Materials capable of adapting to different environments and applications become a handy go-to in the back pockets of manufacturers, and 410 stainless steel is definitely one such example. Thanks to its easy machinability and relatively low cost—along with a few other helpful properties—410 has risen among the ranks of useful stainless steels. Here’s what you should know about it.
What Is 410 Stainless Steel?
You’ll find this popular steel neatly categorized under the family of steels with martensitic structures. Its composition will vary slightly, but it’s usually made up of iron chromium, magnesium, and nickel, then around 0.08 to 0.15% of carbon, 1.0% or less of silicon, 0.03% or less of sulfur, and 0.04% or less of phosphorus. You can see the breakdown in the pie chart below.
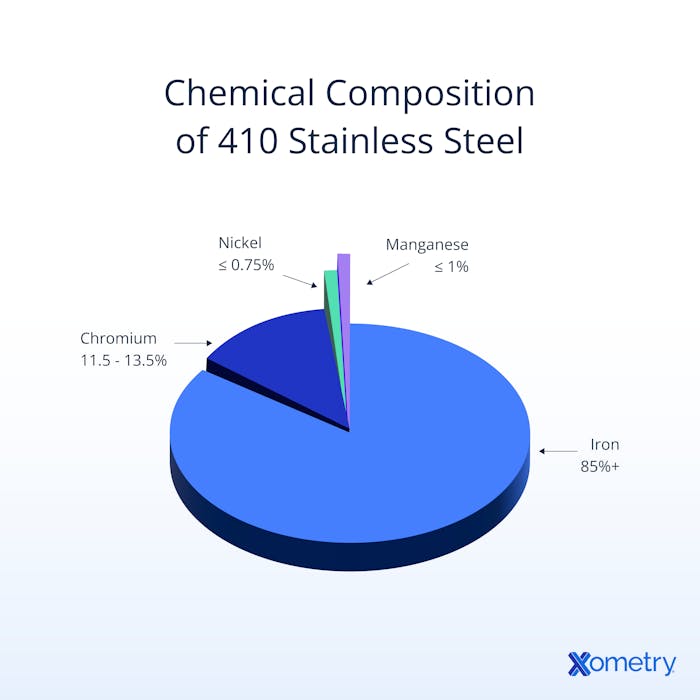
Because 410 brings a decent corrosion resistance and good hardness to the table, it’s found in everything from your standard pair of kitchen scissors to heavy-duty steam turbine blades. You can also harden it, which can’t be said for other kinds of martensitic steels.
How It’s Made
With the help of an electric arc furnace, the components of this stainless steel are melted and formed into whichever format the manufacturer has in mind. Here’s how the process works on a more granular level:
- First, the raw bits needed to make 410 steel are poured into an electric arc furnace or an induction furnace—these usually include chromium, carbon, and other alloying elements. Higher grades will usually have this done under a vacuum. The melting process cuts out contaminants and oxides, creating a floating slag that’ll be removed.
- Once it’s melted down, the mixture will be poured into casts to form some kind of ingot or billet.
- After they’ve formed and cooled, the maker will reheat those ingots to get them to a place where they can be turned into different shapes. This’ll be done through forging, rolling, or extrusion.
- Then, these shapes will go through annealing to lessen internal stresses and boost their ductility and workability.
- After this, you or the manufacturer can choose from a few different finishing processes, including more annealing or heat treatment, hot rolling, or cold rolling.
- Lastly, grinding, polishing, and other surface treatments are popular in order to get the steel in shape for the application it’s being made for.
Property | Value |
---|---|
Property Density | Value 7.8 g/cc |
Property Yield Strength | Value 1,225 MPa at a strain of 0.2% |
Property Ultimate Tensile Strength | Value 1,525 MPa |
Property Hardness | Value 126–192 Brinell hardness (annealed) or 201–255 Brinell hardness (hardened and tempered) |
Property Bulk Modulus | Value 200 GPa |
Property Melting Point | Value 1,480–1,530 °C |
Property Corrosion Resistance | Value Good corrosion resistance in milder environments, including chemical-laden ones and water. Pitting, corrosion, and staining happen in salt water conditions and acidic environments. |
Property Magnetism | Value Magnetic thanks to its martensitic structure and a permeability of 700–1,000. |
Property Thermal Conductivity | Value Low, 24–27 W/mK |
Property Coefficient of Thermal Expansion | Value 9.9 to 11.0 x 10-6/°C between 0–100 °C |
Property Minimum and Maximum Service Temperature | Value -70 °C (min), 400–580 °C (max) |
Property Machinability Rating | Value Moderately so at 55% for a 12% chromium alloy, but it will strongly depend on the steel’s specific carbon content and how it is heat treated. |
Property Applications | Value Scissors, knife blades, kitchen utensils, valves, pumps, pipe fittings, petroleum refining/processing equipment, firearm barrels, fasteners, screws, bolts, nuts, steam turbine blades, springs, and Belleville washers. |
410 Stainless Steel Properties
Common Formats of 410 Stainless Steel
There are a few formats that are most typically found when you’re sourcing or making 410 stainless steel, and we’ve put a small explanation of shapes and finishing processes below:
Shapes
- Sheet: This is a flat-profile sheet material that often has a thickness between 0.5 to 3.5 mm and can come as a hot-rolled or cold-rolled variation, the latter usually being stiffer.
