CAM (computer-aided manufacturing) milling is a process that uses software to automate the controls of milling machines to make complex objects in many different materials, like metal, polymer, and composites. It has many benefits, including high accuracy and precision, efficiency, and repeatability, making it a valuable tool for many industries.
At Xometry, we make a lot of complex parts, often with elaborate compound angles, freeform surfaces, undercut features, and more, all of which need to be machined to tight tolerances. Without the use of CAM, producing such components to specification would be virtually impossible.
In this article, we’ll go over exactly what CAM milling is, how it works, what materials it can work with, and we’ll also have a look at some of its challenges.
What is CAM Milling?
Before we dive into what exactly CAM milling is, let's start with an analogy. In the past, if you needed to drive someplace far away, you might have had to plan a route manually by using road maps and stick to that route to make it to your destination. Nowadays, most people use GPS devices or apps to plan their road trips and can benefit from the automation and handy features they offer, such as automatic re-routing when you take a wrong turn or route optimization based on traffic or road conditions. In this case, CAM is a lot like a GPS, helping machinists navigate the traditional machining process and offering automation and other features to make things more efficient and to create more complex parts.
The CAM software automates the process on CNC (computer numerical control) machines by translating CAD designs into code instructions that milling machines understand. No manual coding is needed, as CAD works directly with the CNC machine. In this way, programs can be made that are used to craft the same high-quality item thousands of times, cutting down on manual labor, time, and manufacturing costs. These programs can even be saved for later use or shared across multiple machines for parallel production.
CAD and CAM work together via an integrating technology, like Mastercam, to make intricate designs that are quite the feat to produce—especially if a large quantity needs to be made. The main factors that make CAM milling different from manual milling techniques are the fact that it’s much more efficient and precise, can easily make complicated shapes, and can be used with CAD to create programs. Everything with CAM milling is automated, so it’s a big time-saver, too.
CAM milling is an umbrella term used to describe all types of milling processes that can be controlled via CAM. Three examples are face milling, pocket milling, or contour milling, and each is better suited to different tasks. Face milling is used for flat surfaces, pocket milling for creating pockets or cavities, and contour milling is best for detailed and curved surfaces. There are also advanced CAM procedures like high-speed machining, adaptive machining, and multi-axis milling.
The Evolution of CAM Milling
Numerical control (NC) machines came out in the 1950s and the relevant technology to control them has progressed a great deal since then. In the 1940s, John T. Parsons wanted to speed up the industrial processses in his family manufacturing company, so he started working on what we now know as an NC machine. After years of hard work and in collaboration with an engineer, Frank Stulen, the first prototype was demonstrated in 1952.
In 1957, Dr. Patrick Hanratty created the first NC G-code, PRONTO, which was further developed with the help from engineers at MIT's Servomechanisms Laboratory. It wasn’t until the 1970s that CAM and CAD started being used together more closely. CAM software initially started as an extension of CAD and was made commercially available with great success in the late 1970s/early 1980s, just as computer technology was starting to take off.
In the 1990s, when CAM moved from UNIX systems to PCs, it became even more accessible and was eventually fully integrated with CAD. It’s safe to say that CAD/CAM technology has completely changed the manufacturing industry for the better. Thanks in large part to its precision, modern CAM/CAD software is used for many processes that Xometry offers, like milling, laser and waterjet cutting, tube bending, and even 3D printing.
Advancements in milling seem to be going in two main directions. The first is using high feed rates and low depths of cut to improve metal removal rates, and the other is using high speeds with low chip cross-sections. One solution that has been adopted in milling is the addition of chip splatter inserts that help keep vibrations down even when the table feed rate has been increased.
Work is also being done on adaptable cutters, i.e., modular systems that can take inserts of all different shapes and forms to avoid having to constantly change tools. Extremely rigid clamping tools (like 160 mm diameter face clamps with XPC spindle units) are also helping to manage high feeds, speeds, and heat. In the future, we can expect even more efficiency from this tech, and perhaps a further blending of engineer and machinist roles with CAM milling.
CAM Milling and CAD
CAM milling and CAD software are like bread and butter; they’re very different but when combined, they make something really special. CAD software, like Autodesk Fusion, is used to create 2D or 3D models and focuses on the design aspect of the parts. Designers can customize intricate parts, and the software will show them what the final product will look like. They can also easily make any adjustments to the design if needed.
