There are several types of turning operations used to create sophisticated custom parts. They can manufacture durable products such as musical instruments, table legs, gun barrels, screws, and cue sticks. However, each step of these manufacturing processes follows different procedures to meet design specifications. One machine that is capable of performing many different operations is the lathe machine.
A lathe is an all-in-one manufacturing device with the capability of performing different turning operations. Turning operations remove unneeded material from a workpiece as it rotates along an axis. There are different types of turning operations, including threading, boring, facing, turning, drilling, and tapping. The time taken to perform a turning or machining operation is given by the formula below:
Time taken = Length of cut (mm) / feed (mm per revolution) × revolutions per minute
This article will discuss the 10 types of turning operations, its definition, and how it works.
1. Threading
Threading is a lathe machining or turning operation that incorporates a mechanical tool that cuts threads on the outer surface of a workpiece. The tool does this motion by moving along the side of the workpiece. Threads—the result of the operation—are helical grooves with pitches and lengths that have been specified. To get deeper threads, the tool needs to pass multiple times along the side of the workpiece. The tool used to perform this action is a thread-shaped cutting tool bit. To get the job done accordingly, the machine must be properly set. In the event that multiple passes of the tool are needed to cut deeper threads, the machine must be set so that the helix begins at the same location.
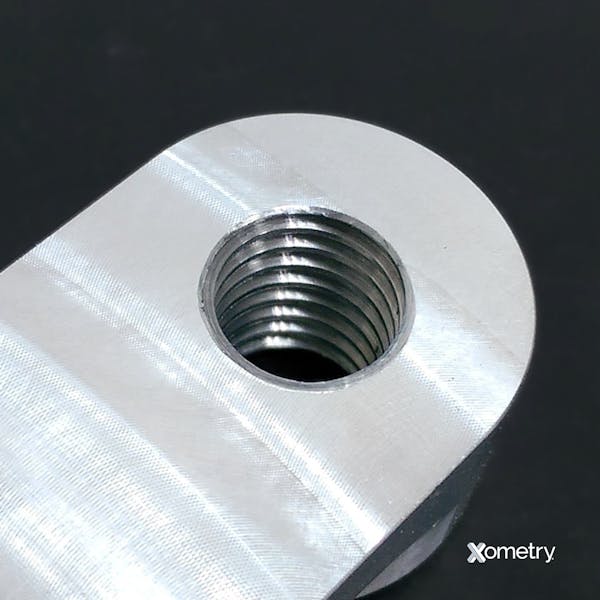
2. Boring
Boring is the process of removing excess material from a hole in a workpiece. The tool used is a single-point cutting tool. It enters the workpiece axially to create specified shapes and makes an existing hole deeper or bigger. However, it is necessary to know that this operation cannot create a hole. Boring comes in handy only when a hole has already been drilled. The procedure is slow and applicable to small-sized works. Moreover, it can be used to correct a hole that is not perfectly round.
3. Tapping
Tapping is a machining operation that employs a tapping tool to create threads as it enters axially through an existing hole of a workpiece. The bit size which is accommodated by the tapping tool is determined by the size of the hole. The instrument used to perform the operation is called a tap, and it is a multipoint cutting tool. The workpiece is placed on a faceplate and made to rotate at a slow speed. While a special fixture is used to support the tap as it is placed on a tailstock spindle.
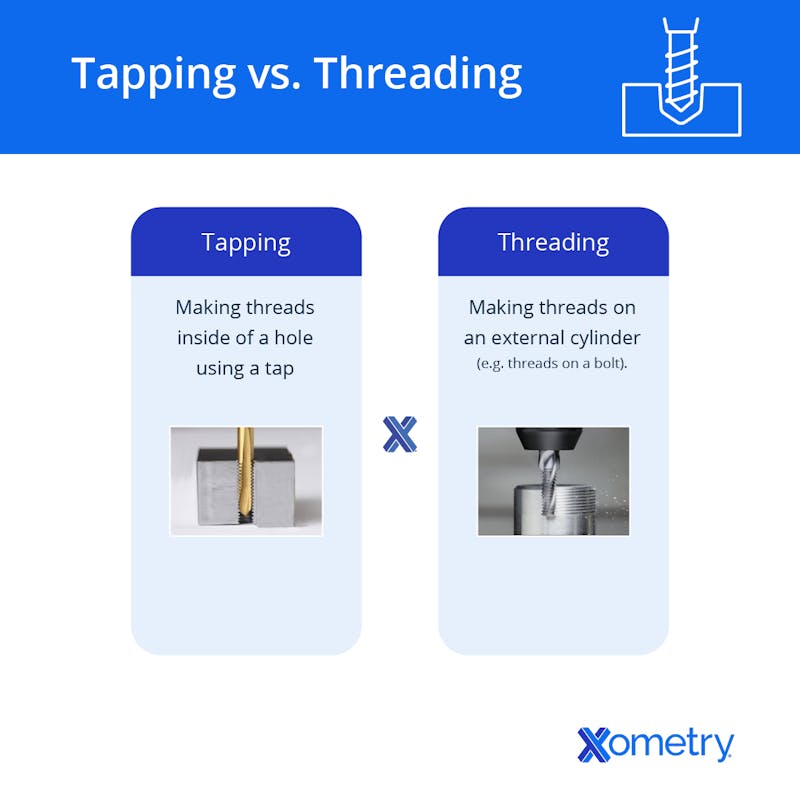
4. Knurling
The purpose of knurling is to create serrated or diamond-shaped patterns on the surface of a workpiece or part. Knurling helps to facilitate the easy gripping of the machined part and also makes it aesthetically pleasing. The tool used to perform this operation is called a knurl. To achieve these patterns, the knurl (or knurls) are brought into contact with the workpiece surface and the (tool) teeth are made to roll against it.
