This article will examine the best plastics for injection molding, including, but not limited to: nylon, ABS plastic, and polycarbonate (PC). All of these plastic materials have different strengths and applications that make them ideal for injection molding.
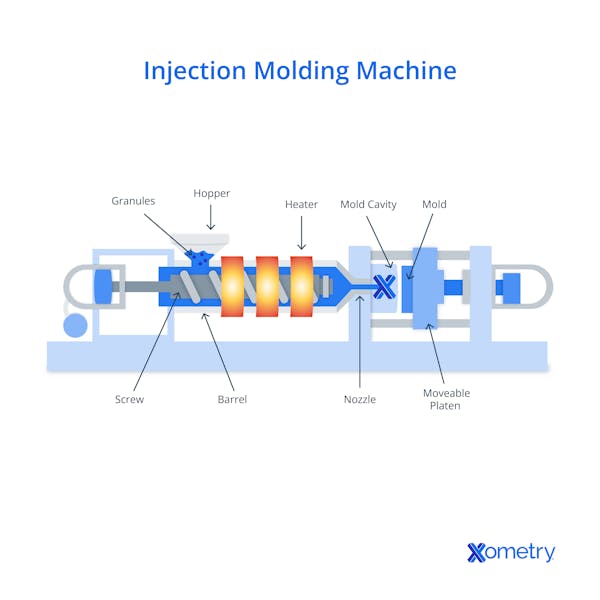
Nylon (PA)
Nylon is the name for a family of synthetic polymers composed of polyamides (PA). Nylon is a silk-like thermoplastic, typically made from petroleum, that can be melt-processed into fibers, films, or shapes. Nylon polymers are used in many commercial applications.
The most commonly used types of Nylon for injection molding are Nylon 6, Nylon 6/6, Nylon 66, and Nylon 6/66. Nylon 66 is a more crystalline version of Nylon 6. It is also called polyamide 66 or PA 66. It has improved mechanical properties due to its more ordered molecular structure. Nylon 66 for machining has improved temperature resistance and lower rates of water absorption when compared to standard nylon 6. Nylon 6 offers increased mechanical strength, rigidity, good stability under heat, and chemical resistance. Nylon 6/6 is stiffer and typically more durable than Nylon 6.
Best Products for Nylon Injection Molding?
Typical applications of Nylon 66 include wear pads, guide wheels, and slide bearings. Other Nylon applications include high-ware parts, quick-release buckles, gears, and hand cranks. Although Nylon is a strong plastic, it absorbs water and is therefore not the ideal choice for marine applications.
Molding Temperature of Nylon
The molding temperature for Nylon is under 220-320 Celsius, with PA 6’s process temperature at 220-300 degrees and PA 66’s process temperature at 260-320 degrees Celsius. Because the processing temperature of Nylon is narrow, the temperature of the machine barrel must be controlled strictly to avoid decomposition of melt.
ABS Plastic
ABS (acrylonitrile butadiene styrene) is a high-strength general-purpose engineering plastic used for many commercial products. ABS is durable and lightweight. It is a terpolymer created by polymerizing styrene and acrylonitrile in the presence of polybutadiene. The proportions can differ from 15% to 35% acrylonitrile, 5% to 30% butadiene and 40% to 60% styrene.
ABS resin is an opaque thermoplastic polymer and an engineering-grade plastic. There are many advantages to using ABS. It’s tough, has good dimensional stability, resists impacts and scratching, and is hard to break. ABS is a good insulator and doesn’t conduct electricity or give off fumes if exposed to fire. These are essential considerations for product developers working on electrical devices.
ABS is used to make products such as electronics, phone adaptors, keyboards, phone hardware, wall socket plastic guards, LEGO bricks, drainpipe systems, and kitchen appliances.
