By now, you’ll likely be aware of how much we love CNC (computer numerical control) machines here at Xometry. They’ve made otherwise arduous manual manufacturing processes, like cutting, drilling, and turning, practically effortless via automation. With CNC machining, almost everything is computerized, so these processes are more accurate than manual methods, resulting in higher-quality parts. Most CNC machines are either 3- or 5-axis, and, in this article, we’ll look at their differences and what they’re each good for.
3-Axis CNC Machining
A 3-axis CNC machine, such as a lathe, mill, or machine tool center, moves its tool (whether it’s a cutter, drill, or mill) along the X (left to right), Y (front to back), and Z (up and down) axes. More specifically, it can move either horizontally (X-Y axes) or vertically (Z axis) to control the cutting depth. This is what a 3-axis CNC machine looks like:
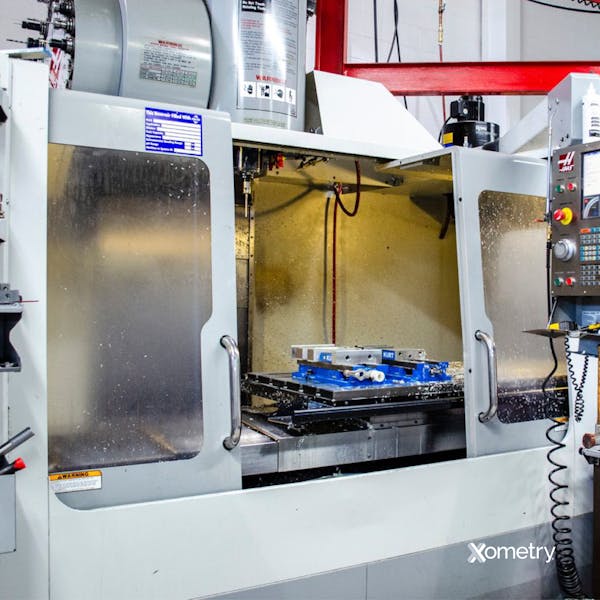
This type of machine can cut and plane to specific depths, depending on the tool used and the material being worked on. Its limited range of motion and the fact that it can’t automatically rotate the workpiece make it best for making simpler parts with straightforward shapes and designs and minimal details. These machines are best for making 2D and 2.5D parts and shorter production runs, and they’re reasonably priced, making them ideal for startups or small to medium-sized businesses.
5-Axis CNC Machining
As well as left–right, front–back, and up–down, a 5-axis CNC machine has two more movements up its sleeve: it can also rotate its tool around the other two axes (A and B). You can see how the process works in the diagram below.
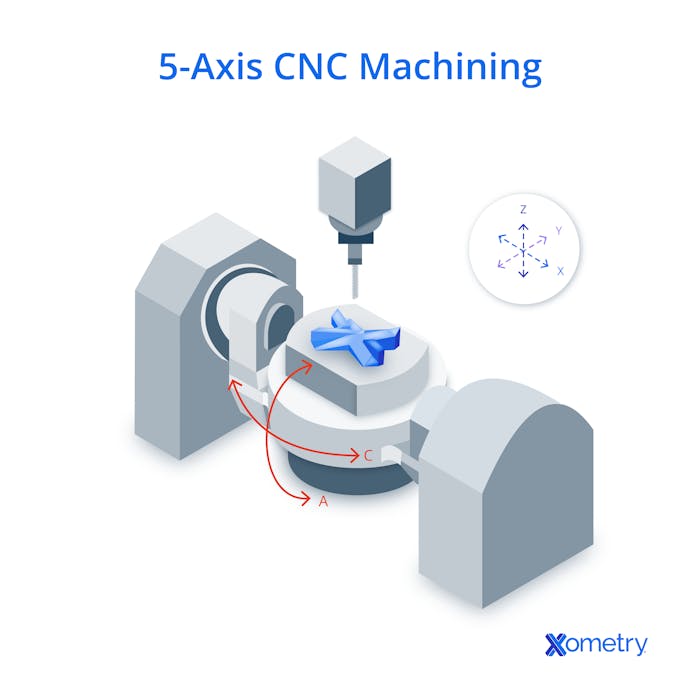
With a full five-axis range of motion, these machines can work at multiple angles to precisely make complex and intricate parts with smooth surfaces, angles, and contours. They can also perform continuous milling, which saves a lot of time, and don’t need any manual intervention as they rotate the workpiece automatically. These high-tech CNC and milling machines or routers can make turbine blades, molds, and impellers, such as the one in the below image.
