The words fragile and brittle are often used interchangeably, however, there is a slight difference between the two. Brittleness is a well-defined mechanical property whereas fragility is a material characteristic that is not well defined. Despite this ambiguity, this article will provide some clarity on the differences between fragility and brittleness by defining the key characteristics, identifying various factors, and listing examples of each.
What Is Fragile Material?
Fragility in the context of materials science refers to the ease with which a material breaks or disintegrates when exposed to a load. The failure of fragile materials is often observed as being sudden, without any warning. This is due to the inability of a fragile material to absorb energy via deformation. While fragility cannot be defined mathematically, it is generally used to broadly describe a range of materials that break easily. Such materials are not suited for any type of application in which high loads are expected to be resisted.
What Are the Key Characteristics of Fragile Materials?
Fragility encompasses a large group of materials that break easily and can include: metals, plastics, organic matter, and green parts (i.e., prior to sintering). Indeed, only the ease with which they break can be used to characterize these materials. This is not something that can be precisely defined. However, the various ways in which fragile materials fail can be used to tighten up the definition somewhat. For example, fragile materials are not elastic and also do not plastically deform when exposed to a load. Instead, on the application of a load they tend to disintegrate or fail catastrophically. Fragile materials are highly susceptible to stress concentrations caused by physical cracks, sharp corners, and impurities in the material. As such, when a load is applied, these discontinuities cause localized increases in stress that cause cracks to propagate, ultimately resulting in part failure. Fragile materials can also be susceptible to sharp temperature gradients. The sudden onset of a temperature change can cause sudden expansion which will produce localized stress concentrations that can cause a fragile material to fail abruptly.
What Is the Importance of Identifying Fragile Materials?
Identifying fragile materials early on in the design process is important because special care must be taken to safely handle, process, install, and transport these materials to prevent damage. When transporting fragile materials, the packaging must be clearly labeled to indicate the fragile materials within.
How Does Fragility Affect the Handling of Materials or Components?
The fragility of materials or components necessitates special handling procedures to reduce the chances of damage. These procedures can include: how to package and transport the components, where to store these components, e.g., in temperature-controlled store rooms, and how to safely dispose of the materials if they break during handling.
What Factors Contribute to the Fragility of Certain Materials?
There are many factors that contribute to the fragility of a material, some of which are listed below:
- Physical Structure: The physical structure of a fragile material can include both microscopic and macroscopic properties. For example, the type of interatomic bonds or whether or not a material has a crystalline structure can all contribute to a material's fragility. On the macroscopic side, a granular material that has been pressed into a solid can be very fragile and is easily broken down as there are no strong bonds between these granular particles.
- Environment: The environment in which materials operate can have significant effects on their fragility. For example, sharp temperature gradients can cause fragile materials to fracture or disintegrate. In addition, chemically corrosive or radiative environments can contribute to the long-term development of fragility in a material.
- Loading Conditions: The manner in which a material is loaded can contribute to its fragility. For example, cyclic loading or shock loading can exacerbate the inherent tendency of a fragile material to fracture.
How Can Fragile Materials Be Identified?
There is no standardized method of classifying fragile materials as fragility is not a defined material property. However, fragile materials can be identified via destructive testing. For example, the load required to destroy a fragile material as well as the manner in which it fails can indicate fragility. In general, the failure of a fragile material is instant as there is no deformation prior to rupture. The loads required are also relatively low when compared to materials typically classified as brittle.
What Are the Common Challenges Faced When Working With Fragile Materials?
Working with fragile materials can be challenging for a number of reasons, some of which are listed below:
- Manufacturing: Processing fragile materials is a challenge as normal processing methods like machining can cause the material to fail. Depending on the material, alternative, more-expensive processing techniques may be required, like molding or sintering for example.
- Installation: Assembling products that contain fragile components requires special training and installation procedures. For example, bolting a fragile material into an assembly requires precise bolt-torque control as over-tightening can cause the fragile component to fail.
- Transport: When transporting products that contain fragile components, it is important to correctly package and label these items. A single shock load during transportation can cause fragile components to fail. Soft packaging and load-sensing stickers on the packaging can help mitigate the risks involved during transportation.
Is Fragility a Type of Defect in the Manufacturing Process?
No, in most cases fragility is not a defect in the manufacturing process and is rather a property of a material. However, it must be noted that fragility can be increased through some manufacturing processes like heat treatment or the introduction of impurities into a material.
What Is Brittleness (brittle)?
Brittleness refers to the tendency for a material to undergo very little or no plastic deformation before fracture. Unlike fragile materials, brittle materials can absorb some energy before failing. Brittleness is a material property that can be tested for and defined, whereas fragility cannot. For more information, see our guide on What is Brittleness?
What Is the Implication of Being Brittle?
A brittle material is not desirable in most applications, especially if cyclic or shock load cases are to be expected. Processing brittle materials like ceramics, for example, pose some challenges. These types of materials are generally difficult to process using typical manufacturing techniques like machining for example. This is in part due to their high hardness and wear resistance. However, some brittle materials have desirable properties such as high compressive strength, and high wear resistance. This means that brittle materials aren’t inherently bad, and there exist many applications in which they can be of some use. However, in the majority of engineering applications, ductile materials are desirable as they will undergo high levels of deformation before failure, making them more predictable and safe.