- Bar: You can find bars in a few distinct shapes, including round, hexagonal, rectangular, or other customized dimensions. They can also go through hot and cold rolling, depending how hard you need it to be.
- Plate: This type looks pretty similar to a sheet, but is usually thicker (though there isn’t a standard definition between when steel becomes a plate rather than a sheet). Typically plates are around 2 to 3 mm, but it’s a guide rather than a strict requirement.
Processes
- Hot Rolled: This is a sizing process that gets ingots or billets into the thickness that manufacturers need for additional processing.
- Cold Rolled: After sizing happens during hot rolling, steel can be cold rolled which gives it a nicer surface finish and more precise thickness. This process also work-hardens it slightly.
- Annealed: Stainless steel that’s gone through annealing means that it hasn’t been hot- or cold-rolled and instead cooled from red hot to the stage it’s in now. This gives the material a better chance to grow its crystal structure without as many internal stresses.
- Cold Drawn: Steel that goes through this will be cold-pulled through a die for better dimensions and work hardening. This process improves its strength and hardness, but reduces its ductility (and it can be brittle after).
Country/Organizational Body | Equivalent Grade |
---|---|
Country/Organizational Body Japan | Equivalent Grade JIS SUS 410 |
Country/Organizational Body AISI | Equivalent Grade AISI 416 / AISI 420 (close grade) |
Country/Organizational Body Europe | Equivalent Grade X12Cr13 (1.4006) |
Country/Organizational Body UNS | Equivalent Grade S41000 |
Country/Organizational Body EN | Equivalent Grade 1.4006 |
How do you heat treat 410 stainless steel?
Manufacturers typically heat treat 410 stainless steel through hot quenching and tempering to harden, strengthen, and toughen it. The process usually involves preheating the material to a temperature between 760–815 °C, and then when it’s hot, it gets quickly quenched in oil, water, or air. This freezes the steel’s microstructure when it has a fine crystallinity. Once this is done, it’ll often get tempered to reduce internal stress—and the temperature this is done at will determine how hard and ductile it remains.
What are the advantages of 410 stainless steel?
Using 410 stainless steel has a few specific advantages, including that it has great corrosion resistance and hardness, as well as pretty high tensile strength. It also has great wear and heat resistance and does well with heat treatment. Lastly, it’s machinable and relatively inexpensive compared to other steels.
What are the disadvantages of 410 stainless steel?
There are a few downsides to working with 410 stainless steel, one being that it isn’t capable of handling highly corrosive environments that have a lot of exposure to chemicals and salt. It’s also not the best steel out there for welding, and it gets brittle in cold temperatures. It’s also good to note that it’s magnetic and has limited formability, which are disadvantages for some scenarios.
What are the differences between 410 stainless steel and 304 stainless steel?
When you look at both 410 and 304 stainless steels, you’ll notice that 410 has lower corrosion resistance when up against 304 but better strength and hardness. 304 is ideal for corrosive environments that 410 might falter in, but it isn’t as strong.
How Xometry Can Help
We’re no stranger to working with various stainless steel materials here at Xometry, including 410. Some of the related services we offer that you can get a free quote for through our website include stainless steel 3D printing, stainless steel laser cutting, and stainless steel sheet metal fabrication.
Disclaimer
The content appearing on this webpage is for informational purposes only. Xometry makes no representation or warranty of any kind, be it expressed or implied, as to the accuracy, completeness, or validity of the information. Any performance parameters, geometric tolerances, specific design features, quality and types of materials, or processes should not be inferred to represent what will be delivered by third-party suppliers or manufacturers through Xometry’s network. Buyers seeking quotes for parts are responsible for defining the specific requirements for those parts. Please refer to our terms and conditions for more information.
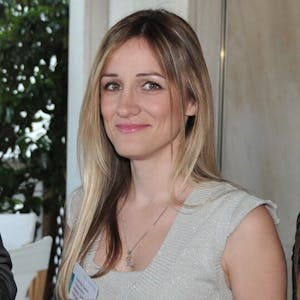