What Is the Fracture or Breaking Point?
A material can be described as fractured or broken only once a degree of cracking has occurred. This is a result of the elastic/plastic deformation of the material by strain (distortion) imposed by stress (loading forces).
This cracking will generally cause the sample to part fully or partially, depending on the loads applied, directions of forces, and the nature of the part being tested. Such failure may, for example, be tensile and complete in a loaded web of a part. However, this may leave the component intact at a lower tensile region, as the loading may be complex and involve non-uniform stress distributions.
The fracture or breaking point of a material depends on factors such as its composition, microstructure, temperature, and loading conditions. The fracture occurs when the loading applied to a component exceeds the inter-atomic or inter-crystalline strength of the material. These are two complex features that depend heavily upon both microscopic and, to a variable degree, macroscopic behaviors of the material/component.
To illustrate (using brittle-material failure), the microscopic effect occurs through applied tensile loads which exceed the material’s ability to resist. This is due to one or more of the following reasons:
- Inclusion, flaw, or pre-existing cracking acts as a stress concentrator. This allows the catastrophic fracture to propagate rapidly through the sample.
- Stress exceeding the intra-crystalline load capacity. This causes failure along cleavage planes between crystals.
- Lattice bond strength being exceeded by applied loads. This initiates a cascading split due to atomic-level stress concentration.
In a ductile material, the eventual fracture modes are essentially the same as for brittle materials. Except that the plastic deformation process can induce hardening as a result of deformation, which makes the behavior more complex.
In compressive, bending, or impact load scenarios, the resulting strains can be both tensile and compressive. This makes the failure modes more complex and regional. However, the mechanisms are closely related other than for a Poisson’s-ratio-related failure mode. Here, the bulge of compression exerts tensile load and shear loads in transition regions outside a purely compressive center line.
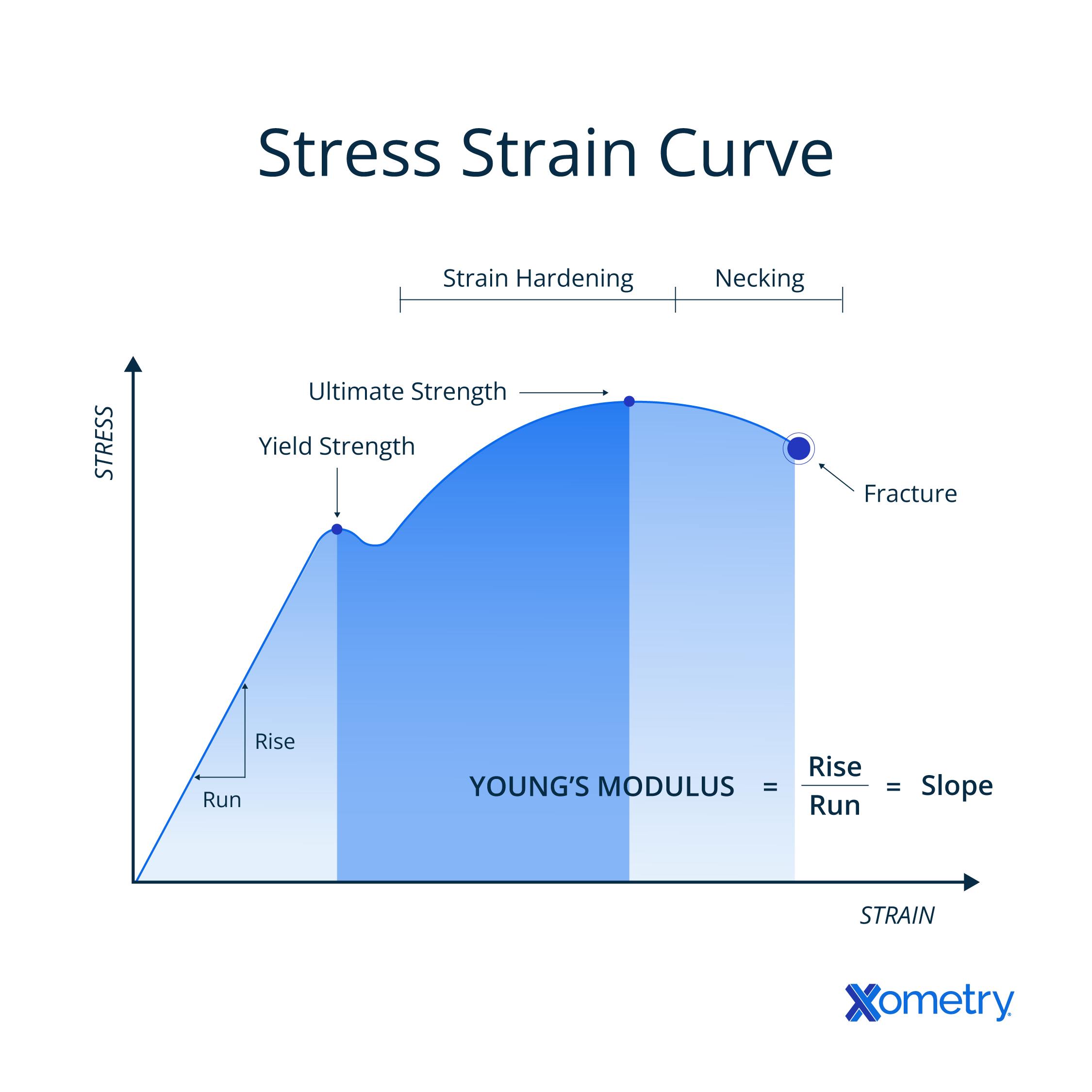
Implications of Fracture or Breaking Point in Engineering
A highly informed and experimentally confirmed understanding of fracture or breaking point is central to good design. A range of considerations is listed below:
- A component may require precision for operation and cannot be allowed to distort under even the most extreme of “normal” operating conditions. The material must be selected (and the design executed) to ensure that only elastic deformation occurs under such loads. Furthermore, this elastic deformation must be limited to that which does not alter the functional capacity of the part by distortion.