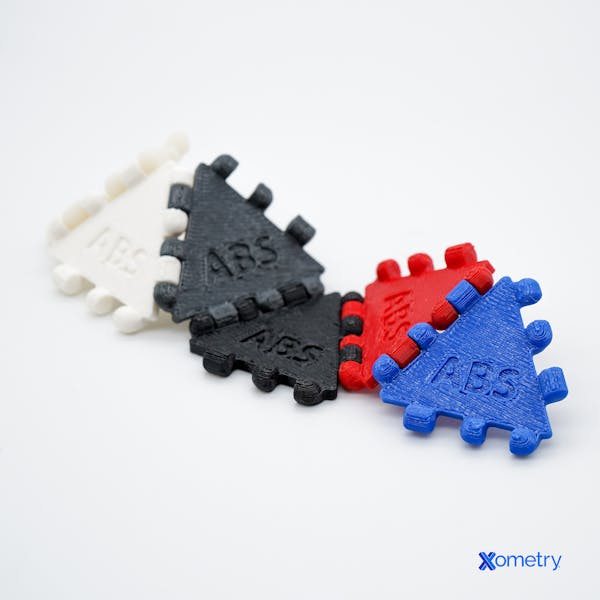
Molding Temperature of ABS Plastic
ABS has a low melting or molding temperature, making it ideal for injection molding. The process temperature is approximately 40-80 °C, preferably as high within that range as possible. Using a higher mold temperature tends to lengthen the molding cycle time, so the mold temperature setting depends on what is most appropriate for the individual product that is to be molded.
FREE Injection Molding Design Guide
Polycarbonate (PC)
Polycarbonate is a high-performance, transparent, engineering-grade thermoplastic that can be used in higher temperature environments, due to its relatively high melting point (155°C). Those qualities come together with a higher price tag, but this aspect is balanced by the versatility polycarbonate.
The main features of this thermoplastic revolve around toughness and high strength, which translates into resistances to impacts and fracture resistance. These resistances are complemented by the material’s high density (1.2 – 1.22 g/cm3).
Advantages of Polycarbonate (PC)
The advantages of Polycarbonate (PC) for Injection Molding are listed below:
- High transmittance (transparency)
- Good operating temperature range (-20°C – 140 °C)
- Flame retardant
- Good electric insulation
- Decent abrasion resistance
Disadvantages of Polycarbonate (PC)
The disadvantages of Polycarbonate (PC) for Injection Molding are listed below:
- Susceptible to damage from hydrocarbons and bases
- Low fatigue tolerance
- Tends to turn yellow after exposure to UV
- Mechanical properties degrade after prolonged exposure to hot water (>60°C)
Uses and Applications of Polycarbonate (PC)
The common uses of Polycarbonate (PC) include: safety helmets, bullet-proof glass, equipment housing, automotive parts, electrical connectors, and electrical insulators.
You can read more about Polycarbonate in our Polycarbonate Guide.
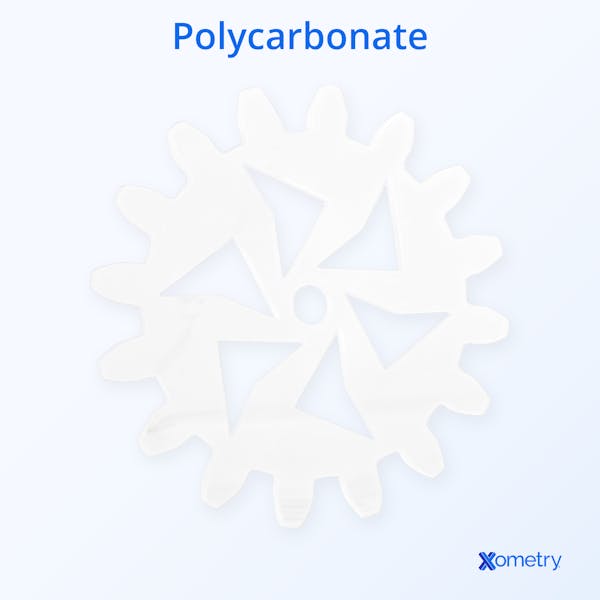
PC-ABS - Polycarbonate-Acrylonitrile Butadiene Styrene
Polycarbonate-acrylonitrile butadiene styrene or PC-ABS is an engineering thermoplastic made of a blend of PC and ABS. The unique balance of properties hinges on the ratio of PC to ABS in the mixture, the polycarbonate’s molecular weight, and any thermoplastic additives in the blend. In addition, the ratio of PC to ABS affects the heat resistance of the final part considerably.
