The Best Ways to Pressure Test Complex CNC Parts
Custom CNC machining features some of the most technologically advanced equipment and cutting-edge robotic technology. It is programmed using G-code and M-code, which facilitates accurate, repeatable manufacturing of parts. Besides, specific components demand strict spec tolerances, all of which are achievable using a custom CNC machining process. However, the next question that arises is how do you test a complex CNC component?
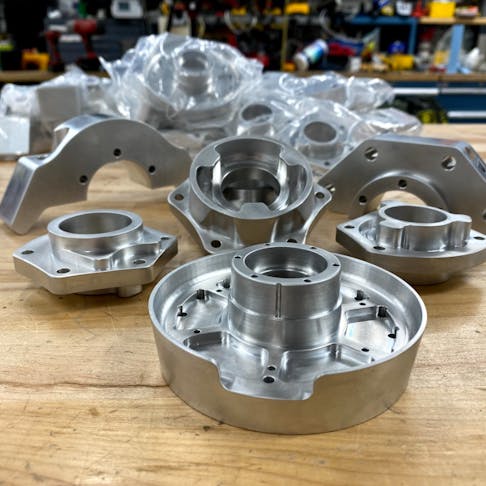
Pressure Testing: A Fundamental Phase of Quality Assurance
Reputable CNC shops employ state-of-the-art inspection tools as their quality management system. Some of the typical tests include Millipore testing, CMM inspection, hardness testing, surface finish testing, and more, which comply with ISO 9001:2015 and IATF 16949:2016 certifications. However, CNC shops must utilize different methods to test parts that hold pressurized fluids or gases due to defects like porosity, which is a void found in the casting. Porosity can cause the fluids or gasses to leak out of the component that was supposed to be pressure-tight. This defect impairs the performance of the component and can lead to internal corrosion or surface defects. Such defects must get hunted more aggressively, especially in the case of complex CNC machined parts. These parts are fully assembled and include different components bound together.
Pressure Testing: When Should you do it?
Pressure testing is typically performed after assembly, machining, or vacuum impregnation, which is a process of sealing the porosity of castings and leak paths using a sealant under pressure. This practice helps contain fluids and gases without leaking. The most common stage after which testing is performed is assembly. In this stage, testers use poka-yoke methodology, which determines the correctness of the assembly process and verifies the quality of the CNC machined part. This approach lets you verify the entire assembly via a pressure test. As per the clients' requirements, testing might stay within limits or reach 100% if the client demands extreme precision in the final part. The greater the testing, the higher the production charges. Manufacturers maintain a cost/value ratio while upholding product quality.
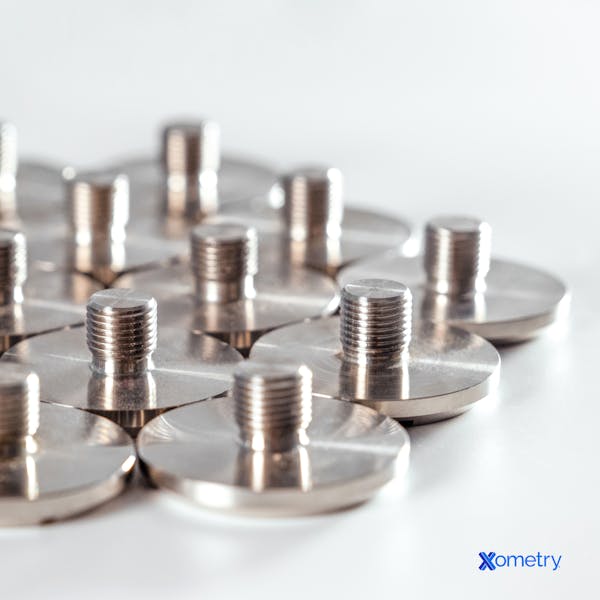
Different Pressure Testing Types Used for Complex CNC Machine Components
There are three fundamental ways that you can follow to pressure test complex CNC components -
- Air Decay
- Mass Flow
- Air Under Water
There are several benefits of a CNC machine, all of which can be enhanced by ensuring premium quality standards via pressure testing.