CAM software is used to control the manufacturing machinery and automate the processes. It takes the CAD designs and makes toolpaths and instructions for the machinery to follow so it can make the physical parts. For CAM and CAD to work together, an integrating software (like Mastercam) is needed. This software’s job is to ensure that the CAD designs are properly translated into CAM manufacturing instructions. The result is efficient and precise production of even the most complex and customized parts.
CAM Milling Benefits
There are several reasons that CAM milling is so popular in modern manufacturing. Firstly, it allows us to be highly accurate and adhere to very precise specifications. It can be used to program complicated multi-axis machining centers, allowing us to easily make complex and intricate shapes and repeat them over and over again at high speeds with the same outcome. Next, automation saves time, reduces manual labor, and lowers the risk of worker accidents and injuries.
It’s also cost-efficient, as the accurate toolpaths reduce waste material, and the quick turnaround speeds up production and lowers labor costs. Customization options with CAM milling are practically endless. Its ability to adjust the cutting settings, like feed, speed, and toolpath, according to specific materials means that less specialized tools are required. Add CAD integration to the mix, and you’ve got an impressively powerful design-to-production manufacturing workflow.
CAM Milling Challenges
CAM milling has a few drawbacks, mainly in relation to cost and training requirements. The initial investment in the software, compatible hardware, and tools can be quite high.
From programming to milling, precision is the most important factor in the whole machining process, and any slight deviation could lead to defective products. This means that staff will need to be trained to an expert level on both software and machine operations. Even so, factors like tool wear and complex programming could still cause problems. The bottom line is that even though CAM can make our lives easier, the time and effort to learn how to use it effectively is critical. All this training will likely further increase costs, as well as take up valuable time. Thankfully, virtually all trade schools that teach new machining apprentices cover CAM in their curriculums since it's so widely used in today's manufacturing environment.
Finally, there have been a few data-security concerns in CAM milling in relation to safeguarding data and designs from cyber threats, theft, and corruption. To avoid these, thorough security measures need to be taken. These include adoption of secure data management protocols, encryption technologies, access control and authentication mechanisms, continuous monitoring and auditing, and cybersecurity awareness training for all staff. We cover this subject some more in our e-book about Cybersecurity Best Practices for Manufacturing.
CAM Milling Material Selection
Any material that can be traditionally machined can be used with CAM milling, including metal (aluminum, steel, titanium, brass, copper), plastic (acrylic, polycarbonate, nylon, ABS), composites (carbon fiber reinforced plastics, fiberglass), ceramics (zirconia, alumina, silicon nitride), foam (polyurethane, polystyrene), wood, and wood composite. If you’re on the fence about which material to go for, you’ll have to think about what exactly you want to make, and what properties it needs to have.
For instance, for aerospace parts, you’ll need a lightweight but sturdy material, like 7075 aluminum. For outdoor furniture, you’ll need it to be rust- and corrosion-resistant, as well as weatherproof, so something like stainless steel may be up your alley.
All in all, while CAM doesn't directly determine what materials you can use, it does play a pivotal role in how well the chosen material can be machined. For example, it can optimize toolpaths, cutting tool selection, machine settings, thermal management, and more, all based on the material you tell the software you intend to work with. Overall, it removes a lot of the guesswork involved when material changes occur and helps machinists expand their material repertoire.
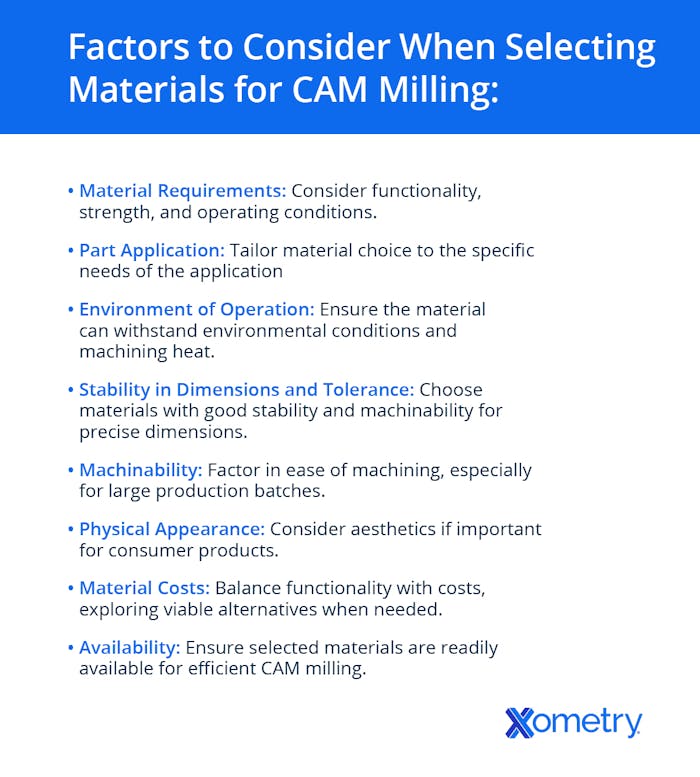
CAM Milling Safety Protocols
Just like with all types of manufacturing, safety protocols are important in CAM milling to keep workers safe. Staff operating machinery should wear all the necessary personal protective gear like goggles, gloves, and ear protection, and the work area needs to be well-ventilated to reduce the chance of them breathing in fumes or vapors. All machinery should be regularly inspected and checked for wear and damage and, if necessary, replaced. All of the machines also need to have emergency stop mechanisms.
