What is a CNC machine? A CNC machine is a programmable machine that can autonomously performing the operations of CNC machining. CNC stands for ‘computer numerical control’, and the CNC machining definition is a subtractive manufacturing process that typically employs computerized controls and machine tools to remove layers of material from a stock piece—known as the blank or workpiece—and produces a custom-designed part. This article explains what the different types of CNC machines are and how they work.
2. CNC 3D Printer
A 3D printer, or an additive manufacturing machine, is a CNC machine in which elements are printed layer-by-layer. The CAD and CAM process creates the product’s design and drawing. Then the 3D printer is used to reflect that design. The 3D printer CNC machine is often used for prototyping. For more information, see our guide on 3D printing.
3. CNC Router
A CNC router is similar to a CNC mill but is generally used for machining softer materials and is typically less precise than CNC Mills. CNC routers are characterized by their ability to use computer numerical control to route spindle and machine tool paths to design and shape materials like wood, steel, foam, composites, aluminum, and plastic.
CNC routers normally consist of stepper motors, stepper drivers, a mechanical base, a spindle, controllers, and a power supply. CNC routers reduce waste, increase productivity and accuracy, and produce products faster.
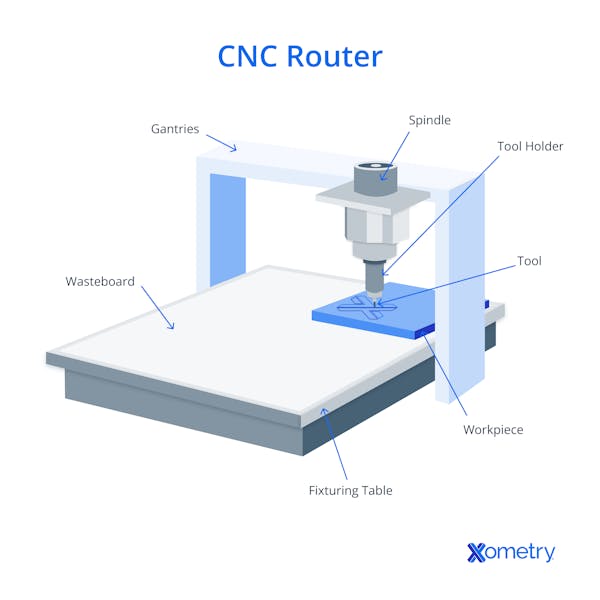
4. CNC Drilling Machine
Drilling employs rotating drill bits to produce the cylindrical holes in the workpiece. The drill bit’s design allows the waste metal—i.e., chips—to fall away from the workpiece. There are several types of drill bits, each of which is used for a specific application. Types of drill bits available include spotting drills, peck drills, screw machine drills, and chucking reamers.
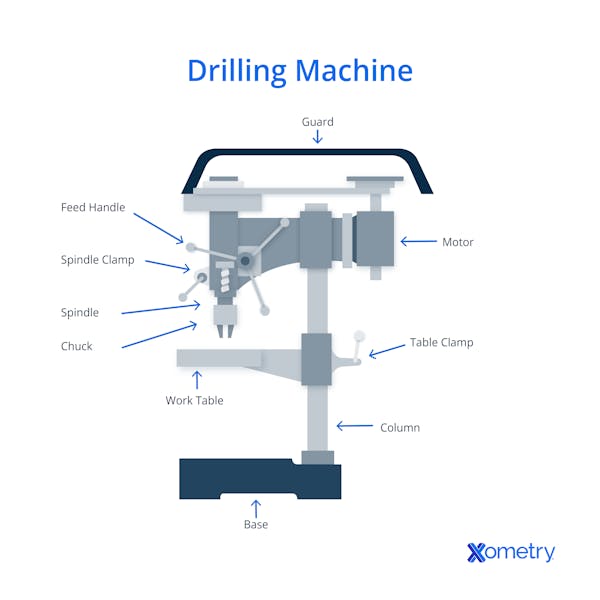
5. CNC Lathe Machine
Turning employs single-point cutting tools to remove material from the rotating workpiece. The design of the turning tool varies based on the particular application, with tools available for roughing, finishing, facing, threading, forming, undercutting, parting, and grooving applications.
The CNC turning process also utilizes CNC-enabled lathes or turning machines. The types of CNC lathes include turret lathes, engine lathes, and special-purpose lathes.
