actual toolmaking.
Kyra Stawson: Yes, we absolutely don't want that to be the bottleneck. Awesome. To get a little bit more specific, we've narrowed it down to a couple different industries. The first being handheld and wearable electronics. So typically we see a PC-ABS blend or just ABS by itself and this to form the housing of those parts. That's something that whenever I think of ABS, I think of those big bulky T-nine calculators, that's all ABS so if you want to get a visual. Then fixturing and brackets. So a lot of times we see a glass filled nylon or an all 10 or PEI, whatever it is it may be [delran 00:21:42] even. So we do see that specific to that industry. And with automotive gosh, there's a wide range, but to narrow it down, PBT glass full nylon, PPE-PS blend and again with that even polypropylene is common as well.
Kyra Stawson: We're working on getting a lot of notice in the medical industry as well. Surprisingly, we do see a lot of PEEK, polycarbonate and polystyrene. Even some HDPE. And we have the capability supply, medical grade, clean room produced, everything like that. I'm sure Greg you have some stories or something that touch on that.
Greg Paulsen: Stories here and there. I could just say, understanding we've been working on medical devices for a while and understanding what your stage gates are, where you're going through your trials, especially if you're going through FDA trials. And understanding when a clean room is necessary. And even what the handling part is, it's really important to get those requirements up front. You can say you're doing over scope and you have certain clean room. Also everything becomes a little bit more pricier because that staff isn't a clean room facility themselves. So even the tool makers, the designers, operators, everything has a little bit of a raise there. And the other side is any handling of the part. So let's say you're doing a double bag of the part right after molding, if that's necessary, that's added labor cost per part.
Greg Paulsen: Again, for the end justifies the means if that's a requirement, or just really importantly working on medical devices to know where you are in the stage of development, and what is necessary for this parts because we want to make sure that we're giving you the best offer possible, the best value for you.
Kyra Stawson: Yep, absolutely. Awesome. So now I'm going to transition a little bit into the tooling. So the tooling is designed around the part. It's designed around the geometry. We specifically designed the tool off of the CAD that we're see from you. So the CAD file that you upload, we prefer step. I'm going to show that out there. Step files, we just take that and that's what we start to cut the tool out of or after of. So when closed, like Greg said, is closed under high-high tonnage. The molten plastic is injected in at a very, very high pressure. So you'll see it's close together very, very tightly where the shut offs are so you can't let plastic flow throughout that. The part is quickly cooled and then the tool must open and inject the part without damage. And that's the image that you're seeing to the right of that.
Kyra Stawson: So the mold is open in this case. There's a little ejector pins are forward, that green part is pulled out by our robot, sometimes it's just ejected out and it falls down into a bin, that robots probably just going to take a two, either a secondary post process, or put it on a conveyor and let it cool just a little bit longer. If the part does have undercuts, either slide or hand-loaded-cores will create those features. So we do have capabilities of each like I did mentioned before. We can easily, easily fixture a slide or have the ability to put hand-loaded-cores into the mold to create those side action features.
Greg Paulsen: Kyra just really quick. When I talk about slide versus hand-loaded-core, what does that look like in the process?
Kyra Stawson: Sure. So a slide is used typically when we have a higher volume. A hand-loaded-core, obviously, by name, it's somebody standing there hand loading these cores into the mold. That way you know, if it's just a low amount of hands being ran, that's no big deal. But once you get into the 10s of thousands, we transition to a slide. So basically a slide is a mechanical feature where once the mold closes, there's a pin. And it basically pushes the slide into the part to create that feature, and then the plastic is molded on top of that.
Greg Paulsen: I think it's really interesting because again, hand loads tend to be cheaper on the tool side because you're not putting that automation in and you don't have this kind of horn feature that's moving that action in place. But from a part side, you do have operator standing there, so it's not a lights out activity. So and this all comes into really that what's my six weeks, what's my six months was my six year plan for this particular revision of this part. If you're in full production, you're probably going to be moving to something that's automated where it's a set it and run it setup. But if you are in something where your part revision may modify before this tool life will expire, it may be worth spending less on the tool, it will do more on those parts by these hand loads and some other tricks of the trade.
