Injection molding is a manufacturing process used for the mass production of identical plastic parts. It’s a method of plastic injection where molten plastic is inserted into a mold to produce a part in the shape of the mold cavity, creating a physical representation of modeled plastic parts. Plastic injection molding has been around since the late 19th century and continues to be popular. If you look around, injection molded parts are everywhere, from the keys on your keyboard to the dashboard of your car to your X-Wing LEGO set.
The plastic injection molding process is commonly used when large amounts of parts are needed quickly, when piece prices need to remain low, and when all parts need to be identical in size and other metrics. The main benefit of this process is its cost effectiveness; sometimes it costs just cents per part for parts at scale. “At scale” typically refers to volumes ranging from thousands to hundreds of thousands of parts. However, it also is one of the most repeatable manufacturing processes, and it also has the highest variety of materials, colors, and cosmetics when compared to CNC machining or even 3D printing.
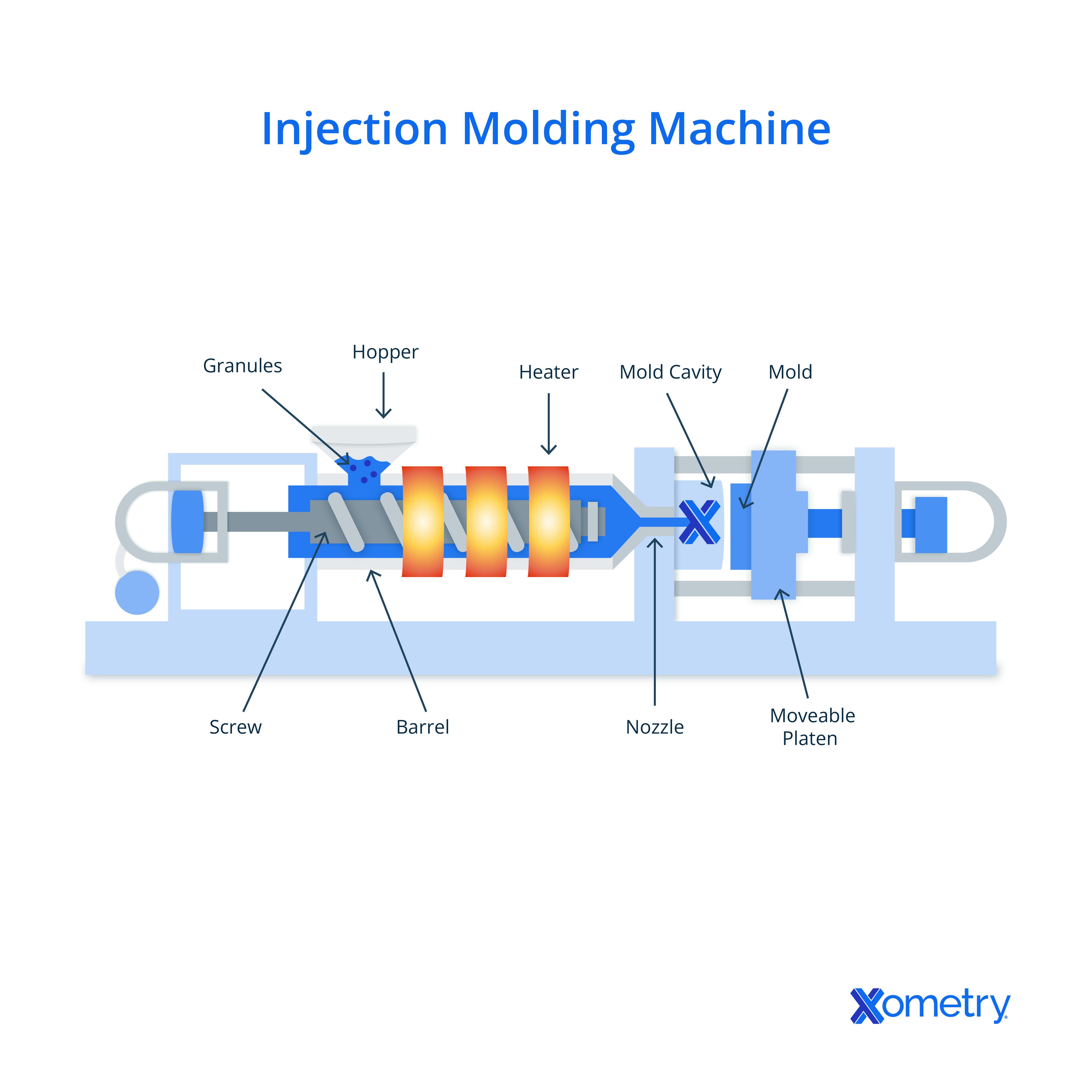
What Are the Advantages of Plastic Injection Molding?
