Turning is a machining process where a lathe is used to rotate the metal while a cutting tool moves in a linear motion to remove metal along the diameter, creating a cylindrical shape. The cutting tool can be angled differently to create different forms. It can be done manually or with a CNC turning machine. CNC machining is generally used when part measurements must be very exact.
Turning can be done manually with a lathe, which frequently requires continuous supervision by the operator, or by an automated lathe that does not. Today the most common type of such automation is computer numerical control, or CNC.
When turning, the workpiece (a piece of a relatively rigid material such as wood) is rotated, and a cutting tool is moved along one, two, or even three axes of motion to produce precise diameters and depths. Turning can be on the outside of the cylinder to have tubular components to various geometries.
A component subject to turning operations can be called a "turned part" or a "machined component". For more information, see our article on the Types of Machining Processes.
Tools Used in the Turning Process
The tools used in the turning process include single-point cutting tools to remove material from the rotating workpiece and a lathe or turning machine. The design of the turning tool varies based on the particular application.
The CNC turning process also uses CNC-enabled lathes or turning machines. The types of lathes used for turning include turret lathes, engine lathes, and special-purpose lathes. Lathes can be manual or CNC.
Materials Used for the Turning Process
The materials used for the turning process are mainly metals. These metals include alloy steel, carbon steel, cast iron, stainless steel, aluminum, copper, magnesium, and zinc. However, the process can also machine plastic parts and work with other materials such as ceramics, composites, thermoplastics, and thermosets.
How the Turning Process Works
The turning process works with a lathe machine moving the cutting tool in a linear motion along the surface of the rotating workpiece, removing material around the circumference until the desired diameter is achieved, to machine cylindrical parts with external and internal features, such as slots, tapers, and threads.
Turning uses single-point cutting tools to remove material from the rotating workpiece. The design of the turning tool depends on its application, with tools available for roughing, finishing, facing, threading, parting, forming, undercutting, and grooving applications.
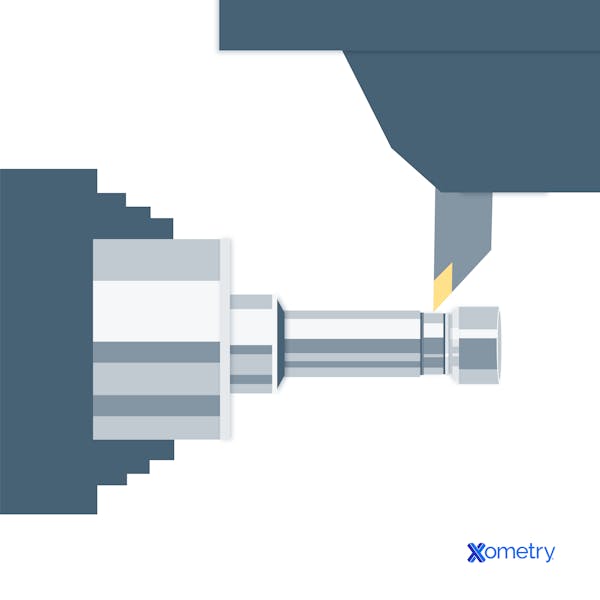
Products Made With Turning
Turning produces rotational, typically axi-symmetric, parts with many features, such as holes, grooves, threads, tapers, various diameter steps, and even contoured surfaces. Products fabricated completely through turning often include components used in limited quantities, especially for prototypes, such as custom-designed shafts and fasteners.
Turning is also often used as a secondary process to add or refine features on parts that were manufactured using a different method.
Some examples of products made with turning are camshafts, crankshafts, baseball bats, bowls, cue sticks, signboards, musical instruments, and table and chair legs.
Types of Turning Processes
Straight turning, also known as cylindrical turning, decreases the work diameter in a uniform motion to prevent variation in the work diameter of the cut. Straight turning is often considered a "roughing" operation that removes large amounts of material before the precision cuts.
Taper turning produces a cylindrical shape that has a gradually decreasing diameter.
Spherical generation occurs when a program creates a form around a fixed axis of revolution or when a specific semicircular tool is used to lower the diameter to zero to make a perfect sphere.
Grooving is done when a shaped tool is pressed into the component gouge to form a narrow cavity.
Parting is used to gouge deeply into the component to remove a completed piece from the original stock piece.
Knurling is done by cutting a serrated pattern into the material. Knurling is usually done with materials that need extra grip.
Threading is done by cutting in a helical path to make grooves that can be screwed into other objects.
Advantages of the Turning Process
The advantages of the turning process are as follows:
1. All Materials Are Interchangeable.
While turning is mainly used to machine metals, any material can be used in turning, including wood and plastic. This makes turning a very flexible process.
2. Tolerance is Excellent.
Turning can be used to create parts with extremely high tolerances. Because of the high tolerances and surface finishes that turning can offer, the process is often used for adding precision rotational features to a part whose basic shape has already been formed through a different method.
3. The Lead Time is Short.
Turning has a short lead time. Lead time is the time between when the customer places an order and when the customer gets the final delivery. Because turning is a fast process, the lead time is short.
4. There is No Need for a Highly Skilled Operator.
Turning does not require a highly skilled operator of the machine. To handle a CNC lathe, a machinist can complete a set amount of coursework and earn certification from an accredited industrial training organization.
5. The Pace of Material Removal is Adjustable.
Another advantage of turning is that the pace of removing material is adjustable. Lathes can operate at different speeds depending on the machined material or the desired end product.
Disadvantages of the Turning Process
The disadvantages of the turning process are as follows:
1. Only Rotatable Components Are Permitted.
Since turning requires the workpiece to be rotated, only rotatable components can be turned. This means that the size of the parts that can be created with turning is limited.
2. Parts May Need Many Procedures and Machines.
Turning may end up being only one process used to create a part. It is often used in conjunction with other procedures, which means more than one machine is required to make the final product.
3. Expensive Equipment.
Turning machines can be expensive, especially if CNC. In addition, turning requires extra fittings and attachments, which increase the cost of the equipment.
4. Tool Wear is Significant.
The repetitive motion of turning means that the cutting tool is subject to significant wear.
5. It Creates a Substantial Amount of Scrap.
As with most machining processes, turning creates scrap metal. The bits of metal produced from turning operations are known as chips in North America, and in some areas, they may be called turnings.
Summary
This article presented turning in machining, explained what it is, and discussed when it is best to use this process in machining. To learn more about turning in machining, contact a Xometry representative.
Xometry provides a wide range of manufacturing capabilities, including CNC machining and other value-added services for all of your prototyping and production needs. Visit our website to learn more or to request a free, no-obligation quote.
Disclaimer
The content appearing on this webpage is for informational purposes only. Xometry makes no representation or warranty of any kind, be it expressed or implied, as to the accuracy, completeness, or validity of the information. Any performance parameters, geometric tolerances, specific design features, quality and types of materials, or processes should not be inferred to represent what will be delivered by third-party suppliers or manufacturers through Xometry’s network. Buyers seeking quotes for parts are responsible for defining the specific requirements for those parts. Please refer to our terms and conditions for more information.
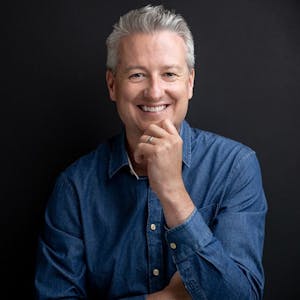