Greg Paulsen: So, I'm going to be going over again this molding trinity, which is something that so useful, and I found after speaking in the past about injection molding, that a lot of folks were using CAD don't know how powerful these three simple things are. I literally just added the screenshot 10 minutes before the presentation from my Sales Works platform here to show you a draft analysis, overall analysis, thickness analysis, it's right under the evaluate section. I'm running solid works, but I also know that in many other professional CAD programs, you're going to have similar analysis available just with the standard packages. This is not mold flow, but these are super, super useful tools here.
Greg Paulsen: So the first slide here, I'm going to focus on undercuts. And when we talk about undercuts, we're talking about thinking about this mold as an A&B side opening, closing. When I set the mold, essentially anything that ... if I'm looking face on to the part, and on the front and back, anything that's under a shadow is considered an undercut. So this part right here, for example, if I'm looking at from top down, I can see all this interior facing here at the top. If I'm looking from bottom up, I could see all the exterior faces here. But this side hole will be obstructed. It'll be under a shadow. And that means I need to somehow form that feature, but not from those two sides meeting.
Greg Paulsen: I could do a couple things there. I could just mitigate it and take that feature out and modifying in a way where I can actually just go and close the mold and maybe add some shut off in the middle or I can go and attack it with a hand-load cores or a side like Kyra is just describing here. So in actual kind of part, I use a lot this a little drone lake design that we throw up around a lot. I chose this face here, the blue face, click the undercut analysis and all of a sudden the things that are highlighted in red are showing me, hey, if I'm thinking about this as a two part mold, I have features that I can't make without adding some sort of extra action here. So, these read parts mean that an extra pool is needed.
Greg Paulsen: This part here instantly becomes a open closed mold with at least a side action whether it is a hand-load-core or slide to create essentially this face and these two holes and this slot feature here. Something to note though, sometimes undercuts can't just be attacked form the outside. So if I have something that, say, I have a sphere, and I drill a hole in it, and I have this hollow inside shell, there's no way that I can actually get a tool in to actually hold that void and then claps and get out of that area. So that would be a dialogue situation where we see this a lot of [inaudible 00:29:12] playing with wasps, or if you're playing with certain designs that have a industrial design outer contour, and so you have access port on the side.
Greg Paulsen: Sometimes if you run and undercut analysis, you'll see like a little red area right at the top of the dome. And that's just a place where you may want to either modify the design, or maybe add a little wall thickness there that'll help you hit right into the draft and mitigate the undercut. So dialogue again, it just means that I can mold it once. I just can't take the molded part afterwards. So it's not something that we prefer to do or that will ever move forward with the mold without some DFM changes there.
Greg Paulsen: This also is a great tool for showing where the parting line is going to be and helping you think about how to attack the parting line creatively. So the second that you choose a face, you're going to see some things highlight, some things not highlight. And I have example a couple slides ahead of us that shows what that will look like where you could definitely see that parting line there. It's a really useful tool for us. And then, again, best practice. You want to save costs. You want to focus on your design intent is while mitigating the need for things like site actions or slides because it just adds time and adds cost to your part itself. So this slot example here, or this, sorry, the snap time example here is a good example of making a feature like a pass through the core.
Greg Paulsen: So if I did an undercut analysis on this face, this whole area under shadow would not be something that I can access with a open close tool, but by adding a hole at the base here, so basically a little rectangular feature. And again, parts in front of you probably have this right now, we can actually put a rectangular tab on one of the pieces of the mold and close it up and creates a shut off that will actually help create this feature when it opens up, you have your snap [inaudible 00:31:12] feature. So that's something called a pass through core. It's a really really powerful mindset and tool use when you're designing for injection molding. They are your friend.
Kyra Stawson: Absolutely.
