Reamer is the family name for the highest-precision tools in wide use. They allow basic machines and even hand work to produce holes within a tolerance of 0.0002 inches. This precision is achieved via a grinding process, using a reamer cutting tool to remove material and expand the hole by no more than 10% – generally less. The purpose of requiring such accuracy is to create precise fits. The ‘hole basis’ tolerance system (H7/g6 for example) used in specifying this precision allows shaft sizes to be adjusted for various purposes. From ‘free running fits’ for approximate fit/location to ‘close clearance’ for sliding and bearing pairs to ‘force fit’ to allow drive shafts to be immovably fitted to heated pulleys (for example), many assemblies need this tight precision.
Reamers come in many styles and are designed for many specific uses. Examples are: hand reamers, adjustable reamers, and machine reamers of many specialist types. Each with various shanks, flute shapes and numbers, tip types, and more. Accuracy can degrade over time due to various causes such as: machine precision, reamer wear, chipping, and excess feed speed or revolution speed.
This article will discuss the 14 types of reamer tools used in machining, their specific purposes, and how to use them.
1. Carbide Reamers
Carbide materials (Tungsten-carbide, Titanium-carbide, and Tantalum-carbide) are among the hardest materials that can be manufactured at scale. Reaming tools are also the main application for cermets, the family of materials that combine metals and ceramics. Carbide reamers are unfortunately very brittle, so they must be mounted and used with great care to avoid cracking and chipping. Carbide tips can be mounted on reamer tools made of cermet or tooling/high-speed steels (HSS). Alternatively, the whole cutter may be made from one piece of carbide. This design is contingent upon the size of the reamer. Brazed tips are fitted to large-diameter reamers, whereas small devices are ground from whole carbide shafts.
2. Taper Pin Reamers
Taper pin reamers have tapered flutes (cutting faces) to allow the precision fitting of tapered pins. These cutters can have straight flutes, slightly twisted (spiral) flutes, or heavily twisted (helical) flutes. They are categorized based on their tip diameter, root diameter, and length rather than a nominal diameter and angle. Taper pin reamers are supplied with a range of parallel and machine-tapered shanks to fit various collets, chucks, and taper locks. They also commonly have a square top end to the shank, allowing them to fit hand tap wrenches and be used by hand. Taper pin reamers are usually made from HSS steel but are available with carbide tips as well.
3. Hand Reamers
Hand reamers are precision-ground cutting tools used to expand pre-drilled holes to an exact diameter by hand. They generally have straight or slightly twisted flutes and commonly have a slight bevel at the tip and a tapered lead-in. The bevel and taper make the reamer easier to start at a precise angle since the tools don’t benefit from being locked into a fixed machining device. Because reamers are made of hardened, brittle material, they are relatively easy to break, so care and attention must be paid to keep the reamer aligned with the hole’s axis. When reaming by hand, the operator should only remove small amounts of material at a time. The tool is more likely to roll off the proper axis if it bites into too much material, thus losing accuracy and risking tool breakage.
4. Shell Reamers
Shell reamers are specially made for larger holes – commonly ¾” and above. They are separate fluted tips designed to fit onto existing shanks. This feature reduces their cost, as they use less material and require fewer steps to manufacture. Shell reamers can be found in any of the standard flute types: straight, twisted, and helical. Flutes that run counterclockwise are intended for blind holes while clockwise ones are more common.
5. Expandable Reamers
Expandable reamers are just what they sound like; the outer diameter of their fluting can be adjusted to enable an operator to ream a non-standard-sized hole. They can also be valuable to machinists who are capable of sharpening dull reaming blades (though this process demands a high degree of skill). After sharpening, the expandable reamer can be adjusted to meet the proper dimensions again. Expandable reamers operate on the same principle as adjustable reamers except that the expansion cannot be reversed. Once the internal screw has bent the flutes outward, they will not return to their original dimensions.
6. Straight Flute Reamers
Straight-bladed reamers have flutes that do not twist along the length of the shaft. Notably, straight-bladed reamers are not ideal for hand use, as they do not clear chips as well as those with twisted flutes. Split holes such as those which clamp to a shaft or contain a keyway or longitudinal slot cannot be reamed with a straight flute reamer because the blades will ‘fall’ into the slot and lock.
7. Floating Reamers
A floating reamer is an ordinary machine reamer of any type that has been fitted to a floating reamer holder. A floating reamer is a device that carries a collet or chuck on an independent bearing system. The collet allows it to “float” off the axis of the machine drive and follow the path defined by an existing hole. This design innovation removes one source of machine error from the reaming process. The drive can be eccentric from the hole and still achieve a precise result in terms of the hole’s centerline.
