The elastic limit is a fundamental mechanical property of solid materials that defines the maximum stress a material can sustain without undergoing permanent (plastic) deformation. It marks the boundary between the elastic deformation region—where the material will return to its original shape when the load is removed—and the plastic deformation region, where the material will undergo irreversible changes in shape or size. Stress beyond the elastic limit causes the material to yield, resulting in permanent structural changes. This threshold is a critical parameter in mechanical design and material selection, especially in applications involving cyclic loading or precision components.
This article covers the definition and significance of the elastic limit, explains its behavior under stress, and describes its relationship to Hooke’s Law, which governs elastic behavior. It also provides a practical overview of methods used to determine the elastic limit through material testing procedures.
What Does Elastic Limit Mean?
The elastic limit is the maximum amount of stress that can be applied to a material before the onset of plastic deformation. When the stress applied to a material is below the elastic limit, the material will return to its original shape once the stress is removed from the object. Conversely, if a stress greater than the elastic limit is applied to a material, the material will remain deformed even when the external force is removed.
What Is the Importance of the Elastic Limit?
The elastic limit is an essential property of any material because it determines the amount of stress a material can withstand before suffering permanent damage. It indicates where elastic behavior ends and plastic deformation begins. This transition is significant because it delineates the range within which a material can return to its original shape upon removal of the applied stress. Stresses beyond the elastic limit cause materials to flow or yield. For brittle materials, the stress at the elastic limit is at or close to the fracture strength, because brittle materials exhibit little or no plastic deformation.
How Does an Elastic Limit Work?
To understand how the elastic limit works, let’s consider an object with an external force acting on it. When the external force is applied, the bonds holding the object's atoms together are stretched. This stretching creates an internal reaction force as the atoms resist being pulled apart. As long as the external stress remains below the elastic limit of the material, the atomic bonds are only stretched, and not broken. When the externally applied force is removed, the stretching of the atomic bonds is relieved, and the material returns to its original size and shape. In essence, the material will behave like a spring.
On the other hand, if the applied force is more than the strength of the interatomic bonds that can resist, the deformation becomes permanent. The object will no longer be able to regain its original shape after the force has been removed. This is termed plastic deformation.
The elastic limit refers to the point where the material transitions from the elastic deformation region to the plastic deformation region, as shown in the stress-strain curve of Figure 1 below
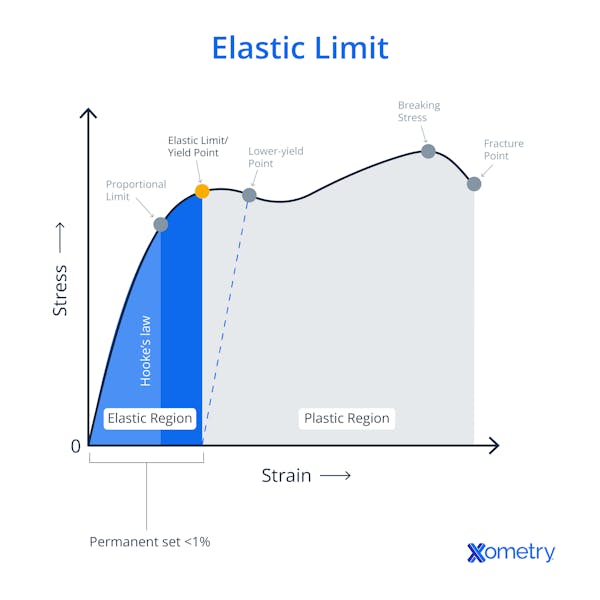
This is the point at which permanent deformation or even failure (in brittle materials) initiates.
What Is Hooke's Law?
Hooke's Law states that within the elastic limit of a material, the strain of that material is directly proportional to the applied stress. When elastic materials are stretched, the atoms and molecules inside deform until they're under stress. When that stress is removed, they'll return to their original state.
We can express this relationship mathematically using Hooke's Law, which is written as:
F = kx
Where:
- F is the force
- x is the extension in length
- k is the constant of proportionality, otherwise known as the spring constant, measured in N/m
How Does an Elastic Limit Relate to Hooke's Law?
Hooke's Law describes the linear relationship between the applied force (stress) and the resulting amount of deformation (strain) in a material, at stress levels below the elastic limit.
According to Hooke's Law, for small deformations, the stress and strain are proportional to each other. This linear relationship holds within the elastic limit of the material. As long as the applied stress does not exceed the elastic limit of the material, the material will deform elastically and will return to its original shape once the applied stress is removed.
