CNC machining makes for a quick and efficient way of production, especially for precise components (even in large batches). It’s little wonder that it’s a firm favorite with manufacturers everywhere. There are, however, plenty of costs associated with this method, which we’ll break down in this article.
CNC Machining Cost Calculator
Before we go into exactly how each part of the process can contribute to how you spend your budget on CNC machining, here’s our very own cost calculator to help you work out how much your custom parts will ring up, and provide you with an instant quote.
CNC Machining Cost Calculator
Cost Breakdown
The costs of CNC machining projects include more than just the material and the machining. Below you’ll find all the factors that impact the final amount you’ll need to pay.
Material Selection
If you’re looking to break down the costs between different types of materials, you’ll have to compare how easily available (or not) they are to find and how easy or difficult they are to machine. High-performance alloys tend to be spendier than common metals, and harder or less machinable materials that need specialized tooling and longer machining time will also affect the total. Choosing more affordable materials is perhaps the most obvious way to cut costs, but standardizing material options across product lines can simplify your procurement process too. This will reduce waste, and improve machining efficiency.
The table below gives you a rough idea of what typical CNC machining materials cost, the forms they come in, and their common applications.
Material | Approx. Cost (USD/kg)* | Form | Applications |
---|---|---|---|
Material Aluminum | Approx. Cost (USD/kg)* $5–$15 | Form Blocks, sheets, rods | Applications Aerospace, automotive, electronics, consumer goods |
Material Stainless steel | Approx. Cost (USD/kg)* $15–$25 | Form Blocks, sheets, rods | Applications Medical devices, kitchenware, industrial machinery, marine |
Material Carbon steel | Approx. Cost (USD/kg)* $2–$5 | Form Blocks, rods | Applications Tools, automotive, heavy machinery |
Material Titanium | Approx. Cost (USD/kg)* $30–$50 | Form Blocks, rods | Applications Aerospace, medical implants, high-performance automotive parts |
Material Brass | Approx. Cost (USD/kg)* $10–$20 | Form Rods, blocks | Applications Electrical connectors, decorative items, fittings, musical instruments |
Material Copper | Approx. Cost (USD/kg)* $9–$15 | Form Sheets, blocks, rods | Applications Electrical components, heat sinks, plumbing fittings |
Material ABS | Approx. Cost (USD/kg)* $2–$4 | Form Sheets, rods | Applications Prototyping, electronics, automotive |
Material Nylon | Approx. Cost (USD/kg)* $3–$6 | Form Rods, sheets | Applications Gears, bearings, machine components, consumer goods |
Material Delrin | Approx. Cost (USD/kg)* $4–$8 | Form Rods, sheets | Applications Precision components, medical devices, mechanical gears |
Material Acrylic | Approx. Cost (USD/kg)* $3–$6 | Form Sheets, blocks | Applications Displays, signage, optical components |
Material Tool steel | Approx. Cost (USD/kg)* $10–$20 | Form Rods, blocks | Applications Cutting tools, molds, dies, high-stress industrial applications |
Material Inconel | Approx. Cost (USD/kg)* $60–$80 | Form Rods, blocks | Applications High-temperature aerospace parts, turbine blades |
Material Magnesium | Approx. Cost (USD/kg)* $10–$20 | Form Blocks, rods | Applications Lightweight vehicle and aerospace parts |
Material Hardwoods | Approx. Cost (USD/kg)* $2–$10 | Form Blocks, boards | Applications Furniture, decorative items, prototypes |
Material Composites (G10) | Approx. Cost (USD/kg)* $30–$50 | Form Sheets | Applications Aerospace, electronics, mechanical parts |
*Based on 2025 estimates
Design Complexity
If your design is complex and has tight tolerances, you can expect to pay a little more. This is because intricacies like these will probably need more advanced machining techniques, specialized tooling, and longer machining times. Although it’s not always possible for some items, if you can simplify your designs and choose more basic products and parts, your costs can go down. If the whole process is a bit confusing, you can reach out to a design engineer to tailor your designs to your specific needs without compromising the functionality and quality of your products. An expert like this can help you get the most out of your money and designs, and even though they will also charge for their services, you’ll likely end up saving a whole lot more in the long run.
Duration
A long machining time almost always equals higher costs. This is due to factors like extra electricity and power being used and the time it takes to cut parts or change tools. The effectiveness of production can also determine how long it’s going to take to get your items machined.
Tooling
Under this category, you can expect to pay for the purchase, maintenance, and/or replacement of the cutting tools used by the machine. The lifespan of the cutting tools and the time required for tool changeovers directly affect efficiency. Proper selection of tools suited to the material and machining process and regular maintenance can reduce machining expenses and improve overall productivity.