Due to its mechanical properties, PC-ABS plastic is one of the world's most widely used engineering thermoplastics. This material has high strength, high stiffness, high heat resistance, and high impact resistance, even at low temperatures. In addition, PC-ABS holds its dimensional stability over time, and its enhanced flow characteristics and processability make it easy to work with.
The molding temperature range recommended for PC-ABS plastic is 50 to 80 degrees Celsius. The cooling time is essential for part performance and cycle time optimization. The melt temperature is between 250 to 270 Celsius.
For more information see our PC-ABS Plastic Guide.
Best Products for PC-ABS Injection Molding
PC-ABS is most commonly used in the automotive and electronics industries, these products include glove boxes, knee bolsters, overhead and middle consoles, and blow-molded seatbacks. It is also used to manufacture many popular consumer electronics, including laptop monitor enclosures, TV frames, phone exteriors, and parts of portable hand-held devices.
Acetal Copolymer (POM)
Acetal is the common name for a family of thermoplastics with the chemical name "PolyOxy-Methylene." As a semi-crystalline material, acetal is has a low coefficient of friction and good wear properties.
Acetal Copolymer resin has high strength, toughness, rigidity, and dimensional stability. It also has decent wear and friction properties that can be enhanced with additives. Like Acetal Homopolymer resin, Acetal Copolymer is easy to machine.
Compared to Homopolymer, Acetal Copolymer resin has better resistance to organic and inorganic solvents and acids. However, it does have longer mold cycling times and is relatively expensive.
The process temperature of Acetal Copolymer is 110 degrees Celsius.
Best Products for Acetal Copolymer (POM) Injection Molding
Acetal Copolymer is used in applications requiring strength, low water absorption, and chemical resistance. This often means it is used to manufacture high-performance engineering components. Acetal Copolymer is extensively used in the consumer electronics industry and for mechanical and automotive parts.
Some applications for Acetal Copolymer are rollers, bushings, wear strips, ball bearings, small gear wheels, fasteners, gas meters, medical technology, aerosol valves, lock systems, fuel tank modules, and disposable applications.
Acetal Homopolymer
Acetal Homopolymer is a tough, resilient plastic that has rigidity, good creep resistance, toughness, dimensional stability, lubricity, surface hardness, and low moisture absorption.
Compared to Acetal Copolymer resin, Acetal Homopolymer provides higher tensile strength, impact resistance, and good stiffness and creep resistance. These properties allow for shorter molding cycles, thinner and lighter part design, and the potential for cost reductions.
The melting point of Acetal Homopolymer is 162 to 122 degrees Celsius. The process temperature is 205–225 degrees Celsius for standard grades and 195–215 degrees Celsius for impact modified grades.
Best Products for Acetal Homopolymer Injection Molding
Acetal Homopolymer is used for high load mechanical applications and in plumbing and irrigation applications because of its excellent thread strength and ability to resist scale build-up. Because of its machinability, it is used to prototype in vivo medical devices. Some applications include bearings, gears, conveyor belts, safety restraints, housings, automotive ventilation, automotive cooling system parts, and fuel system components.
Engineered Thermoplastic Polyurethane (ETPU)
Thermoplastic Polyurethane is soft and elastic, with excellent tensile and tear strength. For this reason, it is often used to make parts that demand a rubber-like elasticity. ETPU is more expensive than other resins, but there is no substitute for many applications, such as protective wire and cable sheaths. Another advantage is that TPU improves the grip for products that need to be held securely in hand.
ETPU is a tough, highly abrasion-resistant resin that bridges the gap between rubbers and plastics. TPUs can be formulated to be rigid or elastomeric. ETPU exhibits a high flex before break and is ideal for wheels and door panels.
