Passivation is a simple, affordable, yet very effective way to ramp up the corrosion resistance of stainless steel… but it has to be done carefully and in controlled conditions. Let’s take a closer look at how this beneficial process is used in industry and how it’s done.
What is Passivation?
Passivation is used in manufacturing to enhance stainless steel’s resistance to corrosion without changing its appearance—it will still have that clean and shiny finish that it’s known and loved for. Thanks to its chromium content (which, when it reacts with oxygen, forms a protective oxide layer), stainless steel is already naturally corrosion-resistant. Passivation helps to bring this back and better than ever by removing ferrous impurities from the metal’s surface.
Companies can save time and money by passivating their metal parts because the extra corrosion resistance minimizes the risk of contamination-related production losses and/or downtime. Regular passivation also reduces the need for system shutdowns and maintenance. The process is widely used across many industries, in large part thanks to the corrosion protection benefits, and here are just a few:
- Aerospace: Fasteners, hydraulic fittings, fuel system parts
- Medical: Biocompatible implants, surgical instruments
- Food processing: Hygienic equipment that complies with strict industry standards
- Electronics: Connectors, semiconductor processing equipment
- Automotive: Engine parts, exhausts, fasteners
Passivation removes chemically reactive free iron or other foreign substances, but won’t eliminate heavy oxide scales or heat tint from welds and heat-treated zones. For that, you’d need to perform a pretreatment called pickling that uses stronger acids, like nitric-hydrofluoric or sulfuric acid.
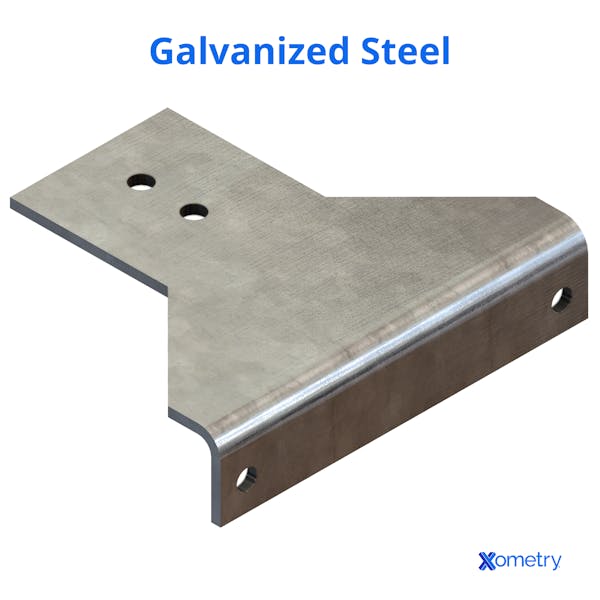
How it Works
To get a little technical, passivation works by increasing the ratio of stable chromium atoms to the more reactive iron ones in the top few atomic layers of the metal's surface, which creates a strong and protective oxide layer. There are two ways it can be done:
- Immersion: Submerging the metal parts in a passivation solution (typically nitric or citric acid) for a set duration and temperature.
- Bluing: Applying a conversion coating that forms a thin, blue-black oxide layer, which reduces glare but needs regular oiling to keep the corrosion protection.
Process
Here’s how it’s done, in four fairly simple steps:
- The metal surface is thoroughly cleaned to remove contaminants like dirt, grease, or scale.
- The cleaned part is immersed in the mild acid solution. This reacts with and removes stray iron particles and contaminants and helps kick-start the oxide layer’s formation.
- The temperature and immersion time must be carefully controlled; too low a temperature may slow the reaction down, but too high could damage the metal’s surface. Somewhere in the 50–70°C range is best for 20–60 minutes.
- The part is rinsed to get rid of any residual acid.
FAQs on Passivation
Which is better, nitric or citric acid?
While they are both effective, the “better” option would depend on your needs. Nitric acid is highly effective at removing iron-based contaminants and forming the protective oxide layer, and it does so quickly… but it’s quite an aggressive substance and needs to be handled with care. Citric acid needs a longer duration, but it’s a safer, more eco-friendly option.
Is there anything that can make the process more effective?
First and foremost, the part has to be extra clean before you start because any trace of dirt can foil the whole thing. A process called electropolishing that smoothes the surface with an electric current, or pickling, which we briefly mentioned above, can be performed before passivation. In addition, many of our customers perform the following specialized tests to check how well the passivation process will work by analyzing the surface to see how much protective chromium is present:
- EDX (energy dispersive X-ray)
- AES (auger electron spectroscopy)
- ESCA (electron spectroscopy for chemical analysis)
Passivation vs. anodizing—what’s the difference?
Passivation is a chemical process that improves a metal’s corrosion resistance by helping to reform its natural protective oxide layer using an acid. Since chromium oxide is a typical passive coating, the process is mainly used on stainless steel because of its chromium content. Anodizing is an electrochemical process mostly used on aluminum for durability and cosmetic reasons. It creates a controlled oxide coating with an electrical current in an acid bath.
How Xometry Can Help
We believe strongly in the power and perks of passivation, which is why, in addition to our main offerings (i.e., CNC machining, 3D printing, etc.), we offer it as a value-added, turnkey service. Get your free, no-obligation quote today, or reach out to one of our representatives for questions or advice.
Disclaimer
The content appearing on this webpage is for informational purposes only. Xometry makes no representation or warranty of any kind, be it expressed or implied, as to the accuracy, completeness, or validity of the information. Any performance parameters, geometric tolerances, specific design features, quality and types of materials, or processes should not be inferred to represent what will be delivered by third-party suppliers or manufacturers through Xometry’s network. Buyers seeking quotes for parts are responsible for defining the specific requirements for those parts. Please refer to our terms and conditions for more information.
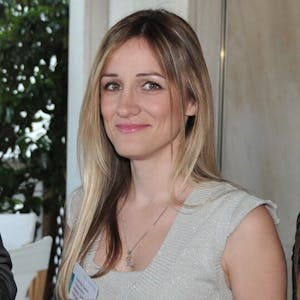