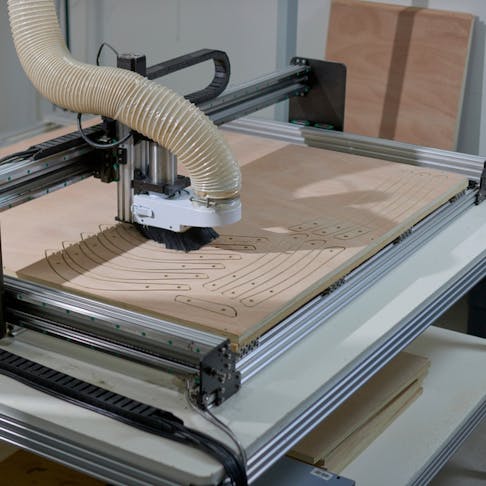
CNC Router vs. CNC Mill — What's the Difference?
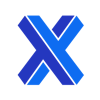
A CNC router is typically used for cutting softer materials such as wood, plastic, or non-ferrous metals, utilizing high-speed spindle rotation to achieve its cuts. A CNC mill, on the other hand, is designed to tackle harder materials such as steel or titanium, focusing on accuracy as the table moves (providing x and y motion). The spindle also moves, providing z motion. The primary difference lies in how motion for cutting is achieved in the two methods. For a router, the cutting tool is mounted on a gantry; the gantry provides x- and y-axis motion, while the tool head provides limited z-axis motion.
This article will further discuss the differences between CNC routers and mills in terms of their purposes, how they work, and their importance.
What Is a CNC Router?
A CNC router is a device that machines soft metals, plastic, and wood to create designs using computer numerical control (CNC). It works using a fast-rotating tool that travels in three or more axes to shape the workpiece according to the programming. It follows computer-generated instructions to automate the cutting process, making it indispensable in industries such as furniture manufacturing, where intricate designs and repetitive tasks are common.
What Is the Purpose of a CNC Router?
A CNC router excels in cutting, shaping, and engraving a variety of materials including wood, plastic, and soft metals, ensuring a moderate level of accuracy in the final product. Its high-speed tool rotation facilitates a smooth cut surface on these softer materials. However, when it comes to processing harder substances, the CNC router is less effective compared to a CNC mill, which is specifically designed to handle such tough materials.
What Is the Importance of a CNC Router?
The CNC router is renowned for its efficiency and versatility in manufacturing. It is an important tool in any workshop, as it significantly reduces production time and waste. It offers a rapid and cost-effective machining method for applications that demand moderate accuracy and relatively shallow cuts. Another significant feature of a router is its ability to cut larger workpieces, thanks to the gantry x-y motion system, which accommodates a large, stationary worktable.
How Does a CNC Router Work?
A CNC router is designed with a flat, stationary table to which the workpiece material is secured. A CNC router is a sophisticated machine used in manufacturing for cutting, shaping, and engraving materials like: wood, plastic, and soft metals. It operates on a Cartesian coordinate system, allowing movement along the X, Y, and Z axes. The 3-axis CNC router can move its cutting tool in three dimensions: left to right (X-axis), front to back (Y-axis), and up and down (Z-axis), making it suitable for creating flat or slightly contoured surfaces. The 4-axis CNC router adds a rotational axis (A-axis), enabling it to perform more complex operations like cutting around a cylinder or creating intricate 3D shapes. Both types use a high-speed spindle to rotate the cutting tool, carving out designs with precision. The CNC router is controlled by G-code, which is generated from a CAD design and dictates the toolpath for the router to follow.
What Are the Typical Applications for a CNC Router?
Typical applications for CNC routers include products in the furniture, advertising, musical instrument, construction model, and decorative metalwork industries.
In woodworking, CNC routers are often utilized to create furniture, cabinets, and ornamental carvings. They are employed in the advertising industry to create elaborate logo designs and sign boards. They are utilized to carve and shape various components of instruments, such as the bodies of guitars and violins. They are also used in the construction of models and prototypes for engineering and architectural projects. CNC routers are useful in metalworking which makes it possible to create unique parts and elaborate ornamental embellishments.
