What Is Annealing?
Annealing is a heat treatment of metals or alloys that restores some of the material’s original physical properties. In particular, it increases ductility and decreases hardness. Annealing is done by raising the temperature of the metal to above its recrystallization temperature but below its melting point. This higher temperature gives enough energy to the metal to allow migration within the metal’s microstructures. This in turn results in dislocations being rectified, and internal stresses being relieved. Once the metal is cooled down again, its ductility will have been restored.
Annealing is understood to have been discovered as a heat treatment in the Middle Ages, around the 12th century. The word likely originated from the Middle English term “anelen”, meaning to set on fire or to bake. It was in Europe, through advances in blacksmithing, that craftsmen discovered that annealing (heating to above a certain temperature and then allowing the metal to cool) changed the properties of iron and steel.
Annealing is important because it significantly reduces the risk of metal cracking from work hardening, and counteracts the work hardening that occurs during forming of a metal component. Annealing allows the original physical properties of a metal to be restored after the component has been formed, removing grain deformations or internal stresses that would have been introduced during forming.
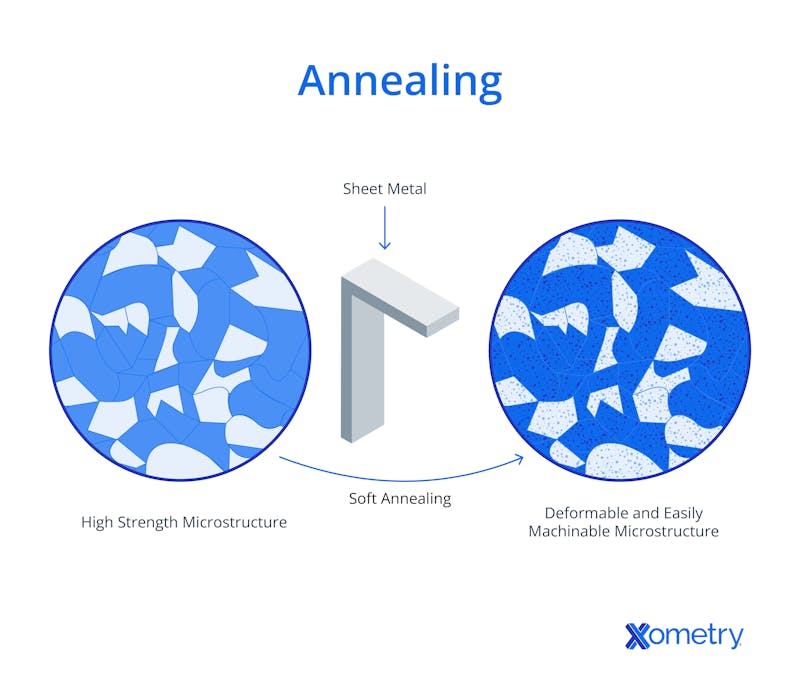
Types of Annealing
Listed below are common types of annealing:
- Stress Relief Annealing focuses on relieving the internal stresses in a metal component, usually used to correct any stresses that may have occurred during uneven cooling after casting. The metal is therefore heated up enough to allow the dislocations within the metal’s crystal lattice to be removed and then cooled slowly in still air. No phase transitions occur in stress relief annealing.
- Isothermal Annealing is the product of having accurate knowledge of an alloy’s temperature-time diagrams. The focus of this type of annealing is to maximize machinability. The alloy is held above the recrystallization temperature for some time (in steel, to fully austenitize it), then the temperature is dropped rapidly to a lower temperature, and held at a constant temperature there, (to allow the controlled decomposition of the austenite).
- Diffusion Annealing restores the homogeneity in the chemical composition of the alloy mix, eliminating segregation that may have occurred during casting. In steels, diffusion annealing fuses the iron and the carbide together. It is carried out at a high temperature, above the upper critical temperature, and held for a number of hours. Typically, further annealing may be required after diffusion annealing, in order to produce the desired grains.
- Incomplete Annealing is usually applied to hyper-eutectic steel. The steel is heated to around the upper basic temperature and then cooled slowly. It aims to achieve spherical pearlite within the hyper-eutectic steel, which has the benefits of improved machinability and decreased hardness.
- Complete Annealing is carried out by heating above the upper critical temperature, and then cooling slowly in a very controlled manner. It requires complete knowledge of the isothermal transformation diagram and the cooling transformation diagram of the alloy so that the desired microstructure of the alloy is achieved.
- Spherification Annealing focuses on achieving spheroid structures within the alloy. For high-carbon steels, this is created by forming carbide spheroids within ferrite. The purpose of this type of annealing is primarily to improve machinability, or else to assist in cold forming. Spherification annealing is usually carried out by heating the metal to below the lower critical temperature and holding it there for a number of hours. Cooling rates are not important.
- Recrystallization Annealing causes new, undeformed grains to form within the alloy structure, which grows and consumes the previously deformed grains. This occurs without phase change. It is typically applied to steels that have been cold worked, to restore ductility and to provide control over grain structure. It is carried out by heating to just below the lower critical temperature for a prolonged period of time, and then cooling.
How Annealing Works
Annealing works by giving the atoms in the steel microstructure sufficient energy to be able to migrate within the structure. This energy is provided by raising the temperature of the steel, and the migration is the key action taking place. This migration of atoms within the steel microstructure allows dislocations and internal stresses to be resolved. It also allows (if the temperature is high enough) for more grains to be formed. Allowing all the atoms to migrate to form a complete and regular crystal lattice restores the original physical properties of the metal. Such migration restores full ductility and removes any work hardening that may have been created previously.
