Ductility and malleability are two important parameters of engineering materials. In general, most metals are both malleable and ductile. Ductility is the ability of a material to plastically deform without breaking when tensile (stretching) stress is applied to it. Malleability is a similar property, but it expresses the ability of a material to plastically deform without breaking under compressive rather than tensile stress. This article will explain the key differences between ductility and malleability.
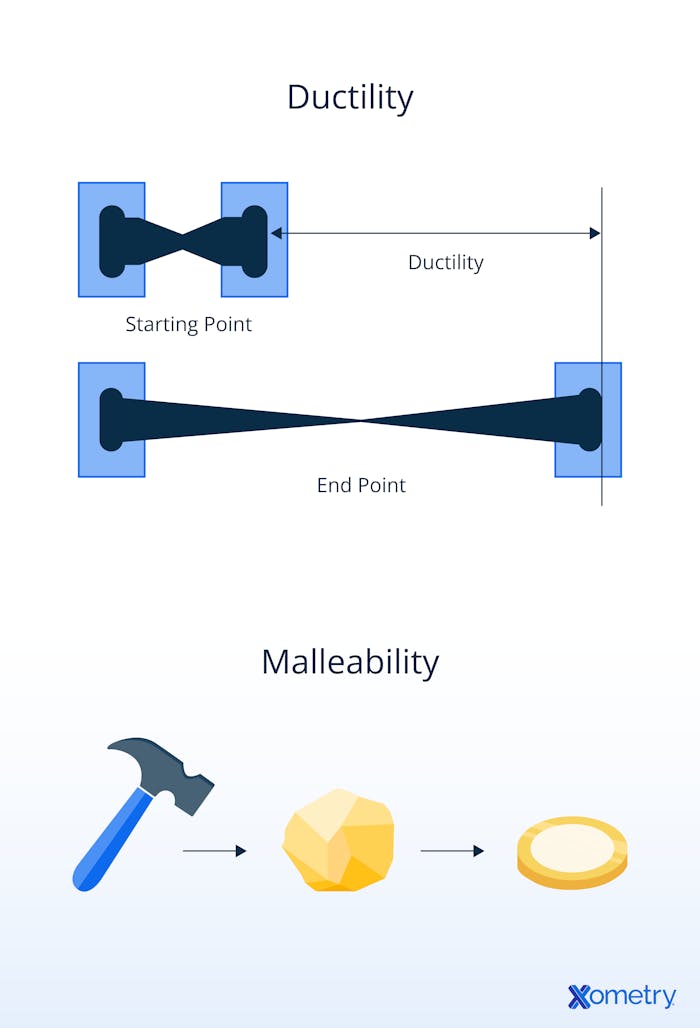
What Is Ductility?
Ductility is the property of a material that indicates how easily it will plastically deform (but not break) under tensile (pulling or stretching) stress. It represents the ability to undergo significant plastic (permanent) deformation. A ductile material can be easily drawn into shapes such as wires without fracturing. For more information, see our guide on Ductility.
How Does Ductility Work?
Ductility is possible due to the arrangement of the atoms within a solid’s structure. In metals particularly, layers of repeating atoms tend to lie on each other. Therefore, as the metal is stretched and tensile stress is induced, the atoms can slip over each other and deform without the overall structure breaking.
What Is the Importance of Ductility?
Ductility is an important property in the engineering of safe, resilient structures that deform before breaking, as well as a requirement for many manufacturing processes. Ductility is important, for example, for the creation of intermediate product forms such as a copper wire. Wire fabrication requires copper (or other metals such as aluminum) to be drawn through a die which gradually decreases the diameter and increases the length of the wire to the desired level. This creates a high tensile stress on the material, but its ductility allows it to deform to the diameter of the wire to be produced.
What Is the Purpose of Measuring Ductility?
The purpose of measuring ductility is to understand the ability of each material to deform rather than break under tensile stress. Once this ductility is measured and understood, it allows material selection for various engineering applications. Ductility measurements can also be used as a means of quality control, particularly for metal alloys that may have been selected for high ductility. Each batch can be tested to ensure that this important characteristic is within specification. Finally, measuring ductility allows materials to be accurately modeled in computer designs of future structures, to accurately calculate the optimum design.
