Titanium is a strong and hard-wearing metal with wide applications. Aside from this, titanium can be anodized to take on vibrant colors that won’t fade. This process, called Type III titanium anodizing, is capable of imparting a variety of monochromatic finishes to the titanium, ranging from bronze to blue, and even magenta and green.
Further, this anodization improves certain properties of the titanium, such as its corrosion resistance and biocompatibility. This article will discuss titanium anodizing colors, their importance, the types of anodization processes and components, as well as provide tips to get the best results.
What Is Anodized Titanium?
Anodized titanium is titanium (including some titanium alloys) that has had its surface converted to titanium oxide by an electrochemical reaction called anodization. This titanium oxide surface has a specific depth that has been controlled by the parameters of the electrochemical reaction, such as the applied voltage. Titanium anodization can be carried out in different ways with different effects. For example, Type II anodization increases wear resistance, while Type III anodization gives vibrant colors.
Available Colors for Anodized Titanium
The available colors for anodized titanium are bronze, blue, yellow, magenta (pink/purple), cyan (teal), and green. The color of the anodized titanium depends on the thickness of the oxidized layer created on the surface of the titanium. Therefore, a range of colors is possible depending on the exact thickness of the oxidized layer created.
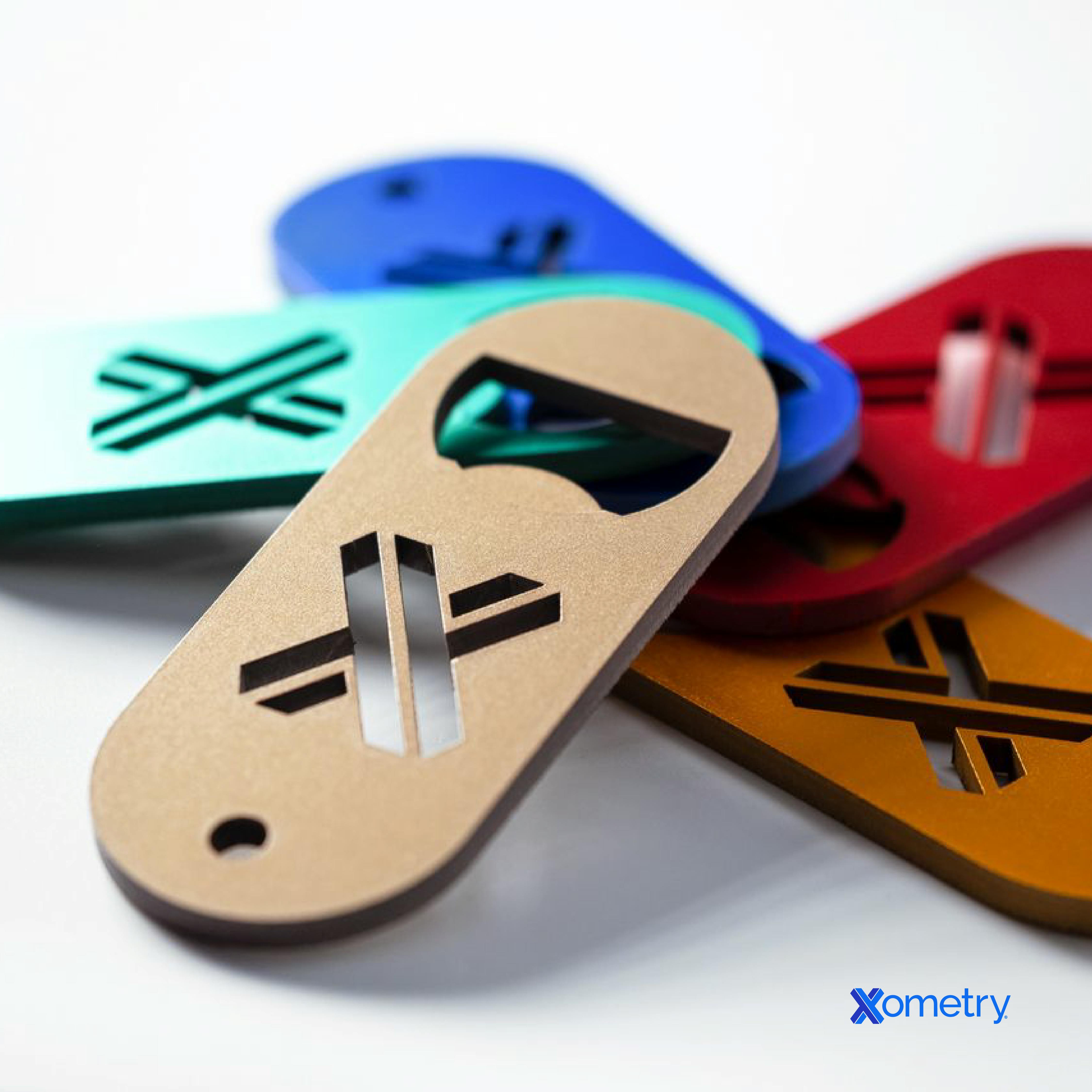
Types of Anodization Processes for Titanium
Anodizing of titanium can be carried out according to three broad types. Each type of anodizing is similar, but with different chemistry, and produces quite different results:
1. Type I
Type I titanium anodizing is a specialized process with limited application. It is a high-temperature electrolytic oxidation process applied to titanium.
2. Type II
Type II anodization gives a gray color to the surface of the titanium. It enhances its mechanical properties like lubricity (low friction) and wear resistance. Type II anodization of titanium is carried out electrochemically. The titanium is placed in an electrolyte solution and a voltage is applied. This voltage is set to maintain a certain current density, and the oxide film that is formed penetrates the titanium base metal. Therefore, the overall dimensions of the titanium component are unchanged after anodizing.
