There is an abundance of machining processes out there, all of which provide specific perks and unique results — and side milling is no different. Working on a vertical plane, you can create different slots and cuts with these machines. While it may seem like these are small details, they’re impactful when it comes to finished products that require smooth finishes and accurate slots to function as they’re supposed to.
Side milling has many different use cases and does differ from other milling methods you might be more familiar with. Below, we’ve given a brief rundown of how this particular type of milling works and how it might be most useful to your day-to-day workflow.
Side Milling and How It Works
The most important distinction with this type of machining process is that the milling cutter works into the side of the workpiece, as its name would imply. The machine has a cutter that’s mounted onto an arbor, which will slice into the material that’s clamped down to the work table. Then, the edges or teeth on the cutter will cut into the object and create the shape or design you need. It’s a popular method that you can use in tandem with the likes of turning, drilling, and boring, too.
There are various materials you can use for side milling, including metals, plastics, and composites, which gives this machine versatility. If you’re trying to calculate feed rate, there are a few equations you can always rely on to get the right number:
First, get the RPM, which is:
RPM = (12 Surface Speed) / (Pi Tool Diameter) [revs/min]
Then you can get feed rate:
Feed Rate = RPM Chip Load Number of Teeth (Flutes) [in/min]
Remember that Pi = 3.14159
Tools and Equipment Needed
To make the most of side milling, you’ll need a machine with several parts. The first is a milling machine, which is the main component that will power the cutter and allow it to move in the right direction. A side milling cutter is also necessary for making cuts into the side of an object. The arbor is also an important part because it’s the bridge between the milling machine and the specialized side cutter. You’ll also want to have some kind of clamps or vises on hand to hold your workpiece in place, as well as a cooling system to keep friction and chips at bay.
It’s worth pointing out that the type of material your cutter is made from will also make a difference in your finished product and how nice the finish is. For instance, a carbon tool steel cutter is great when it comes to abrasion resistance, but it loses hardness when it hits a certain temperature, making it a mediocre choice for materials that need to be cut at higher speeds. Carbide, on the other hand, is able to handle these temperatures and cut precisely and accurately, but these cutters may be more expensive.