Greg Paulsen: Sometimes honestly the mentality is all right, I got my design. Now let's get the undercuts and see what I can do with passers, and you start kind of chopping away and so it really does spur some creative juices sometimes. So it's-
Kyra Stawson: Yeah, not to mention or to pick off on that. If you do have an undercut of course there's going to be costs associated with that. So if you are able to design around it and mitigate it, like Greg said, then you can reduce the per piece price and the tooling cut price so it's a win win.
Greg Paulsen: Absolutely. The second check I have there is a wall thickness. So I'm not going to go in this presentation, the details of what a good wall thickness is because it's so dependent on different materials that you're using. Some materials flow better can make really thin features. Some materials are a little bit more viscous when they're being injected under pressure. So they actually light some pathway there. So maybe like a two millimeter thickness or something where they can kind of move through. I know we're using a glass bowl polycarbonate that was kind of favored thick to actually move around into a part design there.
Greg Paulsen: But just understand that say I have something that is designed like a top hat. So we're getting my little upside down top hat here. When I build a design like this, and it 3D prints well and machines well, not a problem in the prototyping stage. Once I move the injection mold, understand that you cannot argue with plastic. You can't be like ABS, today I want you to be different. It's always going to act like [crosstalk 00:33:00]. So you want to come back and take a look at your design and look at these differentiation between your nominal wall thickness and a fixed section here. And again on my little drone way you can tell I have like kind of like some thicker areas here and here. And even this mid wall here is thicker.
Greg Paulsen: And what that's going to do is it's going to cool slower than the rest of the parts. This nominal wall thicknesses are actually going to cool at the at a very even rate or predictable rate. We have these thicker areas. They are cool slower, and when it's cooling up, that material shrinking, it's pulling. It'll pull everything else around it. So with this hot app design here is going to have a little dimple. Sometimes this looks like a straight line, sometimes it looks a little thumbprint, sometimes it looks like a void where you actually looks like a pothole and that's where it actually crystallizes, freezes off on the outside but it leaves some stuff on the inside because it's actually cooling from inside out. So we want you to make coring. We want you to use ribs. We want you to use even wall features to design the mechanical functions your part versus just making a part thicker for example to add stiffness to a part there.
Greg Paulsen: I always talk about customers when we talk about strength about the plastic forks and knives that you get at picnics. You can cut a steak with this plastic knife. And the reason why it's not because that knife is thick. It's because it's designed with the proper ribbing. So it's almost a T shaped in a cross section. It's engineered to actually perform the way that needs to perform. So it is keeping those principles of even wall thickness while also having mechanical function through design.
Greg Paulsen: So yeah, again, like looking at this part here, I have some sink marks, I have some places where very likely I'll have some dips and even this thick area right in the middle. So thing is a kind of a center rib, we'd probably see if I didn't mold this part as is, see a little pothole here, a little dip here and I probably see a little depression line going down lengthwise on this part because what's going to be doing is pulling from somewhere and it's going to end up affecting my outer wall surface there.
Greg Paulsen: So just to understand that that tool is really useful. Find your nominal, put that in, look for overly thick features, press calculate, last couple seconds and you get a really nice output about where to attack. So we talked about undercuts, wall thickness and now the last check that we have is draft angles. It is actually the required thing that we need for releasing apart from the mold by put it last because a lot of times you want to fix your file for moldibility first, fixing those undercuts, fixing the wall thicknesses and then draft your part. So that's why I have as kind of my last check. You can do these at any time during your design stage though.
Greg Paulsen: Think about if you had ... let's think about stacking solo cups. So stacking solo cups and cups, I can take two fingers, take one solo cup out. The second that moves a millimeter up, it's now released from the solo cup underneath. It has that angle design. And that's kind of what we're looking for in draft angles. Now think about stacking paper towel rolls. And if you're trying to shove paper towel rolls into each other and take this out, it doesn't work well. And it's the same principle in injection molding that if you have something without draft, what's going to happen is I can melt plastic around there. The plastic again, plastic will behave like plastic. But the second I try to actually open up that tool, it's going to drag that feature likely to form or look like or create what looks like what a scrape marks to it. It's not good for your part. It's not good for your tools. It's not good for repeatability, consistency or anything that we really stand for here at Xometry.
