Ferrous metals are metals with iron as one of the main components. These metals are typically strong, durable, and magnetic. They are usually prone to rust, with exceptions like stainless steel which is more resistant to rust due to the addition of chromium in its composition.
This article is all about ferrous metals, including topics like: their properties, their uses, the different types on the market, etc.
What Is Ferrous Metal?
Ferrous metal is a term that is used for any metal that has iron as its main component in its composition. There is a broad range of metals that fall into this category. Examples include: wrought iron, cast iron, steel, and stainless steel. These metals usually have good mechanical properties, like high strength and durability. They are also known to have magnetic properties and most are prone to rust when exposed to moisture, due to the iron content. These metals are highly recyclable which contributes to their popularity in many applications, especially in the industrial sector. Ferrous metals are also commonly used in the construction and manufacturing industries.
What Are the Different Properties of Ferrous Metals?
Ferrous metals have a set of unique properties. These include:
1. Recyclability
One of the most significant properties of ferrous metals is their ability to be recycled. They can be melted down and re-forged repeatedly without losing much of their structural integrity. This makes ferrous metals environmentally friendly and economically advantageous as they can be reused across many cycles.
2. Heat Resistance
Ferrous metals, especially those high in alloy content like stainless steel, exhibit excellent heat resistance. This makes them ideal for use in engines, boilers, and cooking tools in which they must withstand high temperatures without deforming or breaking down.
3. Magnetic Properties
Most ferrous metals are magnetic, making them essential in the manufacture of: motors, generators, and transformers.
4. High Tensile Strength
Ferrous metals are known for their high tensile strength, which means they can endure significant stretching without breaking. This is why ferrous metals are commonly found in the construction of: buildings, bridges, and other structures.
5. Durability for Structural Applications
Ferrous metals are very durable and ideal for structural applications. They keep their structural integrity over time, provide the necessary support, and withstand the stresses of modern architectural demands, from skyscrapers to residential homes.
6. Variable Corrosion Resistance
The corrosion resistance of ferrous metals varies widely. While some, like carbon steel, are prone to rusting when exposed to moisture, others, such as stainless steel, are highly resistant to corrosion due to the presence of chromium which forms a passive layer of protection against oxidizing agents. However, most ferrous metals are considered to be susceptible to corrosion due to their high iron content.
What Are Examples of Ferrous Metals?
Some examples of ferrous metals include: cast iron, wrought iron, steel, stainless steel, and carbon steel. These metals are used for their strength in the construction and manufacturing sectors. Cast iron finds use in heavy-duty applications like pipes and machinery, whereas stainless steel is used in cutlery or medical instruments due to its favored corrosion-resistance properties.
Are Ferrous Metals Prone to Rusting?
Yes, ferrous metals are generally prone to rusting due to the iron content in their composition. Iron reacts with oxygen and moisture to form iron oxide, commonly known as rust. This reaction is a form of corrosion and can significantly weaken the metal over time if not properly managed or treated. However, not all ferrous metals rust at the same rate. For instance, stainless steel has a higher resistance to rust due to the presence of a protective chromium oxide layer that prevents extensive oxidation of the underlying iron. Other ferrous metals, like carbon steel, do not have this protective layer and are more susceptible to rusting.
Do Ferrous Metals Have High Conductivity?
No, ferrous metals are not particularly famous for either their thermal or electrical conductivity. Compared to non-ferrous metals they exhibit much lower thermal and electrical transmission. This is why they are less suitable for applications in which these properties are desired such as: heat exchange applications, electrical wiring, or power transmission.
What Is the Use of Ferrous Metals?
Ferrous metals are highly valued for their strength and durability. With their high tensile strength, they are ideal for structural uses such as: in buildings, bridges, and vehicles. They also possess unique magnetic properties crucial for making electrical components like motors and transformers. Additionally, ferrous metals can withstand high temperatures, which is beneficial for applications involving heat, such as in engines and cooking appliances. Their recyclability further enhances their appeal, as it allows for repeated reuse. This reduces both costs and environmental impact. This combination of useful properties makes ferrous metals a popular choice across numerous sectors.
