430 stainless steels are a commercially important class of materials, as they deliver much of the material-property range of similar, higher-cost materials. This is a result of careful tuning of the alloy to provide many of the beneficial properties of the broader class, with minimal use of the highest-cost alloying components such as nickel (at most, variants contain 0–0.75%). It derives many of its beneficial properties from the 16–18% chromium content. It is generally manufactured using a carbon arc furnace or inductive furnace.
430 stainless steel is not suited to the highest-stress applications and has only moderate resistance to aggressive environments. These materials, however, function extremely well and offer fairly good processing characteristics which make them well-suited to the majority of stainless steel applications. This article will further discuss 430 stainless steel, its uses, composition, and properties.
What Is 430 Stainless Steel?
430 stainless steel is a ferritic stainless steel alloy, from the 400 series of stainless steels. This material is valued for its corrosion resistance, moderate strength, and affordability compared to other stainless steel grades. It contains approximately 17% chromium, which provides its corrosion resistance. However, it has a low nickel content, around 0.75% (maximum), which makes it less expensive than austenitic stainless steel.
430 stainless steel is commonly used where corrosion resistance is required, such as in kitchen appliances, automotive trim, architectural trim, and industrial equipment. It is also used for some cookware and utensils. However, it is not suitable for highly corrosive environments. While 430 stainless steel offers good corrosion resistance in pH-neutral and mildly acidic environments, it is susceptible to pitting corrosion in saltwater environments.
To learn more, check out our guide on Carbon Steel Properties.
430 Stainless Steel Uses
The material is used in applications where moderate corrosion resistance, relatively low cost, and good mechanical properties are required. Listed below are some examples of its uses:
- Kitchen appliances and cookware such as: sinks, range hoods, oven liners, pots and pans, and dishwasher/refrigerator/oven panels.
- Automotive trim and accents.
- Used in architectural applications such as decorative trim, door frames, window frames, and handrails.
- It is employed widely in industrial equipment, including liquid and powder storage tanks and hoppers, chemical processing equipment, heat exchangers, and pumps and valves for less-aggressive fluids.
- Suitable for exhaust system parts, such as exhaust pipes, catalytic converter housings, and mufflers.
- Fasteners and hardware such as screws, bolts, nuts, and other items like hinges and brackets.
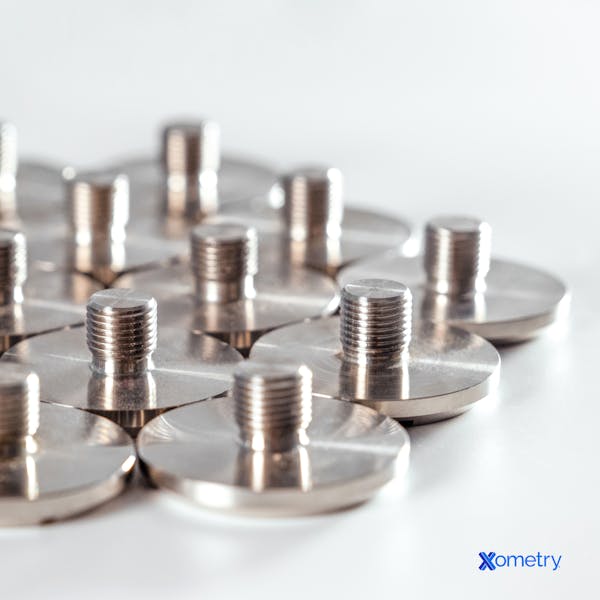
How 430 Stainless Steel Is Made
430 stainless steel is made by refining and melting in a furnace with reducing agents that purify the melt. This can be an electric arc furnace, heated by arcing between two carbon electrodes, or an induction heating furnace surrounded by a high-power AC coil. In either case, purification under a vacuum is used to produce the highest grades. This is followed up with hot working and heat treatment.
Chemical Composition of 430 Stainless Steel
430 stainless steel is mostly made up of iron. The rest of its typical chemical composition is shown in Table 1 below:
Iron (Fe) | Chromium (Cr) | Nickel (Ni) | Carbon (C) | Manganese (Mn) | Silicon (Si) | Sulfur (S) | Phosphorus (P) |
---|---|---|---|---|---|---|---|
Iron (Fe) typically 85%+ | Chromium (Cr) 16–18% | Nickel
(Ni) 0–0.75%* | Carbon
(C) 0.12% | Manganese (Mn) 1.0% or less | Silicon (Si) around 1.0% | Sulfur
(S) 0.03% or less | Phosphorus (P) 0.04% or less |
*sometimes reported as 0.5% max.