What Are the Key Characteristics of Brittle Materials?
Listed below are some key characteristics of brittle materials:
- High Hardness: Brittle materials are often very hard and resist deformation, especially when loaded in compression. Some of the hardest known materials are extremely hard while also being brittle.
- Minimal Deformation Before Failure: Brittle materials undergo no or very little plastic deformation prior to failure. In some materials, especially metals, there is a small amount of elastic deformation prior to fracture.
- Poor Resistance to Shock Load: Brittle materials can fail suddenly if exposed to a sudden shock load.
How Does Brittleness Affect the Mechanical Properties of a Material?
Listed below are some ways in which brittleness affects mechanical properties:
- Low Fatigue Resistance: Brittle materials have poor fatigue resistance as they are very susceptible to crack initiation and propagation.
- Low Toughness: Toughness is the ability of a material to absorb energy before failure, often through plastic or elastic deformation. However, brittle materials absorb comparably lower amounts of energy before failure and are not resistant to shock loading.
- Low Tensile Strength: In general brittle materials are much weaker when loaded in tension, this is in part due to their inability to deform plastically during loading.
What Are the Factors That Caused Brittleness?
Listed below are some factors that cause brittleness:
- Temperature: A material's brittleness can be affected by temperature. For example, a normally ductile material can become brittle as temperature decreases and a typically brittle material can become more ductile as temperatures increase.
- Impurities: Impurities within a material can increase its brittleness. These impurities create stress concentrations within the material that promote crack initiation. Once a crack initiates in a brittle material it may cause the material to fail at a lower load.
- Corrosion: Corrosion, specifically inter-granular corrosion, can cause a normally ductile material to exhibit brittle behavior. This happens when a corrosive agent attacks the granular boundaries in a metal resulting in brittle corrosion products.
How Can Brittle Materials Be Identified?
Brittle materials are often identified via destructive testing. Two common tests are the Charpy impact test and the IZOD impact test. Both of these tests expose a sample to a sudden shock load. Alternatively, a tensile test can be performed; brittle materials will exhibit very low levels of deformation prior to failure when loaded in tension.
How Does Brittleness Influence the Susceptibility of Fracture?
Brittle materials are more susceptible to sudden fracture than ductile materials. This is due to the fact that brittle materials allow for very little deformation prior to fracture.
How Does Temperature Impact the Brittleness of the Materials?
In general, higher temperatures tend to reduce the brittleness of a material, whereas lower temperatures tend to increase the brittleness of a material. For example, a normally ductile material can exhibit brittle behavior at sufficiently low temperatures. For more information, see our guide on Thermal Resistance.
How Does Engineering Work Around Brittle Materials?
Brittle materials are often used in various industries for a range of applications. However, special considerations must be taken to ensure these materials perform as expected. For example, when designing a part with a brittle material, stress concentrations like sharp corners must be kept to an absolute minimum. Another factor is processing. Some brittle materials like ceramics cannot be machined in their final state. As such, ceramics are often formed into shape by pressing ceramic powder along with a binder into a shape using a hydraulic press. In this state, the ceramic is fragile and can be machined. Once machined it can be sintered in a furnace to achieve its final properties.
Is Brittleness a Type of Defect in the Manufacturing Process?
No, brittleness is a material property and is not considered a type of defect. However, some manufacturing processes like hardening for example can increase the brittleness of a material.
How Does Fragility Differ From Brittleness?
Fragility is not a well-defined physical property whereas brittleness is defined, and materials can be tested for brittleness.
What Are Examples of Fragile Materials?
Listed below are some examples of fragile materials:
- Metal Foil
- Porcelain
- Polystyrene Foam
What Are Examples of Brittle Materials?
Listed below are some examples of brittle materials:
- Cast Iron
- Sintered Ceramic
- Concrete
Can Brittle Things Be Fragile?
Yes. For example, glass is brittle and is also considered to be fragile.
Are Fragility and Brittleness the Same?
No. Fragility is not a defined material property whereas brittleness is.
Is Steel Brittle?
Not all steels are brittle. Steels with high carbon content are often considered to be brittle.
Is Glass Fragile?
Yes, glass can be considered to be fragile.
Summary
This article presented fragile vs brittle materials, explained what it is, and discussed each of their various characteristics. To learn more about fragile vs brittle materials, contact a Xometry representative.
Xometry provides a wide range of manufacturing capabilities and other value-added services for all of your prototyping and production needs. Visit our website to learn more or to request a free, no-obligation quote.
Disclaimer
The content appearing on this webpage is for informational purposes only. Xometry makes no representation or warranty of any kind, be it expressed or implied, as to the accuracy, completeness, or validity of the information. Any performance parameters, geometric tolerances, specific design features, quality and types of materials, or processes should not be inferred to represent what will be delivered by third-party suppliers or manufacturers through Xometry’s network. Buyers seeking quotes for parts are responsible for defining the specific requirements for those parts. Please refer to our terms and conditions for more information
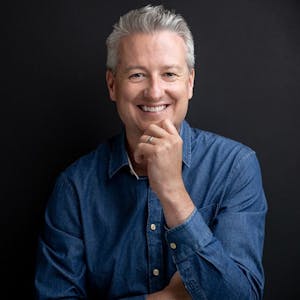