Greg Paulsen: So we're going to ask you about drafting, adding draft angles to your parts. And as part of our DFM feedback that we have. Understand that one degree is usually a good rule of thumb about, would you say about a dripper inch, Kyra something like that?
Kyra Stawson: Yeah, just about. We do request at least one degree. Again, it could change for different locations or features on the part like for instance, shut offs. Ideally, we would like more than that just because you are shutting steel on steel. So it could be a little bit more abrasive right? Exactly. So it can be a little bit more abrasive. So we do request maybe three to five there but uniformly across the part on ribs or other features, that one degree is ideal.
Greg Paulsen: Yeah, and I even be looking like yeah, increased draft angle. So there's a part of that we did very beginning looks like this blue part actually. I had for Q&A and don't forget guys, anytime during this, write some questions down. We're going to answer them shortly here. But I have a little part here that has a ... it's empty 1020 but the mold texture texture to it and it gives a kind of a matte outlook. But on the side it actually has a finer matte finish. It's actually in one of our SPI finishes, so it's the SPI B3 on the side here. And the reason why was the angle of they needed to design this part they couldn't do the MT texture because usually about three degrees draft in order to release it without those cosmetic pool marks to it.
Greg Paulsen: We ended up keeping it very nice and matte and making the part of a consistent where the cosmetic phase had that mold texture and while the sides actually has more of a matte finish like a beat glass finished to the side there. So we can again do clever things to this. So sometimes it's just change your texture here if you need that draft angle. Sometimes it's add draft in order to get that texture. But understand texture does usually add a degree or so for proper release. So let's put it together. So I have this drone like here. I was doing these checks, right. I was like, "All right, so this guy ... we need to put it on a diet, we need to send it out areas a little bit." So added some [inaudible 00:39:19], chopped away a little bit. You can't see from this side, but I took out some material from the bottom here.
Greg Paulsen: Also, talking about the draft position. So in my mind, I looked at undercuts, and I said, "You know what, I think that I should actually have a parting down the center here." So I went in essentially made this part as if I was making half the part, drafted it appropriately and then neared it, because this is a mirror image here, to make the other half. So you can see I have a draft. On one direction draft another direction with the intent of a parting line going down the center to create most the body of this and then a side pool. So a side action, creating this flat face here.
Greg Paulsen: [inaudible 00:40:01] side action, that also means that these edges, so any edge that I actually want to create using the pool here, I need to make sure I'm drafting for that direction. So there's actually three directions of pool with this part here. So you can take a quick look and by doing this, this is probably this part from about 70% to about 92% ready to be molded. And then a few quick tweaks and we're ready to get going with the design.
Greg Paulsen: Honestly, this design is probably good to go. I was actually criticizing myself about a little bit more here that I could have done. But otherwise, this is something where we did this exercise and probably within like 25, 30 minutes, we had a modification of a design from a CNC designed to injection mold. So it's a really great way to get started and understand principle of molding.
Kyra Stawson: And one thing that, real quick on that is we do pride ourselves on offering feedback and guidance in your designs as well. So we are here to help you along the way that's typically ... I do that a lot. So that is typically one of the major roles in my job here at Xometry is to help the customer and help you understand, maybe make this tweak here make a little bit more multiple or reduce costs or whatever we can do to help you get that part across the finish line. So we are here to help.
Greg Paulsen: Yeah, we always talk about making parts like 3D printing is kind of dating and injection molding is a marriage. You want to find the right spouse. And I think that's where really if you look at the feedback from Xometry, it's all about the service aspect that we give. We have this really slick interface that makes it as easy as that click drag, upload and buy. But really what that does is it gives us time to really focus on the parts of the project. And our goal is not to make parts, our goal is to make your project successful. And so that's what we really have a mindset for.
Kyra Stawson: Absolutely.