CAM Milling Training and Development
Although we’ve already covered this above, it’s worth reiterating the importance of continuous CAM milling training. To make sure that the procedure is accurate, productive, and above all safe, all professionals working with CAM milling software and machinery need to go through training and skill development. Regular refresh trainings are also necessary to keep up-to-date on all the latest advancements in the related software. With proper training, workers will be able to troubleshoot early, improve programs, and reduce mistakes and waste. Overall, ongoing training is the best way to ensure efficient and productive CNC milling operations.
CAM Milling vs. Cam Milling
Yes, you read that right. CAM milling (caps) and cam milling (lowercase) are two very different things. Thankfully, cam milling also goes by “index milling” to save further confusion. Index milling is a machining process that creates cams (irregularly shaped lobes or protrusions on shafts) on a milling machine using a universal dividing head and vertical milling attachment. The dividing head rotates the piece to make the lobes or protrusions, while the milling attachment shapes them. As we’ve already seen, CAM milling involves the use of computer software to control and automate milling processes, making it different from index milling. However, CAM milling can be used to operate and program index milling techniques. Saying that you used CAM to help produce cams is an accurate, albeit confusing, statement!
CAM Milling vs. Face Milling
Face milling is another milling procedure that CAM can operate and program. It uses a milling cutter with teeth on its face to make flat surfaces on a workpiece. Its ability to precisely create smooth, flat, and straight items makes face milling great for gearbox casings and engine blocks.
CAM Milling vs. Saw Milling
CAM milling and saw milling are two entirely different manufacturing methods. CAM uses computer-aided precision and automation, while saw milling is typically a semi-automated process that uses cutting materials and saws. CAM can work with CAD for intricate and precise designs, whereas saw milling is used for simpler designs and cuts; it simply doesn’t have the ability to make precise and complex products as CAM does.
How Can Xometry Help
We hope you have a better understanding of CAM milling and why it's so prevalent in today's manufacturing scene! As we mentioned earlier in this article, there are some downsides to CAM, primarily around training, software cost, and potential cybersecurity concerns. By using Xometry, you can have peace of mind knowing that our platform is secure and that our network of over 10,000 suppliers is expertly trained in using CAM to produce complex and intricate parts with tight tolerances.
Start today by uploading your 3D CAD to the Xometry Instant Quoting Engine® to get an instant quote on CNC milling and more!
Copyright and Trademark Notices
- Mastercam® is a registered trademark of CNC Software, LLC.
- Autodesk Fusion® is a registered trademark of Autodesk, Inc., and/or its subsidiaries and/or affiliates, in the United States.
Disclaimer
The content appearing on this webpage is for informational purposes only. Xometry makes no representation or warranty of any kind, be it expressed or implied, as to the accuracy, completeness, or validity of the information. Any performance parameters, geometric tolerances, specific design features, quality and types of materials, or processes should not be inferred to represent what will be delivered by third-party suppliers or manufacturers through Xometry’s network. Buyers seeking quotes for parts are responsible for defining the specific requirements for those parts. Please refer to our terms and conditions for more information.
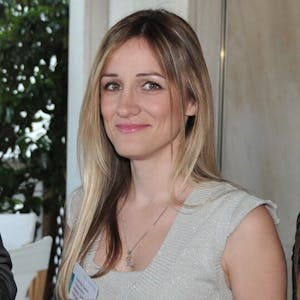