With a long list of aluminum alloys out there, it’s good to know the differences between each type when you’re sourcing. This prevents unexpected disappointment and ensures you’re manufacturing and machining aluminum products that have the characteristics you need, whether it’s superior corrosion resistance or good tensile strength. There are many to look at up close, but we’ll be deep-diving into 7075 aluminum and the qualities it brings to the table.
What Is Aluminum Alloy?
This is a style of aluminum alloy that came out of Japan in 1935. It originally was a popular pick for producing military aircraft, but its applications have since expanded, and you can find it in everything from bicycles to the gear you need for rock climbing.
Below, you can see an example of aluminum sheet metal cut into specific shapes.
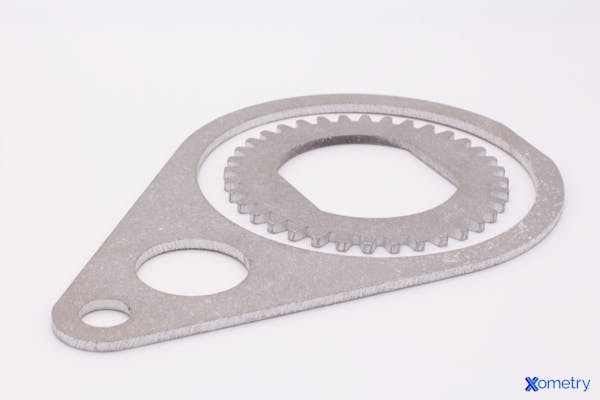
Although 7075 is primarily made of aluminum, it is an alloy, meaning there are lots of other small concentrations of other elements that make it what it is. You’ll find silicon, copper, magnesium, tin, and manganese in its composition (which we’ll go into further detail about below). Because of how its structure forms, it’s also an aluminum that has altered properties.
Composition
Here’s the breakdown of 7075’s composition:
- Aluminum: 87.1–91.4%
- Zinc: 5.1–6.1%
- Copper: 1.2–2.0%
- Manganese: 0.0–0.3%
- Silicon: 0.0–0.4%
- Iron: 0–0.5%
- Magnesium: 2.1–2.9%
- Chromium: 0.18–2.0%
- Titanium: 0–0.2%
- Other elements: 0.05–0.15%
Properties and Characteristics
If you’re wondering how 7075 compares overall to other types of aluminum, you’ll find that it has high strength, average corrosion resistance, and pretty poor weldability. Its high zinc and chromium also mean that it has decent ductility and toughness, too. In the table below, you can compare several variations of 7075 and how their characteristics stack up.
Property | 7075-O Aluminum | 7075-T6-T62 Aluminum | 7075-T73 Aluminum |
---|---|---|---|
Property Density | 7075-O Aluminum 2.7–2.85 g/cm3 | 7075-T6-T62 Aluminum 2.7–2.85 g/cm3 | 7075-T73 Aluminum 2.7–2.85 g/cm3 |
Property Tensile strength | 7075-O Aluminum 228 MPa | 7075-T6-T62 Aluminum 572 MPa | 7075-T73 Aluminum 505 MPa |
Property Yield strength | 7075-O Aluminum 103 MPa | 7075-T6-T62 Aluminum 503 MPa | 7075-T73 Aluminum 435 MPa |
Property Modulus of elasticity | 7075-O Aluminum 71.7 GPa | 7075-T6-T62 Aluminum 71.7 GPa | 7075-T73 Aluminum 72.4 GPa |
Property Brinell hardness scale (500g weight, 10 mm ball) | 7075-O Aluminum 60 | 7075-T6-T62 Aluminum 150 | 7075-T73 Aluminum 128 |
Property Elongation at break (12.7 mm test piece) | 7075-O Aluminum 16% | 7075-T6-T62 Aluminum 19% | 7075-T73 Aluminum 5% |
Property Shear modulus | 7075-O Aluminum 26.9 GPa | 7075-T6-T62 Aluminum 26.9 GPa | 7075-T73 Aluminum 27 GPa |
Property Shear strength | 7075-O Aluminum 152 GPa | 7075-T6-T62 Aluminum 331 GPa | 7075-T73 Aluminum 296 GPa |
Property Fatigue strength | 7075-O Aluminum N/A | 7075-T6-T62 Aluminum 159 MPa | 7075-T73 Aluminum 117 MPa |
Property Thermal expansion coefficient | 7075-O Aluminum 23.6 µm/m°C | 7075-T6-T62 Aluminum 23.6 µm/m°C | 7075-T73 Aluminum 23.2 µm/m°C |
Property Solidus | 7075-O Aluminum 477 °C | 7075-T6-T62 Aluminum 477 °C | 7075-T73 Aluminum 477 °C |
Property Liquidus | 7075-O Aluminum 635 °C | 7075-T6-T62 Aluminum 635 °C | 7075-T73 Aluminum 635 °C |
Property Annealing temperature | 7075-O Aluminum 413 °C | 7075-T6-T62 Aluminum 413 °C | 7075-T73 Aluminum 413 °C |
Property Solution temperature | 7075-O Aluminum 466–482 °C | 7075-T6-T62 Aluminum 466–482 °C | 7075-T73 Aluminum 256 °C |
Property Thermal conductivity | 7075-O Aluminum 173 W/mK | 7075-T6-T62 Aluminum 130 W/mK | 7075-T73 Aluminum 151 W/mK |
Property Specific heat capacity | 7075-O Aluminum 0.96 KJ/Kg°C | 7075-T6-T62 Aluminum 0.96 KJ/Kg°C | 7075-T73 Aluminum 0.96 KJ/Kg°C |
Property Applications | 7075-O Aluminum Military components and equipment, aircraft skins, bicycle parts, rocking climbing equipment, archery components, automotive parts | 7075-T6-T62 Aluminum Same | 7075-T73 Aluminum Same |
7075 Aluminum Alloy Properties
Choosing an Aluminum Grade
There are a few factors to think about when you’re weighing up different aluminum grades that’ll help you select the best one for the job:
- Strength: Think about, can your design accommodate the volume of material necessary to achieve the level of strength you’re after?
