Although it’s more than 100 years old, rotational molding is still popular with manufacturers who want to make high-quality and uniform products. It’s quite a fascinating process and can make a wide range of products, from hollow water tanks to kayaks. If you want to know how to use this process in your business, this article explains all the ins and outs of rotational molding, as well as how Xometry can help lessen your company’s workload with this process.
What is Rotational Molding?
Also known as roto molding, roto casting, or roto mold, rotational molding features a large machine with molds in the right shapes and specifications needed for the final product—whether it’s a container for holding chemicals or a children’s plastic slide. It’s often compared to the blow molding process, but rotational molding costs much less and is more versatile.
The steps that commonly take place when it comes to rotational molding, though they’ll vary slightly depending on the product and material, involve heating and slowly rotating a hollow mold with powdered plastic (usually polyethylene) inside in various directions. The heat melts the plastic powder, and it sticks to the inside of the mold. The rotating trick helps it do so evenly. It’s then cooled and allowed to harden before the solid part can be taken out of the mold.
The process is quite slow compared to other super speedy high-pressure processes. Many machines spin molds around eight rotations per minute, and it can take up to three hours to complete. Even still, it’s a remarkably effective method for creating hollow, one-piece construction products.
There are specific materials that are better suited to this type of molding, and you’ll find that polyethylene is the most common because of its low cost, thermal stability, and the structural integrity it has after cooling. A very tiny percentage of companies use other materials, like silicone, ABS, and acrylic, but that’s extremely rare for most applications.
To help you visualize what this looks like, you can see several important steps from the rotational molding process in the image below, including filling, heating, cooling, and removing the product from the molds.
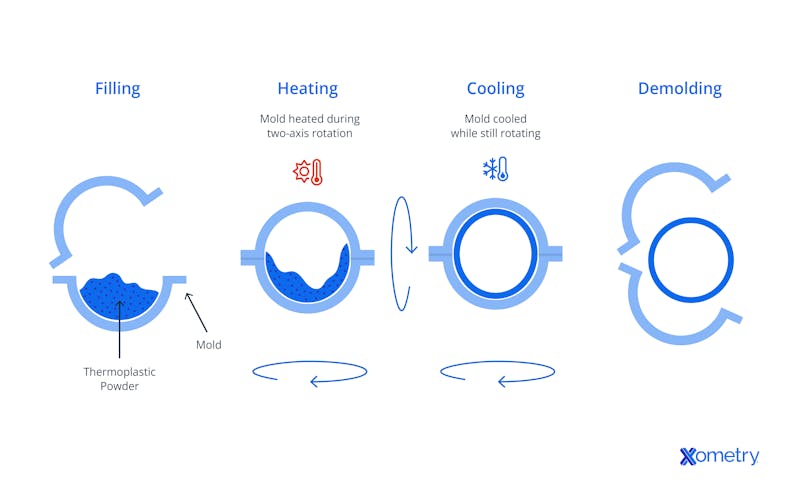
Types of Machines Used for Rotational Molding
There are several types of rotational molding machines to consider, and the best one for your operation will depend on the type, size, and use of the products you’re interested in making.
Turret Machines
This type of roto molding machine has between three and six rotating arms, which makes it look similar to an amusement park ride. It’s built in such a way so that each mold on all of the arms gets the same number of rotations, level of heat, and cooling time.
Rock and Roll Machines
No, this machine isn’t musically inclined. In fact, its name speaks to the motion it moves in when shaping products. It has a tilting oven and automatic cart movement, which makes this large piece of equipment ideal for bigger roto mold products, like tanks and vessels.
Clamshell Machines
These smaller machines have a lid that opens and closes similar to a clamshell, and they’re a good fit for businesses after low-quantity production orders. Normally, they’ll have one arm and an oven, meaning they’re more compact and great for smaller facilities, too.
Open-Flame Machines
An open-flame machine has exactly what its name suggests, rows of open flames that get as close as possible to the molds. If you want to make cylindrical parts, it’s worth looking into because it’s efficient and cost-effective.