Greg Paulsen: So these are some cool tips. I didn't want to overcrowd the slides because they already overcrowded. So I have a few tips at the very end here. And then like I said, we're going to go over some resources Q&A. But I found this really useful. It's something I actually wish I knew when I was in product development about five years ago on how to use ribs and bosses because we talked about uniform wall thickness. And usually I'm trying to spot over thick features. A lot of times, that means when you're designing everything and all things equal in rib thickness, you still may get something like a show through on your design part. Actually, even on that blue part that I have right there, I can actually see a small little ring where a rib feature on the inside shows you a little bit but the mold texture almost completely negates it, but it's just something that does exist because again, you can't argue with plastic. You can't say no, this time don't think. It's designed in [inaudible 00:42:58].
Greg Paulsen: By making your ribs 40 to 60% of the outer walls. So say you have the outer wall, it's 100,000. And if you make that rib at about half of that, you're probably going to still have good structure. You're going to allow material to flow through. And it actually will have a lot less chance or a lot less show through on the other side, a really good example is i'm making a panel and say I have a grid pattern on the on one side of ribs, making those ribs thinner will help not show the grid pattern on the other side. Sometimes if I'm making something that's for construction or mechanical, it doesn't really matter. It's all about stiffness and strength anyways, but if you're looking for something that has a cosmetic showcase finish to it, is something to really consider.
Greg Paulsen: Other side draft still apply so if you have a really tall part and a really tall rib, sometimes that drafting will get so thick at the boss that you need to really consider that. And there's some tricks and even sometimes we just need to reduce the draft angle necessary and do a little bit more careful tooling strategy with that, but it's just something to understand is that if you have something really, with really deep draw and you're drafting it, that thickness at the base is going to be thick because of the draft angle and that the very top.
Greg Paulsen: The boss trick that I really like is sometimes when you're making bosses, if you look on the other side of your part, and again, there's probably like three parts in front of you that you could see this on. You'll see a little donut shape, a little donut shape depression, and that's from these ... So the boss is essentially a cylinder. And what will happen is that the material here, even though you're following all these good wall thicknesses, if you imagine this as a sphere, like there's actually material at this point in here, and it's going to be pulling in as it's cooling, a little bit more material creating a depression here.
Greg Paulsen: What you want to do is kind of relieve that and you could do that by thinking about your part as 100%. If you make the inside your boss at that 30% so again if I'm talking about something that's 100,000 and I make my boss 30,000 deeper as well as create a group move that is 30,000 deep and then goes up 30 degrees here so basically a ring around the boss there, you can actually significantly mitigate and sometimes negate sink showing through on this part. It's a really neat trick. It even works if you have ribs so if you have a boss that's kind of designed like a rocket ship there, you have some fins coming out. You can do that just the fins actually have to go down and meet at the bottom there because if not, you create an undercut or bank of other gods.
Greg Paulsen: But otherwise, it's something that's very, very useful. And especially if you're using something as showcase and use I'm doing that I suck that 50, 100,000 thousand, 1 million production mold, it starts to become much, much more useful for you.
Kyra Stawson: Absolutely.
Greg Paulsen: Again, I want to say going back to sinks. You can't argue with plastic, sometimes it wins. But depending on what materials and what your application is. I have a couple workhorses at home, some new stands for wood cutting and stuff, and they are full of sink. But I don't care. I have two by fours in them, and I could hammer away and they're absolutely fine. So it's application depending on what's really matters most of your project. Other couple items I want to talk about very briefly and we can answer some more questions about this in the Q&A as well is a mold inserts and overmolds.
Greg Paulsen: So we do insert molding and we also do a overmolding. Insert molding would be like for example, this is a CNC machine part that we put an elastomer and automotive it on here. So this is where I'm taking a part. Sometimes it's off the shelf, sometimes it's custom manufactured and I'm actually molding plastic around it. The thing to understand is that metal and elastomers don't usually bond well. So you want to add mechanical features. So if I had an X ray to this, you would actually see that this has what looks like a few O-ring groups on the metal part there. That allows me to mold this molten plastic around it. And it also will build this grooves creamy, an actual mechanical joint where it's difficult for [inaudible 00:47:23] move.
