1045 carbon steel is a widely used material known for its strength, durability, and versatility. With a carbon content of roughly 0.45%, it is considered a medium-carbon steel. 1045 carbon steel, which is made up of the elements 98.51-98.98% iron, 0.60-0.90% manganese, and trace amounts of silicon and phosphorus has a lot of uses in many different industries. Gears, bolts, studs, and axles are just a few examples of the components that can be made with it, and that need 1045’s high tensile strength and good machinability.
The manufacturing process for 1045 carbon steel involves carefully melting iron with carbon and other alloying elements, then shaping the metal using rolling or forging techniques. For industries looking for dependable materials for their applications, it is essential to understand the characteristics and applications of 1045 carbon steel. This article will discuss 1045 carbon steel's characteristics, chemical makeup, potential drawbacks, advantages, and more.
1045 Carbon Steel Uses
There are numerous uses for 1045 carbon steel in different industries. It is suitable for manufacturing a variety of components due to its high tensile strength and good machinability. Gears, bolts, studs, axles, crankshafts, and machinery parts are a few examples of common applications for 1045 steel. Furthermore, it is used in products like hydraulic shafts, couplings, and farm machinery that need to be strong and impact resistant. 1045 carbon steel strikes a favorable balance between affordability and impressive properties such as strength, machinability, and wear resistance. This makes it a preferred choice for various applications, including blades, cutting tools, and industrial knives that are exposed to wear and abrasion. 1045 carbon steel’s versatility and reliable performance make it highly sought-after in the manufacturing and engineering industries.
How 1045 Carbon Steel is Made
1045 carbon steel is made using the basic oxygen furnace (BOF) method or the electric arc furnace (EAF) method. It starts with the melting of iron in the presence of controlled amounts of carbon and additional alloying elements such as manganese. The molten metal is then altered to achieve the desired chemical composition. After determining the final composition, the steel is cast into various shapes such as ingots or billets. This casting process for billets is carried out using a continuous casting machine (CCM). The next stage in transforming these forms into the desired products involves methods such as hot rolling or forging.
Chemical Composition of 1045 Carbon Steel
1045 carbon steel contains carbon, manganese, and trace amounts of phosphorus and sulfur in its chemical makeup. An overview of 1045 carbon steel's chemical makeup can be found in Table 1:
Chemical | Percentage |
---|---|
Chemical Carbon | Percentage 0.45% |
Chemical Manganese | Percentage 0.60-0.90% |
Chemical Phosphorus | Percentage <= 0.040 % |
Chemical Sulfur | Percentage <= 0.050 % |
Chemical Iron | Percentage 98.51 – 98.98 % |
Carbon Content of 1045 Carbon Steel
Medium-carbon steel like 1045 has a carbon content of roughly 0.45%. The amount of carbon in plain carbon steels is a key factor in determining their strength and mechanical characteristics. With a good balance of strength and toughness, 1045 steel can be heat-treated to harden due in part to the carbon content. Due to its medium-carbon composition, the specific mechanical properties of 1045 steel fall within the mid-range.
Properties of 1045 Carbon Steel
Table 2 summarizes the properties of 1045 carbon steel:
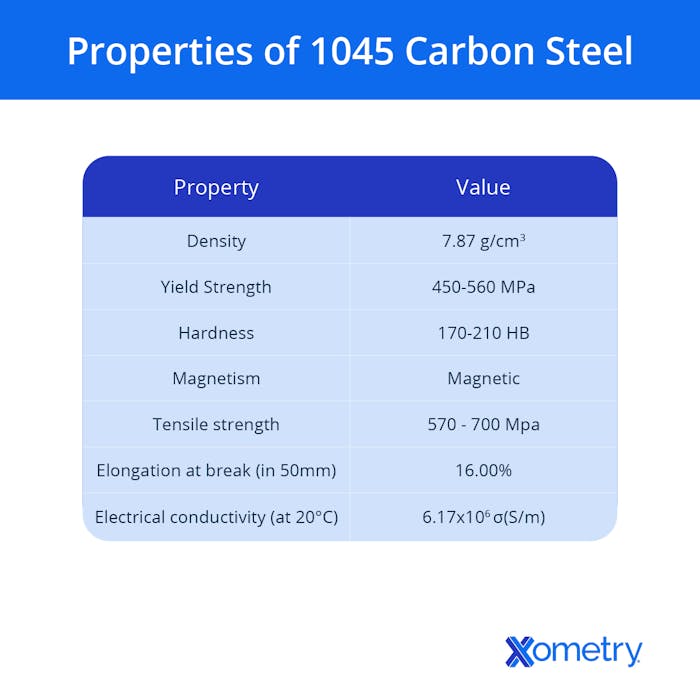
Machinability Rating of 1045 Carbon Steel
Steel, a versatile material, exhibits varying machinability based on its carbon content. Optimal machinability is achieved with medium carbon amounts, approximately 0.20%. For instance, 1045 carbon steel, which falls within this range, possesses a machinability rating of approximately 65% in its annealed condition. This rating reflects the favorable machinability characteristics of 1045 steel, categorizing it as a material with good machinability. To achieve the best machining results, AISI 1045 steel must undergo the proper heat treatment. Machinability can be impacted by a history of cold work or heat treatment.
