When designing parts for CNC machining, engineers are always trying to push the limits in terms of what’s possible: thinner, lighter, better performance.
One way to achieve this is by incorporating thin walls in a part’s design. This is especially true in the aerospace industry, where having lightweight components is critical, and designing thin walls can help reduce a part’s weight. But as with any manufacturing process, there’s a limit to how far you can push design, and at what cost.
As a general rule of thumb, CNC machined walls should have a minimum width of 1/32” (0.794mm). But, the actual number and costs can vary based on several key factors:
- Wall Height:Thickness (H:T) Ratio
- Wall Height: Length (H:L) Ratio
- Part Geometries and Supports
In some cases, walls thinner than 1/32″ may be possible, but would become cost-prohibitive to machine.
The reason for this is that CNC components with tall, thin walls have a tendency to chatter, which slows down machining speeds. They can also cause distortion, which makes it difficult to hold tolerances. The result can be additional costs.
Besides just wall thickness, this post investigates the other key cost-drivers for CNC machined thin walls.
Note: for other ways on to save on CNC machining, check out our earlier post on the Top 10 Ways to Reduce CNC Machining Costs.
FREE CNC Machining Design Guide
H:T Ratio
In order to keep machining costs low, we recommend a H:T ratio no larger than 10:1. Any bigger than that could cause machining with a poor surface finish (i.e. chatter marks), or sub-optimal parts. Additionally, thin designs tend to have more difficult setups and sometimes require special fixturing, which further drives up costs.
Conversely, designs with short, thin walls, like the part on the right, are inherently more rigid, and thus can be easier, faster and less expensive to mill.
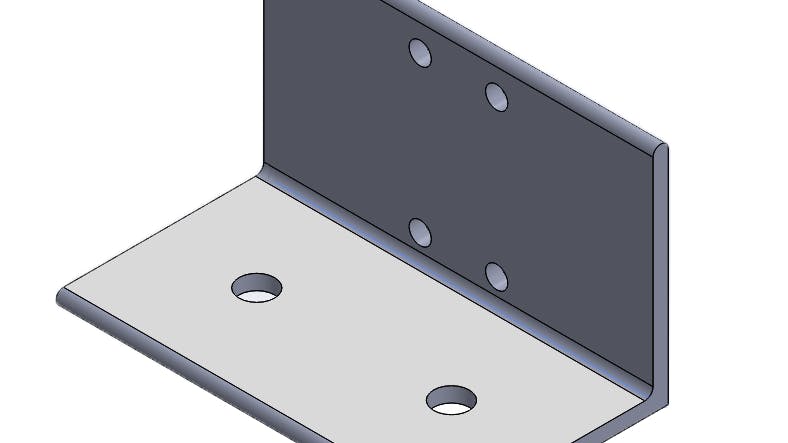
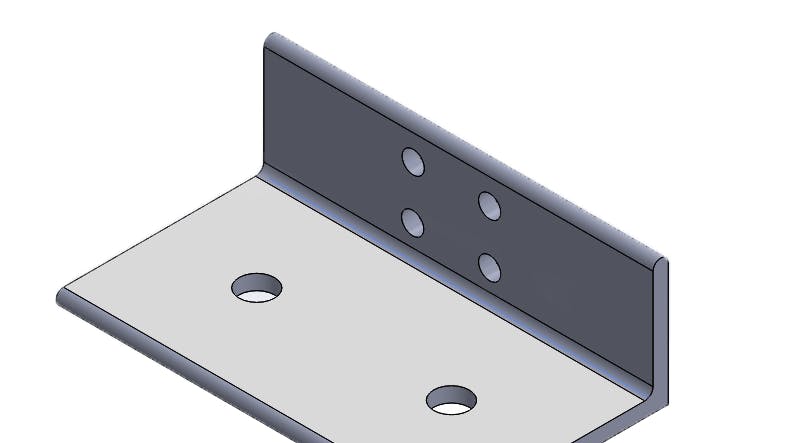
Geometries and Supports
Various part geometries, such as jogs and curved walls, can help stiffen parts and allow for thinner machinable walls.
Similarly, walls that are supported on either end tend to be more rigid and can potentially be made thinner. In some cases, a relatively short wall or rib can have a H:L ratio of 25:1, without significantly impacting cost.
When in doubt about the machinable limits of your design, simply consult your Xometry project manager.
