Angle milling is a machining process that removes material at a non-orthogonal angle to the workpiece’s axis. It is commonly used to create beveled edges, chamfers, and other angled features required for functionality, aesthetics, or assembly. Depending on the setup, angle milling can be performed using machine adjustments, specialized cutters, or a combination of both.
This article explores the fundamentals of angle milling, including its applications, processes, types of cutters, and best practices.
What Is Angle Milling?
As mentioned above, angle milling is a machining process used to remove material from the edges or faces of a workpiece at an angle other than 90° to the machine axis. This process is performed using a milling machine with an adjustable quill, a rotary table, a fully orientable work clamping setup, and/or an angled cutting tool. Angle milling creates beveled edges, chamfers, and more complex angled features on the workpiece. In the most basic milling setup, where neither the workpiece holder nor the machine spindle axis can be adjusted, excellent angle milling results can still be achieved by the use of specialist angled cutters. A common example is a countersink tool, primarily used to apply a bevel to the edges of cylindrical holes rather than general angle milling operations. A stiffer version of the same cutter can be used in climb or conventional milling to cut on one side, for holes larger than the cutter diameter, or for irregular holes and straight edges.
Similar results can be achieved using a range of single and double-angle specialist side cutters that allow the selection of fixed and precise angles of surface to be extracted from the part.
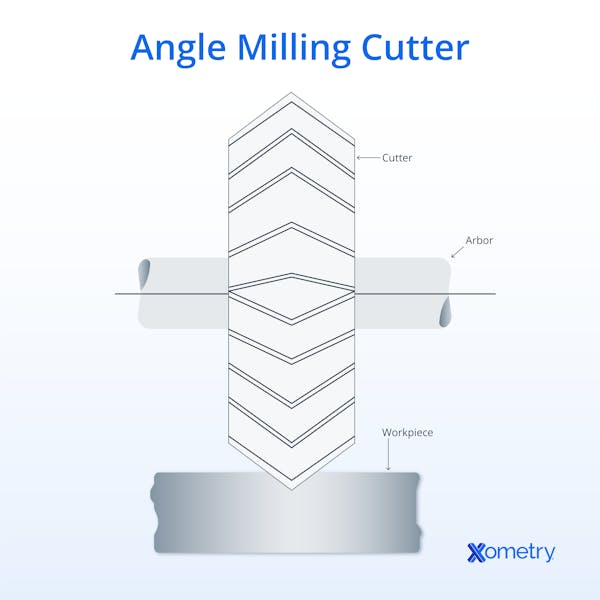
Is Angle Milling and Angular Milling the Same?
Yes, angle milling and angular milling are often used interchangeably. However, in some contexts, angle milling refers to cutting at a single fixed angle, while angular milling may involve machining multiple angled surfaces or contours. For example, angle milling typically refers to the process of milling at a specific angle relative to the workpiece's axis. Angular milling can have a slightly different interpretation and might refer to the milling of angular surfaces or contours, including angle milling, in a more generalized process description of the creation of complex and potentially multi-angled features.
What Is the Purpose of Angle Milling?
Angle milling removes material at an angle other than 90° to the workpiece’s axis, using machine adjustments or specialized cutters. It is used to create beveled edges, chamfers, and angled features for welding preparation, part engagement, weight reduction, and improved clearance in mechanical assemblies.
What Are the Features of the Angle Mill Machine?
Milling machines are versatile tools used for removing material from workpieces to create specific shapes or surfaces at various angles. The specific angled milling capabilities of a mill setup can vary extensively, depending on various machine features.
The spindle is the primary component that holds and rotates the cutting tool. It is responsible for material removal during milling. The machine table is where the work is secured. On basic machines, it can be moved on three axes but not rotated or angled. On more complex machines, the work-holding apparatus can include manual adjustment (a rotary table) or full rotational powered-axis motility (on a 5+ axis CNC machining center).
Milling machines use various cutting tools, such as end mills and face mills, which can be applied using an angular preset of the spindle axis, and an adjustment of the workpiece angle by various means. However, special angled cutters can also be employed to deliver angular offset cuts alone or in combination with other machine capabilities. More advanced machines are equipped with computer numerical control (CNC) systems that allow for automated and programmable machining operations. Different degrees of freedom can be dynamically adjusted during machining, improving toolpath efficiency and minimizing tool changes for complex cuts. Various work-holding devices, such as vises, clamps, and custom fixtures, can secure workpieces at precise angles, allowing vertical cutters to produce accurate angled faces.
How Much Does Angle Milling Cost?
The cost of angle milling varies based on several factors, such as:
- Material: The type and hardness of the workpiece material can influence tool wear and machining time, significantly altering costs.
- Complexity: More intricate bevels and angles will require additional setup time and tool changes, resulting in higher costs.