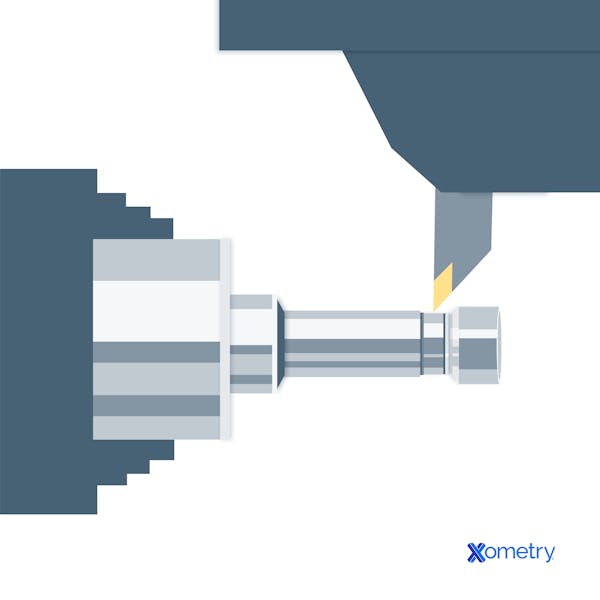
6. 5-Axis CNC Machine
A 5-axis CNC machine adds to the traditional machine tool’s 3-axis linear motions (X, Y, Z) two rotational axes to provide the machine tool access to five out of six part sides in a single operation. By adding a tilting, rotating work holding fixture (or trunnion) to the work table, the mill becomes what is called a 3+2, or an indexed or positional, machine, enabling the milling cutter to approach five out of six sides of a prismatic workpiece at 90° without an operator having to reset the workpiece to machine different sides. A 5-acis CNC machine is often used to make sculptures.
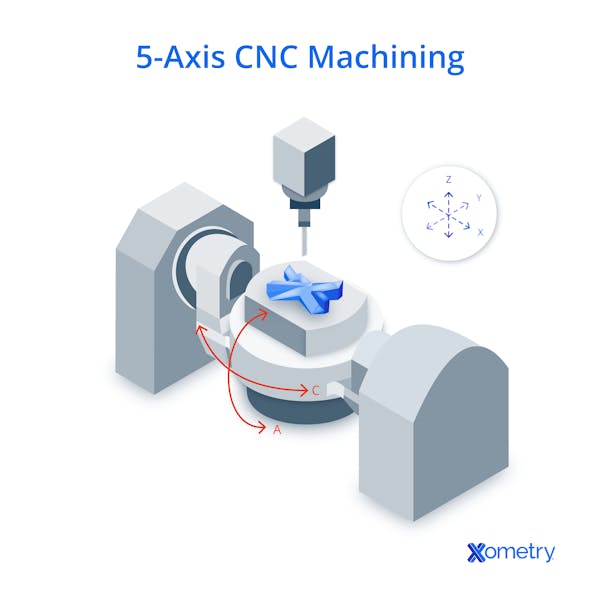
7. CNC Milling Machine
Milling employs rotating multi-point cutting tools to shape the workpiece. Milling tools are either horizontally or vertically oriented, including end mills, helical mills, and chamfer mills.
The CNC milling process also utilizes CNC-enabled milling machinery, referred to as mill machines or mills, which can be horizontally or vertically oriented. Basic mills can have three-axis movements, with more advanced models accommodating additional axes. The types of mills available include hand, plain, universal, and omniversal milling machines.
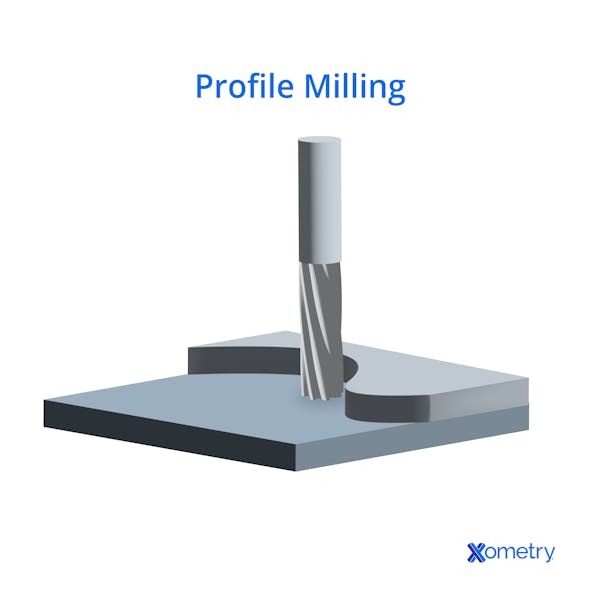
8. CNC Plasma Cutting Machine
Plasma cutting CNC machines cut materials. They use a plasma torch to cut through their materials. The main condition for CNC plasma cutting machines is that the material or workpiece to be cut must be electrically conductive. Some of the typical materials used with plasma cutting are brass, copper, aluminum, steel, and stainless steel.
A CNC plasma cutting machine has a high-powered torch that can cut through even the toughest materials, like titanium and steel. In a CNC plasma cutting machine, the high-powered torch is created by passing high-velocity gas through a nozzle.
When the torch is created, an electric arc is produced. The arc forms through the high-velocity gas and jumps onto the material being cut, changing some of the high-velocity gas into plasma, electronically ionized gas.
9. CNC Laser Cutting Machine
Several types of laser cutting machines are available, categorized into gas, liquid, and solid-state lasers. The types are differentiated based on the state of the active laser medium—i.e., whether the medium is a gas, liquid, or solid material—and what the active laser medium consists of (e.g., CO2, Nd:YAG, etc.). The main two types of lasers employed are CO2 and solid-state lasers.