How it Differs From Other Milling Methods
You might be curious about how side milling compares to other milling processes you’ll come across. The answer is relatively simple and present in the name: it cuts sideways. Because of how the cutter is positioned and what it’s meant to do, it stands out from milling machines that cut on different axes or from different directions, like in face milling, where you’d cut a workpiece from the top. It’s also built for the purpose of creating slots, contours, and designs into the sides of objects (whether on a vertical or horizontal plane) which not all other milling processes are capable of doing.
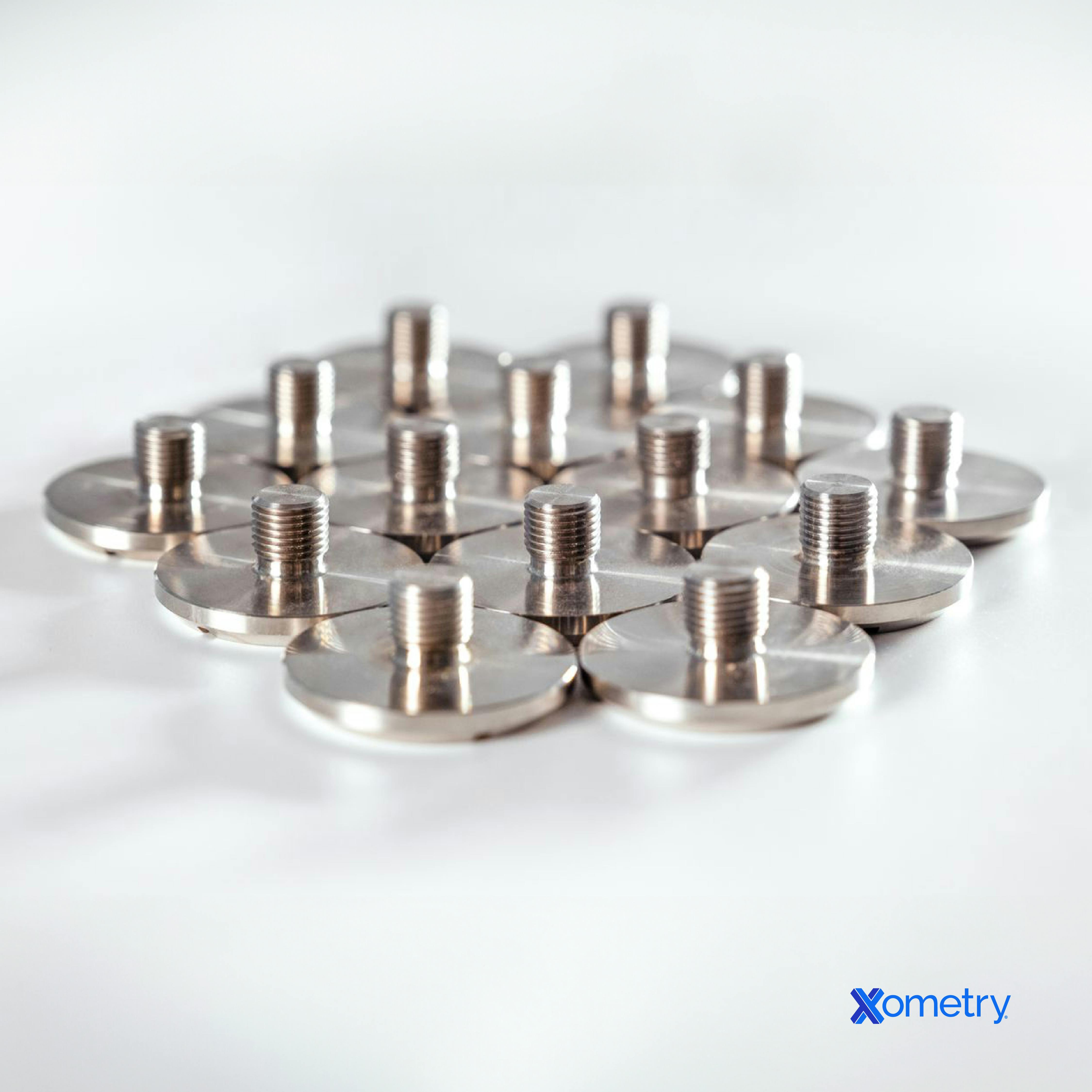
Types of Side Milling
As you’ll find, there are two styles of side milling that involve different types of cutters, which you can learn below:
- Plain Cutters: Also called straight-tooth cutters, this type of side milling uses cutters with teeth lined up single file rather than staggered. It’s the right cutter to use if you’re doing all-purpose work, creating slots, or working on flat surfaces.
- Staggered-Tooth Cutters: Alternatively, you can use a staggered-tooth cutter, which features teeth that alternate along its circumference. This is particularly useful if you want to cut down on vibration or chatter and get a smoother finish overall. It is also a great type to use in heavy-duty operations or instances where surfaces are drastically uneven.
Factors That Can Affect the Quality of Milled Products
When you’re side milling, it’s worth being aware of the specific details that can impact how the final piece looks and functions. Here are a few factors to keep your eye on:
- The feed rate and how deeply you cut
- The design of the tool, including the number of teeth, chip formation, and helix angle
- What the cutting tool is made out of
- How accurate and well-aligned the spindle is on the milling machine
- How stiff the tool is
- How hard your workpiece is and the type of material it’s made out of
- The speed of your cutting tool and how quickly it moves across and into the workpiece
- How well-trained and skilled you are as a milling machine operator
Applications
This list covers some of the most important applications you can use side milling for:
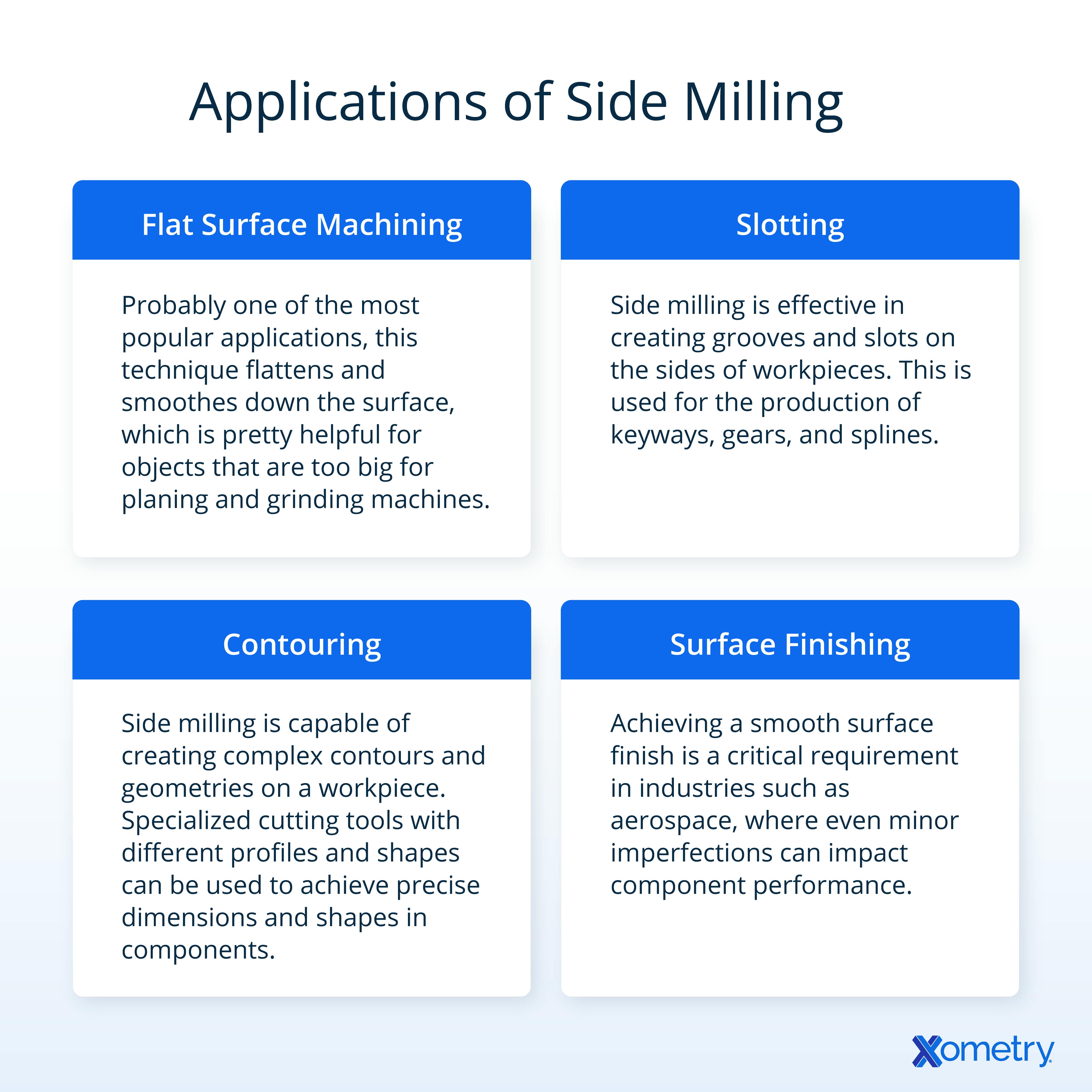
Advantages and Disadvantages
Here are some of the benefits you’ll reap when working with side milling machines:
- Various textured finishes: A side milling machine can produce a wide range of surface features, such as flat vertical surfaces, slots, and intricate contours.