What Materials Can Be Worked on With a CNC Router?
CNC routers can handle a variety of materials, including: woods of different hardness and density, composite laminates, plywood, plastics, and soft metals like aluminum and brass. Each material interacts differently with the router's cutting surfaces, affecting the choice of cutting tools and machine settings. For instance, wood is generally easy to cut due to its low hardness, which results in minimal wear on the machine and easy chip removal. Composite materials, however, require careful handling to prevent delamination during the cutting process. Understanding these material properties is essential for optimizing the CNC routing process and achieving the desired results.
What Types of Tools Can Be Used With a CNC Router?
CNC routers can utilize a variety of tools such as: face mills, drill bits, end mills, V-bits, chamfer bits, and ball nose end mills. Depending on the material being machined and the desired finish of the workpiece, these tools are selected to accommodate various operations such as: shaping, engraving, and cutting.
Are CNC Routers Easier To Upgrade Than Mills?
Yes, CNC routers are generally easier to upgrade than mills. This is because CNC routers are designed with a modular structure that often allows for straightforward enhancements, such as adding a more powerful spindle or expanding the work area. Their gantry-style configuration is conducive to upgrades that can improve efficiency and versatility. In contrast, CNC mills simply don't require the same kinds of updates as the router, but rather are sold as upscale items.
What Are the Safety Considerations for Using a CNC Router?
When operating a CNC router, safety is paramount. Here are some key considerations:
- Reading the Manual: Familiarize yourself with the machine's operating instructions and safety warnings.
- Proper Training: Seek training before operating the machine to prevent injuries and machine breakdown.
- Wearing Personal Protective Equipment: Use safety goggles, ear muffs, and a dust mask. Do not wear gloves or loose clothing.
- Securing Work Area: Ensure the work area is clean, well-lit, and free from clutter.
- Machine Inspection: Verify the power is off before plugging in the machine and inspect all parts for damage.
- Material Handling: Ensure workpieces are securely clamped down to prevent shifting during operation.
- Focus: Always keep your focus on the work being done and avoid distractions.
These practices help maintain a safe, productive environment and prevent workplace accidents.
What Are the Best CNC Routers?
Selecting the best CNC router depends on your budget and the materials you plan to work with. Here are some of the top picks:
- SainSmart Genmitsu CNC Router Machine: This router is appreciated for arriving at its destination already partly assembled, which reduces setup time. It is designed for quiet operation and includes safety features such as acrylic baffles and emergency stop controls. In the context of CNC routers, acrylic baffles help contain debris and provide a safety barrier between the user and the moving parts of the machine.
- MYSWEETY CNC Pro Engraver Machine: Ideal for beginners, this machine is known for its accuracy and ease of use. It comes with a solid build and is also equipped with a laser engraver, although it does not include software.
- Genmitsu CNC Router Kit: A great choice for complete beginners, this model uses flexible hardware and open-source software, making it easier to upgrade. The spindle of the CNC router can be replaced with a laser module, which is a relatively straightforward process. This modularity allows users to expand the machine’s capabilities without purchasing a new setup.
- Mcwdoit CNC 3018 Pro Router: Best for desktop use, this router is compact yet capable, and suitable for smaller projects and spaces.
What Are the Advantages of CNC Routers?
CNC routers offer several benefits that make them a valuable addition to any manufacturing or creative workspace:
- These machines can produce high-quality items in less time compared to manual methods.
- With the ability to create complex shapes and designs, CNC routers can be used with a variety of materials and applications.
- CNC routers produce less material waste due to their efficient cutting processes. The actual numerical tolerance for a CNC router is typically ± 0.005″ or 0.13 mm. This standard tolerance level indicates the allowable limit of variation in the dimensions of a part compared to its design specifications.
- Many CNC routers have a compact design, which helps to save space in the workshop. However, a router can also handle large workable and consequently large workpieces.