- Where a component has a life-critical function, such as in aerospace and automotive components, medical implants, etc., significant factors of safety (FoS) must be applied. This is to ensure that the part will only fail under conditions so destructive that all associated systems are liable to have failed simultaneously.
- If parts are considered weight-critical, a balance must be struck between component survivability and component weight. Such a trade-off often drives the selection of higher-performing materials and more complex stress distribution engineering.
Testing Fracture/Breaking Point Behavior
There is a range of related tests that provide information as to the fracture or breaking point behavior of both standardized/simplified material test samples and actual components.
Test methods fall into three basic categories and are listed below:
- Tensile Tests: Tensile tests apply a highly regularized linear tensile loading to one of a range of standard dog-bone test pieces. As load is applied, a record of the stress and resulting strain is kept. This provides a graphical output of the relationship between the two factors. It informs about the nature, behavior, and stress-induced alteration of the material through the entire loading cycle up to fracture. Tensile tests are appropriate for both ductile and brittle materials, though they’re more widely applied to ductile engineering materials which are better suited to tensile load bearing. Ductility is often considered the most useful characteristic of materials suited to general engineering and construction tasks. This is because brittle materials are more commonly applied to compressive loading scenarios.
- Compressive Tests: Compressive tests function in an identical way, except that the load is in pure compression. Failure modes in compression tests generally result from a catastrophic fracture in brittle materials or a period of bulge/compression in ductile materials that is followed by fracture.
- Bending and Impact Tests: Bending and impact tests are often used to evaluate failure/fracture behavior. A swinging or dropping weight applies a disruptive force to an encased sample, bending, fracturing, or shearing the material. The absorbed energy is translated into a comparative measurement, although the nature of the failure is in many ways more informative than the energy absorbed.
Benefits of the Testing the Fracture Point
- Informs engineers and scientists as to functional and reliably usable strength, and provides an understanding of that strength’s limitations and variability.
- Facilitates and validates the safety of structures, products, and systems.
- An invaluable tool for quality control in manufacturing processes. By testing materials for their load response, it is possible to identify variations or defects in the material composition, manufacturing process, or treatment methods.
- Informs material selection by testing and comparing the fracture properties of various materials.
- Helps in designing and optimizing product shape, stress distribution, weight, dimensions, and material selection to ensure the product's durability and reliability.
- Informs researchers and scientists studying the material behavior of new materials, the improvement of existing ones, and the advancement of combination/process development.
Challenges in Testing for Fracture or Breaking Point
Testing for fracture or breaking point in materials is fraught with problems. Such challenges are listed below:
- Preparing samples for fracture testing presents challenges, especially for complex or heterogeneous materials like composites. Improper sample preparation by inaccuracy, or surface imperfections, or invisible internal defects can introduce stress concentrations or other artifacts that deliver anomalous test results.
- Material manufacturing processes can exhibit variability in their properties, even within the same batch or production run. Anisotropic materials, such as composites or some processed metals can make fracture testing complex. These typically demand very careful sampling and testing strategies.
- Fracture testing often involves testing materials under specific environmental conditions, such as temperature, humidity, or exposure to chemicals. Controlling these conditions can be challenging and require costly equipment.
- Variations in fracture testing methods exist, and methods must be selected with care, so they’re suitable for the target material.
- Fracture behavior varies considerably with specimen size or scale. Small-scale testing rarely represents the behavior of larger structures, and testing large structures is virtually impossible, with the same degree of rigor.
- Fractures can occur in ductile, brittle, or fatigue modes and be severely affected by strain rate. Testing for each mode generally requires alternate techniques and equipment.