- Precision: Tighter tolerances and higher precision requirements may increase costs as they demand more careful tool selection and setup. Angle settings provide additional axes for error in setup or toolpath, and angular tolerances can be harder and more costly to control because of this.
- Tooling: The choice of angular milling cutter can impact costs, as specialized cutters cost more due to the relatively small demand for them.
How Does Angle Milling Differ From Traditional Milling?
Angle milling and traditional milling share the same fundamental principle of material removal, but they differ in terms of the machining angle. In angle milling, the material is removed at specific angles other than 90 degrees relative to the workpiece's axis. This allows for the creation of beveled edges, chamfers, or angled features on the workpiece. Traditional milling, on the other hand, typically involves cutting at right angles to the workpiece's axis, resulting in flat surfaces or features. The key distinction is that angle milling focuses on machining at non-90-degree angles, enabling the creation of more complex geometric features and angled surfaces.
To learn more, see our All About Milling in Machining article.
Is Angle Milling Better Than Angle Grinding?
It depends. Angle milling is a precision machining process that is used to extract non-orthogonal surfaces from a workpiece. This might involve light beveling of feature edges to remove sharp corners. It can also be used to apply a lead-in for holes that must receive a close-fit component.
An angle grinder, on the other hand, is a freehand grinding wheel that is used for freeform surface alteration and cutting, including approximate beveling. While some applications in which beveling is required may achieve satisfactory outcomes by use of a manual process such as angle grinding, these would be limited by differentials in the quality of the outcome.
Although both processes involve material removal, angle milling is a precise machining method, whereas angle grinding is a manual process primarily used for rough shaping or finishing. They serve different functions, and direct substitution between them is uncommon.
How Does the Angle Milling Process Work?
Angle milling is a machining process that removes material from a workpiece at a specific angle other than 90° to its primary axis. This can be achieved by adjusting the cutter axis, tilting the workpiece, or using specialized angled cutters. It is a versatile process that allows for the extraction of beveled edges, chamfers, and angled features on workpieces, making it a valuable technique in various industries. The complexity of angled features and surfaces that can be created depends heavily on the capabilities of the equipment, the availability of specialist cutters, and the ability to create custom fixtures to support/retain workpieces in non-right-angled positions.
What Are the Types of Angle Milling Cutters?
Angle milling cutters come in diverse types and sizes, tailored to specific machining needs and applications. Listed below are common types of angle milling cutters, though other specialized tools, such as dovetail cutters and chamfer mills, may also be used for specific applications.
1. Single Angle Milling Cutters
Single-angle milling cutters are designed to create a single-angled surface on a workpiece. They are available in standard angles such as 30°, 45°, 60°, and 90° and can be custom-made for specific requirements. These cutters typically feature cutting edges around the circumference and are used for chamfering, beveling, and angled slotting.
2. Double Angle Milling Cutters
Double-angle milling cutters have cutting edges on both sides of the circumference, allowing the machining of two angled surfaces in one operation without a tool change. They are used for V-grooves, dovetail slots, and undercuts and come in both symmetrical and asymmetrical designs.
How to Perform Angle Milling?
Angle milling follows the general setup of conventional milling but requires additional considerations, such as work-holding adjustments, specialized cutters, and adapted machining parameters to accommodate angled cuts. The workpiece is securely clamped to the bed or work table of the milling machine using appropriate work-holding devices like clamps, vises, or fixtures. This can involve the use of a rotary fixture that is manual or CNC controlled, allowing the angle of presentation to be manually or dynamically set. The appropriate cutting tool, often a single-angle or double-angle milling cutter, chamfer mill, or dovetail cutter, is selected based on the specific machining requirements. Where a specialist cutter that has the required angle integrated into it is used, this allows angle milling without any other setup specifically related to the cutter angle.
Set the spindle speed and feed rate based on the material type and machining requirements to ensure efficient material removal without causing tool wear or overheating. Angled tools can have some specialist requirements in this regard, as options in flute angle and number of flutes can be more limited than for general cutters. The milling proceeds as the cutting tool engages with the workpiece. The tool advances along the workpiece, and the material is removed, extracting the angled surface or feature in a single plunge (Z-axis) cut or multiple X/Y cuts with Z steps. A coolant stream is used to cool the cutting tool and workpiece and to aid in chip evacuation.
When To Use Angle Milling?
Angle milling is used when beveled edges, chamfers, or angled features are required on workpieces. The process can do the following: remove sharp edges and burrs from workpieces, create beveled edges on parts for welding to ensure deep penetration and fusion, deliver improved aesthetics of components, prevent or reduce stress concentrations in components, create functional features requiring specific angles, reduce part weight, and act as roughing in preparation for complex and compound curvature surface cutting.