How Is Ductility Measured?
Ductility is measured through a tensile strength test. A flat or round specimen with a grip section on each end and a smaller gauge section in the middle, suggesting a dog bone or a dumbbell, is held tight by upper and lower jaws, one of which is connected to a load cell. The load cell applied tensile stress in a slow and controlled manner. A stress-strain curve can then be plotted as the test specimen is stretched to the point of fracture. Ductility is inferred from a measurement of elongation — the percentage change in the final gauge section length compared to its original length.
What Are the Benefits of Measuring Ductility of Materials?
Measuring the ductility of materials has the following three benefits:
- Careful Material Selection: Ductility is a crucial parameter in some manufacturing applications. Selecting a material that is known with confidence to have sufficient ductility may be necessary for the successful implementation of a project.
- Accurate Engineering Design: If the ductility of a material has been accurately measured for the intended service conditions of an application, it allows more accurate finite element modeling of designs. Better modeling of structures and components can shorten total design and test time, and result in parts and systems with better durability at a lower cost.
- Material Quality Control: For materials where ductility is a critical property, the ductility measurement can be used as a quality control parameter to ensure that any given batch of material is within specification.
What Are Examples of Ductile Materials?
Below is a list of the three most ductile metals:
- Gold
- Silver
- Platinum
These three precious metals are all highly ductile and can be pulled into very fine wires. These can be used in precision industrial applications or in jewelry.
What Is Malleability?
Malleability is the ability of a material to deform without breaking while under compression. For instance, a malleable metal can be worked with a hammer and beaten.
How Does Malleability Work?
Malleability is controlled by how atoms within a metal move over one another as the metal is compressed. Depending on the atomic structure and the grains within the metallic structure, the atoms can slide past each other into new positions, and thus compress without cracking. However, some metal grain structures do not easily allow atoms to move over each other. Therefore, as compressive stress is induced, fractures begin to appear. These fractures can be at grain boundaries, but the mechanism for failure can be more complex — fracture will actually occur due to highly localized tensile stresses, usually introduced by surface discontinuities.
What Is the Importance of Malleability?
Malleability is important for metalworking and rolling or forming metals into final product shapes and forms. Many metals are available in bars, rods, sheets, tubes, or profiles that are rolled. The shapes and forms that can be produced in a given metal depend on its malleability.
What Is the Purpose of Measuring Malleability?
The purpose of measuring malleability is to understand how well each material can withstand deformation under compressive stress without fracturing. Further, this plays a role in the selection of optimal materials for engineering applications. The measurement of malleability also provides some quality control of materials that are commonly used for their compressive strength and malleability.
How Is Malleability Measured?
Malleability is usually measured by inferring it from hardness. Hardness measures the resistance of a material to localized plastic deformation. Brinell and Rockwell are the two popular methods of measuring hardness.
Brinell hardness is measured by pushing a spherical ball into the surface of the material with a constant force and measuring the diameter of the resulting indentation. To measure Rockwell hardness, a differential depth of penetration is measured. First, a standard load is applied with a standardized tool to make an initial indentation, and then, a larger load is applied to make a deeper penetration. The increase in depth is used to calculate the Rockwell hardness.
Malleability can also be inferred from compressive strength tests, where a cylinder of material is squeezed between two plates until it breaks or bends. The stress-strain curve from this test provides information about the compressive strength of the material.
What Are the Benefits of Measuring Malleability of Materials?
The following three benefits arise from the measurement of the malleability of materials:
- Facilitates Optimal Material Selection: Knowing the malleability of various materials allows the best material to be selected for particular applications that require high malleability, such as forging and stamping.
- Provides Data for Accurate Engineering Design: In order to model a structure or manufacturing process, it is vital to have accurate data. This data allows designs to be optimized.
- Material Quality Control: It is important for consumers and end-users to know that a material’s malleability is within specification, particularly in materials where malleability is a key attribute. The measurement of malleability can therefore be used as a quality control parameter.
What Is an Example of Malleable Materials?
