
Base Metals: Definition, Properties, Use, and Types
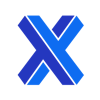
Base metals such as: iron, zinc, copper, and nickel are not so much prized as investments as they are for their practical uses. These metals are vital to industry due to their numerous qualities, including: conductivity, malleability, and corrosion resistance. Base metals are essential in our everyday lives and are often used in manufacturing, electrical wiring, and building.
There are a few varying definitions of base metals. A base metal is commonly used to describe metals that are abundant and affordable, unlike precious metals like gold and silver. In mining and economics, ‘base metals’ specifically denote industrial non-ferrous metals, excluding the precious category. This group comprises metals such as copper, lead, nickel, and zinc, which are fundamental to numerous applications.
This article will examine base metals' varied kinds, uses, and properties.
What Are Base Metals?
Base metals are common and inexpensive metals, such as: copper, tin, or zinc. They are distinguished from precious metals by their greater abundance and lower value. These metals are known for oxidizing or corroding relatively easily and are widely used in industry and manufacturing.
What Are the Different Properties of Base Metals?
Below are some common properties of base metals:
1. Density
Density, or mass per unit volume, is usually high for base metals. This characteristic is essential for uses requiring stability and weight, such as building materials. However, the high density could be a disadvantage for applications that require lightweight materials.
2. Strength
The strength of base metals, which is their ability to withstand force or load without breaking, makes them ideal for structural support and machinery. On the flip side, their strength can make them less ideal for applications requiring flexibility.
3. Luster
When newly prepared, polished, or shattered, many base metals have a luster or shiny look. This increases their aesthetic appeal for decorative reasons but may also make wear and corrosion more noticeable.
4. Versatility
Base metals can be alloyed and treated to suit a wide range of applications. While this is a significant advantage, it also means that their properties can vary widely depending on the treatment, which can complicate selection and use.
5. Melting Point
The melting points of base metals vary. Iron, for example, has a very high melting point, making it appropriate for use in high-temperature environments. Although they are simpler to cast and shape, metals with lower melting points might not be appropriate for high-temperature settings.
6. Thermal Conductivity
The thermal conductivity of base metals allows them to transfer heat efficiently, which is essential in applications like heat exchangers. However, this can be a disadvantage in situations in which thermal insulation is required.
7. Conductivity
Base metals such as copper are essential for electrical wiring and components because of their important attribute of electrical conductivity. The drawback of high-conductivity materials is that improper insulation can make them a safety risk.
8. Corrosion Resistance
Corrosion resistance varies among base metals. Some, like aluminum, form a protective oxide layer, while others, like iron, are prone to rust. Corrosion resistance is vital for longevity and maintenance costs but can add to the material cost.
9. Malleability and Ductility
Base metals can be bent without breaking because of their malleability and ductility, which is advantageous for manufacturing processes like rolling and forging. These characteristics, meanwhile, may lessen the material's strength.
10. Magnetic Properties
Some base metals exhibit magnetic properties, which are exploited in various technologies, from motors to data storage. However, magnetic materials can be problematic in environments in which magnetic fields must be controlled or minimized.
What Are Examples of Base Metals?
Base metals include: aluminum, copper, nickel, lead, tin, and zinc. These metals are more common and more easily extracted than precious metals, and they are used extensively in various industries due to their practical properties.
What Is the Use of Base Metals?
Base metals find extensive use in commercial and industrial domains, including manufacturing and building. Examples include the use of zinc to galvanize steel to prevent corrosion and copper in electrical wire.
What Industry Uses Base Metals?
The construction and manufacturing sectors heavily utilize base metals. They serve a wide range of functions, from structural components to electrical wiring, due to their durability and strength.
Are Base Metals Typically Used in Industrial Applications?
Yes, base metals are typically used in industrial applications. They are essential for their utility and ubiquity in various sectors, including: construction, manufacturing, and transportation.
What Are the Different Types of Base Metals?
The different types of base metals include:
1. Copper
Plumbing and electrical wiring are perfect applications for copper since it is a highly conductive and ductile metal. It is well renowned for its corrosion resistance as well as its electrical and thermal conductivity. Copper is used in a variety of applications, including electronics and construction. It’s also antimicrobial and recyclable. However, it can be expensive and is a finite resource. End products include electrical wires and pipes.
2. Aluminum
Aluminum is lightweight with a high strength-to-weight ratio, making it ideal for transportation and construction. It is corrosion-resistant and can be recycled. Aluminum is used in packaging, transportation, and construction. Cons include it being less strong than some metals and energy-intensive to produce. End products include: cans, foils, and airplane parts.
3. Zinc
Zinc is well renowned for its capacity to galvanize other metals, giving them protection from corrosion. It is utilized in the production of alloys including: brass, die-casting, and galvanizing steel. For human health, zinc is also necessary. It is not as strong as some metals, though, and it can corrode in some situations. Coins and zinc-plated steel are examples of final products.