What Are the Disadvantages of CNC Routers?
While CNC routers are highly beneficial, they come with certain drawbacks:
- CNC routers can be relatively loud due to the vacuum system, extraction, and spindle operation.
- Even with extraction systems, CNC routers can produce residual dust and swarf that need to be managed.
- Compared to some other CNC machines like mills, CNC routers may have lower accuracy, especially for intricate or detailed cuts.
- CNC routers typically have a shallower depth of cut capabilities compared to mills, which may limit their suitability for certain applications.
- CNC routers may struggle to work with hard materials like metals or certain composites, limiting the range of materials they can effectively process.
What Maintenance Do CNC Routers Need?
For optimal operation, CNC routers need to have regular maintenance performed. Important tasks include: lubricating properly, tightening belts, tightening screws, cleaning dust, and inspecting the water and air cooling systems. The machine’s life and dimensional accuracy can be extended with a regular maintenance program.
What Is a CNC Mill?
A CNC (Computer Numerical Control) mill is a type of machining tool that uses computerized controls to operate and manipulate a rotating cylindrical cutter. It removes material from a workpiece to create parts with precise dimensions and shapes. CNC mills can work on various materials and are essential in industries requiring high precision, such as aerospace and electronics. Figure 1 is an example of a CNC mill:
A CNC mill.
Image Credit: Shutterstock.com/al7
How Does a CNC Mill Work?
A CNC mill removes material from a workpiece using a spinning cutting tool. The machine moves the tool along several axes to shape the material into the required shape according to a computer program, commonly in G-code. This technology makes it possible to manufacture parts for a variety of industries with high accuracy and complex geometries. CNC mills can produce complex and detailed parts because they can work on several axes, usually three to five. CNC routers excel with softer materials and offer expansive work areas ideal for large sheets. Conversely, CNC mills are tailored for hard materials like steel and titanium, featuring smaller workspaces that accommodate compact, hard material blocks.
What Is the Purpose of a CNC Mill?
The purpose of a CNC mill is to remove material from a workpiece to create accurate and complex parts. It is essential in industries that demand high accuracy, such as aerospace and electronics, where it is used to machine a variety of materials into final components.
What Is the Importance of a CNC Mill?
CNC mills are essential to modern production because of their great precision and reproducibility in producing complicated parts. They are essential for sectors like aerospace and medical device manufacturing that have high standards. The precision of CNC mills leads to improved efficiency, reduced waste, and the ability to fabricate intricate designs that would be impossible with manual machining.
What Types of Materials Can a CNC Mill Work With?
CNC mills can work with a broad range of materials, including metals like aluminum, brass, steel, and titanium, as well as plastics such as acetal (POM), acrylics (PMMA), polycarbonate (PC), and polypropylene (PP). They are also capable of machining wood and various foams. The choice of material depends on the specific requirements of the project, including: strength, weight, and resistance to the conditions of the service environment.
What Are the Features of Xometry’s Custom CNC Milling Services?
The features of Xometry's custom CNC milling services include:
- Rapid Prototyping: Quick turnaround for CNC milled parts and prototypes.
- Material Variety: A broad selection of materials, including metals and plastics.
- Precision Machining: High-quality milling following AS9100D and ISO 9001:2015 certifications.
- Advanced Capabilities: Support for 5-axis and right-angle milling.
- Design Feedback: Instant quotes with design-for-manufacturability feedback on materials and processes.
Can a CNC Mill Be Used for Large-Scale Production?
Yes, a CNC mill can be used for large-scale production. CNC mills offer various space options, allowing for flexibility in accommodating different project sizes. They are appropriate for projects requiring deeper cuts due to their deeper Z-axis.
What Are the Typical Applications for a CNC Mill?
CNC mills are essential in precision manufacturing. They are commonly utilized in industrial settings to produce high-quality components from metals, plastics, and wood. In the automotive sector, they are indispensable for creating cylinder heads. CNC mills also play a pivotal role in the aerospace industry, medical device production, and mold-making, where exacting specifications for accuracy are required for complex and detailed components and assemblies.
