Anodizing is the deliberate oxidation of the surface of metals by electrochemical means, during which the component oxidized is the anode in the circuit. Anodizing is only applied commercially to metals, such as: aluminum, titanium, zinc, magnesium, niobium, zirconium, and hafnium, whose oxide films offer protection from progressive corrosion. These metals form tough and well-integrated oxide films that exclude or slow further corrosion by acting as an ion barrier membrane.
Titanium anodizing is the oxidation of titanium to alter the surface properties of produced parts, including improved wear properties and enhanced cosmetic appearance. This article will further discuss titanium anodizing, its purpose, uses, how it works, limitations, benefits, and important properties.
What Is Titanium Anodizing?
Titanium anodizing is the deliberate electrolytic oxidation of the surface of titanium (or titanium alloy) components to produce surface properties suited to the application for which the part is being made. The electrolytic chemistries differ between aluminum and titanium anodizing, and also between titanium anodizing types 1, 2, and 3.
What Is the Purpose of Titanium Anodizing?
Titanium anodizing can provide a variety of useful properties that enhance the characteristics of components for a wide spectrum of applications. Type-2 anodizing makes titanium’s surface harder and provides improved corrosion and abrasion resistance. These enhanced properties make it widely used in the manufacture of aerospace components. It results in a matte gray surface that can tolerate more abrasion than the metal in its naturally oxidized condition. Type-4 anodizing—which is Type 2 with the addition of surface impregnation with PTFE (Teflon™) compounds integrated into the porous oxide film—adds another enhanced property which is a self-lubricating surface. Type-3 anodizing, on the other hand, apply a thin film of color to the material. This property is generally a cosmetic treatment, and it makes resilient “false” color films, exploiting the “oil on water” color effect. This cosmetic treatment can have great technical value in differentiating parts to ease assembly. It is also commonly used on surgical implant components to differentiate left- and right-hand versions to aid surgeons in selecting components.
Where Is Anodized Titanium Used?
Titanium is used most effectively where the combination of toughness, fatigue resistance, and lightweight is necessary—and in particular applications where enhanced corrosion resistance and/or high-temperature performance are of significant benefit. The anodizing of titanium parts can render them virtually chemically inert, and add color without dyes. Anodized titanium is widely used in commercial and military jet engine applications, rocket engines, airframe components, and to a limited degree in aircraft skin parts—in particular around jet engine inlets and the leading edges of wings where abrasion resistance is vital. Titanium has a very low susceptibility to chloride ion (salt) induced corrosion and lends this characteristic to a range of alloys. These are increasingly being used in high-value and high-performance boat, ship, and fishing components to provide high strength, low weight, and (particularly) low corrosion performance compared to even the most effective “marine” stainless steels. These applications include: oilfield and subsea components, dive equipment, fishing gear, pumps, and valve parts. Anodized titanium is a material of choice for the widest range of surgical and dental implant parts, combining high strength with low weight, and very low biologically induced corrosion.
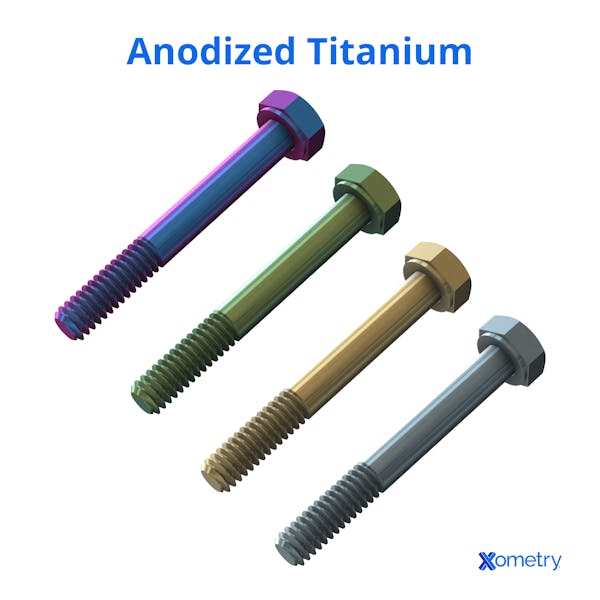
How Does Titanium Anodizing Work?
Anodizing titanium works by building up an enhanced oxide film on the surface parts by a variety of electrochemistry processes, according to whether the part is receiving Type 1, 2, or 3 anodization. This coating can be a “thin film” that lends false color to the part; Type 3 typically creates this effect. A shade from gold to green results from the application of 200 to 1700 Å transparent film thickness. Type-2 anodizing produces tougher, thicker coatings that typically improve wear properties. Type-4 anodizing creates a self-lubricating film that impregnates the surface oxide film with PTFE. Type-1 anodizing, on the other hand, can be a semiconducting oxide layer that is used before extrusion and for some radiative or absorptive properties for thermal control. Titanium naturally develops a protective oxide film—rapidly growing to a very thin 12 Å over a period of hours, then slowly developing to 500 Å over 5+ years.
What Are the Benefits of Titanium Anodizing?
There are several benefits of titanium anodizing, including:
- Reduced risk of galling by providing reduced friction and increased hardness, where the parts are abraded.
