An undercut is a feature that cannot be reached with a standard end mill. For this reason, designing parts with undercuts can often be tricky. Parts with undercuts can often more be more costly and potentially more difficult to manufacture than standard parts.
Below are two examples of how to undercuts can affect the design of your part.
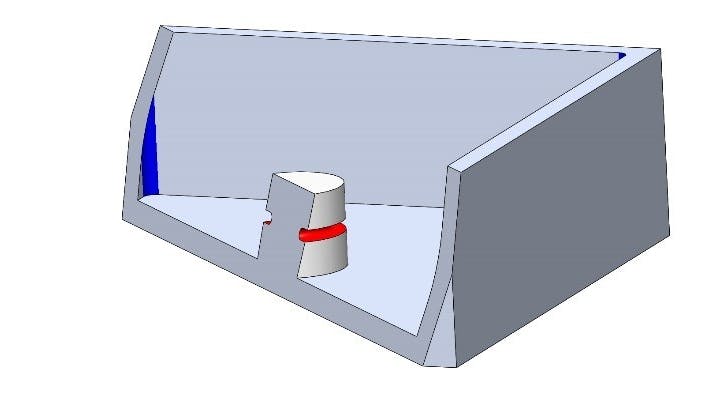
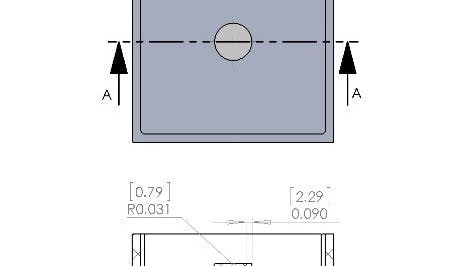
A special tool may be required if the feature is not a standard dimension. In the example below, the radius in the slot is 0.053”. An expensive custom tool would be required to create the geometry and the cost of the part would increase significantly.
If a standard .062” (1/16”) radius is used, then the cost of the tool would be less than half the cost of the custom tool. The pictures below illustrate an example of a simple undercut design.
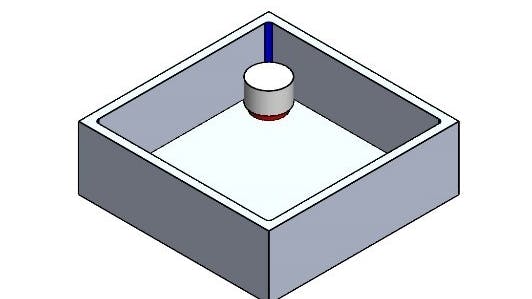
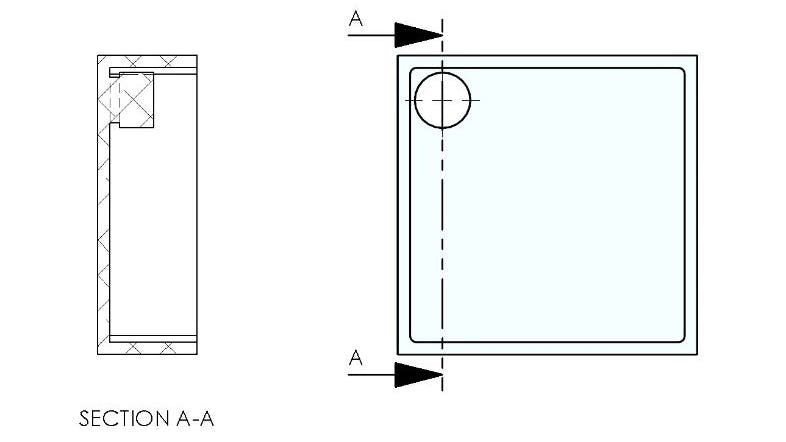
In some cases, the undercut feature may be too deep to be reached by any tool.
Because the tool required has a horizontal cutting blade attached to a vertical shaft, there are limits to the depth of the cut. There is no hard and fast rule as to the depth of the undercut, but the shallower the better. Also, when designing the undercut feature, it is critical to only create undercuts in areas that the tool can reach. The illustration below depicts and undercut feature that cannot be reached in the machining process.
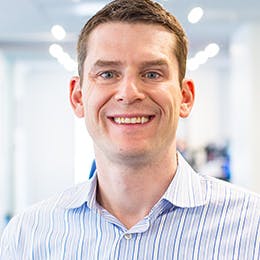