Machine tools of transformative capability are becoming the norm, even in home workshops. Machine shop capabilities enter the hobby market through lightweight machines of relatively modest capability. Such devices, along with a spectrum of other machines, are redefining the home workshop.
CNC routers are rotating cutter devices that are driven by G-code. A speed-controlled electric drive can apply a wide range of drill, router, and milling cutter bits. Commonly, the workpiece is fixed to a stationary table on the router itself. However, the tables of some CNC machines can move in the X, Y, and Z axes to bring the cutter to bear on the work. The lowest-cost machines can only handle “soft” materials, whereas the mid-range can cut aluminum, brass, and light metals. This article will discuss the six parts of a CNC router, the accessories, and how to identify them.
1. Frame (Supports the Machine)
It’s critically important that the frame of a CNC router is as stiff as it can be. Precision is impossible if the position of the workpiece or the cutter is uncertain because of the flexure of the frame. The consequences of an insufficiently stiff structure in a router vary, depending on the degree of flexibility, including: chatter, cross-bridge flexing, and displacements on any one axis.
2. Table (Spoilboard or Wasteboard)
Tables vary in their construction and locating systems for workpieces. The most adaptable tables are those made with vacuum pull-down or integrated T slots (or both), so a wide variety of workpieces can be clamped anywhere. Aluminum extrusion construction is very common and offers a good mix of adaptability, stiffness, and low weight. Alternatively, a range of strong materials can be machined to make a T-slot table with slots on two axes, making a checkerboard pattern of mount points.
3. Spindle (Heart of any CNC Machine)
The spindle is the single most critical component of a CNC router. In most machines, the spindle is integral to the motor shaft and relies on the motor bearings. This is a low-cost construction method, but unless the motor bearings are sufficiently robust, premature wear problems may result.
Spindle/motor bearings come in various qualities; they wear items that require periodic replacement. Loose bearings mean a loose cutter, and accuracy is lost. Stiff bearings add hard work and more heat to the process. Bad quality or worn bearings add a lot of noise to a fast-turning cutter.
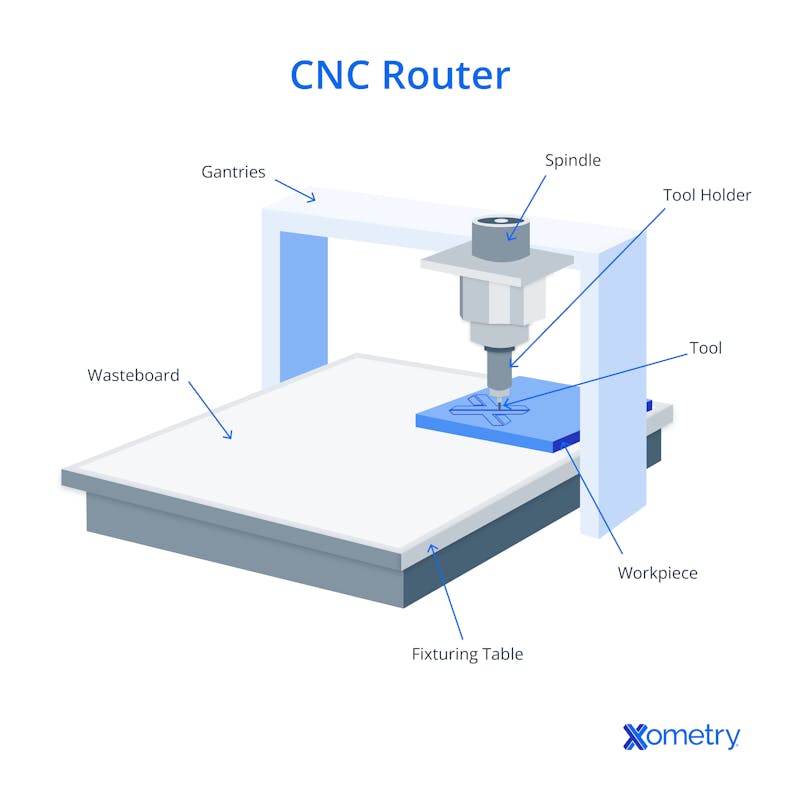
4. Ways (Sliding Ways)
The ways or slides are the motion tracks that enable X-Y-Z movement. It is from these (and a stiff frame and good quality lead screws) that any router derives its precision …or lack of it. The most common ways are precision-ground stainless steel rods on which either plain bushes or recirculating ball collars run. An axis requires at least two such rods – and the further apart those rods are, the more precise the axis motions will be. Plain bushes are lower cost, recirculating ball bushings are freer moving but more expensive. Free motion means more precise positioning.
More expensive machines tend to employ V-form tracks with grooved, sealed ball races locked onto both sides of the track. This track provides equal stiffness but requires less height to maintain the motion. Recirculating ball slides are harder to protect from dirt than sealed ball races. They have wiper seals that clean the ground shaft way, but some material will often get past this.
