The profession of CNC Machinist or CNC Machine Operator is a highly skilled one that is exposed to technically challenging work. It can open up a wide spectrum of opportunities such as: programming, product design, quality control, and planning.
For those with the right mix of detail—centered reasoning, a creative approach to problem-solving and time-sensitive delivery, and other critical skills, a CNC machinist position can be a great gateway job. Many have used it as a stepping stone to other facets of engineering and productization. When you dive into the CVs of successful team members in engineering organizations, you may be surprised how many spent their early years at this end of the spectrum.
This article will explore the important CNC machinist skills, their role, how much they earn, and the ways to pursue such a career path.
1. Paying Close Attention to Detail
Nothing focuses the attention quite like the risk of crashing the cutter into the table of a $500,000 machine. If you’re not able to shut out the world and focus hard on a sequential task, then CNC machining work is not for you.
The most important skill for a machine operator is the ability to ‘see the matrix’ — to understand the implications of each step in the process, cut through the noise, and develop the skills to see risks, inefficiencies, and opportunities in developing a manufacturing process. Advanced CNC programmers/machine operators learn to see 3D CAD models as cutter paths expressed in G-code. The step from finished design to cut parts then becomes frictionless. This skill comes from both practice and a detail-focused mindset.
2. IT and Math Abilities
While careful G-code programming is an important part of the CNC machinist’s skillset, it’s not the whole picture. Interpreting drawings or models often means a little creative math and a propensity for juggling numbers. You must be able to envision each action in the machine and mentally evaluate how they’ll affect the process and how the next action will change things further. Efficient G-code programming works by arranging actions in such a way as to optimize the cutting process, minimize movement that isn’t a cut, minimize tool changes, switch diameter offsets when the tool does need to be changed, and make it all flow.
There is a raft of other IT-type skills that make an operator stand out. Gain an understanding of some or all of the following: CAD, G-code editors, simulators, file management, customer communications, work planning tools, quality control and audit tools, and more.
The best CNC machinists become masters of interoperability and learn to integrate multiple processes seamlessly into an optimized whole.
3. Practical Abilities
Programming and part/cutter path optimization are only part of the skillset. The greatest challenge is the hard engineering of setup.
No two designs are quite the same, and each will present its own challenges. You may not always get much time to solve these previously invisible tasks. They often demand that you understand:
- Material preparation — squaring and facing billets of raw materials
- Material clamping — how to locate and lock a billet into place for cutting
- Jigs and fixtures — many machining tasks require specialist jigs to be made
