Knurling is a manufacturing process that creates a pattern of straight, diamond-shaped, or raised ridges on a metal workpiece. It's achieved by pressing a knurling tool against the workpiece, causing plastic deformation as the raised elements of the tool depress and deform the surface. Knurling serves to improve grip, facilitate assembly, and enhance the appearance of objects like handles, knobs, and tool handgrips. It often provides a visual guide to use by signaling “hold here.” Additionally, knurling is used on metal components that are designed to be embedded in overlaying polymer or composite materials, to provide increased engagement between substrate and over-coating.
This article will discuss knurling, how it works, its uses, its advantages, and the types.
What Is Knurling?
Knurling is a machining process used in manufacturing to create a textured pattern on the surface of a workpiece, typically made of metal. It serves three basic purposes: provide a grip area on handhold regions of parts such as thumbwheels and handles as a functional grip improver and user indicator, impose a decorative finish on parts, and prepare parts for a press fit. Additionally, knurled patterning is often applied to plastic mold tooling to form the appearance of knurling in molded components.
Knurling, in a rudimentary cut or edge-hammered form, dates to the earliest metalworking techniques. During the medieval period, as blacksmithing and metalworking techniques advanced, more sophisticated tools and methods for creating textured surfaces emerged. This included peening with featured hammers, which is essentially identical to modern knurling except that it involves impacts rather than rolling. The Industrial Revolution brought significant advances and greater repeatability in manufacturing techniques. Machining tools, including lathes, became more precise and widespread and supplanted the craft skills that had previously been so rare. Early steam engines show evidence of engraved and likely rolled knurling on hand controls. Swiss watchmakers in the 19th century are credited with crystallizing knurling as a machining process, for precise and decorative patterns on watch components. In the 20th and 21st centuries, knurling became a universal machining operation. Advances in CNC machining technology further enhanced the precision and versatility of the process.
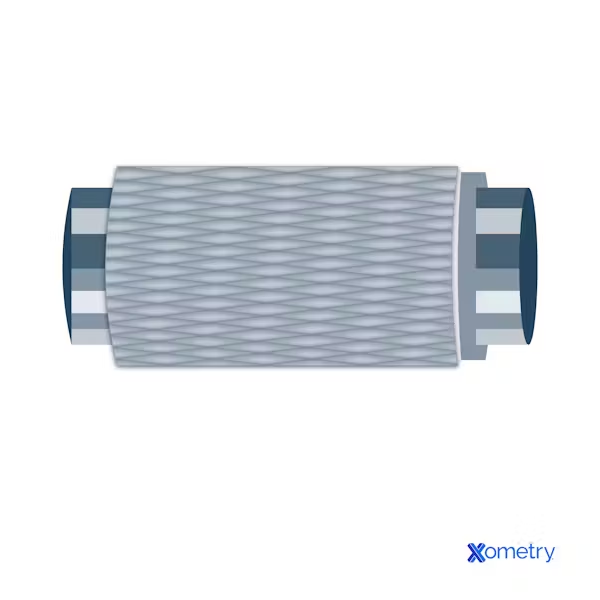
Drawing of a knurled handle
How Knurling Works
Machine knurling uses a hardened steel tool that carries the inverse of the required surface form. The tool rolls the pattern onto the component in a tightly controlled plastic distortion process. The material of the surface is pressured to plastically deform into the recesses of the tool. It makes a diapositive copy of the tool pattern as an imprint on the surface, with no material removal. Such a process can be performed on cylindrical parts on a lathe, using a relatively low imposition of force and a rolling action. On non-cylindrical surfaces, the tool must carry the overall shape of the target surface. It will generally be pressed onto the part to form the desired result. Where the tool (rather than the workpiece) moves, the knurling tool is either moved using a milling machine or on a lathe. Some tooling is adapted to clamp the stationary workpiece and use the machine axes to traverse and impress the tool.
Knurling is not always a plastic deformation process but can involve a sliding cutting tool that uses a similar approach to broaching. Hand knurling can be achieved using a rotary hand tool (plastic deformation), a hammered pattern tool (plastic deformation), or a cutter/file format (material cutting). The results from a cut-based rather than plastic deformation knurling process can generally be visually identified by linear scoring (or lay) along the sides of individual grooves of the pattern.