The typical mold temperatures are 150 Fahrenheit to 700 Celsius, depending on the TPU being molded.
Best Products for Engineered Thermoplastic Polyurethane (ETPU)
Some of the ETPU products manufactured are automotive instrument panels, caster wheels, sporting goods, power tools, drive belts, medical devices, footwear, inflatable rafts, and a variety of extruded film, sheet, and sheet profile uses. It is also a popular material found in flexible outer cases of devices like mobile phones cases.
High Density Polyethylene (HDPE)
High-density polyethylene (HDPE), also called polyethylene high-density (PEHD), is a thermoplastic polymer made from the monomer ethylene. When used for HDPE pipes, it is sometimes called "alkathene" or "polythene." With a high strength-to-density ratio, High-density polyethylene (HDPE) is used to produce plastic bottles, corrosion-resistant piping, geomembranes, and plastic lumber. In addition, HDPE is commonly recycled.
High-density polyethylene has excellent processability, a high strength to high-density ratio, good stiffness, strength, toughness, and moisture resistance. It can be susceptible to environmental stress cracking if internal stresses are not minimized by proper design.
The melting point of HDPE is 115 degrees Celsius, while the process temperature is 84 degrees Celsius.
For more information on HDPE see our High-density polyethylene (HDPE) Guide.
Best Products for High Density Polyethylene (HDPE) Injection Molding
HDPE resin is best for large parts that require outstanding physical performance. It is commonly used in corrosion-resistant piping, plastic lumber, packaging, and plastic bottles, such as ones shown in the image below:
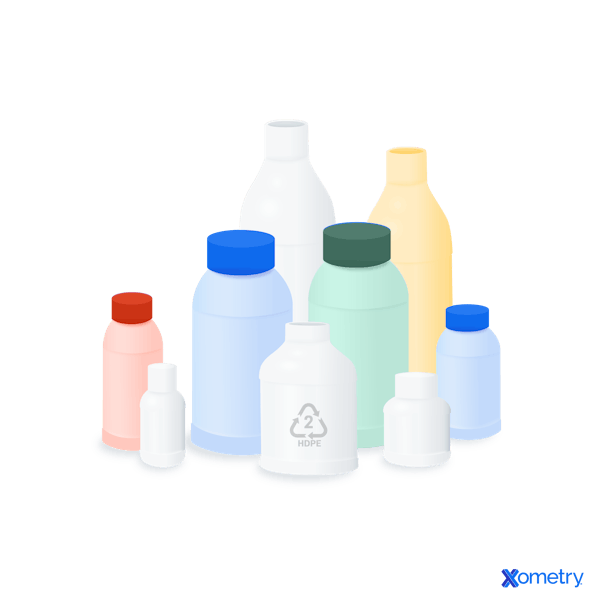
Liquid-Crystal Polymer
Liquid-crystal polymers, or LCPs, are polymers with liquid crystal properties, usually containing aromatic rings as mesogens. In spite of uncrosslinked LCPs, polymeric materials like liquid crystal elastomers (LCEs) and liquid crystal networks (LCNs) can also exhibit liquid crystallinity. They are both crosslinked LCPs but have different cross-link density. They are commonly used in the digital display market.
Liquid-crystal polymer is flame retardant, has excellent mechanical strength, excellent dimensional stability, a low coefficient of thermal expansion, high dielectric strength, outstanding mechanical properties at high temperatures, excellent chemical resistance, and good weatherability.
LCP has a process temperature of 240 degrees Celsius.
Best Products for Liquid-Crystal Polymer Injection Molding
Injection molding with LCP resin is ideal for high-stressed parts. LCPs are also injection molded into IC sockets, HF network switches, custom high-power electrical connectors, power modules for wind and solar inverters and converters, and many other precision devices.
LCP is also particularly suitable for microwave-frequency electronics, medical devices, and dental tools.
Low-density Polyethylene
Low-density polyethylene (LDPE) is a thermoplastic created from the monomer ethylene. The EPA estimates 5.7% of LDPE is recycled in the United States. In spite of competition from more modern polymers, LDPE is an important plastic grade, with the worldwide LDPE market reaching a volume of about 33 billion US dollars in 2013.
