When it comes to electromagnetic applications and electrical equipment, electrical steel is the real MVP thanks to its unbeatable magnetic properties. If you’re thinking of using it, there are a lot of technical details to know (type, forms, properties, etc.), so we’ve broken it all down for you below.
What is Electrical Steel?
With iron as its main ingredient and up to 6.5% silicon, electrical steel is classed as an iron-silicon alloy. Its standout feature is its magnetism thanks to the silicon content (and why it’s also known as silicon steel—one of its several monikers). It’s a type of low-carbon alloy (typically under 0.05%) to minimize magnetic losses. The amount of silicon added plays a big role in what it’s used for. For example, silicon levels around 2–3.5% are ideal for non-oriented electrical steel used for electric motors and generators. If it has 3–4.5% silicon, it’s used for grain-oriented electrical steel, which is specially processed for transformer cores, where reducing energy loss is important.
The most common form it comes in is thin sheets, which are usually coated with an insulator for lamination—which is the reason for another of its aliases, “lamination steel.” This involves stacking several sheets together, while keeping them protected from each other to cut down on energy losses caused by eddy currents. The magic is all in the combination of iron, which helps guide magnetic flux, and silicon, which increases electrical resistance and reduces energy waste. To top it off, its crystal structure is aligned in a way that allows for fast magnetization and demagnetization—something that also adds to its usefulness in motor and transformer cores.
Advantages
- Durable, can handle mechanical stresses without deforming at low-silicon levels
- Low core loss that minimizes energy waste
- More cost-effective than some advanced magnetic materials (i.e., neodymium iron boron)
- Higher magnetic permeability than plain carbon steel, allowing magnetic fields to pass through easily
- Low electrical conductivity
- Minimal heat generation keeps devices cooler
Disadvantages
- High cost ($1,000–2,000/ton) compared to 1020 carbon steel ($300–550/ton)
- Could rust, so protective coating (i.e., varnish, oxide) needs to be applied everywhere (even in small crevices)
- Brittle at high silicon levels
- Limited to electrical and magnetic purposes, can’t be used for structural or general-purpose applications
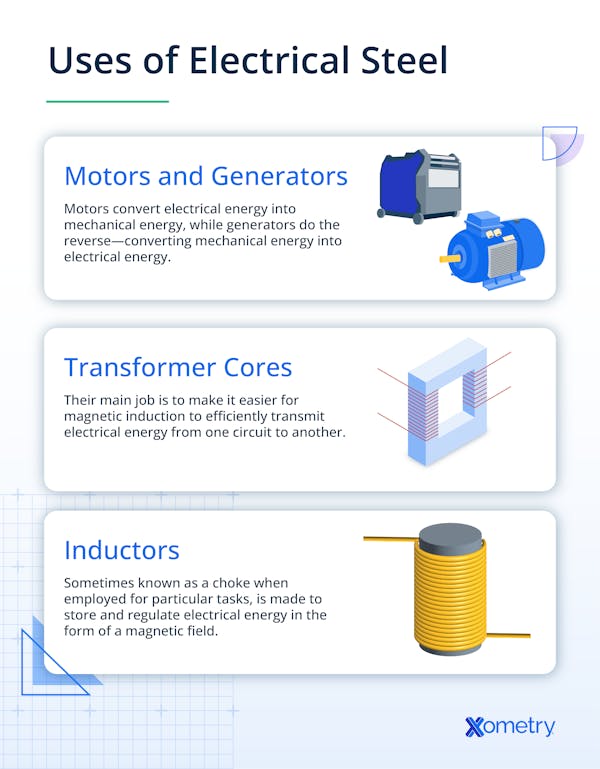
A Brief History
Silicon steel was first used for electrical applications in the late 1800s, when English metallurgist Sir Robert Hadfield, who discovered manganese, found that silicon increased the magnetic permeability of iron. The correlation between magnetic permeability and crystallographic orientations in iron single crystals was discovered in 1926 by Honda and Kaya, which led to subsequent developments to silicon steel. It wasn’t until 2008 that Baosteel—after inventing the technologies and machinery for high-grade, effective non-oriented silicon steel production—managed to accomplish a rapid, all-encompassing product upgrade.
How it’s Made
To make electrical steel, the raw materials (i.e., iron ore, scrap steel) are melted together in an electric arc furnace, and then the appropriate amount of silicon is added. The mixture is hot-rolled into thin sheets and refined. This entails deoxidization (removing the oxygen from the molten mix) and vacuum degassing to up the purity and give it better electrical properties. After that, it’s annealed to boost the magnetism.
Types of Electrical Steel
There are two main electrical steel types, non-grain-oriented (NGOES) and grain-oriented (GOES). They both have high permeability and low core loss, but where they differ is in their grain structure and magnetic properties. NGOES has randomly oriented crystal grains, making its magnetism uniform in all directions (isotropic), allowing it to adapt well to changing magnetic fields. GOES, though, has a deliberately aligned crystal structure (anisotropic) for magnetization in a specific direction. This makes it good for fixed-field applications but not so much for constantly changing magnetic fields.