One of the most commonly employed gas state lasers, a CO2 laser uses a carbon dioxide mixture as the active laser medium. CO2 lasers typically cut non-metal materials since the early machine models were not powerful enough to cut through metals. Laser technology has since progressed enough that CO2 lasers can cut through metals. However, CO2 lasers are still better suited for cutting through non-metals and organic materials and simply engraving metals or other hard materials. Pure nitrogen lasers are another commonly used gas state laser. These lasers are used for applications that require the material not to oxidize as it is cut.
10. Electric Discharge CNC Machine
Electric discharge CNC machines are also known as spark CNC machines. They are a special type of CNC machine that uses electric sparks to manage materials to the desired shape.
Electrical discharge has a transient effect, meaning it can degrade the elements from which it is presented. The electric discharge CNC machines take advantage of this by designing controlled sparks to reshape materials. The workpieces are placed between the top and bottom of the electrode. The computer then decides the amount of electrical discharge the electrodes produce.
11. CNC Grinding Machine
A grinding CNC machine is a precision performance tool that uses a rotating wheel to cut metal away from the metal. CNC grinding machines are typically used for camshafts, ball bearings, transmission shafts, and other working pieces, which require an accurate and correct finish. Numerous pieces made using a CNC grinding machine are cylindrical.
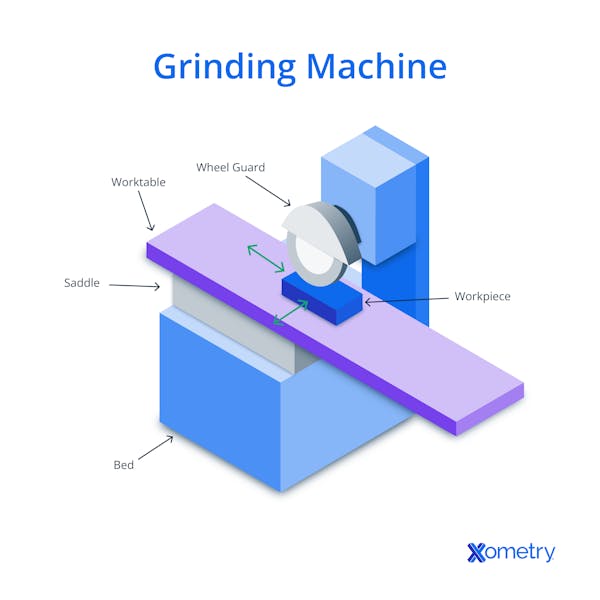
12. CNC Machine with Automatic Tool Changes
The automatic tool changer CNC machine develops the machine’s tool carrying capacity and production rate and improves the machine’s capacity to work with many tools. This type of CNC machine changes tools very quickly and efficiently handles and changes worn out or broken tools.
This CNC machine reduces non-productive time during the machining process. A CNC machine with automatic tool changes is an ideal step toward complete automation.
How to Select the Best CNC Machine Type
The best CNC machine type is selected by knowing what CNC process you want to use and what materials you are working with. Some key considerations are the machine’s weight, the work radius, the machine’s speed, the availability of spare parts, and power consumption.
The common materials used in constructing CNC machines are aluminum, polymer composite, and iron cast. The iron cast is the best build when you need a durable machine for tough jobs. Other materials are suitable for lighter tasks.
Your CNC machine should be larger than the maximum area for your products. Your machine must have a radius bigger than the largest material you cut. It would help if you considered the feed rate when selecting the best CNC machine type. It determines the rate you can cut materials during the manufacturing processes.
Like any other appliance, a CNC machine may break down or wear down with use. You should ensure that your technicians can easily repair the brand that you purchase and that the spare parts are available. This will reduce machine downtime.
Depending on the machine you choose, you may need to increase the power available in the workshop. Checking the power requirements of your machine and making the necessary adjustments at the workplace is essential.
Summary
Xometry provides a wide range of manufacturing capabilities including custom machining solutions, 3D printing, injection molding, laser cutting, and sheet metal fabrication. Get your instant quote today.
Disclaimer
The content appearing on this webpage is for informational purposes only. Xometry makes no representation or warranty of any kind, be it expressed or implied, as to the accuracy, completeness, or validity of the information. Any performance parameters, geometric tolerances, specific design features, quality and types of materials, or processes should not be inferred to represent what will be delivered by third-party suppliers or manufacturers through Xometry’s network. Buyers seeking quotes for parts are responsible for defining the specific requirements for those parts. Please refer to our terms and conditions for more information.
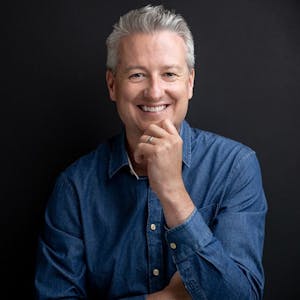