Carbon Content of 430 Stainless Steel
The typical carbon content of 430 stainless steel is between 0.08 and 0.12%. This significantly affects the behaviors and properties of the material, compared with lower carbon steels.
Properties of 430 Stainless Steel
The properties of 430 stainless steel are shown in Table 2 below:
Property (Annealed) | Value |
---|---|
Property (Annealed) Density | Value 7.62–7.82 g/cc |
Property (Annealed) Yield strength | Value 345 MPa at a strain of 0.2% |
Property (Annealed) Ultimate tensile strength | Value 517 MPa |
Property (Annealed) Hardness | Value 85 Rockwell B |
Property (Annealed) Modulus of elasticity | Value 200 GPa |
Property (Annealed) Melting point | Value 1,425–1,510 °C |
Property (Annealed) Heat resistance | Value Good heat resistance up to temperatures of about 815 °C (1,500 °F). It can withstand intermittent high-temperature exposure without significant scaling or deformation. |
Property (Annealed) Corrosion resistance | Value Good corrosion resistance in mild atmospheric environments, water, and some mild chemical environments. It shows pitting corrosion and brown staining in saltwater conditions and offers lower resistance to acidic environments than the austenitic stainless steel alternatives. |
Property (Annealed) Formability | Value Annealed 430 stainless steel has good formability, allowing it to be easily formed into various shapes, including sheets, coils, plates, and other fabricated components. It can be bent, stamped, drawn, and roll-formed without much difficulty. |
Property (Annealed) Weldability | Value 430 stainless steel has fair weldability. It can be welded using common welding techniques, such as resistance welding and fusion welding, including TIG and gas MIG. Intercrystalline corrosion can later result from poor technique |
Property (Annealed) Magnetism | Value Typical permeability of 800. Moderately responsive to magnetic fields; acts as a moderate magnetic flux carrier due to its ferritic structure.
NOTE: 430F (free machining grade) has an elevated sulfur content and is considered nonmagnetic. |
Thermal Properties | Value |
---|---|
Thermal Properties Thermal conductivity | Value 23 to 27 W/mK @ 23 °C |
Thermal Properties Coefficient of thermal expansion | Value 10.4 to 10.8 x 10-6/°C |
Thermal Properties Max service temp | Value 815 °C continuous, 870 °C short time |
Thermal Properties Min service temp | Value -40 to -70 °C |
Thermal Properties Melting point | Value 1,425–1,510 °C |
Thermal Properties Annealing temp | Value 790–835 °C |
Thermal Properties Stress Relief annealing | Value 430–595 °C |
How To Heat Treat 430 Stainless Steel
430 stainless steel is ferritic stainless steel and does not respond well to heat/quench hardening to achieve changes in its mechanical properties. In general, the properties do not undergo phase transformations that lead to increased hardness and strength. Examples of heat treatment processes that can be applied to 430 stainless steel are stress relief annealing and annealing/normalizing. In stress relief annealing, the material is heated within this range and held at a temperature for a sufficient time to allow for stress relaxation. On the other hand, annealing/normalizing is a more aggressive heat treatment process that involves heating the material and then cooling it slowly to fully relieve residual stress and improve ductility.
Common Forms of 430 Stainless Steel Material
430 stainless steel is manufactured in a range of profiles and forms, according to the needs of the application and the processes to be applied to the material. The common forms are listed below:
Sheet
This describes flat material cut into a variety of rectangular shapes/sizes. Definitions of “sheet” vary, but 0.5 to 3.5 mm thickness is fairly typical. This is manufactured in both hot-rolled and cold-rolled conditions. The cold-rolled sheet, having undergone a degree of work-hardening, will be both stronger and harder. The hot-rolled sheet will be in the annealed state of fully soft and maximum ductility. Edges of sheets can be supplied as full round (a result of the rolling process), skived (beveled off in a single pass cut), or slit (generally roller cut to a square edge). A full round is only available on the as-rolled edges, not on cut edges.