- Cutter selection — different cuts require different tools, but it’s best to minimize the tool changes to reduce machining time
CNC machinists require a good understanding of general engineering principles and good practical skills in handling tools. These skills are highly transferable, but often require specialist knowledge of the particular machine in use — familiarity with the equipment (and the shortcuts that can safely be taken) is key.
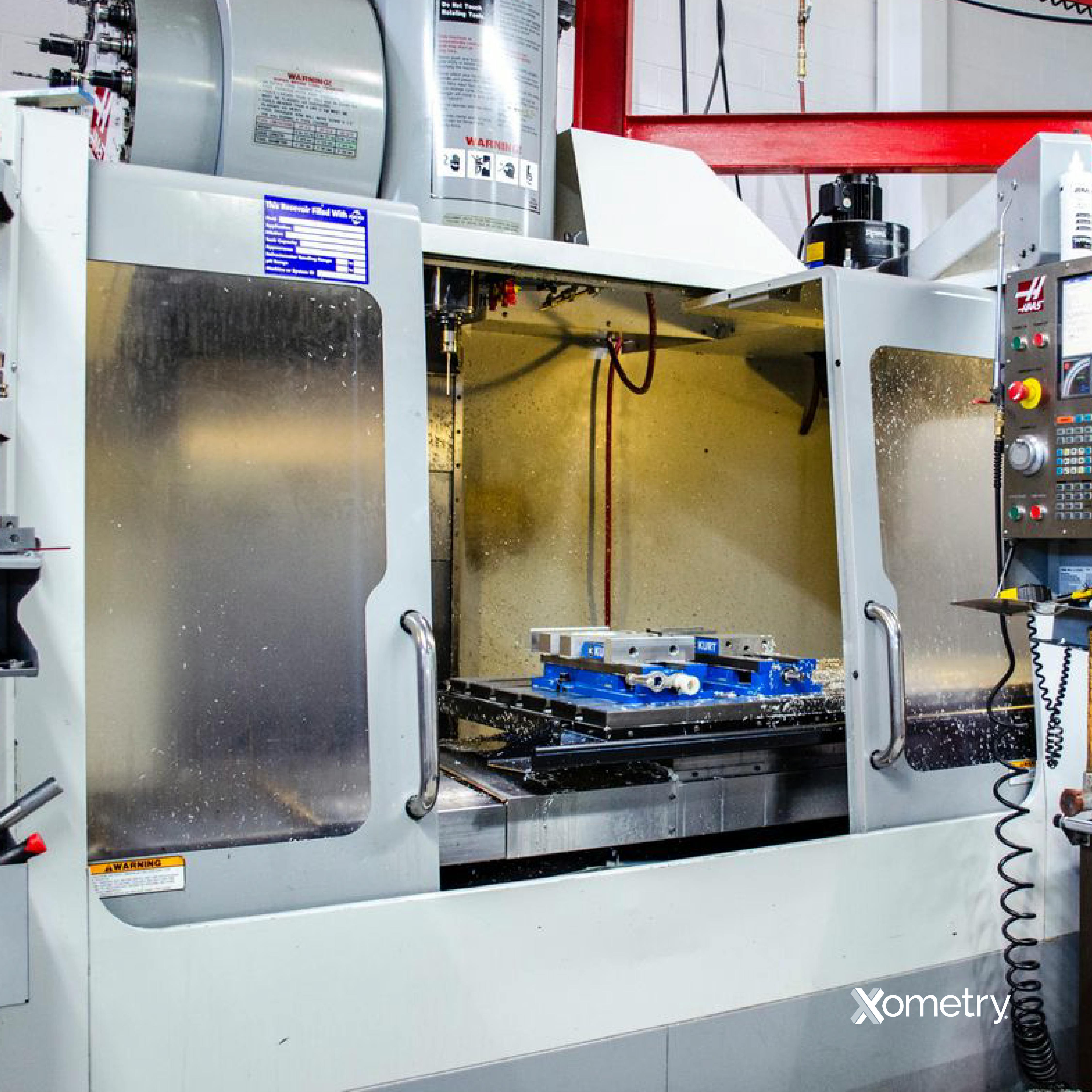
4. Problem-Solving
Very few jobs go exactly as planned, so an agile mind that can both identify problems and intuit ways to solve them is a great asset. The best tool here is experience. Eventually, you’ll have seen most of the things that can go wrong, and you’ll have the experience to foresee others, allowing you to solve problems before they disrupt your work.
While being a strong problem solver is important, your greatest resources are colleagues with more experience. One of the problems that most CNC machine operators need to solve early on is understanding when to get advice and when to fearlessly try. The whole job is about solving problems, and it’s critical that every CNC machinist enjoys the challenges that will arise all the time.
5. Desire to Gain Expertise
Perhaps the least measurable skill needed for the CNC machinist career path is drive. It’s important in any career. In this sector, it is embodied, at all levels, as the desire to learn. More learning means more skills, more flexibility in task assignments, and greater employability.
It’s a competitive work area, where the strongest differentiator of the potential that employers desire is the energetic acquisition of skills. And that comes from a can-do approach that great apprentices show from the earliest stages and never lose as they grow in experience.
All About CNC Machinists
CNC machinists are creative engineers with broad (and usually ever-expanding) skill sets who turn ideas into things using a range of software and hardware tools. They perform many different tasks using tools such as: CAD/CAM software, G-code programming, checking and editing tools, and many more. They must also understand how to: select the proper materials, choose relevant tools, set up clamps and jigs, check and execute the CNC toolpath, act as quality assurance, and clean up after each job.
To become a CNC machinist, you need to be at least a high-school graduate and get accepted for an apprenticeship. You’re typically best off in a medium to a large company where you can learn from a larger team and lean on them for support as you develop. The apprenticeship will generally involve outside (classroom) education, in theory, math, and general engineering practice. On the production floor, you’ll receive rapid-development training in the preparation, operation, validation, and reporting aspects of the job. After completing their apprenticeship, the trainee is a journeyman/journeywoman who is qualified to work unaided and to teach others and generally receives higher pay. External certifications and ongoing learning allow advancement into more complex work, related fields, and management. A proportionate increase in pay is expected as the employee becomes a more valuable contributor to the team.