What Industries Use Angle Milling?
Any industry that uses milled components may require angle milling for creating beveled, straight-angled, and compound-angled surfaces, particularly in aerospace, automotive, and tool-making applications:
- Aerospace applications, in which machining complexity is less important than final part weight. Angle milling is used to remove low-stress material for weight saving and improve stress distribution by easing sharp corners.
- Furniture production, in which aesthetic considerations override basic cost concerns, allows complex surfaces to be used for visual appeal.
- Sports equipment, in which handling is expected, to remove sharp edges.
- Machinery manufacture, in which both reliefs of sharps and reduction of weight in fast-moving parts require/allow complex surfaces and additional machining costs.
What Materials Are Suitable for Angle Milling?
Any material that is suited to milling is amenable to angle machining. Listed below are some materials:
- Tool/alloy, stainless, high-, and medium-carbon steels
- All aluminum grades except pure aluminum
- Exotic metals, such as titanium, advanced nickel alloys, tungsten, niobium, and tantalum
- Engineering plastics
- Rigid composites
- Ceramics
- Stone
Is Angle Milling Suitable for Cutting Metal Pipes?
Yes, angle milling is suitable for beveling and angle-cutting metal pipes. However, in high-production environments, lathe-based or tube-cutting processes may be more efficient alternatives. It is also common to angle-cut the ends of pipes to a non-orthogonal profile. In both cases, angle milling is an option for processing components from pipes.
Is It Possible To Use Angle Milling on Stainless Steel?
Yes, stainless steel responds well to angle milling, but it requires carbide or coated cutting tools, high feed rates, and ample coolant to prevent work hardening and tool wear.
What Are the Tips for Angular Milling?
Angular milling requires attention to detail and precision to deliver useful and high-quality outcomes. Listed below are some tips to remember:
- Ensure that the job is possible and that the workpiece is securely and accurately set up in the work-holding device or fixture.
- Choose sharp and undamaged cutters suited to the angle and material type.
- Use precise measuring instruments to verify the machining angle, whether adjusting the machine, work-holding fixture, or selecting a pre-angled cutter to achieve the desired feature.
- Follow safety protocols, including the use of PPE and machine guards.
- Maintain a consistent and appropriate feed rate to reduce tool wear and achieve a smooth surface finish.
- Use appropriate coolant or air-blast systems to control heat buildup and aid in chip evacuation.
- Use effective workpiece clamping to minimize vibrations and ensure stability during machining.
- Set appropriate spindle speed and feed rates according to the material and cutter type.
- Check the alignment of the milling machine's worktable and/or head using a dial
gauge or other suitable alignment system to ensure accurate cutting.
- Regularly check the angular and linear dimensions of the cut and make any necessary adjustments during machining.
- Inspect the workpiece after angular milling to verify that linear and angular dimensions and surface finish meet specifications. Perform any required finishing or deburring.
What Is the Difference Between Angle Milling and Conventional Milling?
Angle milling and conventional milling are closely related but distinct machining methods. At its core, angular milling is simply one form of milling, and generally only an element of an otherwise conventional milling process, rather than a distinct process
Angle milling delivers cuts at specific angles other than 90° to create beveled edges, chamfers, or angled features. The process uses specialized angular cutters designed for bevels or chamfers, or angled machine setups, or a combination of the two. It is employed when beveled or chamfered edges are needed for aesthetics, weld preparation, or reducing stress concentrations.
Conventional milling, on the other hand, generally involves material removal perpendicular to the workpiece and machine axes. Standard end mills and milling cutters are used, although these can serve in angle milling when the spindle or workpiece is angled appropriately. Conventional milling is used for general milling operations, such as facing, slotting, and contouring.
Summary
This article covered angle milling, explaining its process, types, and applications. To learn more about angle milling, contact an Xometry representative.
Xometry provides a wide range of manufacturing capabilities, including machining and other value-added services for all of your prototyping and production needs. Visit our website to learn more or to request a free, no-obligation quote.
Disclaimer
The content appearing on this webpage is for informational purposes only. Xometry makes no representation or warranty of any kind, be it expressed or implied, as to the accuracy, completeness, or validity of the information. Any performance parameters, geometric tolerances, specific design features, quality and types of materials, or processes should not be inferred to represent what will be delivered by third-party suppliers or manufacturers through Xometry’s network. Buyers seeking quotes for parts are responsible for defining the specific requirements for those parts. Please refer to our terms and conditions for more information.
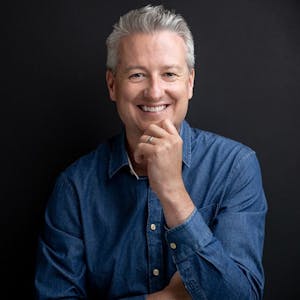