Thermal Properties of 1045 Carbon Steel
The thermal properties of 1045 carbon steel include a thermal conductivity of approximately 51.9 W/m·K and a specific heat capacity of around 486 J/kg·K. These properties determine how the material conducts and stores heat. With its relatively high thermal conductivity compared to 304 stainless steel (16.8 W/(m·k)), AISI 1045 steel is efficient in transferring heat. This makes it suitable for applications that involve heat dissipation or thermal management. The specific heat capacity indicates the amount of heat energy required to raise the temperature of the material one degree Celsius. Table 3 shows these properties at a glance:
Property | Value |
---|---|
Property Thermal Conductivity | Value 51.9 W/m·K |
Property Specific Heat Capacity | Value 486 J/kg·K |
Property Melting Point | Value 1510 °C (2750 °F) |
Common Forms of 1045 Carbon Steel Material
The common forms of 1045 carbon steel material include sheet, bar, plate, hot rolled, annealed, and cold drawn variants. These are described below:
Sheet
1045 steel sheet is a thin and flat form with moderate strength, good machinability, and moderate weldability. It typically contains around 0.45% carbon, along with manganese, phosphorus, sulfur, and other trace elements. Its annealed microstructure consists of ferrite and pearlite, offering strength and toughness. 1045 steel sheet is used in manufacturing, automotive, construction, toolmaking, agriculture, industrial machinery, and oil and gas industries.
Bar
The strength, machinability, and wear resistance of the 1045 carbon steel bar are primarily determined by its composition and metallurgical properties, rather than its shape. However, the solid, cylindrical shape of the bar is widely recognized for facilitating efficient handling, machining, and installation processes. In summary, while the shape itself does not directly influence the mentioned properties, the cylindrical form of the 1045 carbon steel bar offers practical advantages in various applications. Ferrite and pearlite make up its annealed microstructure, which gives the material strength and toughness. Shafts, gears, bolts, studs, and other machinery parts are merely a few instances of the bar's numerous uses.
Plate
The main distinction between steel plates and steel bars lies in their sizes. Steel products that are more than 8 inches wide are classified as plate products, while those less than 8 inches wide are considered flat bar products. Both 1045 carbon steel plate and bar refer to specific types of steel made from carbon with the designation "1045," indicating its carbon content. 1045 has high strength, good machinability, and moderate weldability. AISI 1045 is a plain carbon steel containing 0.45% carbon, 0.45% manganese, 0.45% phosphorus, 0.45% sulfur, and other trace elements. Its ferrite and pearlite annealed microstructure contribute to good toughness and impact resistance. Construction equipment, industrial machinery parts, and machinery frames are common uses for 1045 carbon steel plates.
Hot Rolled
Hot rolling is a manufacturing process employed in various industries to produce hot-rolled 1045 carbon steel. This process results in a scaled surface finish. Hot-rolled 1045 steel exhibits enhanced ductility, toughness, and machinability in comparison to cold-drawn or cold-rolled forms. Industries such as automotive, construction, and machinery utilize hot-rolled 1045 steel for the production of shafts, gears, axles, and structural components.
