Swiss machining has become a staple in modern manufacturing thanks to its ability to create components with remarkable accuracy… no wonder it’s a hit in demanding sectors like aerospace and medical. In this article, we’ll discuss what exactly Swiss machining is, how it works, and how it can be — and is — used.
What is Swiss Machining?
It all starts with the machine itself (also referred to as a Swiss lathe/machine/automatic lathe) that can carry out several tasks using different tools to work on a material or workpiece at the same time. The initial costs of buying and setting up a machine like this are most often higher than other basic equipment, but manufacturers feel that they end up paying for themselves. Although we don’t know exactly when it was invented, this machining procedure has gone through many refinements and developments that continue even today.
As you may have guessed, Swiss machining comes from Switzerland, back when almost every quality watchmaker was based there. In fact, it was originally developed in the late 19th century (generally attributed to Swiss watchmaker Jacob Schweizer) as a lower-cost and more precise way of making watch components, as the traditional manufacturing methods just weren’t cutting it. It eventually outgrew watchmaking and started being used for other products, like medical devices, electronics, and aerospace and automotive components. Some parts made with Swiss machining are shown in the image below.
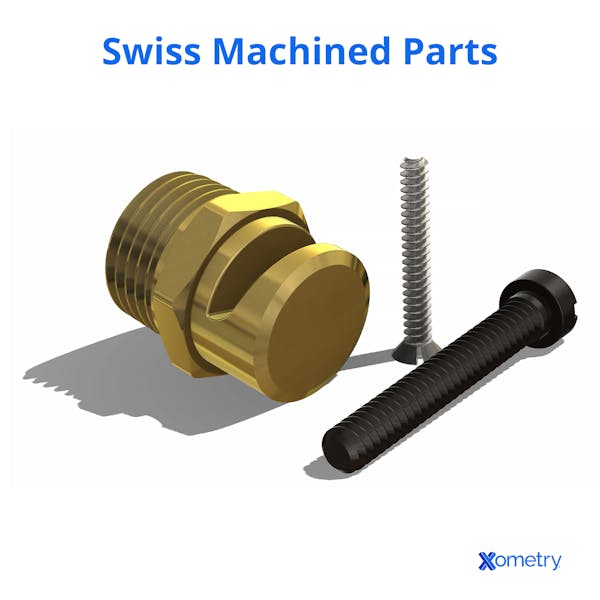
Precision aside, the process offers many other benefits, too, including lower chatter, the ability to process longer and thinner parts quickly, and overall speed because it uses multiple tools at once. In addition to small and high-precision parts, it’s a great way of working on long pieces with small diameters that could bend with other methods, workpieces that need both turning and milling in a single setup, and components that are made in large quantities or are highly valuable. As they’re designed to work on small parts with extreme precision, these machines aren’t ideal for huge, bulky pieces. They also need a certain level of skill to operate.
How it Works
It uses an automated clamp to push a long rod of material (called bar stock) into the machine. The clamp holds the material and just about feeds enough of it into the cutting area to make a part. Right behind that area, the material is supported by a rotating guide that keeps it steady and reduces vibrations. This design allows you to machine components with higher aspect ratios and tighter tolerances.
In a regular lathe, the material that’s being worked on is held in place, and it spins while tools work on shaping it. Longer parts can have extra support by means of a second holder to keep them in place. A Swiss lathe, though, is different in that the material can spin but also move back and forth, allowing multiple tools to work on it at the same time. This is great because it’s faster and much more versatile, allowing you to do other things like milling on the same machine.
The workpiece, which is usually a long, slim rod of metal or plastic, is fed into the machine from behind the headstock. Right next to the work area is a guide bushing, and the workpiece is inserted through it. That way it’s guided and supported during the work which reduces vibrations and helps everything run smoothly and precisely.
The machine also has a bar feeder that provides a continuous flow of the material, which means that it can keep going without you having to intervene all the time. When a part is finished, the bar feeder automatically releases the clamp, moves the material forward to the length of the next part, and then reclamps it. The machine’s headstock will hold and spin the material using its main spindle, and that will provide the needed rotation for machining.
