Did you know that end milling can perform face milling tasks, but face milling tools can’t carry out end milling jobs? Although these two metal-removing milling processes are alike in many ways, they have some important differences that you have to know about before starting a project using any one of these methods. All is revealed below.
What is Face Milling?
Face milling is used to create high-quality flat surfaces with either a fly cutter, end mill, or shell mill. These cutting tools typically have different head inserts so you can swap them out as necessary, kind of like you would with a regular drill/driver. The material you want to cut should be placed face-up on the machine, perpendicular to the cutter’s axis. After you’ve adjusted all the important settings, like the spindle speed and feed rate, secure the material in place so that you can start cutting. The below diagram depicts the face-milling process.
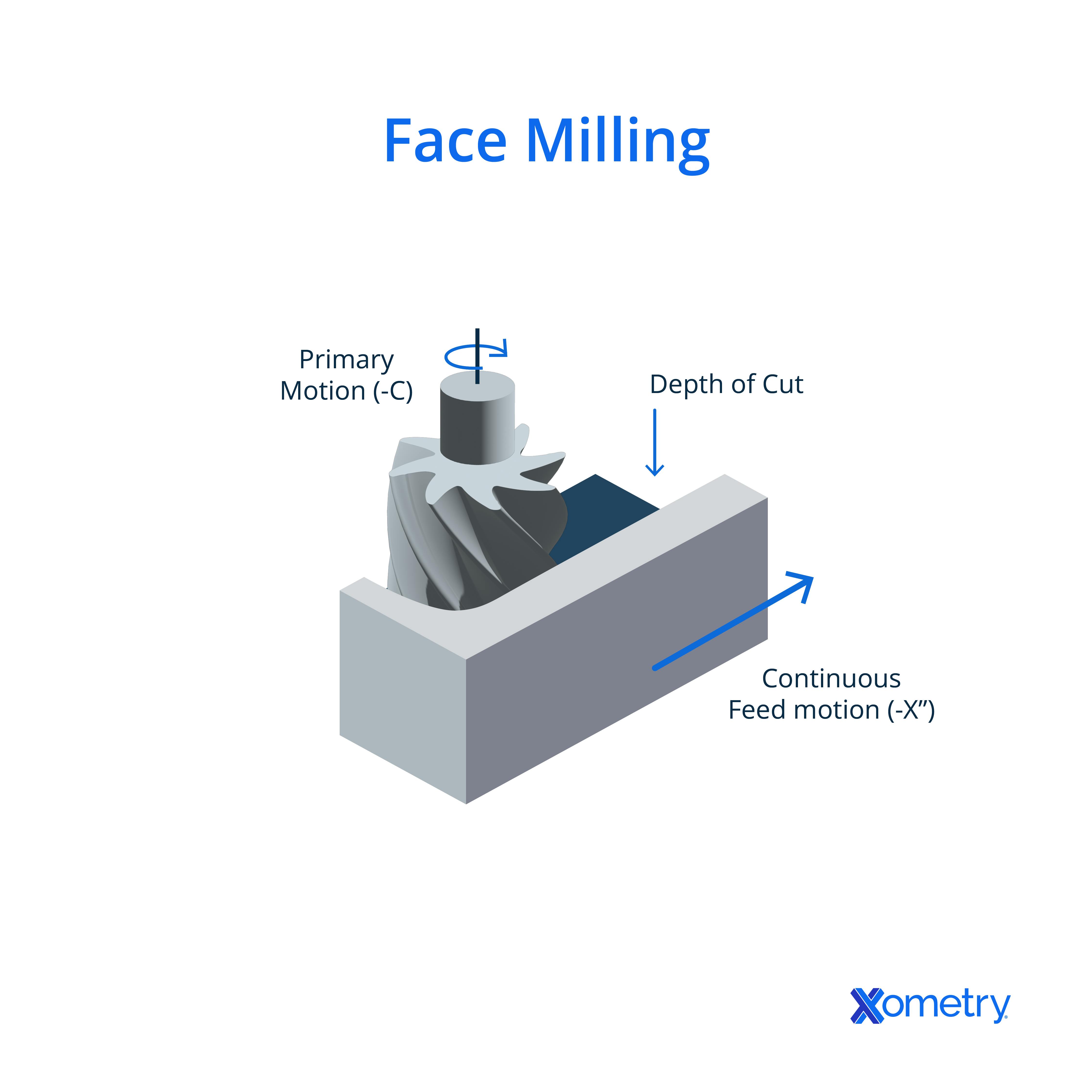
Some of our customers manage to make their cuts using this process in a single pass, but don’t worry if you need more than one (it happens to the best of us). Face milling does a great job of removing a lot of material quickly, but the surface quality finish is medium. You can face mill lots of metals like steel, aluminum, nickel, brass, and titanium, and use this method for leveling surfaces and raised edges, and making parallel surfaces, pockets, and recesses, too. Tools that are used for face milling are large diameter ones — including square-end tipped, ball nose, radius tipped, and chamfer tipped — and they could have many different inserts.
What is End Milling?