Plastic injection molding's advantages include uniformity, decreased cost, and quick high-volume production. Additionally, injection molded parts feature excellent stability and their scrap materials can be recycled, helping to eliminate waste.
- Providing Uniformity: forming all parts from the same molds ensures parts keep the same dimensions with little effort (and therefore cost). Part tolerances can reach +/- .125 mm (.005 in) comparable to CNC machined or 3D printed parts, and are commonly found at +/- .500 mm (.020 in).
- Making Virtually Identical Parts: since all parts produced come from the same few molds, even pieces with detailed features or complex geometries remain consistent.
- Decreasing Cost: due to the nature of injection molding, the more parts you produce, the less you pay per piece. Manufacturing this way involves little in the way of labor or time expenses once the initial equipment and materials are set up. Injection molding is the cheapest process at scale for plastics because it can produce hundreds or thousands of parts per day.
- Increasing Speed of Production: other manufacturing methods including CNC machining and 3D printing require more work around each part, while injection molding simply requires the injection of material and the cooling time to create a part (some part types do require secondary processes depending on their applications, however). Production can also be increased by including mold cavitation (the number of hollow forms inside each mold). It’s important to note, however, that this only applies once the tooling has already been made. Tooling creation adds time to the lead time for new molded parts.
- Benefitting Compatibility: some forms of injection molding (such as overmolding and insert molding) enable the use of multiple materials to create a single part. Injection molding itself can utilize over 18,000 thermoplastics, thermosets, and elastomers by some estimates. This means that it’s easy to create parts that are compatible with the components they will interact with.
- Ability to Make Complex Parts with Less Expense: since it involves filling plastic into a mold, complex and intricate parts can be made by this method in large batches without a lot of labor or time. It’s just important to ensure the design follows injection mold best practices, which we cover in more detail further on.
- Material Flexibility: since injection molding can utilize so many thousands of types of plastic and additives, it’s easier to find plastic with the properties you need.
- Stability: Injection molded parts are isotropic, which means they form a solid part. This makes them stronger and more reliable than some 3D printed parts, so they will last longer before needing replacement.
- Material recyclability: injection molding can reuse scrap material, reducing both waste and the need to purchase more material.
- Low cost of labor: since injection molding is mostly run by machines, labor costs are limited to supervision, quality checks, and other similar tasks.
What Are the Disadvantages of Plastic Injection Molding?
Injection molding disadvantages include high prices for single prototypes or small production runs in most cases, as well as a lack of flexibility in design once tooling has been created. Parts made from this process must also stay small, and they have certain design limitations that will greatly increase price if ignored.
- Unsuitable for small production runs: custom tooling (which includes molds, fixtures, jigs, and other equipment) is expensive to create. There are also costs associated with setting up molds and buying the plastic to be molded. Anyone looking to start injection molding should ensure the number of parts they want produced make sense from a financial standpoint.
- Long initial lead times: it can take 5-7 weeks to manufacture tooling and 2-4 weeks to make and ship the actual parts. Those who don’t already have injection molding set up for them will find that CNC machining or 3D printing have faster turnaround times.
- Lack of design flexibility: once a mold is created, it is difficult or impossible to make changes. Any major design changes must use a new mold, so it’s important to ensure the design going into the first mold is the one you want.
- Limitations on part sizes produced: while large injection molded parts are possible, they are also more difficult to make and therefore more expensive. Products like car door panels or cart bodies are possible to injection mold, though.
- Certain designs are difficult to accomplish: parts produced using this method should have walls with even thickness, draft angles (which allow the part to separate from the mold) and few or no undercuts. Some undercuts are possible in injection molded parts, as are uneven walls, but they drive the price up because of the added difficulty in producing them.
When part production doesn’t work within these limitations, other manufacturing methods such as 3D printing take over. It’s best to go with 3D printing for part designs that will require frequent changes, smaller production runs, and quick turnaround times. 3D printing is also best used for small parts.
FREE Injection Molding Design Guide
What is the Plastic Injection Molding Process?
The plastic injection molding process injects liquid material into a mold to cool into a part. It features four key steps: clamping, injection, cooling, and ejection.