The workpiece in the machine is surrounded by holders for tools, so you can mount anything you need in them. These tools can move independently on all three axes without any slack, and they’re extremely accurate. Each tool will either be a single-cutter or a rotating multi-cutter, and that way, you have everything happening at once—turning, drilling, milling, threading, or cross-drilling—depending on what you need. The tools are very close to the workpiece so the fact they don’t need to travel far is another reason why the whole thing is pretty quick. When the part is done, it’s separated from the rest of the material using a cut-off tool. Most modern Swiss lathe machines are usually CNC-controlled (computer numerical control).
Compatible Materials
We already mentioned that metals and plastics are quite common materials used in Swiss machining, but here’s a more detailed breakdown of some specific examples:
Material | Description |
---|---|
Material Copper | Description Electrical connectors, pins, sockets, and other components that need good electrical performance and heat dissipation |
Material Brass | Description Excellent palatability and used for connectors, fittings, valve bodies, decorative parts, and other things that need to be visually appealing and corrosion-resistant |
Material Nylon | Description Bushings, gears, insulators, and other components that require resistance to corrosion, as well as being low in density, and having a low friction coefficient (slippery surface) |
Material Titanium | Description Amazing strength-to-weight ratio, corrosion-resistant, and biocompatible, often used for aerospace components, medical implants, and other high-performance parts |
Material Aluminum | Description Easy to machine, low in density, and impressive resistance to corrosion, so often used to make aerospace parts, automotive fittings, and consumer goods |
Material Nickel | Description High-temperature strength, corrosion resistant, and electrically conductive, found in aerospace, electronics, and chemical processing applications |
Material Plastics | Description Includes lots of different rigid and engineering plastics found almost everywhere, with qualities like low friction, low density, low cost, and resistance to corrosion |
Material Carbon Steel | Description Durable and cost-effective, usually found in automotive fasteners, shafts, firearms, and industrial machinery parts |
Swiss Machining Compatible Materials
FAQs on Swiss Machining
How accurate is it?
Usually, you can get tolerances of +/-0.0004 mm on small and flex-vulnerable parts. Many other traditional machines can only get that close if you spend a very long time fine-cutting to the extreme. You can also typically get very good length tolerances with Swiss machining, but that has more to do with the construction of the machine itself rather than the process—which is almost the same as in other machines.
How long does the process take?
This depends. It’s hard to put a number on it because it differs from project to project. But a similar series of operations by Swiss machining will typically be faster than the traditional or capstan lathe equivalent. The same applies when compared to a 4+ axis CNC machine, which again usually carries out a single job at a time.
What’s the difference between Swiss machining and traditional milling?
There are lots of differences between the two, but some of the main ones are that traditional milling generally uses a stationary workpiece while the cutting tools move around it. It’s quite versatile and can work on bigger items too that don’t need extreme precision. But it can take longer because it doesn’t multi-task like Swiss machines can. We have a whole guide on traditional milling. Why not check it out?
What’s the difference between Swiss machining and CNC machining?
Comparing the differences between these two can become somewhat blurry, but their main dissimilarities lie in the way they support parts and how the tools are used. Swiss machines usually use less than 10 cutters in a setup. CNC machines, though, can have as many as 40 of them ready for change. Additionally, they usually hold the piece stationary while the cutter rotates in 3-axis machining, but in 4+ axis work, the part can rotate for more complex cuts. These machines don’t normally have localized support, which could potentially cause the workpiece to distort unless it’s managed very carefully in programming. They also don’t have an automatic feed of material. As technology advances, the differences between these two procedures are becoming harder to find.
How Xometry Can Help
If you need further clarification on the topic of Swiss machining, why not reach out to one of our representatives? Xometry also offers a plethora of related services, including CNC machining, laser cutting, and 3D printing. You can get your project started as soon as possible by requesting a free, no-obligation quote directly from our website.
Disclaimer
The content appearing on this webpage is for informational purposes only. Xometry makes no representation or warranty of any kind, be it expressed or implied, as to the accuracy, completeness, or validity of the information. Any performance parameters, geometric tolerances, specific design features, quality and types of materials, or processes should not be inferred to represent what will be delivered by third-party suppliers or manufacturers through Xometry’s network. Buyers seeking quotes for parts are responsible for defining the specific requirements for those parts. Please refer to our terms and conditions for more information.
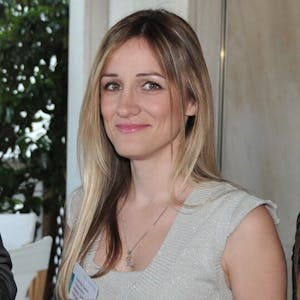