5. Axis Drive (Converts Rotary Motion)
The axis drives convert the output of the stepper motors that drive the machine from rotary to linear motion. Lower-cost machines often use toothed or timing belts for this. While that may sound less than optimal, toothed belts have been used in robotic positioning systems in this way for decades and can be durable, when kept clean.
More expensive machines tend to have recirculating ball screws. These offer the advantages of freer motion and lower hysteresis. But they pose the same contamination/wear issues that similar systems in the sliding ways suffer, so cleanliness is essential for long machine life.
6. CNC Controller (Executes G-Code)
The control computer module is the brain of any CNC machine. It takes G-code and turns it into motion by driving/controlling the various axis stepper motors and the spindle motor. These devices are sophisticated I/O control devices that control a range of outputs – from simple 3-axis and cutter speed up to 5-axis, with coolant pumps, motor cooling systems, automated cutter/router changers, and more.
CNC controllers are generally single-board computers. They are composed of processors, memory, integrated self-protection mechanisms, and power supply. CNC controllers are designed to turn the input G-code the user provides into precise and repeatable movements that cut a complex net shape from a material blank.
What is a CNC Router?
CNC routers are automated machine tools that are widely used for cutting 2D and shallow 3D profiles from generally soft materials. A CNC router uses three motion axes that transport a rotating cutter to remove material in a programmed pattern. This motion is driven by the point-to-point instructions of the G-code. Cutting tools can be changed (either manually or automatically) to remove material in progressive and generally small-depth cuts to maintain higher accuracy and better surface finish. For more information, see our guide on CNC Machining.
Some Common CNC Router Accessories
CNC router accessories include many categories of equipment, including a surprising number of tools and accessories – of wide-ranging cost and usefulness. These are:
1. CNC Router Bits
“Bits” is a catch-all term for a wide range of drills and cutters. This accessory includes the face or shell mill, square and bull nose end mills, and ball end mill. Bullnose and ball end mills are good for cutting the surfaces of curves, as they don’t create grooves and can blend surfaces to a smooth roundness.
2. CNC Collet
A collet is a simple clamping system that uses a split tube (with a tapered nose). It forms a close fit with the straight tool shank and has a lock nut that clamps the taper to squeeze the split tube onto the tool. The collet will sit within a tool holder, often called a collet chuck, which is generally fitted to the router with a taper locator and spring locator to lock it in place. In many simpler setups, the collet chuck is not removed from the spindle but is fixed in place, so new tools and collets to suit them are handled in place.
3. CNC Tool Holder in Place
Collet clamped tools that are fitted to a removable collet chuck can be quickly fitted to the machine's cutter drive, using a variety of locating and locking systems. For auto tool change setups, each required tool will be placed into its collet. The machine will pick up new tools from fixed positions on the table when required. Each of these collets will have a quick-release upper portion that the router can attach to without difficulties.
4. Automatic Tool Changer Tool Forks
Tool changer forks are devices in which a collet chuck sits when not in use. These devices are usually placed in a line to make a tool rack. The position of each collet chuck is fixed, and the machine can deposit the used tool in an empty fork and then acquire the next from another position.
After each tool change, the machine confirms the tool position and cut depth. If the tool has been incorrectly set in the collet, this will result in over- or under-cutting the part. A tool sensor, a low-cost touch-and-go detector, helps ensure tools are set correctly.
5. Vacuum Suction Pods and Cover
Vacuum clamping devices, or suction pods, are a convenient way to locate and retain workpieces on the table. They can be clamped down using the T slots or other table-clamping systems and allow quick release of the parts. This part is particularly useful when a run of parts is being produced, as it allows precise and fast repositioning of the next workpiece without tools. Suction pods come in a wide range of shapes, sizes, and heights.
Xometry provides a wide range of manufacturing capabilities including CNC machining, 3D printing, injection molding, laser cutting, and sheet metal fabrication. Get your instant quote today.
Disclaimer
The content appearing on this webpage is for informational purposes only. Xometry makes no representation or warranty of any kind, be it expressed or implied, as to the accuracy, completeness, or validity of the information. Any performance parameters, geometric tolerances, specific design features, quality and types of materials, or processes should not be inferred to represent what will be delivered by third-party suppliers or manufacturers through Xometry’s network. Buyers seeking quotes for parts are responsible for defining the specific requirements for those parts. Please refer to our terms and conditions for more information.
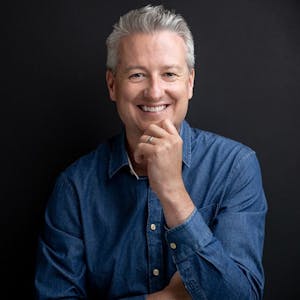