There are different purposes of annealing, and so it can be applied in a few different situations such as those listed below:
1. Reverse Work Hardening
Annealing reverses the hardening of a metal, restoring its ductility and reducing hardness. Annealing “resets” the material after working, allowing the migration of atoms within the metal’s structure. In this way, the hardness caused by deformed grains and dislocations within the structure can be rectified. Using annealing after cold working a component restores its original mechanical properties of ductility and hardness.
2. Reduce Weld Solidification
Annealing improves the physical properties around a weld’s heat-affected zone (HAZ). When welding, the temperature on each side of the weld is high enough that some of the components in an alloy can start to come out of solution and precipitate (solidify), particularly carbide in steels. This results in brittleness and susceptibility to corrosion in the HAZ. Annealing reduces this solidification in the weld HAZ and restores some of the homogeneity and original mechanical properties to the welded area.
3. Enhance Electrical Conductivity
Annealing can even improve a metal’s electric conductivity as well as its magnetic properties. Again, this is due to the annealing process reducing dislocations and restoring the regular crystal lattice throughout the material. This provides a higher conductivity for electrical currents and magnetic fields.
4. Remove Residual Stresses
Annealing is applied to remove residual stresses within a metal component. The process of annealing allows the migration of atoms within the metal’s lattice structure to undo dislocations, and therefore remove any stresses from deformations.
The Stages of Annealing
1. Recovery Stage
The recovery stage is when the temperature of the metal is raised. As the temperature is raised, this provides energy to the atoms in the crystal lattice and allows them to migrate. As a result, the dislocations in the metal are removed, which in turn relieves stresses that were present in the metal, and restores the ductility of the material.
2. Recrystallization Stage
In the recrystallization stage, the temperature is raised to the recrystallization temperature, which is below the melting point. At this temperature, the crystal structure is reorganized and a new grain structure can begin to form. This grain structure is free of pre-existing stresses and returns the material to its original properties before working.
3. Grain Growth Stage
In the grain growth stage, the new grains develop and grow in size as the material cools. The controlled growth of these grains is dependent on the cooling conditions, such as the rate of cooling and the atmosphere in which it cools.
The annealing process takes a number of hours and can take as long as a day, depending on a number of factors. The two main factors that affect the duration of annealing are the metal (or alloy) being annealed, which in turn determines the hold time at the recrystallization temperature and the cooling time. These factors determine whether annealing is carried out as quickly as four hours, or whether it may need to be done over a 24-hour period.
Advantages and Disadvantages of Annealing
Metallic items that have been annealed have advantages over components that have not. The advantages of the annealing process are explained below:
- Restores the physical properties of the metal, and ductility in particular. The energy provided in heating allows the migration of molecules within the metal’s microstructure, and this removes work hardening and brittleness that may have been introduced during forming.
- Relieves internal stresses within a component after forming or working. In this way, annealing significantly reduces the risk of cracking in that component.
- Increases machinability. This is a product of the regular microstructure and the relief of internal stresses and work hardening.
- Allows dislocations in the metal’s crystal lattice to be rectified, which can in turn improve the electrical conductivity of the metal, as well as the magnetic properties.
- Some types of annealing allow control over the grain structure, by selecting what temperature to heat the alloy to, and how quickly to cool it down. Different phases and types of grains can be targeted with these parameters. The grains can also influence the physical properties of the alloy.
Annealing has some downsides that need to be weighed up against its benefits such as:
- It can be very time-consuming. Depending on the specific material to be annealed, and the type of annealing applied, the process can take more than 24 hours. Particularly slow, controlled cooling rates can extend the amount of time required to carry out annealing.
- Adds cost, not only in the equipment and labor needed to carry it out but also in the energy requirement to heat up each component and also to cool it (if forced cooling is used).
Examples of Annealing - Commonly Annealed Components
There are various components that are commonly annealed such as:
- Sheet metal (particularly that which has been cold rolled) is usually annealed to remove the work hardening and restore the sheet’s ductility. This allows further working and forming of the annealed sheet by bending, punching, or cutting.
- Manufactured components such as springs, washers, and saw blades are frequently annealed after forming to restore their physical properties and remove brittleness.
- Drawn aluminum can be subjected to more extreme, deep drawing which may otherwise tear or crack the metal.
Xometry provides a wide range of manufacturing capabilities including CNC machining, 3D printing, injection molding, laser cutting, and sheet metal fabrication. Get your instant quote today.
Disclaimer
The content appearing on this webpage is for informational purposes only. Xometry makes no representation or warranty of any kind, be it expressed or implied, as to the accuracy, completeness, or validity of the information. Any performance parameters, geometric tolerances, specific design features, quality and types of materials, or processes should not be inferred to represent what will be delivered by third-party suppliers or manufacturers through Xometry’s network. Buyers seeking quotes for parts are responsible for defining the specific requirements for those parts. Please refer to our terms and conditions for more information.
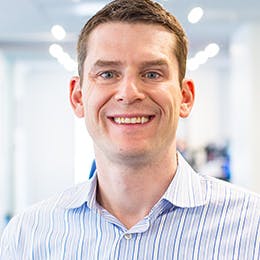