Types of the Knurling Process
There are several different types of knurling processes, each with its unique characteristics and applications. The choice of knurling process depends on the desired texture, material, and the specific requirements of the workpiece. Here are some common types of knurling processes:
1. Machine Knurling
Most knurling is performed using a lathe (for cylindrical parts) or a milling machine (for flat surfaces. It is also possible to pass a knurling tool precisely over a surface with complex curvature, using a CNC milling machine. This is commonly performed on elements of a plastic mold tool, to create a knurled pattern in the resulting molded parts. It can also be performed on high-value machined metal parts, such as: on the surfaces of firearms, for grip, decorative, or branding purposes.
2. Hand Knurling
Hand knurling uses a basic rolling element hand tool that is clamped around the cylindrical axis of a part. It is rotated by hand while adjusting the applied pressure/depth by screwing in an adjustment on the diametral axis of the part. In a more traditional sense, hand knurling can also be performed with a hand-engraving tool, for customized and craftsman-made parts. This was the common technique used for handmade tools and instruments before the advent of precise machine tools, and it still finds application in decorative use in very high-value applications and one-offs.
Types of Knurling Patterns
Knurling on cylindrical parts, both internal and external, is of three basic patterns:
1. Straight Knurling
Straight knurling, or linear knurl, forms linear and parallel grooves along the axis of a cylindrical part. This can be used for grip or decorative purposes. It is also widely used to facilitate the push fitting of permanently engaged parts. This allows lower part precision with extremely good concentricity and a very tight fit that will perform equal service to other methods such as higher force smooth push fits or cryogenic push fits, but at lower operational cost.
2. Annular Rings
Annular groove knurling, or helical groove knurling, is a mostly decorative choice that can also provide improved grip on thumbwheels. Helical groove knurling is essentially identical to thread rolling, in that a single (or multi-start) helical groove is indistinguishable from a screw thread.
3. Diamond Knurl
This pattern uses two straight-cut pattern wheels that roll at an angle to the axis of the cylindrical parts. It co-imprints overlapping angled grooves that result in a diamond pattern cross-hatching. The angle between the grooves is commonly fixed at 30°, but a range of angles is possible.
Uses of the Knurling Tool in Manufacturing
Knurling tools are used on a variety of cylindrical, flat, and complex surfaces for a variety of purposes. Diamond and straight knurling are used for handle traction on long-service equipment in which a soft grip is liable to age badly. Expanding a malleable shaft to make it a push fit into a hole, reduces the precision required and enables high pull and torque resilience in the coupling. Decorative finishes on a range of surfaces break up the appearance and also help to disguise evidence of surface wear and scratching. Knurling is used to facilitate grip between plastic molding materials and metal components that are press-fitted or introduced before molding.
When To Use Knurling
Knurling serves a variety of purposes and can be selected for type and extent accordingly. It provides traction for wet and oily hands. It is widely applied to tools and equipment that are handled, particularly in sub-optimal grip conditions. Its advantage over options such as rubber grips is that it is formed in the intrinsic and hard materials of the tool/equipment and will not degrade in prolonged use.
Straight knurling facilitates great-quality shaft/hole engagement and very high torque resilience while allowing components to be made with relatively low tolerances. The allowance for plastic distortion in the engagement results in stronger coupling at a lower cost.
Knurling also provides an appealing transition from smooth surfaces. It can be used to remove machining marks, and provides an “engineered” feel to products. Custom knurling tools can be used to impose very resilient branding onto high-value parts. A mix of diamond and straight knurling is often used on metal components that are to be overmolded with plastics, to ensure optimal engagement between the metal and plastic elements which can otherwise have limited chemical bonding. A subset of the decorative use of knurling is its application to leather, as an attractive finish that can reduce the visual impact of wear and abrasion in long-term use.
Materials for Knurling
Knurling is most commonly applied to steel and brass, both of which are suited to the plastic deformation that rolled knurling requires. Additionally, knurling of steel tooling components will result in knurled patterning of the molded parts that the tool produces. Roller and cut knurling can be applied to a variety of materials, generally for decorative purposes. This includes: paper, leather, glass, precious metals, hard engineering metals, and wood.