LDPE retains its toughness and flexibility over a wide temperature range. It is a highly recyclable material. It does have the disadvantage that its density drops off dramatically above room temperature, and exposure to light and oxygen results in loss of strength and a loss of tear resistance.
LDPE resin is typically used when injection molding laboratory equipment, containers, and bottles. It is also widely used for molding liners for tanks and ponds.
Lastly, LDPE has a process temperature of 46 degrees Celsius.
For more information on LDPE see our Low-Density Polyethylene Guide.
Linear Low-density Polyethylene
Linear Low-density Polyethylene is one of the most commonly used packaging films in the packaging industry. The density reduction comes about by using comonomers that put side groups on the main chain that act like branches in decreasing crystallinity. It is a soft, flexible material.
LLDPE is stretchable and recyclable. Therefore, thin sections are possible without losing the material’s strength. It also does not strain harden. However, it does have some disadvantages that include shear thickening, that it is more difficult to mold with than some of the other materials on this list, and it has a poorer flow.
LLDPE resin is typically used to manufacture plastic films, bags, stretch wrap, covers, lids, toys, and cable insulation.
The molding temperature for LLDPE is 90 degrees Celsius to 110 degrees Celsius.
Acrylic (PMMA)
PMMA, also known as acrylic glass, is a transparent thermoplastic often used as a replacement for shatterproof glass. PMMA is fully recyclable, but due to its similarities to glass, it is usually combined with various additives or fillers to enhance specific properties such as impact resistance, flame retardancy, chemical resistance or UV light filtering.
PMMA also has a quite high density (1.17-1.20 g/cm3) which confers strength while not making the material too heavy.
Advantages of Acrylic (PMMA) for Injection Molding
The advantages of Acrylic (PMMA) for Injection molding are listed below:
- Transparent
- Tough and durable
- Scratch-resistant
- Resistant to weathering and UV
- Resistant to chemicals(detergents, cleaners, acids, alkalies, hydrocarbons)
- Good dimensional stability
Disadvantages of Acrylic (PMMA) for Injection Molding
The disadvantages of Acrylic (PMMA) for Injection molding are listed below:
- Limited heat resistance
- Attacked by organic solvents
- Poor wear and abrasion resistance
- Can crack under heavier loads
- Low impact resistance
Uses and Applications of Acrylic (PMMA) in Injection Molding
Common uses of Acrylic in Injection molding include: Interior and exterior panels, bumpers, fenders, screens (including smartphone screens), dental equipment, and medical storage devices.
For more information see our Acrylic (PMMA) Guide.
Polystyrene (PS)
Polystyrene is a very commonly used plastic in packaging applications and consumer goods due to its relatively low cost. However, PS-based litter takes a very long time to decay. Depending on the type, PS can either be classified as a thermoplastic or thermoset (a plastic that is not melted for processing).
Besides the low cost, polystyrene is easily processable for techniques including gluing, painting, cutting, and sanding.
Advantages of Polystyrene (PS)
- Cheap
- Transparent
- Easy to mold and process
- Good electrical properties
- Rigid
Disadvantages of Polystyrene (PS)
- Poor chemical resistance
- Flammable
- Brittle
Applications of Polystyrene
Applications and uses of polystyrene include: packaging, toys, cutlery, cassette cases, electronic housing, containers, glazing, and tool cases.