Types of Fracture or Breaking Points in Materials
There are several types of fractures or breaking points that can occur in materials. This depends upon the material type, its condition, external influences from thermal or chemical effects, and in particular the loading scenario. These types are listed below:
- Ductile fracture results when materials exhibit plastic deformation before failure. Tensile loading, in particular, is characterized by gradual necking and deformation of the material, eventually parting at the narrowest point. The ductile phase can be short or long, depending on the degree of ductility. Ductile fractures have what is often described as a fibrous appearance at the parted surfaces and are typical of many metals/alloys and some polymers.
- Brittle fracture occurs in materials that undergo little or no plastic deformation before failure. It is characterized by a sudden, catastrophic failure without any detectable change in behavior. Brittle fractures often have a crystalline appearance and exhibit little or no necking or deformation. Materials such as ceramics, metals at cryogenic temperatures, concrete, and certain polymers can experience brittle fractures.
- Fatigue results from repeated cyclic loading and tends to be a progressive failure mechanism. It generally starts with the formation of microcracks at any microscopic discontinuity or macroscopic fault, gradually growing and linking multiple cracks together, leading to the final fracture. Fatigue fractures are often characterized by a distinctive pattern of crack propagation, such as beach marks or striations.
- Stress corrosion cracking (SCC) is a type of fracture that occurs due to the combined action of mechanical stress and corrosive environmental damage providing a stress concentration point. It can occur in metals/alloys. SCC can lead to sudden, brittle fracture even at stress levels below the material's yield strength and in essentially ductile materials.
- Creep fracture refers to a failure mode in materials subjected to long-term exposure to sustained loading and sometimes elevated temperatures. Creep is a time-dependent deformation process that some ductile materials are prone to, potentially leading to creep fracture.
- Impact fracture occurs when a material is subjected to a sudden and energetic or high-impulse loading. It is characterized by a rapid and violent failure, often resulting in significant damage or fragmentation of the material. Impact fractures can be observed in materials subjected to dynamic loadings, such as during accidents or impulsive deceleration impacts.
Stress and Strain and the Fracture Point
In most materials, the relationship between stress and strain goes through a number of phases. These phases are sometimes distinct and evident in test data but are often subject to soft transitions of mode. Under initial loading, the overwhelming majority of materials will experience a truly elastic phase as the load is applied. This involves a period of extension as the load increases. This is defined as elastic because the removal of the load will result in a complete and undistorted recovery of the pre-stress dimensions. This truly elastic phase sees virtually all of the energy used in the extension of the material being recovered in the relaxation phase. Notable exceptions to this are elastomers, which have a time component in their recovery that forms a hysteresis curve, implying some energy absorption/dissipation in the process.
As the elastic-limit loading is exceeded, materials undergo a transition to a process defined as yield. In some materials, this is a sharp transition, in which the stress-strain curve deviates from the linear, elastic phase. In others, there is a very slow transition from elastic to plastic behavior, indicated by a slow deviation from the linear elastic phase. In either case, this is the point at which ductile behavior commences and the material undergoes plastic deformation with increased load. Note that truly brittle materials will not display this yield point or phase.
As the load further increases, a variety of forms result. In some cases, the ductile behavior continues and the strength is reduced as the plastic deformation reduces the cross-sectional area. This leads to the stress-strain curve reaching an asymptote followed by fracture. In some cases, the material may undergo a hardening/toughening process at some point in the ductile phase. This is analogous to work hardening and it can add complexity to the stress-strain curve as this new effect begins to influence the test.
At the point at which the gradient of the stress-strain curve reaches zero, no additional force is required for further extension. The material is described as having reached its ultimate tensile strength (UTS). Generally, fracture follows rapidly from this point. If the material is truly brittle (i.e., has no ductile phase), the yield point/phase is absent. There is no non-linearity in the stress-strain curve and the material will fracture at a load that is its UTS.
For more information, see our guide on the Stress-Strain Curve.
Xometry provides a wide range of manufacturing capabilities including CNC machining, 3D printing, injection molding, laser cutting, and sheet metal fabrication. Get your instant quote today.
Disclaimer
The content appearing on this webpage is for informational purposes only. Xometry makes no representation or warranty of any kind, be it expressed or implied, as to the accuracy, completeness, or validity of the information. Any performance parameters, geometric tolerances, specific design features, quality and types of materials, or processes should not be inferred to represent what will be delivered by third-party suppliers or manufacturers through Xometry’s network. Buyers seeking quotes for parts are responsible for defining the specific requirements for those parts. Please refer to our terms and conditions for more information.
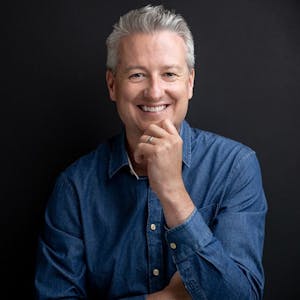