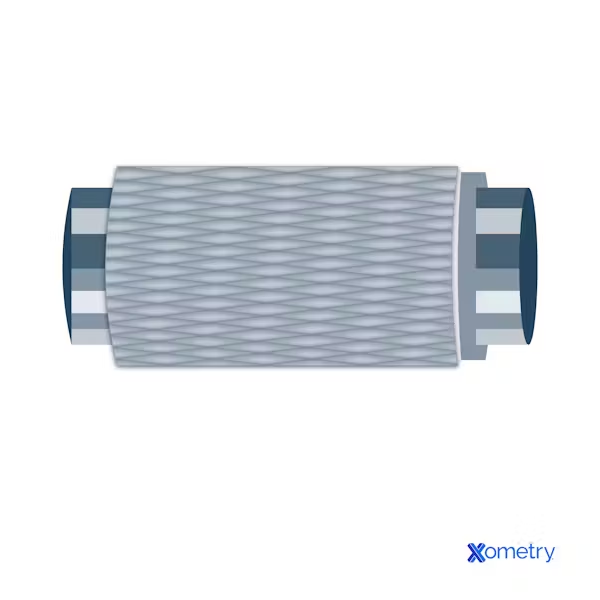
5. Drilling
The purpose of drilling as a machining operation is to create a hole in a workpiece by removing unneeded materials from it as it rotates. The diameter of the hole will be equal to the size of the drill bit which is used to perform the operation. For a drill bit to be well optimized, it should be properly positioned. Proper positioning is done with a lathe tool holder or tailstock drill holder as the workpiece rotates in a faceplate or chuck.
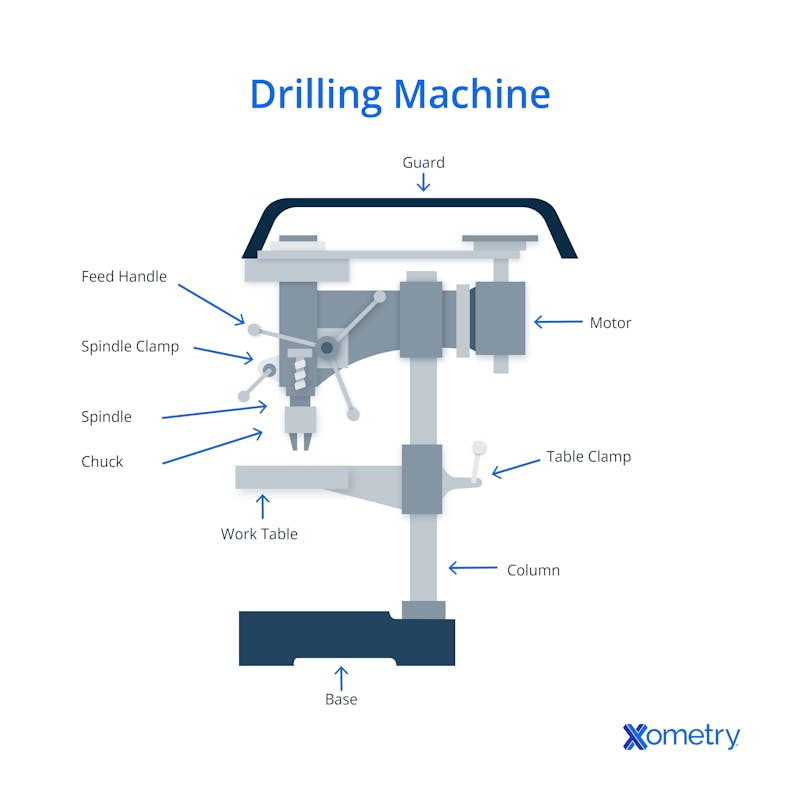
6. Reaming
The reaming operation is used for the enlargement of a hole in the workpiece. Essentially, reaming is a sizing operation. The reamer or reaming tool penetrates axially through the workpiece and enlarges an existing hole to the diameter of the reamer. The reamer comes after the drilling operation has been concluded. It removes only a small amount of material and produces a rounder hole with a smoother internal finish compared to the drill. The reamer is held in place on a tailstock spindle while the workpiece rotates at a very slow speed.