They have broad utility in both industrial and domestic settings. Ferrous metals are crucial in the automotive industry for making car cylinder blocks, gear wheels, and engine parts. In construction, they are used to manufacture girders, plates, and metal cables to enhance structural integrity. Additionally, ferrous metals are essential in manufacturing sturdy machinery and tools, including: machine tool parts, chisels, lathe tools, and cutting equipment. They also appear in everyday items such as: kitchen draining boards and cutlery, as well as in garden tools like hammers and drills.
What Industry Uses Ferrous Metals?
Ferrous metals are extensively used across a wide range of industries due to their versatile properties such as: strength, durability, and magnetism. Some key industries include:
- Construction: Ferrous metals like steel are fundamental in the construction industry for: building structural frameworks, reinforcements in concrete (rebar), beams, and columns in high-rise buildings, bridges, and other infrastructure projects.
- Automotive: The automotive sector uses ferrous metals extensively for manufacturing: car frames, cylinder blocks, gear wheels, engines, and other components. Steel is particularly valued for its durability and ability to absorb impact.
- Manufacturing: Various manufacturing sectors use ferrous metals to produce tools, machinery, and equipment. Steel and cast iron are common in machine tools and heavy equipment due to their strength and wear resistance.
- Transportation and Shipping: Beyond automotive vehicles, ferrous metals are used in: shipbuilding, railway construction, and the production of containers. Their strength and durability support the weight and stress involved in transportation and shipping activities.
- Aerospace: Although less common than non-ferrous metals like aluminum, certain ferrous metals are used in aerospace for aircraft parts.
What Are the Different Types of Ferrous Metals?
There is a wide range of metals that contain iron as their main component and are considered ferrous metals. Some popular examples include:
1. Stainless Steel
Stainless steel is an alloy that crucially includes chromium (over 10.5% by mass) along with iron and carbon. It is renowned for its corrosion resistance, which is due to the chromium forming a passive layer of chromium oxide. This layer blocks oxygen diffusion to the steel surface and thus prevents corrosion. Stainless steel is used extensively in cookware, cutlery, surgical instruments, major appliances, and as construction material in large buildings. It can be classified into different types based on its crystalline structure, including austenitic, ferritic, and martensitic, each offering unique properties for various applications. One drawback is that stainless steel is generally quite expensive due to the higher cost of the alloying constituents that create its corrosion-resistance properties. The cost will depend on the type and the quality.
To learn more, see our full guide on Stainless Steels.
2. Cast Iron
Cast iron is a group of iron-carbon alloys with a carbon content greater than 2%. It is known for its excellent castability owing to the presence of silicon, which helps control the structure of the alloy. Despite its hardness and strength, it is relatively brittle. Cast iron is typically used in the manufacturing of: heavy-duty cookware, machine tools, automotive and machine components, and pipes. It offers good wear resistance and has a relatively low melting point, making it ideal for casting.
3. Wrought Iron
Wrought iron is almost pure iron with about 1–2% slag that is fibrous, which gives it a "grain" resembling wood, visible when it is etched or bent to the point of failure. Wrought iron is known for its ductility, malleability, and corrosion resistance. Its ideal uses are ornamental ironwork used in: gates, fences, and railings. Historically, it was also used in: construction, tools, and maritime hardware.
4. Carbon Steel
Carbon steel is an alloy of iron and carbon, with up to 2.1% carbon by weight. This type of steel can further be classified based on the carbon content: low-, medium-, and high-carbon steels. Each has varying degrees of hardness, malleability, and toughness. Low-carbon steel is particularly known for its ductility and toughness and is commonly used in: car bodies, appliances, and wire. Medium and high-carbon steels are harder and stronger but less ductile and are often used in: cutting tools, springs, and high-strength wires.