4. Nickel
Nickel is tough, malleable, and resistant to corrosion, often used to strengthen alloys like stainless steel. It’s used in batteries, electronics, and as a catalyst. Nickel is recyclable but can be expensive and difficult to machine. End products include stainless steel and rechargeable batteries.
5. Lead
Lead is a thick, pliable material that has long been utilized in radiation shielding and batteries. Moreover, it is soundproof. However, lead is hazardous, so there are risks to human health and the environment. Batteries and protective gear are examples of final goods.
6. Tin
Tin is soft, malleable, and corrosion-resistant, often used to coat other metals. It’s used in soldering, plating, and making alloys like bronze. Tin is recyclable but has a lower melting point and strength compared to other metals. End products include tin cans and solder.
7. Iron
The most common metal, iron, is utilized to create alloys like steel. Constructed and utilized in production, it is robust and magnetic. Iron rusts readily in the absence of protective treatment. Machines and building supplies are examples of final products. However, iron is prone to rusting if not properly treated or protected.
In contrast, nonferrous metals — those without iron content like copper, lead, nickel, and zinc — are key in mining and economics. They don’t rust like iron and are essential in electrical wiring, batteries, and roofing, among other uses.
8. Chromium
Chromium enhances the hardness and corrosion resistance of steel. It is used in stainless steel, dyes, and pigments. Chromium is durable but can be expensive and challenging to work with. End products include stainless steel and chrome plating.
9. Manganese
Manganese improves the strength and toughness of steel and aluminum alloys. It is used in steel production and batteries. Manganese is abundant but can be brittle and prone to oxidation. End products include steel and dry-cell batteries.
10. Magnesium
Magnesium is used in alloys for the automotive and aerospace sectors because it is strong and light. Its flammability and reactivity can potentially be a disadvantage. Automobile and aircraft components are examples of end products.
How To Choose Which Types of Base Metals To Use
When selecting a base metal for your project, consider the following factors:
- Determine the metal's intended use, as different metals excel in various applications.
- Assess the metal's physical and chemical properties, such as: strength, ductility, and corrosion resistance.
- Ensure the metal is compatible with other materials it will contact.
- Consider the environmental conditions, like temperature and exposure to elements.
- Factor in the cost, as some metals are more expensive than others.
- Check the availability of the metal in your region.
- Evaluate how easy the metal is to machine or fabricate.
- Be aware of any regulations or standards that apply to the metal in your industry.
What Types of Base Metals Are Used for Laser Cutting?
Common base metals for laser cutting are: copper, brass, titanium, aluminum, carbon steel, and galvanized steel. The reason for selecting these metals is their capacity to efficiently absorb laser energy and melt, enabling accurate cutting.
What Types of Base Metals Are Used for Laser Engraving?
Metals suitable for laser engraving include: stainless steel, steel, aluminum, titanium, brass, and copper. These metals can be etched with a laser to create permanent marks for identification or decoration.
To learn more, see our full guide on How to Do Laser Engraving.
What Types of Base Metals Are Used for CNC Plasma Cutting?
Materials like: aluminum, mild steel, stainless steel, brass, copper, and cast iron are used in CNC plasma cutting. Using ionized gasses to melt the metal and produce precise cuts, plasma cutting is perfect for these conductive metals.
What Is the Advantage of Using Base Metals?
Base metals are inexpensive, abundant, heat resistant, strong, and good conductors of electricity and heat. They have a long life span and can be easily shaped and joined, making them versatile for various industrial applications.
What Is the Disadvantage of Using Base Metals?
The drawbacks of base metals are weight, rusting, and corrosion. Certain base metals have a high cost, and if not handled carefully, their ability to bend can occasionally work against them.
Are Base Metals Vulnerable to Price Volatility in the Market?
Yes, base metals are vulnerable to price volatility in the market. Factors such as supply disruptions, geopolitical tensions, and economic conditions can lead to significant price fluctuations.
What Is the Difference Between Base Metals and Actinides?
Base metals are low-cost, widely used metals that tarnish and corrode over time. The filling of the 5f electron shell is what distinguishes actinides, a class of radioactive metals whose atomic numbers range from 89 to 103. Actinides' radioactivity makes them mostly useful in nuclear applications.
Summary
This article presented base metals, explained them, and discussed their various applications. To learn more about base metals, contact a Xometry representative.
Xometry provides a wide range of manufacturing capabilities and other value-added services for all of your prototyping and production needs. Visit our website to learn more or to request a free, no-obligation quote.
Disclaimer
The content appearing on this webpage is for informational purposes only. Xometry makes no representation or warranty of any kind, be it expressed or implied, as to the accuracy, completeness, or validity of the information. Any performance parameters, geometric tolerances, specific design features, quality and types of materials, or processes should not be inferred to represent what will be delivered by third-party suppliers or manufacturers through Xometry’s network. Buyers seeking quotes for parts are responsible for defining the specific requirements for those parts. Please refer to our terms and conditions for more information.
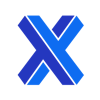