3. Type III
Type III anodization of titanium gives a colored appearance. It is the most visually distinctive anodizing process as a wide range of colors can be created, from bronze to blue to green. The process of anodizing uses an electrochemical cell to create an oxide layer on the surface of the titanium article, which interferes with the reflection and refraction of light off the surface.
Coloring Process of Type III Anodized Titanium
There are a number of steps to be followed in the coloring process of type III titanium anodizing. These steps are:
- Clean the titanium part to be anodized. The alkaline clean specifically removes organic residue such as oils from fingerprints. These organic residues would otherwise interfere with the anodizing process.
- Rinse the alkaline cleaner off the titanium article. It is important to see the water running off the titanium in sheets, rather than in beads. If the water beads, it shows that there is still some residual oil on the surface (oil is hydrophobic, causing the water to bead).
- Hot rinse the part. A hot rinse allows the water to evaporate after the rinse so that minimal water is introduced at the next step.
- Prepare the surface with an acid clean for the best results in color anodizing. The purpose of this preparation step is to remove the residual oxide film that would have formed over time with exposure to air. If this oxide film is stripped off, exposing the base metal, it provides the best starting point for the controlled anodization to give a uniform color.
- Remove the excess acid with a cold water rinse.
- An alkaline solution can be used to neutralize any residual acid.
- Rinse off the alkaline solution.
- The anodizing process can now be carried out. Submerge the titanium component in an electrolytic solution (such as trisodium phosphate) and apply an appropriate voltage. The electrochemical reaction takes place to form the oxide film of a specific thickness on the surface of the titanium.
- After the titanium component is removed from the electrolyte solution, rinse off any remaining solution from the component.
- Execute a final hot rinse. A final hot rinse ensures that no residual solution is left, and the rinse water will evaporate to leave a dry, colored piece of anodized titanium.
Getting the Best Results With Color Titanium Anodizing
There are two key aspects to getting the best results with color titanium anodizing. The first is the surface finish of the titanium article to be anodized. This will depend on the manufacturing process of the component, particularly if it was machined. It may be necessary to polish the item beforehand to achieve a smooth and consistent finish over the whole surface. If the machining process leaves a rough surface, or areas with a work-hardened or smeared finish, this will affect the electrical current flow through the titanium part. This results in an uneven film thickness and uneven color.
The second important aspect that should be considered carefully is the surface preparation of the titanium part before anodizing. The preparation essentially removes a thin layer of material to expose the base metal before anodizing. This preparation needs to be completed to give consistent results. Further, the anodization should happen immediately after the preparation is complete. If the titanium part is left exposed to air for some time (a number of hours), the base metal will naturally begin to react with oxygen in the air. This will interfere with the anodizing process and result in a splotchy color. Also, if any contaminants are deposited on the surface after preparation (even fingerprints), these will also result in uneven coloration.
How to Recover From Mistakes in Color Titanium Anodizing
To recover from mistakes while anodizing titanium for color (Type III), simply remove the oxide layer and start the process again with a fresh metal surface. Mistakes that may occur include arriving at the wrong color (by making the oxide film too thick) or getting a splotchy, uneven color (by not cleaning and preparing the surface correctly before anodizing).
A strong acid, usually hydrochloric acid, will remove the oxide layer. This is commonly an ingredient in household rust removers or oven cleaners. Another method for removing the oxide layer is by abrasion, using sandpaper to remove it mechanically.
Equipment Used for Anodizing Titanium
The equipment used for anodizing titanium is essentially the equipment needed for an electrochemical reaction. It includes a bath (or tank) to hold the electrolytic solution, an electrode as the cathode, a conductive rack for holding the titanium parts that will function as the anodes, and a power supply. Other tanks or baths are necessary for the surface cleaning and preparation before anodizing, and for the rinse afterwards. All these items of equipment can be combined efficiently in purpose-built titanium anodizing machines.
Why Anodized Titanium Changes Color
Anodized titanium changes color due to the way the oxide layer on the titanium surface interferes with the reflection and refraction of light off the surface. If white light (sunlight—made up of its well-known spectrum of colors) shines onto anodized titanium, the oxide layer reflects a portion of that light, and also allows some light to pass through (refraction). This light is then reflected by the base metal underneath the oxide layer. This portion of light is then displaced from that which was reflected off the oxide layer by a distance that depends on the thickness of the layer. The two beams of light interact with each other, and the wavelengths of the various colors of light interact with each other. Depending on the distance of the displacement of the refracted light, some color wavelengths “cancel” each other, while other color wavelengths constructively amplify each other. This effect filters out some colors while enhancing others. The colors that are filtered or enhanced depend on the thickness of the oxide layer, as this determines the distance that the refracted light is shifted as it passes through the layer.
Xometry provides a wide range of manufacturing capabilities including CNC machining, 3D printing, injection molding, laser cutting, and sheet metal fabrication. Get your instant quote today.
Disclaimer
The content appearing on this webpage is for informational purposes only. Xometry makes no representation or warranty of any kind, be it expressed or implied, as to the accuracy, completeness, or validity of the information. Any performance parameters, geometric tolerances, specific design features, quality and types of materials, or processes should not be inferred to represent what will be delivered by third-party suppliers or manufacturers through Xometry’s network. Buyers seeking quotes for parts are responsible for defining the specific requirements for those parts. Please refer to our terms and conditions for more information.
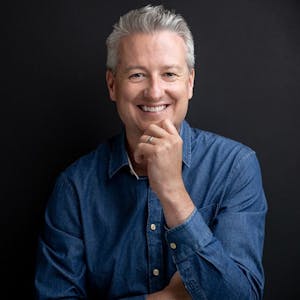