How To Find the Elastic Limit of a Material?
The elastic limit for a material can be determined following these steps:
- Prepare a standard test sample shape that is free of any defects or damage, as these can affect the results.
- Apply a known amount of stress to the sample using a mechanical testing machine or similar instrument. The specific method of applying stress can vary depending on the type of material and testing method being used. However, the stress is typically increased gradually until the material begins to exhibit permanent deformation. The point at which permanent deformation initiates is known as the elastic limit of the material.
- Measure the resulting strain (deformation) as the stress is increased. This can be done using displacement sensors or strain gauges.
- Plot the results with stress on the y-axis and strain on the x-axis. This is known as a stress-strain curve, which illustrates how the sample responds to varying levels of stress.
- Determine the point where the material starts to exhibit permanent deformation. This is the elastic limit of the material and is typically close to, or equal to, the point where the stress-strain curve transitions from linear to non-linear behavior. Be sure to record all the observations and measurements accurately for analysis.
What Is the Formula for Elastic Limit According to Hooke's Law?
Hooke's Law describes the proportional relationship between stress and strain up to the proportional limit, while the elastic limit is the point beyond which the material undergoes permanent deformation.
The formula for Hooke's Law, adapted from force units to stress units, is:
σ = Eε
Where:
- σ is the stress applied to the material
- E is Young's modulus of the material
- ε is the resulting strain in the material
The relationship between Hooke’s law and the elastic limit, however, cannot be expressed through an equation. The elastic limit is a value that is tested experimentally and not calculated through an equation.
Can Hooke's Law Accurately Describe Material Behavior Beyond Its Elastic Limit?
No, Hooke’s Law does not accurately describe material behavior beyond its elastic limit. Hooke's Law assumes that material behaves elastically, meaning that it will return to its original shape once the applied stress is removed. Beyond the elastic limit, the material will undergo permanent deformation, meaning that it will not return to its original shape, and the relationship between stress and strain is no longer linear.
Hooke's Law is only applicable within the proportional limit of a material, where the stress and strain are proportional and the material behaves elastically. Beyond the elastic limit, the material's behavior becomes more complex, potentially involving plastic deformation, yielding, or fracture, depending on the specific material and the magnitude of the applied stress.
What Is an Example of an Elastic Limit?
An example of an elastic limit is the elastic limit of steel, which is 8 x 108 N/m2.
Does Steel Have a High Elastic Limit?
Yes. Steel has a relatively high elastic limit of about 8 x108 N/m2, depending on the grade. It can withstand a significant amount of stress before undergoing plastic deformation. This property makes steel highly desirable in applications where strength and durability are required, such as in building construction, bridges, and heavy machinery.
Does Titanium Have a High Elastic Limit?
Yes, Titanium (Ti) has a high elastic limit. The elastic limit of titanium can vary depending on the specific alloy and processing method used. The elastic modulus of Ti alloys ranges from 55 to 114 GPa, which is about half that of steel but is still considered high for a lightweight metal. A higher elastic modulus means that the elastic limit of titanium and its alloys will also be reasonably high, even though it is not one of the materials with the highest known elastic limits.
What Material Has a Low Elastic Limit?
Materials with low elastic limits are those that undergo permanent (plastic) deformation when subjected to relatively low levels of stress. These materials do not return to their original shape once the stress is removed. Polymers such as certain plastics often have low elastic limits and can deform significantly under modest mechanical loads. Rubber, while a polymer, behaves differently; it is highly elastic and can endure large strains without permanent deformation, so its classification depends on the specific type and context of use.
Glass, although hard and brittle, also demonstrates a low tolerance to stress beyond its elastic range. It does not undergo plastic deformation; instead, it fractures once the elastic limit is exceeded. This characteristic makes it behave as though it has a low elastic limit, as it cannot absorb much stress without failing.
What Are the Factors That May Affect the Elastic Limit of a Material?
The elastic modulus is an intrinsic property of a material, and there are not a lot of factors that can change it. However, factors that can affect the elastic properties of a material include:
- Fatigue: Fatigue describes the progressive and localized structural damage that occurs when a material is subjected to cyclic loading. As cracks initiate and propagate, the effective cross-sectional area of the material is reduced. This results in an apparent decrease in stiffness and elastic performance. While the true elastic modulus remains unchanged, the perceived elastic limit may decrease due to the compromised structural integrity of the material.
- Pressure: External pressure can alter the interatomic spacing within a material, affecting its elastic response. This effect is non-linear and can significantly influence materials subjected to high-pressure environments (e.g., deep-sea or high-pressure gas systems).