Volume/Batch Size
Larger production volumes benefit from bulk prices so there’s lower cost per part as fixed setup costs are spread across more units. Smaller batch sizes will often have higher costs per part, so you should consider whether it’s worth increasing your batch size to keep costs low.
Labor
Skilled CNC operators are responsible for programming, setup, and operation, and are needed for effective and accurate machining processes. When these workers are required to spend more of their valuable time, such as on projects with intricate parts, you can expect additional costs. Further down we mention how automation can help lower what you’ll have to pay for workers.
Overhead
Expenses will start even before you get started making products. Facilities, utilities, administrative operations, quality control, and inspection processes… these are all overheads that will need to be factored in. Effective management is the best way to keep track of everything, make sure you’re within budget, that income is more than outgoings, and that you’re not overpaying for anything.
Waste
Machining errors or deviations from design specifications can lead to wasted material… which is basically money down the drain. You can keep scrap material and the need for reworking parts down with effective quality control measures, precision machining techniques, and thorough inspections. Again, this has to do with management.
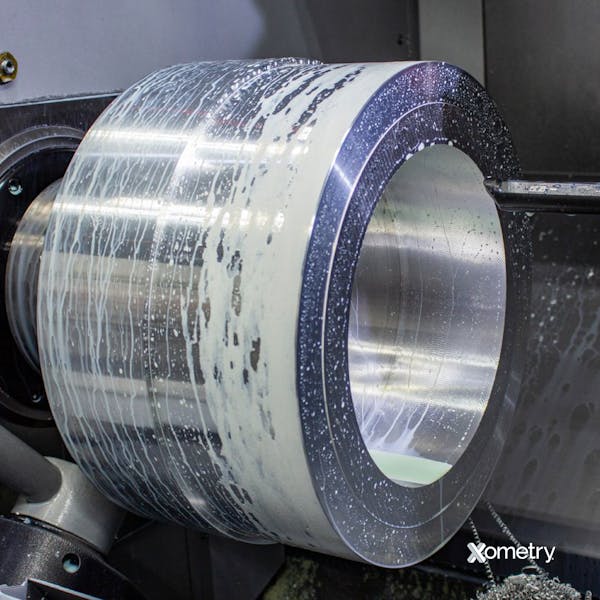
Reducing CNC Machining Costs
In addition to the tips provided in each of the above cost-influencing factors, here are some of the categories in which you can save some cash.
Process
Compex toolpaths will make more movements and more machining time (in other words, more money), but if you try to simplify these, use work-holding solutions, and strategic tool change methods, the process and setup can be sped up. Lean manufacturing techniques such as 5S, value stream mapping, and continuous improvement initiatives will help identify and eliminate waste — which can also be helped with proactive maintenance and scheduling to maximize machine uptime for consistent output.
Automation
Robotics and automation are making their way into every industry, and CNC machining hasn’t been left behind. Here’s why these systems can be more beneficial than using human-powered work:
- Much less likely to make mistakes
- Won't get fatigued—even when working for hours on end
- There aren’t labor laws limiting your use
- Excellent for repetitive tasks and great at repeating the same design or action
- Makes consistently high-quality parts with no variations
- Not as expensive (they might have hefty upfront costs, but more than make up for the initial investment, especially for mass production)
- Very accurate
- Very little waste and reworking needs
Offloading these jobs to robots can give skilled operators the chance to focus on other more complex assignments that are a much better use of their time, energy, and expertise (and your money!).
How Xometry Can Help
For additional information about CNC machining costs, contact an Xometry representative. We also provide a wide range of manufacturing capabilities and other value-added services for all of your prototyping and production needs. Visit our website to snag a free, no-obligation quote.
Disclaimer
The content appearing on this webpage is for informational purposes only. Xometry makes no representation or warranty of any kind, be it expressed or implied, as to the accuracy, completeness, or validity of the information. Any performance parameters, geometric tolerances, specific design features, quality and types of materials, or processes should not be inferred to represent what will be delivered by third-party suppliers or manufacturers through Xometry’s network. Buyers seeking quotes for parts are responsible for defining the specific requirements for those parts. Please refer to our terms and conditions for more information.
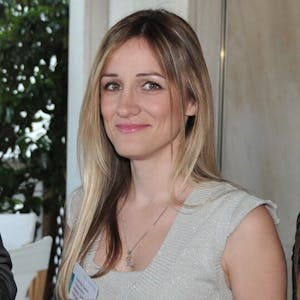