4340 Carbon Steel and How It's Used
4340 is an American standard carbon steel that is sought after for its high-strength properties. 4340 steel is ferromagnetic which means its magnetic properties will depend on the phase of the steel. However, the lack of substantial alloying elements results in the iron creating very magnetic steel.
4340 carbon steel is a strong material, and so it has uses in structural and high-strength applications. These can include but are not limited to transmissions, gears and shafts, landing gear, hydraulic systems, automotive frames, and fasteners. It finds uses in heavy-duty applications including landing gear, transmissions, and other structural components.
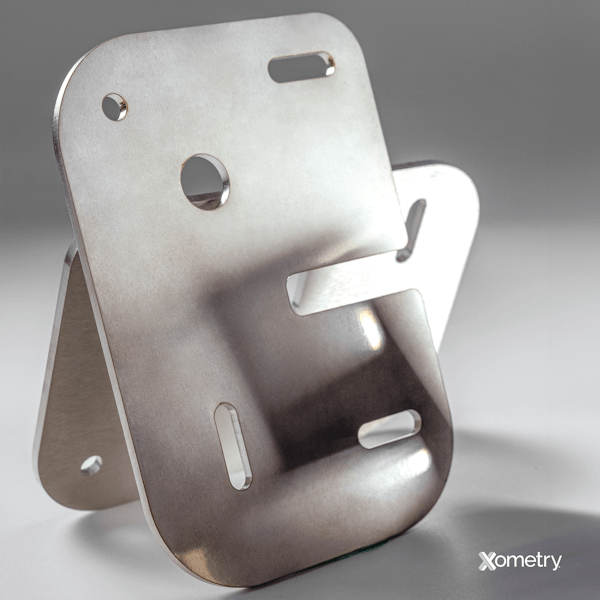
How 4340 Carbon Steel is Made
Creating 4340 carbon steel involves melting the elements and then cooling them in a controlled manner. The steel is heat treated, and then cut into its final form. The iron and all alloying elements are weighed and added to an electric furnace which takes up to 12 hours to melt all the elements. A Vacuum Oxygen Decarburization (VOD) system can control the amount of carbon in the steel. The amount of carbon removed will affect the hardness and tensile strength of the material. Before cooling, the steel will be stirred to ensure the elements are uniformly mixed. As the metal is cooled into billets it may be hot rolled while still above its crystallization temperature to form the steel into shape. If precise dimensions are required the steel may be cooled and rolled below its crystallization temperature. Once cooled, the steel may be heat treated to relieve its internal stresses. Finally, the 4340 steel will be cut to its final shape and surface finish, which will depend on the application of the steel but may include grinding.
Chemical Composition of 4340 Carbon Steel
The main element of 4340 steel is iron which makes up approximately 95.5% of the total composition. The next most common elements in 4340 steel are nickel, which makes up 1.85%, and chromium, which makes up 0.8% of the total composition. Table 1 below shows the full composition of 4340 steel:
Element | Content |
---|---|
Element Iron | Content 95%–96% |
Element Nickel | Content 1.65%–2% |
Element Chromium | Content 0.7%–0.9% |
Element Manganese | Content 0.6%–0.8% |
Element Carbon | Content 0.37%–0.43% |
Element Molybdenum | Content 0.2%–0.3% |
Element Silicon | Content 0.15%–0.3% |
Element Sulfur | Content 0.04% |
Element Phosphorus | Content 0.03% |
Carbon Content of 4340 Carbon Steel
The carbon content of 4340 steel is between 0.37% and 0.43%. This means it is not a low-carbon steel as low-carbon steels have a carbon level of less than 0.3%. As the carbon content of steel increases so does its hardness, meaning that 4340 carbon steel is harder than any low-carbon steel.
Properties of 4340 Carbon Steel
Below is Table 2 which contains various properties of a typical 4340 steel variant:
Property | Value |
---|---|
Property Density | Value 0.284 lb/in3 |
Property Yield Strength | Value 125,000 psi |
Property Hardness (Rockwell B) | Value 100 |
Property Magnetism | Value Ferromagnetic |
Machinability Rating of 4340 Carbon Steel
4340 carbon steel has a machinability rating of 55% in the annealed condition. The recommended speed for turning is between 710–950 SFM. The recommended speed for milling is 430–590 SFM.
Thermal Properties of 4340 Carbon Steel
The melting point of 4340 steel is 2,600 °F. 4340 carbon steel also has a thermal conductivity of 309 Btu-in/hr-ft2°F, a specific heat capacity of 0.114 Btu/lb-°F, and a rate of linear expansion of 6.83 µin.in-°F.
4340 Steel Heat Treatment
4340 steel is heat treated using an annealing process in which internal stresses are relieved with the application of heat. To anneal 4340, the steel must first be heated to 1,525 °F and then cooled slowly. Initially, it must be cooled to 1,350 °F and then furnace-cooled to 1,130 °F. Cooling between 1350–1130 °F must happen at a rate of 20 °F an hour. Finally, the steel must be air-cooled to room temperature.
Common Forms of 4340 Carbon Steel Material
The common forms of 4340 carbon steel are listed below:
Sheet
The sheet form of 4340 steel can be found in thicknesses between 0.018” and 0.25” thick. Sheet metal is usually used for bodywork and panels for machinery.
Bar
The bar form of 4340 carbon steel can be found in multiple geometries including tubular and circular forms. The bar form of 4340 steel will be used to create structural support for different applications, especially in aircraft and automotive applications.