- Change of Length: The change of length, i.e, ∆l, affects the elastic limit, as strain is the ratio of change of length to initial length of the material.
- Elongation: Elongation behavior is influenced by Young’s modulus, which is a measure of stiffness. Materials with a lower modulus exhibit greater elongation under stress, potentially approaching their elastic limit more quickly under the same loading conditions.
- Composition: The composition of a material can significantly affect its mechanical properties, including its elasticity, and ultimately its elastic limit. When alloying elements are added to materials, they can cause variations in their elastic properties. The extent to which the elasticity increases or decreases depends on the type of impurity that is introduced.
- Temperature: Most materials exhibit reduced elasticity at elevated temperatures due to increased atomic mobility, which facilitates plastic deformation. Conversely, at lower temperatures, materials typically become more brittle, sometimes increasing the elastic limit but reducing toughness.
- Environmental Exposure: Long-term exposure to corrosive chemicals, radiation, or moisture can cause degradation of material properties. This can result in premature yielding or embrittlement, reducing the material’s elastic limit over time.
- Surface Defects: Microscopic flaws such as scratches, cracks, or voids act as stress concentrators. These imperfections can significantly lower the local elastic limit, leading to the earlier onset of plastic deformation under otherwise manageable loads.
What Are the Advantages of Elastic Limit?
The advantages of understanding the elastic limit of materials are listed below:
- The elastic limit provides valuable information about the behavior of materials under stress. This information can be used to improve the design and performance of structures and components.
- Knowing the elastic limit helps engineers and designers select the best material for a specific application by providing information about the material's ability to withstand stress without undergoing permanent deformation. This can lead to improved performance and reliability of products and structures.
What Are the Disadvantages of Elastic Limit?
The disadvantages of an elastic limit are as follows:
- Sets a limit on the amount of stress a material can withstand before it undergoes permanent deformation or failure. This can make the material unsuitable for high-stress applications or environments.
- Can limit design flexibility by constraining the choice of materials that can safely withstand expected stresses while also meeting other design criteria, such as weight, cost, and appearance.
What Is the Difference Between an Elastic Limit and Yield Strength?
The elastic limit is the maximum stress a material can endure without sustaining permanent deformation. It is the point on a stress-strain curve beyond which the material cannot return to its original shape when the stress is removed. It is the stress beyond which the material's elasticity is permanently lost and begins to exhibit plastic deformation.
Yield strength, on the other hand, is the stress at which a material begins to exhibit plastic deformation. It is generally defined as the stress at which 0.2% plastic strain has occurred to standardize and facilitate comparison between materials that do not have well-defined yield points.
To learn more see our full guide on, Yield Strength.
What Is the Difference Between an Elastic Limit and a Proportional Limit?
The elastic limit and the proportional limit are two different concepts related to the behavior of materials under stress. The elastic limit is the maximum stress that a material can be stretched without undergoing permanent deformation after the stress is removed. In other words, if the stress applied to a material does not exceed its elastic limit, the material will return to its original shape after the stress is removed, with no permanent deformation.
The proportional limit, on the other hand, is the maximum stress at which a material exhibits a linear relationship between stress and strain. In other words, up to this point, the material behaves elastically, and the strain is directly proportional to the applied stress. Once the proportional limit is exceeded, the material begins to deform plastically, and the relationship between stress and strain becomes non-linear.
Summary
This article presented elastic limit, explained what it is, and discussed how it works and provided examples of it To learn more about elastic limit, contact a Xometry representative.
Xometry provides a wide range of manufacturing capabilities and other value-added services for all of your prototyping and production needs. Visit our website to learn more or to request a free, no-obligation quote.
Disclaimer
The content appearing on this webpage is for informational purposes only. Xometry makes no representation or warranty of any kind, be it expressed or implied, as to the accuracy, completeness, or validity of the information. Any performance parameters, geometric tolerances, specific design features, quality and types of materials, or processes should not be inferred to represent what will be delivered by third-party suppliers or manufacturers through Xometry’s network. Buyers seeking quotes for parts are responsible for defining the specific requirements for those parts. Please refer to our terms and conditions for more information.
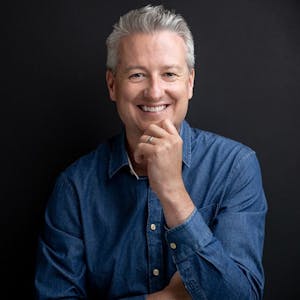