Greg Paulsen: Same thing with overmolds. So overmolds, sometimes you can do flat on flat overmolds where you're adding say an ABS with a TPE material. And there is a little bit of a chemical bond that happens there. But if this thing is going to head anywhere and you want to do risk [inaudible 00:47:40], add features. So for example, a little dovetail features, anything like through holes, anything that allows that material to actually inject through be exposing the other side and create a mechanical attachment there. It's just very useful. It's something that we see a lot where we can see the design intent. We used to go in and say, go in and ask for some more mechanical features. It's the exact same thing if you're bonding parts together. Physically, you know up in the part seeing something else scratch up those surfaces in order to add a little bit more friction there. And I'm doing the exact same thing when I'm when I'm designing mold.
Greg Paulsen: The other side of this is so just by the way, you can insert mold inserts or like threaded inserts, something that you may sometimes ultrasonic or heat stake in. Sometimes it's best for us to do that in mold, depending on what the throughput is needed for these parts. You can do that. We could do that on molds as required. I wanted also mentioned that when you're talking threads in general, we can tap for consistency sake and labor sake, I would actually go on to insert because it's much higher throughput, and usually cheaper and more consistent. The other thing is that if you have external threads, external threads actually tend to be dragging well. You have these little triangles there. So if I actually attack an external thread with a parting line down the middle. Most the time, I'm like one small radius away from being able to actually make that a two part mold as a feature.
Greg Paulsen: But that being said, I will have a parting line up those ridges there. I recommend, and you'll see some best practices where you just take a little cut, essentially shave off the two sides of this. And you may see those again, parts in front of you right now that may have this feature. And that will actually mitigate where that parting is, so it doesn't interfere with what it's going into. So that's that's some considerations, but just something that we get asked a lot. And again, we can go into further detail with that. I want to save yet 10 minutes or so for Q&A. So I did show you the site. We have a resources page. We also have live engineering support. If you go to our chat online, we're open 8 AM to 9 PM Eastern. You always [inaudible 00:50:00] contact us from prone and you have a dedicated account representative.
Greg Paulsen: We have a great injection mold design guide Xometry.com/resources. You can take a look at design guides for all our processes, but definitely worth checking out here. And Serena.
Serena Ngoh: Already. Thanks everyone for sticking around. So I'm here to close us out with a promotion as well as Q&A after this. So if it's your first time ordering injection molding from Xometry, please feel free to mention this coupon code new mold order to get $500 off your first Xometry molding order. And now for Q&A. We had a couple of questions come in here. So let's start with talking about the Xometry injection molding suppliers. So what is one point of contact mean? Because customers and what happens when there are multiple types of parts do you send it to various suppliers and does the customer have a role in managing those various suppliers which is obviously not ideal.
Greg Paulsen: Kyra, do you want to [inaudible 00:51:08] this one?
Kyra Stawson: Yeah, sure. So, what one point of contact means is your account representative is your primary point of contact. Now once the order is placed, we do transition to a project management role and then that becomes your single primary point of contact. So once the sale is handed over and it's closed, then you will have a project manager leading your project. And with that being said, there is no supplier/customer interface. It all goes through Xometry. We are your single point of contact, there is no management on your end, we handle everything and with that being said, obviously communication is desired. So we do provide significant communication as much as you would like. If you don't want any at all, great, we'll still email you and let you know what the status is or if you want to talk daily, we are open for it. So we basically want to make this customer first mentality. We want you to be happy and feel comfortable working with us.
Greg Paulsen: Yeah. And Kyra also on that, do you want to talk about just kind of kickoff? So what happens once a PO comes in? Just very briefly.