Shuttle Machines
This style of roto mold machine is great for larger quantities and bigger products because it contains two carts and two stations as well as an oven. Operators can choose to use one station at a time or both, which cranks up efficiency and productivity and keeps the process running smoothly since multiple steps are happening at once.
Applications and Uses
While it might seem niche, roto casting can be a helpful process for making all kinds of interesting and useful products like:
- Watercraft like kayaks, canoes, and pontoons
- Containers and vessels for storing chemicals, water, and other loose goods
- Kids toys, such as tricycles, slides, and playground equipment
- Trash cans and recycling bins
- Coolers, usually the portable kind for food and beverages
- Tanks for processing and agricultural needs
- Carts and carriers
- Barriers for roads and highways
Factors to Consider When Designing Parts
There are a few unique details to be mindful of when you design a product to be made with rotational molding. These might not come up when you’ve worked with other manufacturing methods:
- Draft angles: By factoring a draft angle into your part’s design, it’ll be easier for operators to remove the components from the molds after the rotating, heating, and cooling process.
- Wall thickness: Think about how thick you intend the walls of your product to be as this can affect the heat transfer rate and how long it takes for the part to cool down. If you’re working with the ever-popular polyethylene, a good rule of thumb is 0.125 and 0.25 inches of thickness.
- Large flat surfaces: To prevent the material from distorting, it’s best to add steps or recesses to these types of surfaces. Parallel walls are also prone to the same issues, but making sure they’re evenly spaced will prevent them from getting too thin.
- Material flow around corners: Rotational molding isn’t the right process if you’re looking for extremely sharp corners and edges. As the material melts, it can get caught up in these points, leading to uneven coatings and bridging. So, it’s better to opt for smoother corners and less severe radii.
- Aesthetics and extra details: If there are small details and flourishes you can work into the overall design, it’s worth testing out so the final product is attractive when it reaches your customer's hands.
Costs
At face value, rotational molding—and all the equipment and tools that are necessary for this process—may seem expensive. But from a long-term perspective, this investment will usually pay for itself. In comparison to other molding techniques, it’s actually pretty affordable as far as start-up costs go. Pulling information from one case study, you’ll find it’s much cheaper than blow molding. For 50-gallon trash cans, the tooling cost was $20,000 and the maintenance cost was $1,000 a year for rotational molding, whereas blow molding the same product would cost $210,000 for tooling and $5,000 a year for maintenance.
Advantages and Disadvantages
Here are some of the reasons that this manufacturing method is so loved (and hasn’t gone extinct even after a century):
- Products come out with even sides and thicknesses all around thanks to the consistent rotation of the machine.
- Its low-pressure operation means you can use metals like aluminum for the mold (something that can’t be said of many other types of molding).
- Creating double-walled containers is a cinch and doesn’t have arduous post-processing needs.
- No need for joining with this method—roto molding makes a one-piece construction, saving time, money, and manual labor.
- During the process, the material stays stable, meaning fewer defects, flaws, and deformations on the finished product.
And now for the downsides:
- It can only really work well with thermally stable materials.
- The machinery and tools needed are pricey, and the price only goes higher when it comes to larger sizes of molds and those that are custom made.
- It takes longer than some other molding processes, so your timeline may be drawn out.
How Xometry Can Help
Our team’s biggest goal is to help you with manufacturing and processing needs and we have a long list of solutions to do so. We offer various molding options, including quick-turn molding, prototype molding, bridge molding, insert molding, overmolding, and assembly.
Disclaimer
The content appearing on this webpage is for informational purposes only. Xometry makes no representation or warranty of any kind, be it expressed or implied, as to the accuracy, completeness, or validity of the information. Any performance parameters, geometric tolerances, specific design features, quality and types of materials, or processes should not be inferred to represent what will be delivered by third-party suppliers or manufacturers through Xometry’s network. Buyers seeking quotes for parts are responsible for defining the specific requirements for those parts. Please refer to our terms and conditions for more information.
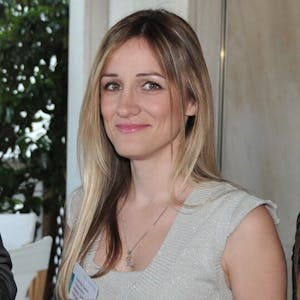