- Clamping. The two halves of the aluminum or steel mold are held together to prepare for the enormous pressure from injecting the molten material.
- Injection. Pelletized resin is heated to a melted state and injected into the mold. Once the majority of plastic is injected, packing and holding occurs, where pressure is applied to ensure plastic has filled all parts of the mold.
- Cooling. The part cools and solidifies into the final plastic part. This may take anywhere from a few seconds to a few minutes.
- Ejection. The molded plastic part is then ejected, either automatically or manually, and the process starts again for the next part.
Overall plastic injection molding is a fairly automated process, so little human labor is involved apart from supervision.
What are the Uses of Plastic Injection Molding?
Plastic injection molding is used in all industries for applications from static-dissipating electronics housings to self-lubricating parts in the oil and gas industry. Some of the most common applications include:
- Consumer products: commonly utilizing inexpensive, mechanically strong plastics like PVC, this industry uses injection molding for handheld items, storage containers, and IoT containers.
- Aerospace companies use products like turbine housings and blades, pump gears, and valve seats, made from engineering plastics such as PEEK and PAI, both of which can handle wide ranges of temperatures seen by aircraft.
- Electronics: in this field injection molded parts include many over molded components like wire cables and connectors. Materials used commonly include static dissipation plastics like ABS and ABS blends.
- Medical manufacturers use injection molding for product parts found in medical tools, light or monitor support arms, infusion pumps, EKG machines, and tomographic imaging machines. Medical companies will utilize plastics that don’t absorb moisture and that can be sterilized via steam, radiation, or gas. Some plastics needed will also have clarity requirements for transparent parts. Commonly used plastics include PEEK, polycarbonate, and polystyrene, though not Nylon, as it absorbs moisture.
- Energy and oil companies utilize high temperature resistant plastics with little to no moisture absorption. This includes PEEK, which is neutral with high temperature resistance, PTFE, which has high heat deflection properties. They also commonly use nylons, which are self-lubricating and can withstand a wide range of temperatures. These companies require products like insert molded valves, electrical connectors, seals, pipe protection and liners, and other parts.
- Automotive: since vehicles can end up in an array of climates and operating conditions, automotive companies will use materials with a wide range of chemical and temperature resistance. Parts, including door panels and engine components, will often be manufactured with glass-filled nylon, as the glass adds stiffness for products like bumpers. Other popular materials include PBT, PPE-PS, and polyether imide, which has high chemical resistance.
What are Plastic Injection Molding Prototypes?
Injection molding prototypes are cheaply produced, relatively short run groups of dozens of injection molded products created in design, testing, and development stages for testing and promotion. More specifically, a company will want to create prototypes to:
- Prove a part design will work using this method specifically
- Ensure the final part that will be injection molded will come out without material or tooling-based design problems
- Use in consumer research or for promotion
- Test the parts, including figuring out cosmetics
- Demonstrate the part to potential distributors
- Getting a specific material or finish that isn’t achievable using other ways, such as creating polystyrene parts (which can’t be printed)
These parts are produced with less expense by using single cavity molds, cheaper materials for their tooling, and less automation in manufacturing them. Not all industries will create prototypes for injection molding; those with tight timelines or that use offshore manufacturers will often skip this step of the process.
However, some part types are best prototyped first. Companies creating small products like contact lens cases that will have many holes in a multicavity mold later will find prototyping more helpful before investing in molds with dozens of cavities. Additionally, companies with large amounts of regulation when creating parts at scale (such as those in the medical sector) use injection mold prototyping to create parts for research without having to go through the regulations and certifications processes required for products to be used on consumers. This allows them to avoid costly mistakes after having gone through the approval processes. Companies like Xometry with ISO 13485 certification can also do full production runs for medical companies.
Generally prototyped parts will be made from commodity plastics, like polycarbonate, nylon, polypropylene, and ABS , as well as elastomers like TPE, TPU, and SAN. Some resins require specialty molds as well. PEEK, for example, requires a heated mold instead of the more standard cooling mold, which only dissipates heat from liquid plastic instead of adding heat at first to keep it liquid.
What are the Plastic Injection Molding Types?
Plastic injection molding types include a wide range from insert and single cavity molds to complex tooling like master unit die (MUD) molds. More specifically:
- A single-cavity mold or tool is typically used for lower-volume batches. Single-cavity tools have one cavity, so they produce one part every injection cycle. They are sometimes called single impression tooling.