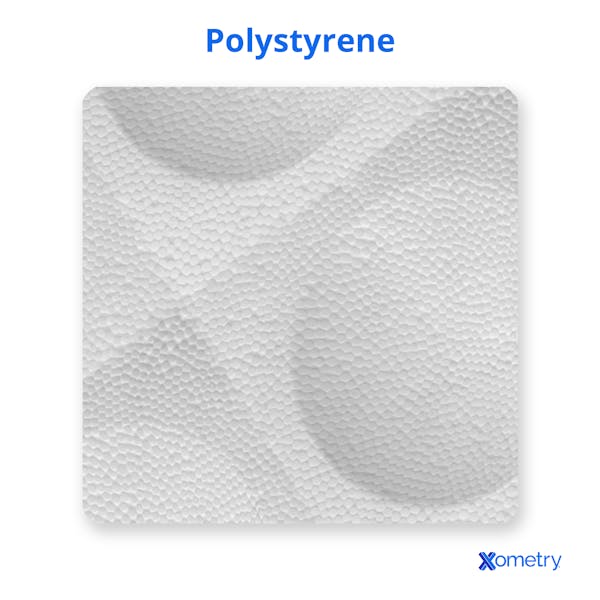
Polypropylene (PP)
Polypropylene is made of a combination of propylene monomers. It’s used in everything from industrial automotive to consumer products. A notable feature of this plastic is its glue resistance, meaning that glue will have a hard time sticking to parts made of this material. For this reason, welding is usually employed whenever bonding is needed.
PP also exhibits a low density and a relatively high coefficient of friction. Because of this, polypropylene may not be the best injection molding plastic to use in high friction environments.
Advantages of Polypropylene (PP)
Advantages of Polypropylene include:
- Polypropylene is highly resistant to solvents such as fats
- Polypropylene is resistant to bases and acids
- Polypropylene is Fatigue-resistant
- PP has high resistance to electricity (can act as an insulator)
- PP has high impermeability
Disadvantages of Polypropylene (PP)
Disadvantages of Polypropylene include:
- Polypropylene is subject to oxidation at higher temperatures
- Polypropylene is will show plastic deformations relatively early in the deformation process
- Polypropylene is affected by UV (will suffer property degradation)
- Polypropylene is hard to paint over
- Polypropylene is flammable
Applications of Polypropylene (PP)
Application of PP include: pipes, laboratory equipment, pallets, and hinges.
Read more at our Polypropylene (PP) Guide.
Polyether Ether Ketone (PEEK)
PEEK is a versatile molding resin ideal for applications requiring sterilized equipment or containers. It is highly resistant to chemicals and heat and capable of resisting submersion in liquids long-term. It also can generally be subjected to harsh operational environments.
The mechanical properties of PEEK allow it to be used as reinforcement material in various scenarios.
Advantages of Polyether Ether Ketone (PEEK)
- PEEK is fatigue and stress-resistant.
- PEEK is resistant to high-pressure water and steam.
- PEEK has high chemical resistance.
- PEEK can be subjected to sterilization (like in autoclaving).
- PEEK is easy to manufacture.
- PEEK has very low emissions when exposed to flame.
Disadvantages of Polyether Ether Ketone (PEEK)
- PEEK is expensive.
- PEEK can be attacked by halogens and acids.
- PEEK has low resistance to UV light.
Applications of Polyether Ether Ketone (PEEK)
Applications of PEEK include: tubes, bearings, seals, valves, electrical cable insulation, medical implants, sterilized containers, pumps, heavy machine parts, and compressors.
Read more at our Polyether Ether Ketone (PEEK) Guide.
Summary
This guide presented an understanding of the most common plastic injection molding materials.
About Xometry
Xometry offers a full range of injection molding services to assist with your production needs. Visit our website to explore the full range of our capabilities or to request a free, no-obligation quote.
Disclaimer
The content appearing on this webpage is for informational purposes only. Xometry makes no representation or warranty of any kind, be it expressed or implied, as to the accuracy, completeness, or validity of the information. Any performance parameters, geometric tolerances, specific design features, quality and types of materials, or processes should not be inferred to represent what will be delivered by third-party suppliers or manufacturers through Xometry’s network. Buyers seeking quotes for parts are responsible for defining the specific requirements for those parts. Please refer to our terms and conditions for more information.
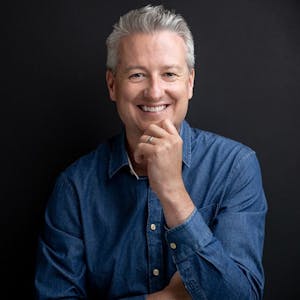