End milling is a little more versatile and is used to make pockets, slots, recesses, shoulders, profiles, and cavities by cutting parallel to the tool spindle. It removes material with a tool sporting cutting edges on both the flat part (the end face) and the sides (peripheral). An end mill’s design also allows it to do some extra things, like engrave, make die cavities, and cut various shapes and contours. The diagram below shows how end milling works.
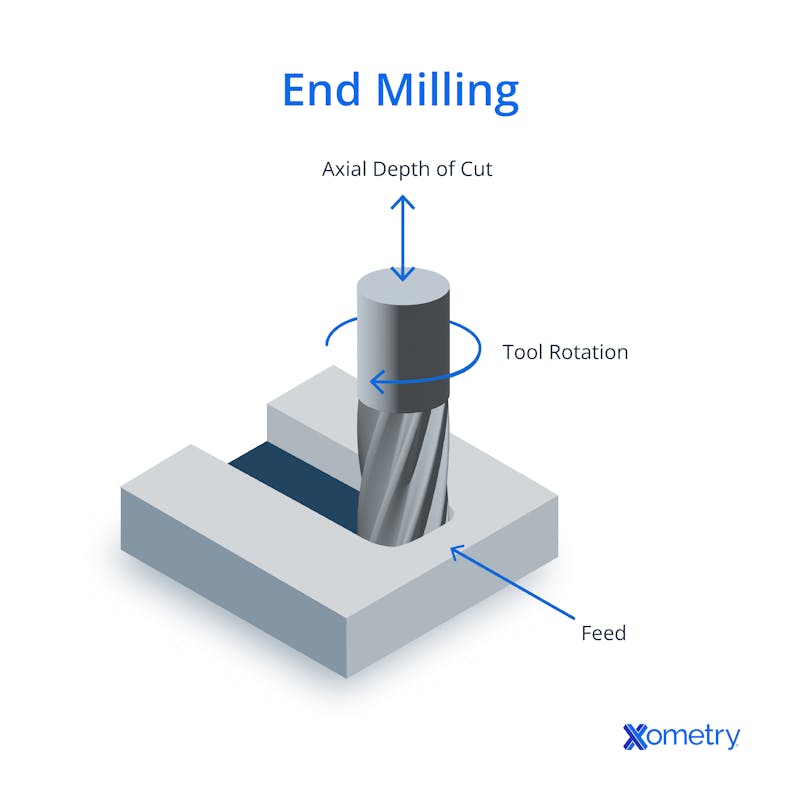
End milling is not massively dissimilar to face milling when it comes to preparation; you still have to set the machine up correctly and position the material securely and exactly where you need to start cutting. This process is used by Xometry customers who need both axial and perpendicular cutting capabilities for things like profiles, slotting, plunge cutting, contouring, counterboring, and making keyways. Compared to face milling, the quality finish of end milling isn’t the best (0.29–0.95µm), but it still looks relatively good.
The is quite a wide range of tools used in this process, some of which are:
- Square end mill (for general end milling)
- Keyway end mill (for cutting keyway slots)
- Ball end mill (for cutting contoured surfaces in dies and molds)
- Roughing end mill (removes a lot of material but leaves a rough surface)
- Corner radius end mill (for cutting corner radii)
- Roughing and finishing end mill (removes a lot of material and leaves a fine finish in a single pass)
- Corner rounding end mill (for cutting rounded edges)
- Drill mill (for drilling, spotting, countersinking, and chamfering)
- Tapered end mill (for die and mold cutting)
Face Milling vs. End Milling
So we’ve established that both methods remove metal from a workpiece, but face milling is better for flat surfaces with stellar quality, while end milling has a lot more tricks up its sleeve and can do lots of different cutting tasks. As briefly covered in the intro, end milling can carry out face milling projects, but face milling can’t be used for end milling tasks because of the way the tools are designed. Basically, face milling is great at one thing, whereas end milling is good enough at many things.
The process you choose will really depend on your exact needs, and where factors like budget, finish, or capabilities sit on your list of priorities. To help you decide, we’ve put all the pros and cons of each of them in the table below.
Process | Pros | Cons |
---|---|---|
Process Face milling | Pros
| Cons
|
Process End milling | Pros
| Cons
|
Face Milling vs. End Milling
How Xometry Can Help
Xometry has a wide range of manufacturing capabilities, offering our customers machining and milling services for both prototyping and production parts. Want to find out more about face milling and end milling, or get a free, no-obligation quote? Contact a Xometry representative today.
Disclaimer
The content appearing on this webpage is for informational purposes only. Xometry makes no representation or warranty of any kind, be it expressed or implied, as to the accuracy, completeness, or validity of the information. Any performance parameters, geometric tolerances, specific design features, quality and types of materials, or processes should not be inferred to represent what will be delivered by third-party suppliers or manufacturers through Xometry’s network. Buyers seeking quotes for parts are responsible for defining the specific requirements for those parts. Please refer to our terms and conditions for more information.
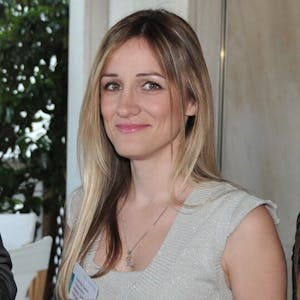