To learn more, see our full guide on Carbon Steels.
5. Alloy Steel
Alloy steel is made by adding various elements such as: manganese, silicon, nickel, and chromium to carbon steel. This improves its mechanical properties such as: strength, hardness, wear resistance, and toughness. Different types of alloy steels are designed for different uses, including in the automotive industry for parts like gears and axles, in energy sectors like wind turbines, and in machinery that requires high durability.
6. Tool Steel
Tool steel is a type of carbon and alloy steel that is well-suited to tool making. This is because of its hardness, resistance to deformation and abrasion, and ability to maintain a sharp edge under high temperatures. As a result, it is used in the manufacturing of tool bits and cutting tools like: drills and gear cutters, dies, and molds. It often contains tungsten, molybdenum, cobalt, and vanadium in varying quantities to increase its heat resistance and durability.
To learn more, see our full guide on What is Tool Steel.
7. Carbon Tool Steel
Carbon tool steel is typically high in carbon content — usually around 0.6% to 1.5% — and is very hard and abrasion-resistant, making it effective for tooling applications. It is used to manufacture tools that do not require the high level of hardness and resistance to heat that alloy tool steels provide. Common applications include hand tools, such as chisels and hammers, as well as industrial cutting blades in which heat-treated sharp edges are crucial.
How To Choose Which Type of Ferrous Metal To Use
Choosing the right type of ferrous metals for your project involves several important considerations. These are:
- Different ferrous metals offer varying levels of strength, ductility, corrosion resistance, and wear resistance, which should be matched to the demands of your project. For example, high-carbon steel is valued for its strength and is often used in cutting tools and blades, while alloy steels like stainless steel provide a balance of strength and corrosion resistance ideal for harsh environments. Low-carbon steel, or mild steel, is favored for its ductility and is commonly used in structures that require forming and shaping, such as automotive bodies and building frameworks.
- The environment in which the metal will be used dictates your choice significantly. Stainless steel is excellent for corrosive environments such as coastal areas or chemical plants due to its chromium content, which prevents rust. For high-temperature applications, nickel-alloy steels are preferred as they maintain structural integrity even under extreme heat.
- Cost-effectiveness and material availability also influence metal choice. Mild steel is the most affordable and readily available, making it a go-to for many general applications. However, for special requirements such as improved wear resistance or specific mechanical properties, more expensive alloys like stainless steel may be necessary. These might require sourcing from specialized suppliers.
- The intended use of the metal often dictates the specific type required. For instance, construction projects typically use mild steel for reinforced concrete due to its excellent tensile strength. The automotive industry uses various steel types to meet safety and performance standards, with critical safety components often made from high-strength steel.
- The ease with which a metal can be machined and welded also affects material choice. Alloys designed for improved machinability may contain additives like sulfur, although this can sometimes reduce other desirable properties such as toughness. Low-carbon steels are generally easier to weld than high-carbon varieties, and some high-alloy steels require specialized welding techniques due to their complex chemical compositions.
- Maintenance requirements and expected life span are also important. Metals like stainless steel, which are less prone to rust, often require less upkeep. It is important to consider both current and future needs, including potential changes in environmental conditions or regulations, which might affect the suitability of the chosen metal over time.
What Is the Advantage of Using Ferrous Metals?
Ferrous metals offer several advantages that make them highly valuable for use across various industries. Here are the main benefits:
- Ferrous metals, like steel and cast iron, are known for their high strength and durability, which make them ideal for structural and load-bearing applications.
- Many ferrous metals are magnetic, making them essential in the production of: motors, generators, and other electromagnetic devices.
- Generally, ferrous metals are less expensive than many non-ferrous metals, making them a more economical choice for large-scale construction and industrial projects.
- Ferrous metals can be recycled repeatedly without degradation in quality, which enhances their sustainability and reduces environmental impact.
- Ferrous metals typically have good heat distribution properties.