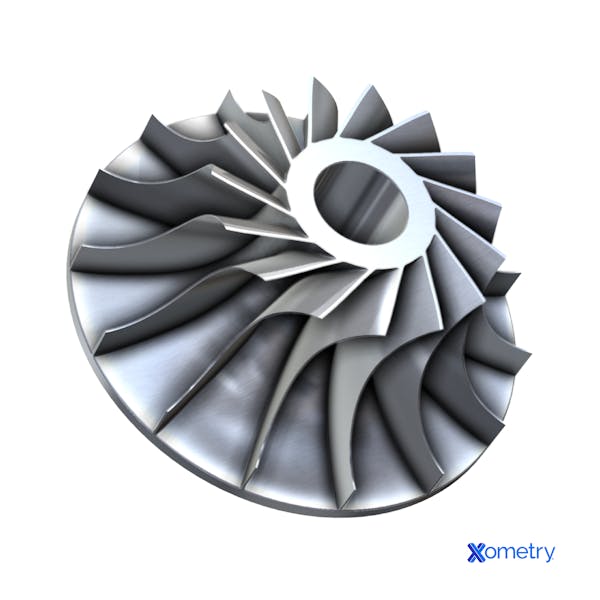
Factor | 3-Axis | 5-Axis |
---|---|---|
Factor Cutting tool movement | 3-Axis Along X, Y, and Z axes | 5-Axis Along X, Y, Z axes, and also along A and B rotational axes |
Factor Efficiency | 3-Axis Good | 5-Axis Excellent, quick |
Factor Tool changes | 3-Axis Need multiple setups for complex parts (re-clamping, repositioning, etc.) | 5-Axis Minimal, can work on part from different angles without repositioning |
Factor Capabilities | 3-Axis Limited, no complex shapes, undercuts, or multi-sided features | 5-Axis Can make deep cuts on all sides of workpiece, intricate shapes and undercuts |
Factor Accuracy | 3-Axis Good | 5-Axis Excellent |
Factor Ease of operation | 3-Axis Minimal training needed, simple to use and program (CNC programming skills needed) | 5-Axis Needs specialized training and expertise and more advanced CAD/CAM programming |
Factor Cost | 3-Axis $25,000 to $50,000 | 5-Axis $80,000 to over $500,000 |
Factor Maintenance/operating costs | 3-Axis Low | 5-Axis Higher |
Factor Cost per part | 3-Axis Lower | 5-Axis Higher, although faster production could lower cost of more complex parts |
Factor Maintenance needs | 3-Axis Low due to fewer moving parts | 5-Axis High, needs regular maintenance to run smoothly |
Factor Wear and tear | 3-Axis Less prone | 5-Axis More prone due to additional moving parts |
Factor Applications | 3-Axis Simpler parts for automotive, aerospace, and electronics (housings, panels, flat surfaces) | 5-Axis Many different sizes and shapes, aircraft engine parts, medical implants and prosthetics |
3-Axis vs. 5-Axis: Pros and Cons
How Xometry Can Help
Xometry provides a wide range of manufacturing capabilities including CNC machining, 3D printing, injection molding, laser cutting, and sheet metal fabrication. You can get started today by quickly and easily uploading your designs to the Xometry Instant Quoting Engine®.
Disclaimer
The content appearing on this webpage is for informational purposes only. Xometry makes no representation or warranty of any kind, be it expressed or implied, as to the accuracy, completeness, or validity of the information. Any performance parameters, geometric tolerances, specific design features, quality and types of materials, or processes should not be inferred to represent what will be delivered by third-party suppliers or manufacturers through Xometry’s network. Buyers seeking quotes for parts are responsible for defining the specific requirements for those parts. Please refer to our terms and conditions for more information.
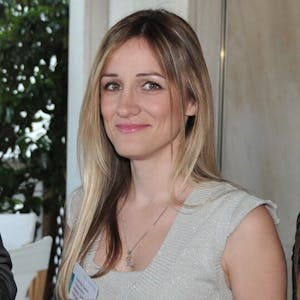