Property | NGOES | GOES |
---|---|---|
Property Composition | NGOES Carbon (0.01% or less), silicon (~3.0–3.5%), aluminum (≤0.5%), manganese (≤0.5%) | GOES Carbon (~0.003%), silicon (~3.0–3.5%), aluminum (≤0.5%), manganese (≤0.5%) |
Property Density | NGOES 7.65 g/cm³ | GOES 7.65 g/cm³ |
Property Thickness | NGOES 0.23–0.35 mm | GOES 0.18–0.35 mm |
Property Ultimate tensile strength (angle to rolling direction 0-90°) | NGOES 361–405 MPa | GOES 361–405 MPa |
Property Thermal conductivity (20–600°C) | NGOES 70–0.0715 Cal/cm²·Sec·°C/cm | GOES 70–0.0715 Cal/cm²·Sec·°C/cm |
Property Electrical resistivity | NGOES 48 Microhm-cm | GOES 45–50 Microhm-cm |
Property Thermal coefficient of resistivity (20–145°C) | NGOES 0.047 Microhm-cm/°C | GOES 0.047 Microhm-cm/°C |
Property Heat capacity | NGOES 0.12 Cal/g/°C | GOES 0.12 Cal/g/°C |
Property Curie temperature | NGOES 730°C | GOES 750°C |
Property Thermal expansion (20–100°C) | NGOES 11.9 × 10⁻⁶ cm/cm/°C | GOES 11.9 × 10⁻⁶ cm/cm/°C |
Property Rockwell hardness (angle to rolling direction 0 –90°) | NGOES 85 | GOES 85 |
Property Magnetism | NGOES Isotropic (same in all directions) | GOES Highly anisotropic (optimized for rolling direction) |
Property Suitable processes | NGOES Stamping, laminating, annealing, laser cutting | GOES Rolling, annealing, domain refinement |
Property Applications | NGOES Electric motor and generator cores, inductors, small transformers, rotating machinery | GOES Power transformers, high-efficiency transformers, large electrical grids |
Property Cost (per ton) | NGOES Approx. $1,000 | GOES Approx. $2,000 |
NGOES and GOES Properties
FAQs on Electrical Steel
Can electrical steel be welded or tempered?
Yes, electrical steel can be both welded and tempered. Fusion welding (including resistance spot welding and laser welding) is commonly used to join laminations and provides a strong bond. But it could affect insulation and magnetic properties, so it needs to be done carefully. Mechanical interlocking and adhesive joints are alternatives but these might not be as durable. The good news is that, mainly due to the rise of electric vehicles, there’s ongoing research into the best welding processes for electrical steel—we might have a new method soon. Heat treatment can enhance electrical steel’s magnetic and mechanical properties. It starts with temper rolling to introduce strain energy, then it’s annealed with controlled heating to relieve stress and improve grain orientation for better magnetic performance and reduced core loss.
How is electrical steel different from regular steel?
Unlike good old traditional steel, electrical steel is created specifically for its superior magnetic characteristics. As we’ve covered (a lot), it has silicon in it, which lessens eddy current energy loss by increasing electrical resistivity—something that cannot be said of regular steel. Since the silicon changes how magnetic the material is, electrical steel is the safe bet for electromagnetic applications.
Is it better than D2 tool or weathering steel?
Not really. They’re all different, and each has its uses—just not the same ones. While electrical steel is good for electromagnetic applications, D2 tool steel is super hard and wear-resistant, making it the top choice for cutting tools, dies, and industrial machinery parts. Weathering steel is corrosion-resistant—just what’s needed for structural applications.
How long does electrical steel last?
If properly designed and well-maintained, electrical steel parts could last a very long time, perhaps several decades. Factors that contribute to this are operating conditions and whether or not protective coatings have been applied.
How Xometry Can Help
To learn more about electrical steel, and how you might be able to use it in your projects, contact us and one of our representatives will guide you in the right direction. We also offer a whole bunch of manufacturing services, from CNC machining and laser cutting to our forte, 3D printing. Your free, no-obligation quote is just a click away.
Disclaimer
The content appearing on this webpage is for informational purposes only. Xometry makes no representation or warranty of any kind, be it expressed or implied, as to the accuracy, completeness, or validity of the information. Any performance parameters, geometric tolerances, specific design features, quality and types of materials, or processes should not be inferred to represent what will be delivered by third-party suppliers or manufacturers through Xometry’s network. Buyers seeking quotes for parts are responsible for defining the specific requirements for those parts. Please refer to our terms and conditions for more information.
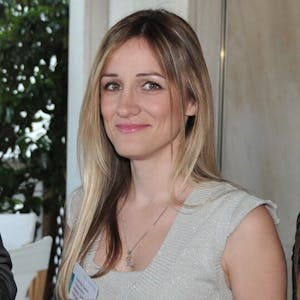