How Much a CNC Machinist Can Earn
Apprentices in CNC machining can expect to earn $22,000 to $50,000 per year. Once qualified and able to work unaided, the median salary for a CNC master is around $50,000. For those who learn more skills and advance faster, salaries are usually higher and bring greater potential for the individual to broaden their skill set.
The factors that influence a CNC machinist's salary vary according to entry qualifications and experience. Generally, a new apprentice who demonstrates basic engineering aptitude and a high school diploma or passing score in the GED will likely start at the bottom of the expected range. An applicant with a ‘college ready’ score and similar evidence of aptitude will do a little better. A ‘college ready + credit’ score and some actual experience in machine tool operation, G-code use/knowledge, or relevant work experience are likely to sit at the upper end of the pay scale.
CNC machinists receive higher pay in some US states than others. A few representative pay rates are shown in Table 1:
State | Hourly Average Pay Rate | Annual Average Salary |
---|---|---|
State District of Columbia | Hourly Average Pay Rate $41.15 | Annual Average Salary $85,600 |
State Alaska | Hourly Average Pay Rate $34.10 | Annual Average Salary $70,920 |
State Hawaii | Hourly Average Pay Rate $34.02 | Annual Average Salary $70,760 |
State Washington | Hourly Average Pay Rate $28.89 | Annual Average Salary $60,080 |
State Maryland | Hourly Average Pay Rate $28.76 | Annual Average Salary $59,810 |
Table Credit: bls.gov
Where CNC Machinists Can Work
CNC machinist jobs are concentrated in certain regions, due to the concentration of relevant industrial sectors. However, not all CNC machinist jobs are created the same, so much of the regional variation follows industry types. Listed below are the places where CNC machinists can most easily find work:
- Seattle: With so many aviation and high-tech companies in the area, there is a large demand for CNC machinists in Seattle. This is a hard-driving technology sector that offers greater opportunities to those with aptitude — and the range of advanced engineering sector jobs reflects the advanced nature of the businesses there.
- Alaska: CNC machinist employment in Alaska generally relates to the oil industry and is highly concentrated in specific parts of the state. There are not a lot of jobs there, but they do pay well (though the career paths in the area may be more limited).
- Chicago, Milwaukee, and the Surrounding Areas: Chicago, Milwaukee, and the surrounding areas have the highest concentration of CNC machinist employment opportunities. These cover the widest spectrum of traditional engineering, high-tech development, aerospace, and more. The critical mass of such businesses in the area makes for great opportunities and career paths.
- California: California, in particular, has great concentrations of high-tech businesses in the South Bay Area — Silicon Valley and its surroundings. These employers are often smaller, more dynamic, and expanding businesses which can represent a higher risk, higher reward environment.
Why a CNC Machinist Is a Good Career
The CNC sector is one of growth and opportunity — and this will only be limited periodically by recessions or other downturns since the tech sector continues to diversify and increase in complexity and depth.
CNC machining roles make for great entry-level career starting points. This career path provides an expansive overview of an area's active businesses and opportunities for career movement. It also offers great prospects for stable, well-paid employment in high-demand sectors for which few people have the proper skills. If you have the right mindset, the career opportunities that open up from CNC machining roles are legion.
How Xometry Can Help
Xometry provides a wide range of manufacturing capabilities, including CNC machining and other value-added services for all of your prototyping and production needs. Visit our website to get started on your next CNC machining quote.
Disclaimer
The content appearing on this webpage is for informational purposes only. Xometry makes no representation or warranty of any kind, be it expressed or implied, as to the accuracy, completeness, or validity of the information. Any performance parameters, geometric tolerances, specific design features, quality and types of materials, or processes should not be inferred to represent what will be delivered by third-party suppliers or manufacturers through Xometry’s network. Buyers seeking quotes for parts are responsible for defining the specific requirements for those parts. Please refer to our terms and conditions for more information.
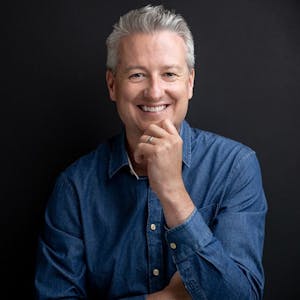