Xometry is familiar with all sorts of threads and threading techniques, allowing us to make custom parts with everything from standard UN or metric threads to custom thread forms. Tapping and threading both involve the creation of threads, but there are some differences.
Let’s take a look at the similarities and differences between these two terms, starting with the area where most confusion stems from: tapped and threaded holes.
Tapped Holes & Threaded Holes — What Are They?
Threaded holes are holes with internal threads created using threading tools such as taps, thread mills, or with the aid of threaded inserts. In engineering, fastened parts aren’t complete without threaded holes. Threads are often added during CNC machining for speed and accuracy. It is common for threading to be one of the final steps of making a part, especially if threaded inserts are involved.
A tapped hole is simply a type of threaded hole. More specifically, it is a threaded hole produced by using a tap. These tools consist of a rod with sharp edges or teeth that cut into the sides of holes, forming internal spiral grooves (threads) as they cut away material. Tapping is a fast and convenient way of threading a hole and is one of the most common techniques we see in our shops.
In short, a tapped hole is a type of threaded hole, but a threaded hole is not always a tapped hole. With Xometrys Instant Quoting Engine® we make it easy to call out the number of threads a part has to ensure an accurate quote and to easily communicate part requirements to the manufacturing shop.
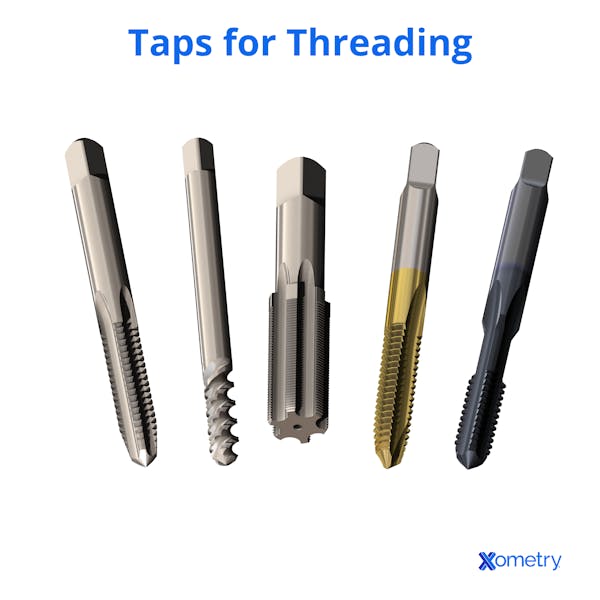
Tapping vs. Threading — Comparison
As mentioned above, tapping is a type of threading process for creating internal threads in holes. Threading is a generic term used to describe when threads, either internal or external, are created using various types of cutting tools. You can thread a hole or bore to create internal threads, but you can also thread external cylindrical features to create threaded rods or fasteners. External threading can be accomplished using a cutting die, a single-point cutting tool on a lathe, roll forming tools, and more.
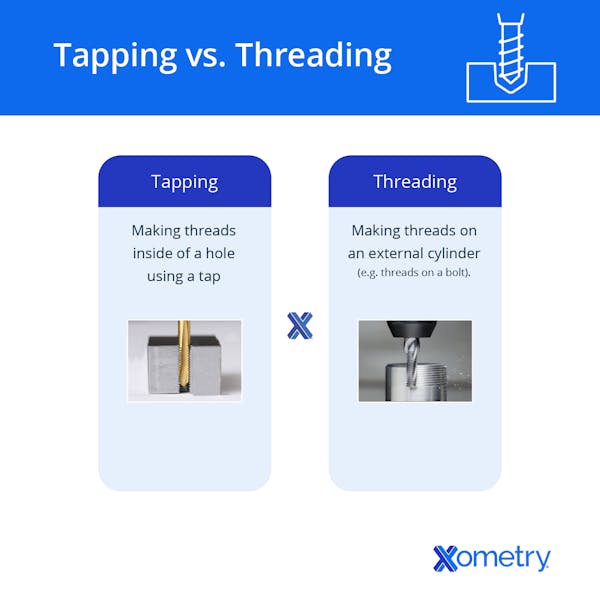
FREE CNC Machining Design Guide
Similarities and Limitations
The tapping and threading processes are similar in that they both create internal threads for a threaded fastener, such as a bolt, to fit into. They can also both be used with blind or through holes. A hole is considered blind when it does not go entirely through the workpiece.
As far as limitations go, we will focus on the limitations of tapping since threading encompasses all other types of thread-creation techniques. Here are limitations to be aware of with tapping:
- Thread Type: Tapping is limited to internal threads only. For external threads you will have to turn to other threading processes, such as using dies.
- Thread Variety: A tap is designed to create a thread with a specific size and pitch. This means if you want to create a variety of threads, you will need a corresponding tap for each. Additionally, this rules out custom thread forms, which would be better handled with a process like thread milling.
- Tool Breakage: Taps are more susceptible to breaking than other threading tools. Broken taps can become nightmares for a machinist as they can be difficult to remove, even warranting scrapping the entire part in some instances.
- Blind Hole Depth: Since most taps have a tapered lead on them to assist with the cutting process, this means they can only go so deep before hitting the bottom of a blind hole. If you need your threads to get as close to the bottom of a blind hole as possible, you may need to resort to other methods, such as thread milling.