Kyra Stawson: Yeah, sure. So once we receive a PO and the order starts, the lead time that's listed on the quote begins that business day after the PO is submitted and processed. At that time, within those first two days, you'll have that project manager reach out to you introduce themselves, kind of have a kickoff meeting, if you will, and then they'll set aside some time for a formal DFM process. So that's basically where we identify the party lines, the ejector pin locations and the gating locations and type. So we do dedicate this first two days in that. That is all built into the lead time. So there's no delaying or anything as long as it's completed within those first two days.
Kyra Stawson: And of course, on your end, as the customer you would approve that and then we move forward with cutting the tool still. So that's what it looks like right after kickoff and again, that communication is our number one priority. So we want to make sure you're satisfied and feel comfortable with every step.
Serena Ngoh: Great. So you guys answered two questions in one.
Greg Paulsen: Oh, really? All right.
Serena Ngoh: All right, next question. So you mentioned drawings with respect to tooling. Does Xometry need to see to 2D drawings to understand the design intent and tolerances?
Greg Paulsen: Tolerances if they're nonstandard, that the answer is yes. So if you have critical tolerances where these are fitting in this assembly and they need to hit this degree, we definitely want to be mindful of that. If not, we are working on standard machining tolerances to make that tool which is going to be usually like a plus or minus four to making that tool but then again, keep in mind the tool is designed with some scaling and offset for the shrink rate of the material itself. But then your design plus material plus tooling is what you actually get in hand. So that's your part. So if there's anything we’re going to be mindful, we just want to make sure we are aware of it or else you're going to be working with global generalized tolerances which isn't bad at all. It just means that it's something that we want to be mindful of with drawing.
Kyra Stawson: To carry off that real quick. I know we talked a lot about over molding and insert molding. So we do require a drawing with those just to understand where that part starts and where it stops and where the next one starts and stops. So just keeping that in mind as well.
Serena Ngoh: Okay, thank you guys and what about small vertical walls that are a few millimeters or less do you need to add draft ankles still?
Kyra Stawson: Greg, you want to take that one?
Greg Paulsen: Yeah, you should, there's still … it really depends on the process because it absolutely can get away with releasing some materials without need for draft to that. My biggest worry there is in that I'm doing ... so we have one degree as a standard, but even if you're getting a quarter degree on these really small walls, it's super helpful because the worst thing that can … what I don't want to happen is a piece of your part getting stuck into the tool in that little wall there, because there's two things that will happen first off, that it'll show on every part until we catch it like a missing feature there. But also you got to dig it out, of the may damage the tool, especially if you're talking about a really thin wall, a wall like that. If I scratch the tool, then that scratch shows on every single part made. So we want to be very mindful about our designs. From an end to end standpoint. We look at the whole process of a holistic process.
Serena Ngoh: Okay, and when you say one degree draft, is that total for both sides, half a degree per side, per wall, or is that one degree from the center line?
Greg Paulsen: So we [crosstalk 00:55:56].
Kyra Stawson: We do request one degree per wall. So that's from either the base of the wall or the very top. So whatever pivot point you want to go after, is one degree per wall.
Greg Paulsen: Yeah, its degree as your card would actually apply. So if you put one in there, it's going to be applying after that per face.
Kyra Stawson: Right.
Serena Ngoh: Okay and we have a lot more questions coming through. I do want to make a note here that while we will end in a couple of minutes, Greg and Kyra are going to be reaching out to anyone whose questions do not get answered. So feel free to keep them coming and enter them here. And we'll try and get through as many as possible in these next couple of minutes before you guys have to get back to designing. So here's a quick one, some companies require MBAs prior to a PO, do you regularly agreed to customer MBAs?
Greg Paulsen: All the time, absolutely. So this is where you'll speak with your account representative. You can even if you want to get started and you just submit your project. If you email support@xometry.com with your NDA, we can actually start going through the process right away. Alternatively, if you do not have an NDA, but want to make sure that you have NDA in place, you can actually go on to our FAQ. So just on that on a live chat, type an NDA, you'll actually see a link where you could download an NDA, you can sign send to support@xometry.com.