- A multi-cavity tool, also referred to as multi-impression tooling, consists of duplicate cavities for the same part and allows for multiple parts to be produced in a single cycle. Multi-cavity tooling also shares a runner system, which can reduce the percentage of waste or scrap material per part which saves costs in production. Multi-cavity tooling is important when producing a high volume of parts as efficiently as possible. This tooling is typically produced in even numbers, and can have 2, 4, 8 and more cavities. It is important to note that adding cavities increases the complexity and manufacturing time of a tool, which can significantly increase tooling costs compared to single-cavity tools.
- Family mold tools are a type of multi-cavity tool where each cavity is a unique part design. Family tooling shares the same mold, reducing overall costs compared to making individual tools per part design. Family molds are popular for low-volume or prototype production. If the parts in a family tool share the same material, range of dimensions, and color, then the tool can share cycle times to produce multiple parts simultaneously. These parts typically run individually using a runner shut-off.
- Master Unit Die (MUD) tooling uses a common frame that remains in the molding machine while interchangeable inserts are added or removed to define the shape of the cavity. This is often more cost-effective than a traditional custom-machined mold and can speed up production time. This makes it useful for prototyping and low-volume production. MUD tooling can be designed with single-cavity, multi-cavity, or family tooling if the part designs, gating system, slides, or cores can fit within the exchangeable insert. However, MUD tooling is not used for production of over 100,000 units since this volume of parts often requires advanced molding customization.
- Insert molds are a type of tool where a metal component, such as a threaded piece or copper conductor, is placed securely in the mold cavity and bonded to the plastic part. Oftentimes, it is faster to insert mold rather than tap or install inserts as a secondary operation to molding. Insert molds reduce the labor and time required to manually assemble parts via ultrasonic and heat-stake tapping insertion. It also increases the reliability of components by merging two materials mechanically.
- Overmolding is when one plastic material is molded over another plastic part, like the rubber grip over the plastic of a toothbrush handle. Overmolds typically involve molding the rigid substrate first and then inserting the part into a second tool to mold the second material over the substrate. Two-shot, or 2K, molds automate the overmolding process using specialized equipment, such as multiple cavities and automated tooling, to heat and feed two separate materials at once. Two-shot molds are best used in production due to high tooling costs.
- Liquid silicone molding differs from thermoplastic injection molding in that it uses liquid silicone materials, which are thermoset and cannot be melted once the part is molded. The process is the same in that it requires a machined tool, high injection pressure, and similar ejection mechanisms.
- Compression molding uses a preheated, open cavity side mold into which material, called a charge, is fed. A vertical hydraulic press comes down to form the material into the final part. Compression molding is advantageous for flat or simple parts because it is less expensive due to the simplicity of the mold.
- Transfer molding is when a plastic material is forced into a mold in a process similar to compression molding with a vertical hydraulic press. Transfer molding is similar to injection molding, however, in that the mold is enclosed and is transferred into the molding cavity from another chamber.
- 3D printed molds are possible but most companies that serve businesses do not print molds because of the higher rate of error involved.
All plastic injection molding types involve the injection of melted plastic into a mold that is then cooled and ejected as a part. However, within this field there are more specific types of manufacturing, including overmolding, injection molding, and compression molding.
Which Products can be Molded with Plastic Injection?
Products that are molded with plastic injection include furniture, car parts, food products, and more. More specifically:
- Construction products, such as roof vents
- Food and beverage items, like cups or trays
- Toys, including models or toy furniture
- Electronics housings, like remote control exteriors
- Automotive parts like car bumpers
- Healthcare products like sharps containers
Is Plastic Injection Molding Better than 3D Printing?
Plastic injection molding is better than 3D printing for larger production runs, stronger parts, faster production, and a larger variety of materials that can be used, including fillers. Because injection molding’s manufacturing process simply involves the injection and cooling of plastic, a part can be formed within a few minutes at the most, as opposed to the layer-by-layer creation of a part via 3D printing. This makes it possible to make higher volumes of parts faster than a 3D printer, though building molds and other setup means that injection molding has a much longer original lead time. Parts are also stronger since they’re not reliant on the bonds between each layer of plastic, which is important for products like car bumpers. At the same time, nearly all plastics can be injection molded, while 3D printing plastic materials do not yet have the same diversity.
Is Plastic Injection Molding Environmentally Friendly?