Air Decay
This approach uses a pressure test control unit that monitors a change in air pressure within the component. Upon securely clamping the part into a fixture, pressurized air is used to fill it up. Pressure typically ranges between 5 psi and 90 and varies with the pore size within the part. The most common air pressure value used is 20-25 psi.
Once the air molecules have stopped moving, roughly after 30 seconds, a measure is taken to calculate the pressure drop and if the value complies with the customer’s expected specs.
A machined part's complexity directly influences the time taken to perform the test. A test can take up to several minutes if the machined part has high volume and the precision expectations of the customer are high.
Some real-life examples of air decay include the air inlets for engines or an engine case where oil is loaded.
Mass Flow
Similar to air decay, mass flow introduces air into the part at about 20 psi range. This approach uses a gauge to monitor the pressure, which indicates when the part is completely full and at 20 psi.
When the machined part reaches the point where it can no longer let in more air, you notice zero reading on the gauge. If air escapes through pores, you will get the reading from the gauge indicating that the part is letting air in, which affirms the presence of a leak.
If the client does not require the highest possible performance specs, then getting zero on the gauge may not be the end goal. Typically, it is acceptable to have a small leak rate of about +5 sccm (Standard Cubic Centimeters per Minute).
Air Under Water
Air under water is a seamless and accurate testing method since it depends on visual observation and not a gauge to perform pressure testing. This practice is simple to execute and features easy leak detection.
An air-filled part with all openings sealed gets immersed into a water tank. Inspectors look for bubbles, which can either be tiny, like champagne or sizeable blurbs. These bubbles reach the water surface, which indicates a leak.
There are underwater lights installed that ensure optimum visibility, considering that this test relies on visual inspection.
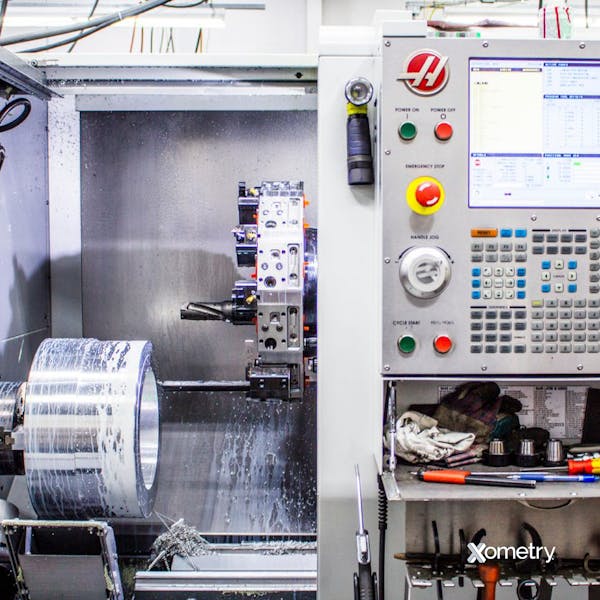
Final Thoughts
Optimum pressure testing of complex CNC parts is crucial to ensure premium-quality standards, satisfy customer needs, and ensure high-performance metrics. On top of that, it is also imperative to minimize production costs if the client does not require high precision.
CNC machine shops with in-house internal pressure testing capabilities can ensure quality control at each step of production. Besides, an in-house pressure testing machine minimizes outsourcing, which creates a shorter lead time.
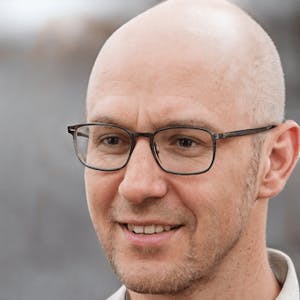