Greg Paulsen: That being said, confidentiality does not require NDA for us. We would not be in business if we share customer information. So we treat every single project as if it's confidential. I love when I can share customer parts when they wouldn't do cross promotions. Actually Serena writes case studies. [inaudible 00:57:47] a great case study that you see is usually there Serena behind that and interviewing with those customers and these are volunteered. So customers are coming and talking about, for example, this great blue part here. Got a great application that they're working on and so the motor parts are projects that we've done for them but everything by nature is confidential.
Serena Ngoh: Yeah, and two people are asking, how are we making ourselves competitive against China molding, especially for our prototype and production?
Kyra Stawson: Greg [inaudible 00:58:25] kick off, I can wrap it a little bit?
Greg Paulsen: Yeah, you can wrap it. So there's a couple things happening right so we have the Manufacturing Partner Network, a domestic network, some of these shops that have a niche for say, doing like higher level spec work, some of these [inaudible 00:58:41] work. When they do low level prototype work, it's kind of like a candy board for them. It's something where they can hit up [inaudible 00:58:49] and if they had the capacity available. Because we have this network approach, a lot of times we can work with mold makers to get a competitive price domestically.
Greg Paulsen: That means that we also do have international partners. So there are some projects that are good for good [inaudible 00:59:05] internationally. And Xometry's network, our aspirations are global as well. So we really do want to be your one-stop shop for on demand manufacturing, regardless of location of origin, we should be able to find the right rates and the right partners to fill your projects.
Kyra Stawson: And I asked Greg to start because I knew he was going to touch on this, but the competitive quoting option. We do always, always, always, always want to let you know that we are open to receiving competitive quotes and either looking to beat or match those. So that's something that we want to do whatever we can to earn your business, excuse me.
Greg Paulsen: Own your business.
Kyra Stawson: Own your business [inaudible 00:59:45]. So, yeah, so we do want to obviously stay competitive no matter what the origin is. And Greg, like I did say before, we do primarily have our largest portion of our network in the US domestically, but we do have international partners as well, those can compete amongst each other. So we do like to stay competitive until.
Serena Ngoh: Okay. Thank you guys. So let's do two more questions before we close it out. And remember, all of your questions will get answered, Yes.
Greg Paulsen: If you have more questions, please write them down because Kyra and I are going to go through these in the next couple days and get back to any of these. So if you do have questions, even right now, please write them down. We'll get back to you.
Serena Ngoh: And you can reach out through them via email. Their emails are right down the screen as well. Okay, so does Xometry do silicone injection molding?
Greg Paulsen: Kyra what's the latest on this one?
Kyra Stawson: So this is somewhere that we're looking to increase our network as well. We do currently have some; I guess you could say partners in our network that are capable. Although it is not a strong speech for us at this time. But we do focus on similar or like material such as a last American material we do offer a Santa [inaudible 01:00:59] or a TP or anything of that nature. So we do offer similarities, although we are strengthening our network in LSR.
Greg Paulsen: Yeah, so stay tuned. It's something that if you do have a project you want us to explore, please feel free to submit it and we will take a look.
Kyra Stawson: Yeah.
Serena Ngoh: And the last one here covers a lot of these other questions, right? Is presale engineering free? Is the consultation free?
Kyra Stawson: Yeah, absolutely. All you have to do is submit your quote for manual review. My self-alongside the account representative will probably be in touch. And like I said, we do offer guidance and recommendations on your design that is all free. Although I will say that we don't do any of the design work ourselves. So we leave that up to the customer just for liability reasons. We don't want to make any of those big decisions. But we offer free consultation. I guess you could say yes.
Serena Ngoh: Okay, great. So with that said, all of your specific questions will get answered during consultation. So that's it for us. Thanks so much everyone for joining our webinar on injection molding design strategies. We look forward to consulting on your quotes. And also don't forget to mention your coupon code.
Greg Paulsen: Thanks so much, guys.
Kyra Stawson: Bye. Thank you.
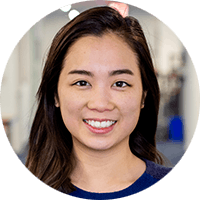