- Fatigue resistance: There are more fatigue-resistant aluminum grades than others, but there are also materials that are much more fatigue-resistant in general in comparison to aluminum as a whole. Understand the level you need and go from there.
- Processing: Not every alloy can handle every type of processing method out there, so be sure to check the grade you select is capable of handling forging and other processes.
- Construction: If you’re planning on constructing or assembling parts, be aware that some grades of aluminum alloy are poor for things like welding (others are better).
- Corrosion: There are a handful of aluminum grades with poor corrosion resistance and others with a decent level of it that can handle long-term exposure to wet and corrosive environments.
- Damage resilience: Some aluminum grades have a better elongation at break points than others, and these are essential when it comes to life-critical structures.
- Cosmetics: If aesthetics are important, take a look at the quality of surface finish you can get with different grades.
You can see another example of aluminum sheet metal in action below, as two metal plates are pictured made of the material.
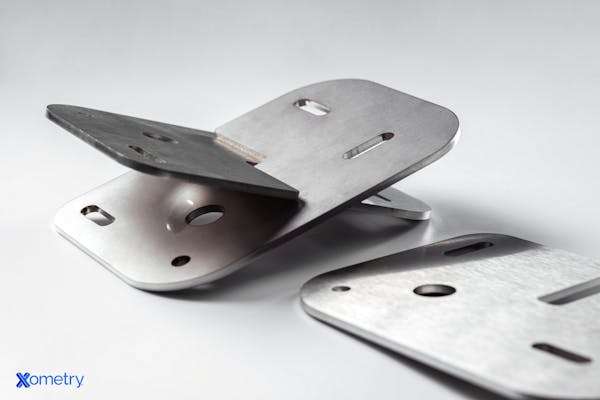
FAQs on 7075 Aluminum Alloy
How is 7075 aluminum different from 6061 aluminum?
There are a few things that make 7075 different from 6061. 6061 aluminum is known for its great machinability (and is often used for CNC machined parts), and it also has higher thermal and electrical conductivity. It also has higher concentrations of magnesium and silicon—hence why it’s categorized into this group.
Is 7075 aluminum as strong as steel?
While 7075 is a strong aluminum alloy, it’s not stronger than all types of steel. It can provide better strength than several types of mild and low-carbon steels, but less than carbon steels (and others).
What are the disadvantages of 7075 aluminum?
Although 7075 has several strengths, there are a few downsides to working with it. It’s a poor choice for welding and it doesn’t have the best corrosion resistance. It’s also not the best aluminum alloy for workability or cost.
How Xometry Can Help
There are a variety of services we offer that are suitable for aluminum alloy processing and production, including aluminum 3D printing, aluminum sheet metal fabrication, and custom extrusions. You can snag a free quote for all of these on our website.
Disclaimer
The content appearing on this webpage is for informational purposes only. Xometry makes no representation or warranty of any kind, be it expressed or implied, as to the accuracy, completeness, or validity of the information. Any performance parameters, geometric tolerances, specific design features, quality and types of materials, or processes should not be inferred to represent what will be delivered by third-party suppliers or manufacturers through Xometry’s network. Buyers seeking quotes for parts are responsible for defining the specific requirements for those parts. Please refer to our terms and conditions for more information.
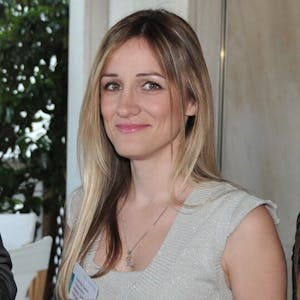