Bar
This can be round, hexagonal, strip, or any specified profile required for a customer or product. Bar shapes are formed either by hot or cold rolling, depending on the hardness specification and surface finish requirements. Bar is also supplied in a range of profile sectionals, available in regular or irregular (asymmetric) profiles.
Plate
The plate is manufactured to the same specifications as a sheet, simply in greater thickness. The thickness at which material can be defined as “plate” rather than “sheet” is quite arbitrary. But generally, any thickness greater than (approximately) 3 mm is referred to as a plate. It is common to see plates supplied in rolled thicknesses of 100 mm and more, in a variety of work-hardened, stress-relieved, or annealed states.
Hot Rolled
Hot rolling uses pinch rollers to reduce the section thickness of the plate, sheet, and strip which pass between the rollers at “red” heat. This is the sizing process to bring the billet/ingot to the thickness for follow-on processing. Hot rolling can produce considerable thickness variance and leaves an imperfect, blue/black surface. Hot-rolled material will be fully soft and have the maximum ductility the material can offer.
Cold Rolled
Cold rolling is the precision sizing process that is applied after hot rolling, to rescue the thickness of a section to a reliable final product. This gauges the product and improves the surface finish. Cold-rolled material will display some degree of work hardening, variable according to the degree of compression rolling performed.
Annealed
Annealed material is fully soft and has been allowed to slowly cool from red heat, to maximize crystal growth and ductility. A larger crystal matrix reduces the internal stresses that manifest as hardness, whereas cold work fractures the larger crystal bodies into smaller parts, displaying great stress at the crystal boundaries that result in higher hardness, stiffness, and strength—but lower ductility.
Cold-Drawn
Cold-drawn material is a cold pull process, drawing a bar through a die to reduce its diameter. This results in better dimensional precision and more work hardening, increasing the strength and hardness and reducing the ductility of the bar. High residual stresses and potential for brittleness will result in the most cold-worked material.
Equivalents of 430 Stainless Steel
There are several stainless steel grades that can be considered equivalents or alternatives to 430 stainless steel, depending on the specific requirements of the application. Some examples are listed in Table 4 below:
Authority | AISI | European standards org | Japanese standards org | US |
---|---|---|---|---|
Authority Specification | AISI AISI 409 | European standards org EN 1.4016 (X6Cr17) | Japanese standards org JIS SUS 430 | US UNS S43000 |
Advantages of Using 430 Stainless Steel
Using 430 stainless steel offers several advantages in various applications. Here are some key advantages of using 430 stainless steel:
- Provides good corrosion resistance in mildly acidic and non-aggressive environments.
- Is less expensive than the austenitic stainless steel grades, such as 304 or 316.
- Has good formability in its annealed form, allowing it to be easily formed into complex shapes and tight curvature. It can be bent, stamped, drawn, and roll-formed without difficulty.
- Has good heat resistance and can withstand intermittent high-temperature exposure without damaging, scaling, or deformation.
- It is magnetic due to its ferritic microstructure. This magnetic property can be advantageous in certain applications if a magnetic response is required, such as in the manufacturing of magnetic components like solenoid cores and other types of electromagnetic parts.
- Has a bright, white-light reflective character that provides an attractive aesthetic appearance. It responds well to mechanical and electropolishing processes, delivering a mirror finish.
- It is readily available in a huge range of forms/profiles, including sheets, coils, plates, bars, and wires.
Disadvantages of Using 430 Stainless Steel
Using 430 stainless steel also brings some limitations and disadvantages that must be considered before specifying it as a solution. Some disadvantages are listed below:
- While 430 stainless steel provides good corrosion resistance in mildly acidic and non-corrosive environments, it is less resistant to chemical attack than some other stainless steel.
- Has lower tensile and yield strength compared to austenitic stainless steel grades like 304 or 316. Failure modes include deformation and dimensional failure under heavy loads or stress.
- While 430 stainless steel has good heat resistance in intermittent high-temperature environments, it is not recommended for continuous high-temperature exposure. This will result in scaling, oxidation, and a reduction in strength, fatigue resistance, and creep resilience.
- It can be quite challenging to weld 430, compared with other stainless steel grades. Intergranular corrosion and reduced corrosion resistance in the heat-affected zones generated during welding is a major, invisible issue that has long-term consequences.
- It has a high work hardening rate, compared to some other stainless steel grades—both austenitic and martensitic types. Difficulties in cold working or shaping the material without causing excessive hardness and reduced ductility lead to pronounced limitations on its use in cold-worked applications.