- The various types of ferrous metals, from carbon steel to stainless steel and cast iron, offer a range of mechanical properties that can be tailored to specific needs, making ferrous metals highly versatile for different uses.
What Is the Disadvantage of Using Ferrous Metals?
While ferrous metals are widely used due to their strength and cost-effectiveness, they also come with several disadvantages that can affect their suitability for certain applications. Here are the main drawbacks:
- One of the most significant disadvantages of ferrous metals is their tendency to rust when exposed to moisture and oxygen. This corrosion can compromise the structural integrity and appearance of the metal over time. Stainless steel is an exception due to its chromium content, which resists oxidation.
- Ferrous metals are generally heavier than non-ferrous metals like aluminum and titanium. This high density can be a drawback in industries in which lightweight materials are preferable, such as in aerospace and certain automotive applications.
Is Stainless Steel More Resistant to Corrosion Than Cast Iron?
Yes, stainless steel is considered to be more corrosion-resistant than cast iron due to the presence of chromium in its composition. The chromium forms a passive layer that protects stainless steel from oxidation.
What Distinguishes Ferrous Metals From Other Types of Metals?
Ferrous metals are primarily distinguished from other types of metals by their iron content. They contain iron as a major component, which gives them specific properties not found in non-ferrous metals. Key characteristics of ferrous metals include magnetic properties, high strength, and durability, which make them ideal for use in construction and industrial applications like building frameworks and machinery. Additionally, ferrous metals tend to be more susceptible to corrosion due to their iron content, except for types like stainless steel which includes chromium to resist rust. Their density generally makes them heavier than non-ferrous metals, which often leads to different uses in various industries based on weight considerations.
What Is the Difference Between Non-Ferrous Metals and Ferrous Metals?
The primary difference between non-ferrous and ferrous metals lies in their iron content. Ferrous metals contain iron, making them magnetic and prone to corrosion when exposed to moisture and oxygen, except for certain types like stainless steel which are alloyed with chromium to prevent rust. These metals are typically stronger and heavier, which makes them ideal for structural applications such as in buildings and vehicles. On the other hand, non-ferrous metals do not contain iron, are not magnetic, and are more resistant to corrosion. This makes them suitable for applications like electrical wiring, roofing, and plumbing that require lighter or non-magnetic materials. Non-ferrous metals include: copper, aluminum, zinc, lead, and tin, and precious metals like silver and gold.
What Is the Difference Between Precious Metals and Ferrous Metals?
Precious metals, such as: gold, silver, and platinum, are naturally occurring, rare metallic elements with high economic value, typically due to their rarity, use in industrial processes, or role in historical monetary systems. They are generally less reactive, more resistant to corrosion, and have higher melting points than other metals. In contrast, ferrous metals mainly contain iron. They are usually more abundant, magnetic, prone to corrosion unless treated, and extensively used in construction and manufacturing due to their strength and durability.
To learn more, see our full guide on Precious Metals.
Summary
This article presented ferrous metals, explained them, and discussed their various uses and types. To learn more about ferrous metals, contact a Xometry representative.
Xometry provides a wide range of manufacturing capabilities and other value-added services for all of your prototyping and production needs. Visit our website to learn more or to request a free, no-obligation quote.
Disclaimer
The content appearing on this webpage is for informational purposes only. Xometry makes no representation or warranty of any kind, be it expressed or implied, as to the accuracy, completeness, or validity of the information. Any performance parameters, geometric tolerances, specific design features, quality and types of materials, or processes should not be inferred to represent what will be delivered by third-party suppliers or manufacturers through Xometry’s network. Buyers seeking quotes for parts are responsible for defining the specific requirements for those parts. Please refer to our terms and conditions for more information.
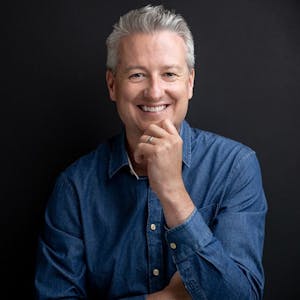