Can CNC Mills Be Used for Metalworking?
Yes, CNC mills are highly suitable for metalworking. They can cut delicately and precisely as required by their programming, even with hard materials such as: titanium, steel, and aluminum. Mills produce lots of torque, which gets converted to the force needed to cut the metal. In contrast, routers, due to their distinct construction, are unable to exert the same level of force on a workpiece.
What Are the Maintenance Requirements for CNC Mills?
The maintenance requirements for CNC mills include: regular lubrication of moving parts, cleaning of chips and debris from the machine bed and cutting area, calibration of machine parameters, and periodic inspection of tooling for wear and damage. Additionally, it is crucial to follow the manufacturer’s recommendations for specific maintenance tasks and schedules.
Do CNC Mills Use More Power Than Routers?
Yes, CNC mills typically use more power than routers. This is so because mills need greater torque to cut through harder materials, which increases power consumption. Even though they are faster, routers require less power because they often work with softer materials.
What Are the Advantages of CNC Mills?
The advantages of CNC mills include:
- They offer high precision and accuracy in machining operations, ensuring consistent and reliable results.
- These machines can work with a wide range of materials, from metals to plastics, and can perform various operations such as: drilling, milling, and cutting.
- CNC mills are capable of running automated processes, reducing the need for manual intervention and increasing productivity.
- The depth of cut in CNC milling allows for control over the amount of material removed during each pass. A larger depth of cut can increase the material removal rate (MRR), enhancing productivity and reducing machining time. However, it’s important to balance the depth to prevent excessive cutting force, which could lead to tool damage.
What Are the Disadvantages of CNC Mills?
The disadvantages of CNC milling include:
- CNC routers can range from a few hundred to a hundred thousand dollars, CNC mills typically start at over a thousand dollars and can go up to $150,000 for high-end models. This makes mills a significant investment, particularly for operations that require the precision and durability they offer.
- Despite their high level of automation, CNC milling machines require skilled operators for programming and maintenance. This necessitates proper training, which can be costly and time-consuming.
- CNC mill is designed for cutting hard materials, with slower cutting operations due to lower spindle speeds and feed rates.
What Are the Safety Considerations for Using a CNC Mill?
By and large, the safety considerations for using a CNC mill are similar to those for other machining equipment, including CNC routers:
- Training and Familiarization: Operators must be thoroughly trained on the specific CNC mill they will use.
- Protective Gear: Safety glasses or goggles, and hearing protection are essential to shield against flying chips and loud noise.
- Machine Inspection: Before use, check that all guards are in place and the workpiece is securely clamped.
- Clean Workspace: Keep the mill surfaces and shop floor free of cuttings and dust to prevent slips and fire hazards.
- Avoid Loose Items: Do not wear gloves, loose clothing, jewelry, or have loose hair that could get caught in moving parts.
- Emergency Procedures: Know the location of emergency stop controls and how to use them.
- Correct Use of Cutting Fluids: Utilize appropriate cutting fluids to ensure efficient and safe milling operations.
- Maintenance: Regularly inspect the machine for damaged parts and tools, ensuring everything is in proper working order.
Summary
This article presented CNC routers and CNC milling, explained each of them, and discussed their key differences. To learn more about CNC routing and milling, contact a Xometry representative.
Xometry provides a wide range of manufacturing capabilities, including machining and other value-added services for all of your prototyping and production needs. Visit our website to learn more or to request a free, no-obligation quote.
Disclaimer
The content appearing on this webpage is for informational purposes only. Xometry makes no representation or warranty of any kind, be it expressed or implied, as to the accuracy, completeness, or validity of the information. Any performance parameters, geometric tolerances, specific design features, quality and types of materials, or processes should not be inferred to represent what will be delivered by third-party suppliers or manufacturers through Xometry’s network. Buyers seeking quotes for parts are responsible for defining the specific requirements for those parts. Please refer to our terms and conditions for more information.
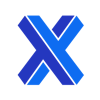