- Material Limitations: Taps do not work the greatest on hard or brittle materials, such as hardened steel. These type of materials tend to quickly wear down taps, making them ineffective at producing good threads, or requiring frequent tool replacements, which increases cost. On the flip side, very ductile materials can also cause issues for taps, as they can become "gummy" and stick to the tap during the cutting process, requiring frequent tool cleaning or swaps.
Overall, tapping can be a great way of threading holes in parts under the right circumstances, but you may need to resort to other techniques when working with certain materials and thread forms or when you want to mitigate tool breakage risk.
How Xometry Can Help
At Xometry, we deal with all sorts of internal and external threads on a daily basis. We can create everything from standardized UN and metric threads to fine-pitch optical threads to completely custom forms. We are also experienced with using various types of inserts such as press-fit, helical, key locking inserts, and more to add threads to parts.
If you have custom parts that require threads, consider Xometry for your next project. You can get instant pricing and lead times by uploading your CAD files to the Xometry Instant Quoting Engine® and configuring your automatic quote today!
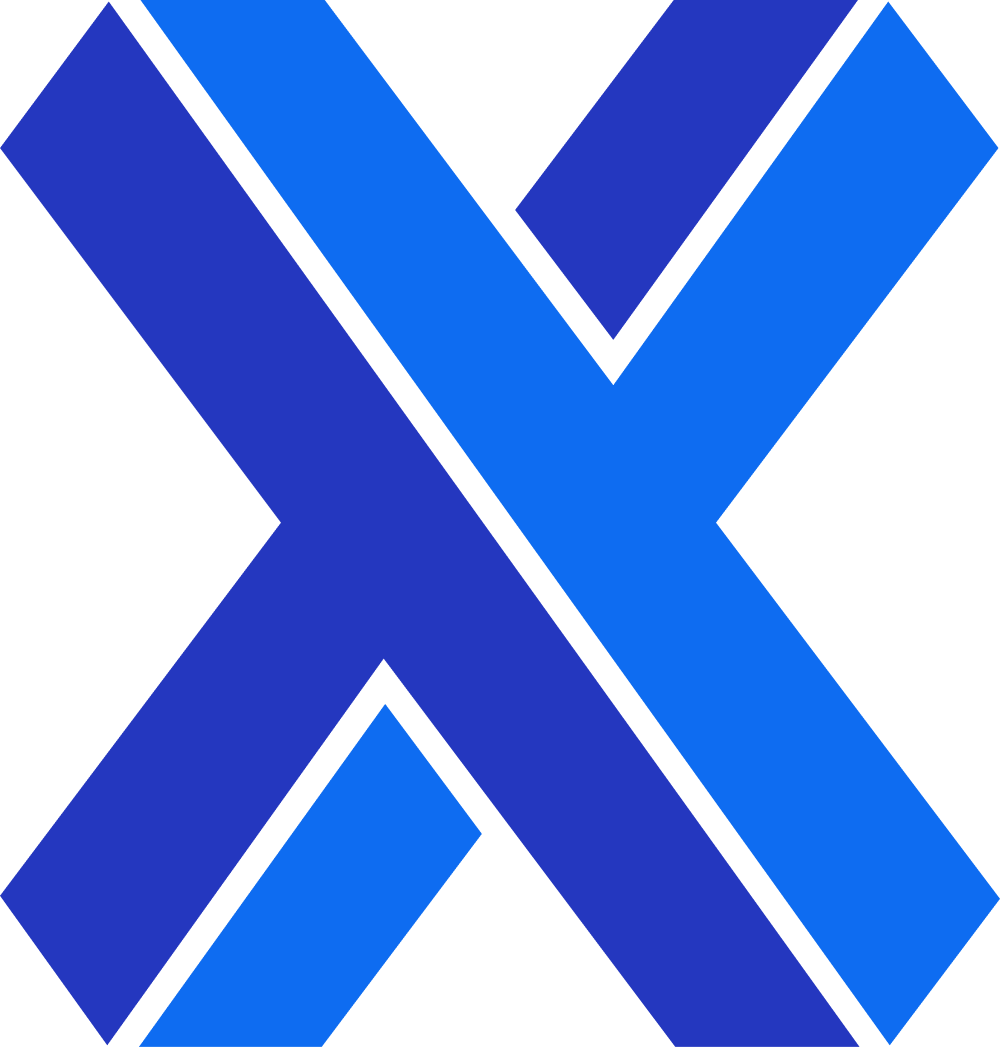
Disclaimer
The content appearing on this webpage is for informational purposes only. Xometry makes no representation or warranty of any kind, be it expressed or implied, as to the accuracy, completeness, or validity of the information. Any performance parameters, geometric tolerances, specific design features, quality and types of materials, or processes should not be inferred to represent what will be delivered by third-party suppliers or manufacturers through Xometry’s network. Buyers seeking quotes for parts are responsible for defining the specific requirements for those parts. Please refer to our terms and conditions for more information.
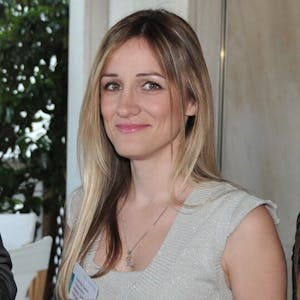