Plastic Injection Molding is environmentally friendly when compared to other plastic manufacturing processes. Since this technique only uses the amount of plastic needed to fill the mold, less material is wasted, especially when excess plastic from the sprue and runner is ground up and reused (which can be done multiple times if necessary). The process also generates fewer emissions and uses less energy compared to other processes.
However, the injection molding industry is so large that the field still uses large amounts of energy, and most plastics produce large amounts of emissions when created. Additional work can be done however to make this process more eco-friendly by optimizing product design, processes, efficiency in production runs, and energy conservation. There are also biodegradable plastics and fillers that can be used to make greener products.
What are the Basics of Plastic Injection Molding Machines?
The basics of Plastic injection molding machines consist of three major parts: the injection unit, the mold, and the clamping/ejector unit. We’ll focus on the injection mold tool components in the following sections, which break down into the sprue and runner system, the gates, two halves of the mold cavity, and optional side actions. You can learn more about the process of plastic injection molding basics through our more in-depth article Plastic Injection Molding Basics.
1. Mold Cavity
A mold cavity typically consists of two sides: an A side and B side. The core (B Side) is typically the non-cosmetic, interior side that contains the ejection pins that push the completed part out of the mold. The cavity (A Side) is the half of the mold which the molten plastic fills. Mold cavities often have vents to allow air to escape, which would otherwise overheat and cause burn marks on the plastic parts.
2. Runner System
The runner system is a channel that connects the liquified plastic material from the screw feed to the part cavity. In a cold runner mold, plastic will harden within the runner channels as well as the part cavities. When the parts are ejected, the runners are ejected as well. Runners can be sheared off through manual procedures like clipping with die cutters. Some cold runner systems automatically eject the runners and part separately using a three-plate mold, where the runner is partitioned by an additional plate between the injection point and the part gate.
Hot runner molds do not produce attached runners because feed material is kept in a melted state up to the part gate. Sometimes nicknamed “hot drops,” a hot runner system reduces waste and enhances molding control at an increased tooling expense.
3. Sprues
Sprues are the channel through which the molten plastic enters from the nozzle, and they typically intersect with a runner that leads to the gate where the plastic enters the mold cavities. The sprue is a larger diameter channel than the runner channel that allows the proper amount of material to flow through from the injection unit.
4. Gates
A gate is a small opening in the tool that allows molten plastic to enter the mold cavity. Gate locations are often visible on the molded part and are seen as a small rough patch or dimple-like feature known as a gate vestige. There are different types of gates, each one with its strengths and trade-offs.
5. Parting Line
The main parting line of an injection molded part is formed when the two mold halves close together for injection. It is a thin line of plastic that runs around the outside diameter of the component.
6. Side Actions
Side actions are inserts added to a mold that allow material to flow around them to form the undercut feature. Side actions must also allow for a successful ejection of the part, preventing a die lock, or a situation where the part or tool must be damaged to remove part. Because side actions do not follow the general tool direction, undercut features require draft angles specific to the action’s movement. Read more about common types of side actions and why they are used.
For simple A and B molds that do not have any undercut geometry, a tool can close, form, and eject a part without added mechanisms. However, many parts have design features that require a side action to produce features like openings, threads, tabs, or other features. Side actions create secondary parting lines.
What are Plastic Injection Molding Machines?
Plastic injection molding machines are machines that heat and mix plastic pellets until they’re melted into a liquid, which is then sent through a screw and forced through an outlet into molds to solidify as plastic parts.
There are four basic types of molding machinery, classed around the power used to inject the plastic: hydraulic, electric, hybrid hydraulic-electric, and mechanical injection molders. Hydraulic machines, which use electric motors to power hydraulic pumps, were the first type of plastic injection molding machines. The majority of injection molding machines are still this type. However, electric, hybrid, and mechanical machinery has greater precision. Electric injection molders, using electricity-powered servo motors, consume less energy, as well as being quieter and faster. However, they’re also more expensive than hydraulic machines. Hybrid machinery uses the same amount of energy as electric models, relying on a variable-power AC drive that combines both hydraulic and electric motor drives. Finally, mechanical machines increase tonnage on the clamp through a toggle system to ensure flashing doesn’t creep into the solidified parts. Both these and electric machines are best for clean room work as there’s no danger of hydraulic system leaks.
Each of these machine types works best for different aspects, however. Electric machines are best for accuracy, while hybrid machines offer more clamping force. Hydraulic machinery also works better than the other types for the production of large parts.