The following are examples of malleable materials:
- Gold: A popular material that has been worked on for centuries.
- Aluminum: Easily rolled into thin sheets, such as the common aluminum foil.
- Copper: Can be worked into sheets for architectural and decorative purposes.
What Are the Key Differences of Ductility and Malleability?
Table 1 below outlines some of the key differences between ductility and malleability:
Characteristic | For Ductility | For Malleability |
---|---|---|
Characteristic Type of Stress | For Ductility Tensile | For Malleability Compressive |
Characteristic Form of Deformation | For Ductility Plastic | For Malleability Plastic |
Characteristic Applications | For Ductility Drawing wires | For Malleability Beating out sheets |
Characteristic Measuring Techniques | For Ductility Tensile strength test (stress-strain curve), elongation | For Malleability Compressive strength test, hardness testing |
Characteristic Materials | For Ductility Gold, silver, platinum | For Malleability Gold, aluminum, copper |
Characteristic Process | For Ductility Drawing/extruding | For Malleability Rolling, hammering, beating, smashing, stamping |
Characteristic Temperature Dependence | For Ductility Higher ductility at higher temperatures (more brittle at lower temperatures) | For Malleability Higher malleability at higher temperatures (more brittle at lower temperatures) |
Characteristic Crystal Structure | For Ductility Regular crystal lattice with atoms able to “slip” past each other | For Malleability Regular crystal lattice with atoms able to “slip” past each other |
Are Metals Ductile or Malleable?
Most metals are both ductile and malleable. This is because the structure of most metals — repeating atoms layered on top of each other — allows for relatively easy movement between them. These layers tend to slip or roll over each other. Most metals deform well, whether being stretched (exhibiting ductility) or being compressed (which is malleability). For more information, see our guide on Metal.
Can a Metal Be Ductile but Not Malleable?
No, generally if a metal is ductile, it is also malleable (at the same temperature). Most metals’ structures allow both qualities simultaneously — if the atomic structure allows for ductility (deformation under tensile stress), then it will also allow for malleability (deformation under compressive stress). However, the converse is not always true. A metal that is malleable may not necessarily be ductile. Lead is a common example of a highly malleable metal that has low ductility — it will fracture easily if pulled.
Is Gold Malleable?
Yes, gold is highly malleable. It is the most malleable metal. It is easily beaten out into thin sheets. Gold foil (gold leaf) was first used as early as 8000 years ago as a decorative overlay or gilding and has been widely used by multiple civilizations since.
Is Steel Ductile?
Yes, generally steel is ductile, although it does depend on the alloy and the temperature. Steel is an alloy of iron, carbon, and other elements, and certain (low carbon) steel alloys can be designed to have higher ductility in order to be easily stretched and drawn into wire and pipe. However, some steel alloys (particularly high carbon alloys) are more brittle, and would not be considered ductile. Temperature also influences the ductility of a material, so it is also important to note the temperature when classifying a material as ductile. Low temperatures (typically below freezing for metals) cause a transition from ductile to brittle.
Summary
This article presented ductility vs. malleability, explained what each is, and discussed their various key differences. To learn more about material comparsions, contact a Xometry representative.
Xometry provides a wide range of manufacturing capabilities and other value-added services for all of your prototyping and production needs. Visit our website to learn more or to request a free, no-obligation quote.
Disclaimer
The content appearing on this webpage is for informational purposes only. Xometry makes no representation or warranty of any kind, be it expressed or implied, as to the accuracy, completeness, or validity of the information. Any performance parameters, geometric tolerances, specific design features, quality and types of materials, or processes should not be inferred to represent what will be delivered by third-party suppliers or manufacturers through Xometry’s network. Buyers seeking quotes for parts are responsible for defining the specific requirements for those parts. Please refer to our terms and conditions for more information.
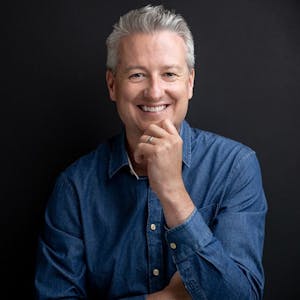