Applications of Knurling
Knurling is used in a variety of contexts:
- For machine handles, on which grip is important and hands are at risk of being wet or oily. It is particularly important as a feature on engineering tools that may have a very long service life and require considerable wear resistance. Example: lathe control handles.
- Whenever metal parts are to be encapsulated by polymer or composite materials, a knurled pattern is commonly used to promote adhesion and improve torsional and pull-out resilience in the coupling. Example: brass inserts for threading in plastic molding.
- Knurling applied to a shaft (or potentially inside a hole) can be used to provide a ductile and malleable zone that allows lower-cost higher-strength push fits in shaft/hole applications. This reduces the overall precision and therefore cost of the two components while enabling a strong coupling. Example: driveshaft fitted to a machine flywheel.
- Knurling is used to provide decorative and wear/abrasion tolerant surfaces. This can also visually enhance surfaces to lend them a more technical and engineered feel/appearance. Examples: patterning on public space seating to increase grip and reduce the appearance of wear.
Advantages of Knurling
The advantages of knurling are listed below:
- It promotes good grip on machine and instrument handles and reduces the appearance of wear.
- It allows lower cost/precision in push-fitted parts.
- It can break up the appearance of surfaces for visual appeal.
- It provides adhesion/traction surface connection in overmolding with polymer or composites over metal components.
Disadvantages of Knurling
Although knurling is a valuable process that produces various benefits, some disadvantages and limitations should be considered:
- The process deforms the material's surface, which can result in a reduction in the material's overall strength and fatigue resistance.
- Unsuitable for hard and brittle materials, such as ceramics or hard plastics which resist plastic deformation.
- Achieving precise control over knurl depth and ridge width requires some skill. Variations in the process, tool wear, and material properties alter the consistency of the knurled pattern and can result in visual and functional variation between parts.
- Knurling tools or wheels are subject to wear over time, which affects the consistency of the outcome. The harder the subject material, the more profound this effect will be.
- The process is typically used on relatively small to medium-sized workpieces.
Precautions To Be Taken When Knurling
The process can produce variable results, so certain practical considerations must be accounted for. For example, tooling must be in good operational condition and the patterns must not be excessively worn. Applied pressure must be within safe operation limits and held consistent, for a uniform outcome. Loading on machines can be high, so care must be taken to avoid excessive machine wear over long-term operation. Quality can vary between operators, setups, and over time, so careful quality assurance is required to maintain consistent outcomes.
Knurling vs. Engraving
Knurling, in most cases, is the roller application of forming tools that plastically distort the target surface to form the required pattern. Engraving, on the other hand, uses a generally single-point tool to cut pattern features into a surface by material removal. Before the advent of precision machine tools, it was common for the knurling of components to be achieved by engraving, blurring the differential between the two processes. Cut knurling is a form of engraving that allows a knurled outcome to be achieved on surfaces that are unsuitable for roller knurling for a variety of reasons. To learn more, see our guide on What is Laser Engraving.
Summary
This article presented knurling, explained it, and discussed how it works and its various uses. To learn more about knurling, contact a Xometry representative.
Xometry provides a wide range of manufacturing capabilities, including CNC machining and other value-added services for all of your prototyping and production needs. Visit our website to learn more or to request a free, no-obligation quote.
Disclaimer
The content appearing on this webpage is for informational purposes only. Xometry makes no representation or warranty of any kind, be it expressed or implied, as to the accuracy, completeness, or validity of the information. Any performance parameters, geometric tolerances, specific design features, quality and types of materials, or processes should not be inferred to represent what will be delivered by third-party suppliers or manufacturers through Xometry’s network. Buyers seeking quotes for parts are responsible for defining the specific requirements for those parts. Please refer to our terms and conditions for more information.
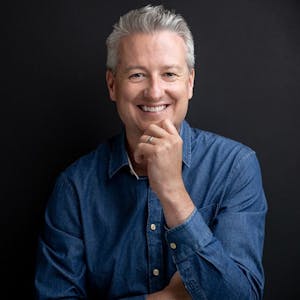