In addition to these types, machines come in a range of tonnage from 5-4,000 tons, which are utilized depending on the viscosity of the plastic and parts that will be made. The most popularly used machines, however, are 110 ton or 250 ton machines. On average, larger injection molding machinery can cost from $50,000-$200,000 or more. 3,000 ton machines can cost $700,000. On the other end of the scale, a desktop injection molding machine with 5 tons of force can cost between $30,000-50,000.
Some of the most popular brands include:
- Husky
- KraussMaffei
- Netstal
- Arburg
- Demag
- Engel
- Wittmann Battenfeld
- Sumitomo
- Fanuc
- Milacron (which owns Robotshot)
Often a machine shop will only use one brand of injection molding machine, as the parts are exclusive to each brand- it costs heavily to change from one brand to another (the exception to this is mold components, which are compatible with different brands. Each brand’s machines will perform certain tasks better than others.
How to Calculate Plastic Injection Molding Cost
You can calculate plastic injection mold cost by adding together the initial and recurring costs in the formulas below. There is a range of factors that goes into the final injection molding cost, including:
For initial costs:
Startup Cost = tooling costs + mold and material setup time and labor (drying resin + hanging molds + arranging water lines and sensors + setting up cooling or gating systems + scrap rates)
Recurring costs:
Recurring costs = raw materials + piece price (setup fees + set scrap rates, 3-5% of total piece price + machine hourly rates, ~60% of final cost + plastic weight + mold maintenance fee + inspection requirements) + secondary operations + packaging + shipping
Initial startup costs are fewer in number, but they cost the most. Tooling costs include all of the factors that go into making the tooling for your parts, including the cavities and slides. Other one-time expenses are usually rolled up in piece price, including configuring the setup of your parts, and the time spent getting the molds and materials ready. This includes drying your resin, hanging molds, arranging waterlines and sensors, and setting up any specific cooling system or gating system. It will also include set scrap rates for purging the machines of previous plastics.
Recurring costs, on the other hand, include setup fees, raw materials, piece price, and any post-production requirements such as packaging or shipping. Setup fees are for the work to calibrate the machines when they’re first turned on- employees must run shots of plastic through the machine to get it working correctly. Raw materials include both plastic resins and additives. Not all parts require secondary operations, but some will need machining, sonic welding, marking, or other services. Often manufacturers will offer secondary services as an option. Packaging can range from the least expensive packaging used to ship the parts to you, up to end-user packaging.
Of all of these components of the final price, piece price is the most complicated. One of the most expensive factors in piece price is the set hourly rates for machinery; the time to form a part (made up of the injection, pack and hold, cooling, and ejection times) is one of the areas that must be best optimized. This is why mold cavitation, the amount of cavities that will create parts in each mold, is so important. There will also be a fee for the plastic weight, including both plastic that becomes parts and scrap plastic left over in the sprue and runners. Finally, mold maintenance fees will cover the cost of mold warranties, and additional inspection will also add cost.
Between runs, you’ll also incur some of the costs mentioned as one time costs above. Once a run is finished, manufacturers will clean and put your mold into storage with a crane or other equipment. Before the next run can start, the mold will have to be reinstalled in the machine, hooked back up to everything, and calibrated. You will also be charged again for purging other plastics from the system.
Calculating these plastic injection molding costs before ordering will enable you to get a more accurate estimate of the potential budget and help you to weigh your options with injection molding vs. other manufacturing methods.
Is Plastic Injection Molding Cheap?
Plastic injection molding is cheap for large production runs and other specific circumstances. While startup costs involving the creation of tooling are relatively high, the process itself is budget-friendly enough to lower the overall piece price as long as production runs are large enough.
In situations where you need thousands or hundreds of thousands of parts, the relatively minor expenses of running the process can drive the price per part down to a few cents per piece. This is especially true for simpler parts, as they will require less complex, and therefore less expensive molds. More complex part molds will feature parts like side actions, hot runners, manually trimmed gates, and water cooling lines. Additional costs can be saved when waste plastic is ground down and recycled.
For situations in which there will be changes to the part design, however, injection molding will get expensive quickly, as each new or modified mold is a significant cost. Small part runs will also cost a great deal more per part, as will smaller quantities of plastics, as buying in bulk lowers the cost of raw materials (if bulk plastic is not used in a timely manner, however, this cost benefit can be swallowed up by storage costs).
For more information see our article on Plastic Injection Molding Cost.
How Long Do Injection Molds Last?