9. Chucking Straight Fluted Reamers
Where a jobbing reamer has a square cut end to the shank, a chucking reamer has only a smooth parallel shank with no square tip. It is designed to fit a collet or 3-jaw chuck (hence ‘chucking’). To be a straight fluted chucking reamer, it must also have straight flutes that do not lend themselves to hand-reaming.
10. Helically Fluted Chucking Reamers
Chucking reamers are those whose shanks have a round cross-section intended to be fitted into a collet or 3-jaw chuck (as opposed to a square shank designed for tap wrenches). To be a helically fluted chucking reamer, the flutes must wrap at least partially around the tool’s circumference, generally at more than 30° inclination.
11. Stub Screw-Machine Reamers
This label can be applied to any reamer type if it has a transverse pin hole in the shaft that allows it to be used in a floating reamer holder. This feature is available on most reamer styles, generally without the square tip that denotes their ability to be used as hand reamers.
13. Structural Reamers
These devices are much like other reamers, except that they generally have morse taper shanks and larger diameters. They’re commonly used to ream rivets and pin holes in large structural assemblies such as ships and bridges. Structural reamers have become less common as riveting has fallen out of favor.
14. Helical (Spiral)—Flute Reamers
Helical flute reamers are those in which the spiral angle of the flute itself is pronounced. They are best used on hard and work-hardening materials with Brinell hardness ratings of 200-400, such as stainless steel and abrasion-resistant steel. Helical reamers have a tendency to score the walls in softer materials, spoiling the hole.
What Is a Reamer Tool?
Reamer tools are radially symmetrical tools with either straight, slightly twisted, or spiral fluted cutting surfaces that are ground to a very precise diameter. They are used to finish holes that have been drilled, end-milled, or punched, leaving them with very accurate dimensions. Reamer tools are only intended to remove small amounts of material and correct holes that are imperfectly rounded or not quite straight.
What Is the Purpose of a Reamer Tool?
The purpose of a reamer tool is to produce smooth and precisely round holes of very high diametral accuracy. They cannot create a hole where there is none; reamers can only expand an existing hole by up to 10%.
How Does a Reamer Tool Work?
Reamers possess at least three precision-ground blades along their shank. They work by rotating within an existing hole so the blades can scrape material from the wall, increasing its diameter and smoothing out the surface. Reamed holes can be used for the following:
- Precisely fitting locating pins (dowels).
- Running fits of components such as bushes opened up to fit precision-ground shafts.
- The precise fit of bearing parts into a machine.
- Hot coupling of a shaft to gear, making an immovable pairing.
There are numerous online guides that give advice about how to use reamer tools.
Feeds and Speeds
Cutter revolutions and plunge feed speeds are highly dependent on a range of factors. Among them are: the material being cut, the reamer material, required precision, and thermal expansion. As a rule, a good quality machine with low feed speeds, low revolutions per minute, and lots of cooling will give the best results. But when productivity is a concern, it’s a good idea to refer to the reamer manufacturer's feed/RPM guidance for the material being cut. Hand reaming is a special case because cut speeds, feed rates, and eccentric forces are hard to control. A practiced hand, however, can achieve the highest tolerances with a good quality tool.
Summary
This article presented the different types of reamer tools, explained what they are, and discussed when to use each one. To learn more about reamer tools, contact a Xometry representative.
Xometry provides a wide range of manufacturing capabilities, including CNC machining and other value-added services for all of your prototyping and production needs. Visit our website to learn more or to request a free, no-obligation quote.
Disclaimer
The content appearing on this webpage is for informational purposes only. Xometry makes no representation or warranty of any kind, be it expressed or implied, as to the accuracy, completeness, or validity of the information. Any performance parameters, geometric tolerances, specific design features, quality and types of materials, or processes should not be inferred to represent what will be delivered by third-party suppliers or manufacturers through Xometry’s network. Buyers seeking quotes for parts are responsible for defining the specific requirements for those parts. Please refer to our terms and conditions for more information.
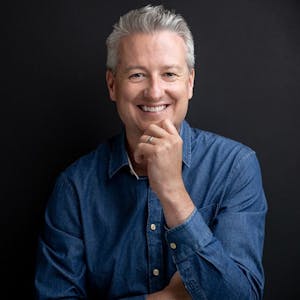