- Improved corrosion resistance from anodized (passivated) surfaces.
- Biocompatibility, making low-corrosion and zero-contaminant surfaces.
- Low cost, durable color.
- High cosmetic quality and a wide spectrum of colors.
- Electrically passive and low-corrosion surface.
- Biocompatible component identification, as there are no dyes or colorants used.
What Are the Limitations of Titanium Anodizing?
The limitations of titanium anodizing are:
- Precise color control is hard to achieve and hard to maintain, as there are many factors in the electrochemical process. Color anodizing is a difficult process that requires tight controls.
- Electrochemical baths for titanium anodizing are generally harmful and toxic to sulfuric(VI) acid, chromic(VI) acid, or phosphoric(V) acid, so health and safety issues in anodizing plants are a concern.
- Damaged anodization will only recover over a prolonged period of time, where conditions are conducive to oxidation. In a reducing (oxygen-free or oxygen-consuming) environment, titanium will lose its anodization progressively. Although such environments are not corrosive, other issues such as chemical-induced stress corrosion cracking can arise.
- Anodizing titanium is not a guarantee of zero corrosion under all conditions. For example, methanol exposure leads to stress corrosion cracking in high-titanium-percentage alloys, in the absence of oxidizing agents. An example is when the surface moisture content is below 1.5%; embrittlement occurs sometimes, under hot and anhydrous conditions. Other conditions in which stress corrosion cracking occurs are exposure to nitrogen tetroxide, red fuming nitric acid, and either bromine or fluorine gas.
Common FAQs About Titanium Anodizing
How To Anodize Titanium
To achieve a basic level of anodizing of small titanium parts, you simply need to build an electrochemical cell with a DC power source and an appropriate electrolyte. With the circuit connected so that the bath is the cathode and the titanium part is the anode, the current carried through the cell will oxidize the surface of the component. Time in the bath circuit, the applied voltage, and the concentration of (and chemistry of) the electrolyte will alter the resulting color. Precise control is hard to achieve and maintain, but satisfying results can be shown very easily.
What Are the Materials Needed To Anodize Titanium?
The materials needed to anodize titanium are:
- Electrolyte: The electrolyte can be a moderately concentrated sulfuric acid (1 to 2 M is appropriate) or concentrated borax (sodium tetraborate) solution. Many other ionic solutions will work.
- Plastic Tank: The plastic tank should be of suitable size for immersing the part. The tank will be lined with aluminum foil. The tank will be filled with electrolytes and act as the cell, bringing all other elements together.
- DC Power Supply: A DC power supply should be capable of supplying 0 to 30 volts and several amps of current. This will drive the anodization process.
- Wires: The wires will be used to connect the aluminum foil to the negative of the power supply (the cathode) and the titanium part to the positive of the power supply (the anode).
How Long Will Anodized Titanium Last?
The anodized surface of a piece of titanium will remain stable for years, if undisturbed by abrasion or the limited chemical attacks to which titanium is susceptible. Titanium is so resistant to corrosion that it even fails to obey the norms of galvanic corrosion.
How Long Does It Take To Anodize Titanium?
The color anodizing process will show rapid results, generally in a few seconds if the electrolyte is moderately high concentration and the power supply can deliver sufficient current. For thicker, mechanical (Type-2) films, the development of the oxide film can take several hours. This process is substituting for the natural development of titanium oxide films which occurs in wet environments over 3 to 5 years.
Is Anodized Titanium Prone to Rust?
No, anodized titanium is not prone to rust. Very little can affect anodized titanium, when a well-integrated and tough oxide film has been formed. Titanium does not corrode rapidly other than under exceptional and very aggressive conditions.
Is the Anodizing of Titanium Permanent?
No, anodizing of titanium is not permanent. Anodized titanium oxide films can be removed by abrasion, so hard-working parts can lose some of their anodized coatings. To fully remove anodization from titanium requires concentrated nitric acid containing some traces of hydrofluoric acid, accelerated by heating. This is not a common condition, however. Otherwise, titanium anodizing is very robust. Components anodized 50 years ago are known to be in close to original condition.
How Xometry Can Help
Xometry provides a wide range of manufacturing capabilities and other value-added services for all of your prototyping and production needs. Visit our website to learn more or to request a free titanium CNC machining quote.
Copyright and Trademark Notice
- *Teflon™ is a trademark of The Chemours Company FC, LLC
Disclaimer
The content appearing on this webpage is for informational purposes only. Xometry makes no representation or warranty of any kind, be it expressed or implied, as to the accuracy, completeness, or validity of the information. Any performance parameters, geometric tolerances, specific design features, quality and types of materials, or processes should not be inferred to represent what will be delivered by third-party suppliers or manufacturers through Xometry’s network. Buyers seeking quotes for parts are responsible for defining the specific requirements for those parts. Please refer to our terms and conditions for more information.
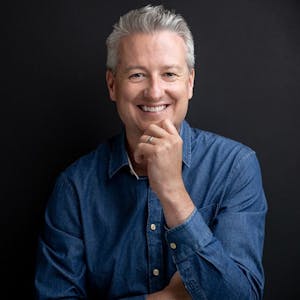