Depending on the material type, a plastic injection molding lifespan can last between 500 parts to over a million. Aluminum is often used for shorter injection molding lifespan, while longer lasting molds utilize heavier duty metals like steel. There is a wide range of steels used, some of which are abrasion resistant for tougher plastics and some of which are simply less expensive. The SPI (Society of the Plastics Industry) has set out guidelines for the different mold classifications depending on how long they’re supposed to last.
The injection molding industry often defines molds by their class. This goes from Class 105 rapid prototype molds that produce no more than hundreds of parts to Class 101 tools that produce millions of parts quickly. The number of parts a tool can produce before it wears down is known as the tool life.
- Class 105, or a Class V tool, is the simplest type of mold. This mold is a prototype mold only and is produced as quickly and cheaply as possible. This class is typically used for rapid tooling, in which a small batch of injection molded parts prototyped for impact and stress testing (over plastic machined and 3D printed parts). A class 105 tool is not built to create more than 500 parts. An example of this tool is a one-time market test of 100 molded units.
- Class 104, or a Class IV tool, is a low-volume production mold that produces under 100,000 parts. It is usually made from aluminum or mild steel and can typically only withstand non-abrasive materials (this means no glass-filled materials, for example). An example of this is an aluminum or MUD tooling, SPI B-3 finish, hand-loaded cores and limited reruns.
- Class 103, or Class III tool, is a low- to mid-volume production tool for making under 500,000 parts. It is cost-effective and is a popular class of mold tool. Example: An aluminum or steel tool with automated lifts or slides that will require multiple re-runs with batches between 1,000-5,000 units.
- Class 102, or Class II tool, is a medium to high production tool for producing under 1,000,000 parts. This tool is made from a more durable metal—typically steel—so it can be used with abrasive materials and/or parts requiring close tolerance. This is a high-quality, and therefore costly, molding option. Example: Steel tooling with an SPI A-2 finish, automated slides, and scheduled production cycles.
- Class 101, or a Class I tool, is the best quality tool possible and is built for extremely high production volumes with a lifetime of over 1,000,000 parts. This is the highest-priced mold. Example: A multiple-cavity steel tool with full automation and overnight production work centers.
What is the History of Plastic Injection Molding?
The history of plastic injection molding has evolved from its 1872 beginnings as first new plastics and then new molding techniques were developed. In 1872 brothers John and Isaiah Wyatt patented the first injection molding machine to create billiard balls from celluloid instead of ivory. The original machine used a plunger to push the celluloid through a hot cylinder, which melted it, and into a mold. From there products including buttons, combs, and other household products started to be injection molded. Cellulose acetate was later developed as a less flammable alternative to celluloid, and additional thermoplastics (including PVC and polystyrene) were invented up until World War II to take advantage of this technology.
During WWII, plastic injection molding history continued to evolve and plastic materials had advanced enough to replace metal and rubber parts, which were in short supply during and after the war. In 1946 James Watson Hendry created an extrusion screw injection molding machine. The screw gave better control over the plastic and enabled better quality control. Hendry also created gas-assist injection molding which allowed companies to create more complex and bigger hollow parts.
Plastics continues to evolve into stronger properties until in the 1970s plastic production had a bigger market share than steel. In the 1990s aluminum molds also became popular, creating a faster, less expensive version of steel molds for certain applications.
What Are Some Plastic Injection Molding Materials?
The top three injection molding plastics in terms of cost and toughness include: polycarbonate, polypropylene, and nylon. These are also three of the six most popular plastic injection molding materials at Xometry, used because of their strong mechanical properties and inexpensiveness. In more detail:
- Polycarbonate (PC) has high impact strength and steam and chemical resistance, as well as abrasion resistance. This plastic is popular in the automotive, construction, electronics, healthcare, and consumer goods sectors, used for applications from safety goggles to food mixers to light housings.
- Polypropylene (PP) is highly chemical and moisture resistant; it’s also tough, food safe, and a good electrical insulator. PP is commonly found in food packaging, but it also commonly used in prototyping.
- Polyamide (Nylon) has a high melting point, strong thermal and chemical resistance, and it very tough. However, it also has a tendency to expand, and it’s brittle. Nylon is often used for gears, bushings, bearings, and other mechanical parts in the automotive and electrical industries.
- Acrylonitrile butadiene styrene (ABS) is tough, as well as scratch and impact resistant. It also has strong dimensional stability and static dissipation properties. ABS is common in the electronics industry for that reason, including in keyboards, housings, and wall socket guards.