- Ideal for slots and grooves: When you need these types of cuts on a workpiece, side milling is the way to go.
- Range of cutter types: You can purchase cutters in plenty of sizes, types, and materials so you can really cater to the kind of work you’re doing and the specific materials you’re machining.
- Quality and accuracy: Side milling machines can give you precise and accurate finishes where other machining processes might not be able to.
There are also a few downsides of side milling to take note of:
- Only machines the sides: As its name says, this machine is built for carving into the side of an object and not other surface areas.
- External feature focus: If you’re looking for a process to machine internal parts, skip the side milling machine and opt for another service like end milling.
- Not ideal for thin workpieces: With the force that comes from these machines, you may find that thinner boards and surfaces will bend, warp, or deflect under the pressure.
Common Challenges with Side Milling
Side milling isn’t too convoluted of a machining operation, but it can be difficult and cause a few tricky problems. Below are the most common issues that arise and what you can do to solve them:
- Jerky or inconsistent chip evacuation: The best way to ensure a smooth chip evacuation is to buy a side milling cutter with specialty chip breakers and monitor the coolant flow. Feed rates can also impact this.
- Excessive vibration or chatter: You can lower the radial engagement angle or use shorter tool holders to stop annoying vibrations or chatter that are affecting the look and finish of your products.
- Premature or overtly quick tool wear: This can be down to feed rate and tool speed or something as obvious as lower-quality tools that aren’t built to last for a long time. Try to only purchase high-quality parts and cutters if possible and adjust speeds and rates for the type of material you’re milling.
- Tool breakage: This can happen when feed rates are too quick or if you use too long of tools. Make sure your alignment is correct, slow down your feed rate, and use shorter tools to prevent this.
- Workpiece deformation: This usually happens when you’re machining a piece that is too thin. Try to side mill materials with thicker diameters and reserve the thinnest pieces for other machines if possible. If this isn’t doable, slow down your feed rate and give the workpiece ample support while you mill it.
Safety Considerations
To make sure your side milling operation is safe, follow these guidelines:
- Wear personal protective equipment, including hearing protection, work gloves, and safety glasses, and make sure your team or milling machine operators do the same.
- Make sure the guards are down and work properly so there are no accidents or injuries that happen with moving parts.
- Uses vises or clamps to keep your workpiece in place and prevent sliding, errors, and serious injuries.
- Inspect your side milling machines every time before you use them and always keep them well maintained.
- Train your team and ensure people are always up to speed with safety requirements, emergency procedures, and proper operation protocol for this type of machine.
- Make sure every person that uses a side milling machine and the people surrounding them know where the emergency stop buttons are.
How Xometry Can Help
Xometry provides a wide range of manufacturing capabilities that are applicable for aerospace, automotive, medical, and construction industries, among many others. Whether you’re interested in CNC milling or something completely different, you can get your instant quote today.
Disclaimer
The content appearing on this webpage is for informational purposes only. Xometry makes no representation or warranty of any kind, be it expressed or implied, as to the accuracy, completeness, or validity of the information. Any performance parameters, geometric tolerances, specific design features, quality and types of materials, or processes should not be inferred to represent what will be delivered by third-party suppliers or manufacturers through Xometry’s network. Buyers seeking quotes for parts are responsible for defining the specific requirements for those parts. Please refer to our terms and conditions for more information.
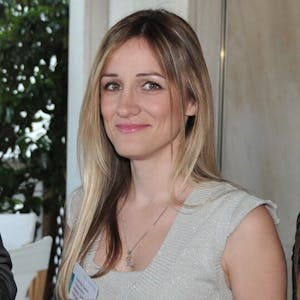