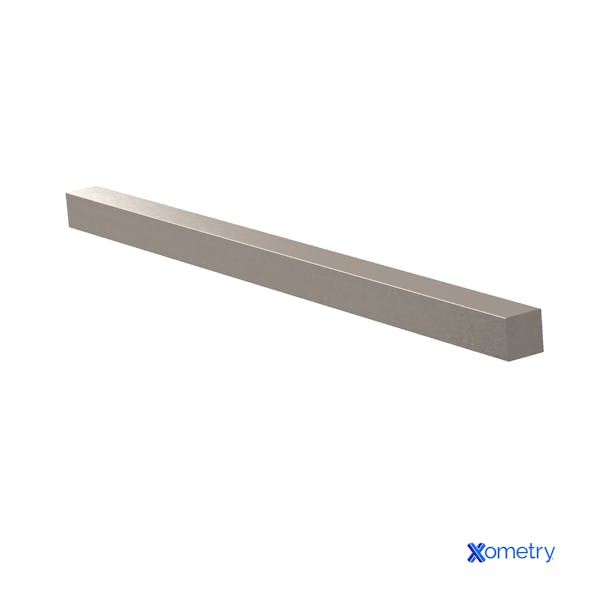
Plate
Plates of 4340 steel will have a thickness greater than 0.25” thick. 4340 plates can be used in various applications but are known for their use as steel armor.
Hot Rolled
Hot rolling 4340 creates a steel that is renowned for its toughness. The hardened condition of hot-rolled 4340 steel also improves the impact and wear resistance of the steel. The hot rolling of steel creates these properties by imparting a strain on the microstructure of the metal causing it to work harden. The strain on the microstructure increases the dislocation density which is what hardens and strengthens the steel.
Annealed
During annealing, 4340 carbon steel is raised to a temperature of 1,525 °F then cooled to 1,350 °F and furnace-cooled to 1,130 °F at a rate of 20 °F per hour. The annealing process is time-consuming, however, it is required to obtain a pearlite structure ready for machining.
Cold-Drawn
Cold drawn versions of the 4340 bar have widespread use in the aerospace industry because of their high strength and high ductility. Cold-drawn steel is very similar to hot-rolling steel as it increases hardness and strength. However, cold drawing has a greater effect than hot rolling. The cold-drawn process also ends with a more dimensionally accurate metal, due to the lack of thermal expansion and contraction. The only downside is that cold-drawn steel is more expensive as it is more labor-intensive.
Equivalent Grades of 4340 Carbon Steel
Table 3 showing the equivalent forms of 4340 steel is given below. Note that some chemical compositions may not be an exact match but are the nearest equivalent:
Country | Equivalent Grade |
---|---|
Country EU | Equivalent Grade 36CrNiMo4 |
Country USA | Equivalent Grade 4340 |
Country Germany | Equivalent Grade 34CRNIMO6 |
Country Japan | Equivalent Grade SNCM 439/SNCM8 |
Country France | Equivalent Grade 40NCD3 |
Country England | Equivalent Grade EN24/817M40 |
Country Russia | Equivalent Grade 36KH2N2MFA |
Country China | Equivalent Grade 40CrNiMoA |
Country Italy | Equivalent Grade 35NICRMO6 |
Advantages of Using 4340 Carbon Steel
One of the advantages of choosing to use 4340 over other steels is it has really good fatigue resistance. Other advantages of using 4340 carbon steel are:
- Good shock resistance.
- Good impact resistance.
- High wear and abrasion resistance.
Disadvantages of Using 4340 Carbon Steel
4340 steel has its limitations. One such limitation is that it is not very corrosion-resistant. Other limitations of 4340 steel are:
- Not highly machinable.
- At high risk of quench cracking.
- 4340 steel, as with every steel, is very heavy.
Difference Between 4340 Steel and 4330 Steel
4330 and 4340 are both medium-carbon and low-alloy steels with distinct differences. For example, 4330 has more manganese, chromium, nickel, and vanadium than 4340 steel. Due to these extra alloying elements, 4330 has a much higher tensile strength, yield strength, and hardness. Both 4340 and 4330 have found use in transmission gears and aircraft landing gear.
Difference Between 4340 Steel and 4140 Steel
4340 and 4140 are very similar metals. However, they do have some differences both in composition and properties. For example, 4340 has a higher carbon content while 4140 alloy steel has a higher chromium content. However, the most significant composition difference is that 4340 includes nickel which accounts for its higher strength and fracture toughness. The lack of nickel in 4140 also makes it more susceptible to fracturing.
Difference Between 4340 Steel and 300M Steel
300M steel and 4340 steel are similar. However, 300M steel has the addition of vanadium and copper and a higher silicon and molybdenum content. 300M is considered a modified version of 4340 steel which has better fatigue strength, ductility, impact strength, and fracture toughness.
Summary
This article presented 4340 steel, explained what it is, and discussed its various applications. To learn more about 4340 steel, contact a Xometry representative.
Xometry provides a wide range of manufacturing capabilities, and other value-added services for all of your prototyping and production needs. Visit our website to learn more or to request a free, no-obligation quote.
Disclaimer
The content appearing on this webpage is for informational purposes only. Xometry makes no representation or warranty of any kind, be it expressed or implied, as to the accuracy, completeness, or validity of the information. Any performance parameters, geometric tolerances, specific design features, quality and types of materials, or processes should not be inferred to represent what will be delivered by third-party suppliers or manufacturers through Xometry’s network. Buyers seeking quotes for parts are responsible for defining the specific requirements for those parts. Please refer to our terms and conditions for more information.
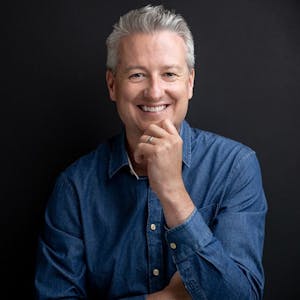