Annealed
Annealing is a heat treatment process that aims to modify the microstructure and grain size of a material. By heating the material to a specific temperature, crystallization occurs, resulting in larger grain sizes. If the material was in the martensite phase before annealing, it will no longer be in that phase afterward. However, the distribution of pearlite and ferrite may vary while the overall amounts remain unchanged. Among various heat treatment techniques, annealing is popular due to its ability to increase ductility and reduce hardness. When 1045 carbon steel is annealed, it undergoes heat treatment to relieve internal stresses and improve machinability. In its annealed state, the steel exhibits enhanced machinability, improved dimensional stability, and reduced hardness.
Cold Drawn
1045 carbon steel that has been cold drawn or cold worked experiences plastic deformation above the temperature of recrystallization, which causes strain hardening. Compared to the annealed state, this decreases ductility while increasing yield and ultimate tensile strength. Cold-drawn 1045 steel has a deformed microstructure despite being primarily ferrite and pearlite. This manufacturing process improves mechanical properties, surface quality, and dimensional accuracy, making it suitable for applications that call for high strength, tight tolerances, and excellent surface quality, such as automotive parts, shafts, and precise machinery components.
Equivalents Grades 1045 Carbon Steel
Table 4 shows equivalent grades for AISI 1045 carbon steel in the naming systems:
Country | Equivalent Name |
---|---|
Country United States | Equivalent Name AISI 1045 |
Country European Union | Equivalent Name C45E or Ck45 |
Country Germany | Equivalent Name 1.1191 or C45E |
Country United Kingdom | Equivalent Name 080M46 or 43A |
Country Japan | Equivalent Name S45C or S48C |
Country China | Equivalent Name 45# or 45B |
Advantages of Using 1045 Carbon Steel
The advantages of using 1045 carbon steel include:
- Offers excellent tensile strength and hardness, making it suitable for demanding applications.
- It can be easily machined into various shapes and forms, allowing for efficient manufacturing processes.
- When techniques for joining medium-carbon steels are used, AISI 1045 is suitable for welding.
- 1045 carbon steel is known for its ferrite and pearlite microstructure, which consists of alternating lamellae of ferrite and cementite (iron carbide). This unique structure contributes to its wear-resistance properties. The carbides present in the pearlite structure are responsible for providing enhanced wear resistance, making 1045 carbon steel suitable for components subjected to wear and friction.
Disadvantages of Using 1045 Carbon Steel
While 1045 carbon steel offers many benefits, there are a few disadvantages to consider:
- It is not highly resistant to corrosion, especially in harsh environments. It may require additional protective coatings or maintenance to prevent corrosion.
- It has a limited ability to be hardened through heat treatment compared to some other steel grades. This can limit its use in applications where high hardness is required.
- Improper heat treatment or welding techniques can lead to cracking or distortion in 1045 carbon steel components.
- While 1045 carbon steel is not considered a high-cost material compared to some specialty steels, it can be more expensive than lower-grade carbon steels. The cost of steel depends on various factors such as the quality, availability, market demand, and the specific requirements of a project.
Difference Between 1045 Carbon Steel and A514 Steel
The difference between 1045 carbon steel and A514 steel (also called “T1”) lies in their composition and strength. While A514 steel, a high-strength, low-alloy steel, contains specific alloying elements such as carbon, chromium, and manganese. It is often employed in structural applications due to its higher strength and hardness, 1045 carbon steel, which has 0.45% carbon, is used for general-purpose applications.
Summary
Xometry provides a wide range of manufacturing capabilities including CNC machining, 3D printing, injection molding, laser cutting, and sheet metal fabrication. We can work with 1045 carbon steel. Get your instant quote today.
Disclaimer
The content appearing on this webpage is for informational purposes only. Xometry makes no representation or warranty of any kind, be it expressed or implied, as to the accuracy, completeness, or validity of the information. Any performance parameters, geometric tolerances, specific design features, quality and types of materials, or processes should not be inferred to represent what will be delivered by third-party suppliers or manufacturers through Xometry’s network. Buyers seeking quotes for parts are responsible for defining the specific requirements for those parts. Please refer to our terms and conditions for more information.
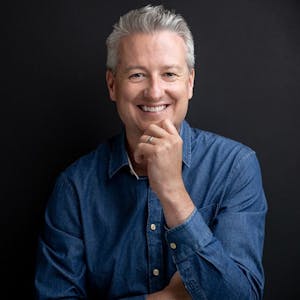