- High-density Polyethylene (HDPE) is a lightweight, durable plastic with high tensile strength, strong chemical resistance, and especially good electrical insulation. Like PP, HDPE is often used in food packaging such as trays, crates, and bottles. However it also is used in certain textiles like fishing nets, rope, and decorative fabric.
- PC-ABS (a blend of ABS and PC), is both tough (with high strength, stiffness, and impact resistance even in low temperatures) as well as heat resistant. It also keeps good dimensional stability. However, it has low weatherability and fatigue endurance, and without reinforcing additives it has low chemical, oxidation, and UV light resistance. You’ll find PC-ABS in automotive parts like glove boxes, or electronics frames and enclosures.
Other commonly used plastics include thermoplastics such as polystyrene (PS), SAN, PVC, PET, PBT, PEI, PPS, PMMA, TPU and TPE. High-performance injection molding plastics like PEEK and PEI are more costly but offer the best heat resistance and stiffness.
Common FAQs About Plastic Injection Molding
Is Plastic Injection Molding Better than 3D Printing?
Plastic injection molding is better than 3D printing for larger production runs, stronger parts, faster production, and a larger variety of materials that can be used, including fillers. Because injection molding’s manufacturing process simply involves the injection and cooling of plastic, a part can be formed within a few minutes at the most, as opposed to the layer-by-layer creation of a part via 3D printing. This makes it possible to make higher volumes of parts faster than a 3D printer, though building molds and other setup means that injection molding has a much longer original lead time. Parts are also stronger since they’re not reliant on the bonds between each layer of plastic, which is important for products like car bumpers. At the same time, nearly all plastics can be injection molded, while 3D printing plastic materials do not yet have the same diversity.
Is Plastic Injection Molding Environmentally Friendly?
Plastic Injection Molding is environmentally friendly when compared to other plastic manufacturing processes. Since this technique only uses the amount of plastic needed to fill the mold, less material is wasted, especially when excess plastic from the sprue and runner is ground up and reused (which can be done multiple times if necessary). The process also generates fewer emissions and uses less energy compared to other processes.
However, the injection molding industry is so large that the field still uses large amounts of energy, and most plastics produce large amounts of emissions when created. Additional work can be done however to make this process more eco-friendly by optimizing product design, processes, efficiency in production runs, and energy conservation. There are also biodegradable plastics and fillers that can be used to make greener products.
Is Plastic Injection Molding Cheap?
Plastic injection molding is cheap for large production runs and other specific circumstances. While startup costs involving the creation of tooling are relatively high, the process itself is budget-friendly enough to lower the overall piece price as long as production runs are large enough.
In situations where you need thousands or hundreds of thousands of parts, the relatively minor expenses of running the process can drive the price per part down to a few cents per piece. This is especially true for simpler parts, as they will require less complex, and therefore less expensive molds. More complex part molds will feature parts like side actions, hot runners, manually trimmed gates, and water cooling lines. Additional costs can be saved when waste plastic is ground down and recycled.
For situations in which there will be changes to the part design, however, injection molding will get expensive quickly, as each new or modified mold is a significant cost. Small part runs will also cost a great deal more per part, as will smaller quantities of plastics, as buying in bulk lowers the cost of raw materials (if bulk plastic is not used in a timely manner, however, this cost benefit can be swallowed up by storage costs).
For more information see our article on Plastic Injection Molding Cost.
Summary
This article presented plastic injection molding, explained it, and discussed its history and materials used for various applications. To learn more about plastic injection molding, contact a Xometry representative.
Xometry provides a wide range of manufacturing capabilities, including injection molding and other value-added services for all of your prototyping and production needs. Visit our website to learn more or to request a free, no-obligation quote.
Disclaimer
The content appearing on this webpage is for informational purposes only. Xometry makes no representation or warranty of any kind, be it expressed or implied, as to the accuracy, completeness, or validity of the information. Any performance parameters, geometric tolerances, specific design features, quality and types of materials, or processes should not be inferred to represent what will be delivered by third-party suppliers or manufacturers through Xometry’s network. Buyers seeking quotes for parts are responsible for defining the specific requirements for those parts. Please refer to our terms and conditions for more information.
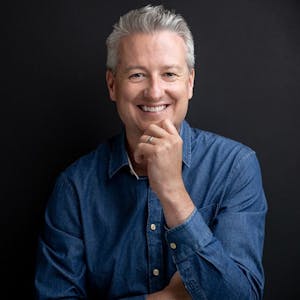