The Difference Between 430 Stainless Steel and 304 Stainless Steel
430 stainless steel and 304 stainless steel are widely employed material grades. Both have significant differences in composition, properties, and optimal use although they have many applications in common. 430 stainless steel has a ferritic (BCC) crystalline structure, containing 16–18% chromium and less than 0.12% carbon. It also has a low nickel content of around 0–0.75%. The absence of nickel is a significant contributor to its lower cost, compared with austenitic stainless steels. 304 stainless steel contains 18–20% chromium and 8–10.5% nickel, making it a higher-cost austenitic material. It also has a low carbon content of less than 0.08%. The nickel enhances its corrosion resistance, as well as delivering other advantageous properties that suit some more demanding applications.
430 is a general-purpose alloy used in applications in which non-acid/chloride corrosion resistance, formability, and material price are key factors. It is a widely accepted material solution for equipment in non-aggressive environments. 304 stainless steel is used when excellent corrosion resistance is required, such as in food- and chemical-processing equipment, pharmaceutical machinery, and marine applications.
The Difference Between 430 Stainless Steel and 316 Stainless Steel
430 and 316 stainless steel are distinct stainless steel grades with extensive differences in composition, properties, and utility. Though, they are essentially interchangeable in lower-stress and milder-environment applications. 316 is a closely related alloy to 304, sharing many of its properties and improving its performance in many regards.
430 stainless steel, being formed from a BCC, ferritic crystalline matrix, contains 16–18% chromium, below 0.12% carbon, and nickel content of 0–0.75%, with trace or zero molybdenum. Low nickel and no intentional molybdenum content make it a low-cost material, compared with 316 stainless steel. 316 is an austenitic stainless steel containing 16–18% chromium, 10–14% nickel, and 2–3% molybdenum, with a very low carbon content of less than 0.08%. The presence of elevated nickel and molybdenum improves a range of properties in commercially beneficial ways. 430 has a high tolerance to heat exposure and can withstand intermittent high-temperature exposure without significant negative consequences, though it responds poorly to continuous high-temperature applications. 316 alloy steel is highly heat tolerant and can withstand continuous high-temperature exposure without significant scaling or deformation, retaining its corrosion resilience at elevated temperatures.
The Difference Between 430 Stainless Steel and 201 Stainless Steel
430 stainless steel and 201 stainless steel are very divergent grades with significant differences in terms of composition, properties, and applications. 430 stainless steel is ferritic and contains 16–18% chromium and a maximum of 0.12% carbon. Its low nickel (0–0.75%) and zero molybdenum content make it very low cost, compared to 201 stainless steel. 201 stainless is a low-carbon (max 0.15%) austenitic alloy, with approximately 16–18% chromium, 3.5–5.5% nickel, and a high proportion of manganese (5.5–7.5%). Higher manganese influences the hot-working properties of steel alloys as well as improving toughness, strength, and heat treatability. The slightly higher nickel content—although still regarded as low—equips 201 stainless steel with enhanced corrosion resistance compared to 430 alloys.
430 alloy offers good corrosion resistance in non-aggressive and non-chloride ion-containing environments. Exposure to chloride ions triggers pitting and crevice corrosion. 201 stainless alloy provides significant improvements in corrosion resistance in all conditions compared to 430 steel.
How Xometry Can Help
Xometry provides a wide range of manufacturing capabilities including CNC machining, 3D printing, injection molding, laser cutting, and sheet metal fabrication. Get your instant quote today.
Disclaimer
The content appearing on this webpage is for informational purposes only. Xometry makes no representation or warranty of any kind, be it expressed or implied, as to the accuracy, completeness, or validity of the information. Any performance parameters, geometric tolerances, specific design features, quality and types of materials, or processes should not be inferred to represent what will be delivered by third-party suppliers or manufacturers through Xometry’s network. Buyers seeking quotes for parts are responsible for defining the specific requirements for those parts. Please refer to our terms and conditions for more information
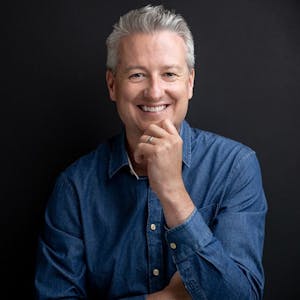