7. Parting
Parting is a turning operation utilized in cutting a workpiece only after it has properly been machined to the specified size and shape. It is an operation that leads to the cutting off of a workpiece or part when a machining cycle reaches an end. The tool used makes a progressive cut in the workpiece, passing through the rotating axis perpendicularly as the workpiece rotates. As the process goes on, the cutting tool gets to the center of the workpiece, a part of which then detaches and drops off.
8. Facing
Facing is a machining operation that reduces the workpiece length. It solves a problem that arises during a machining operation—when the workpiece length is slightly longer than it is expected to be. Facing machines the workpiece length to the exact size. The workpiece end is perpendicular to the axis of rotation. To produce the expected part length, the cutting tool moves along the workpiece radius.
9. Grooving
Grooving, sometimes called necking or processing, is the process of creating a narrow cut in the workpiece. However, the size of the cut is determined by the width of the cutting tool used. If wider grooves are required, the tool has to move along the same path on the workpiece multiple times. When it comes to grooving operations, two types exist: face and external grooving. In the face grooving, the tool creates a narrow cut on the workpiece face. On the other hand, external grooving removes materials by moving radially into the workpiece side.
Turning Operation in CNC
A turning operation in CNC (Computer Numerical Control) involves a process whereby (typically) bars of materials are held in a chuck and rotated. Excess materials are removed using a cutting tool until the final and desired shape is created. It is a subtractive manufacturing process since the desired item is created by the controlled continuous removal of material from the workpiece. CNC turning operations take place at a relatively fast speed. This speed makes the process relevant in the production of high volumes of parts. For more information, see our guide on CNC machining.
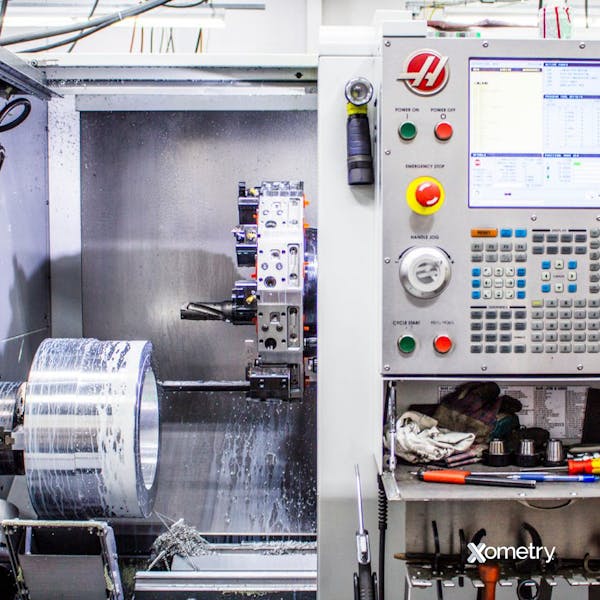
How Xometry Can Help
Xometry provides a wide range of manufacturing capabilities including CNC machining, 3D printing, injection molding, laser cutting, and sheet metal fabrication. Get your instant quote today.
Disclaimer
The content appearing on this webpage is for informational purposes only. Xometry makes no representation or warranty of any kind, be it expressed or implied, as to the accuracy, completeness, or validity of the information. Any performance parameters, geometric tolerances, specific design features, quality and types of materials, or processes should not be inferred to represent what will be delivered by third-party suppliers or manufacturers through Xometry’s network. Buyers seeking quotes for parts are responsible for defining the specific requirements for those parts. Please refer to our terms and conditions for more information.
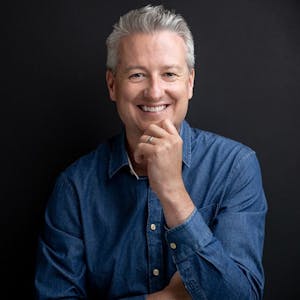